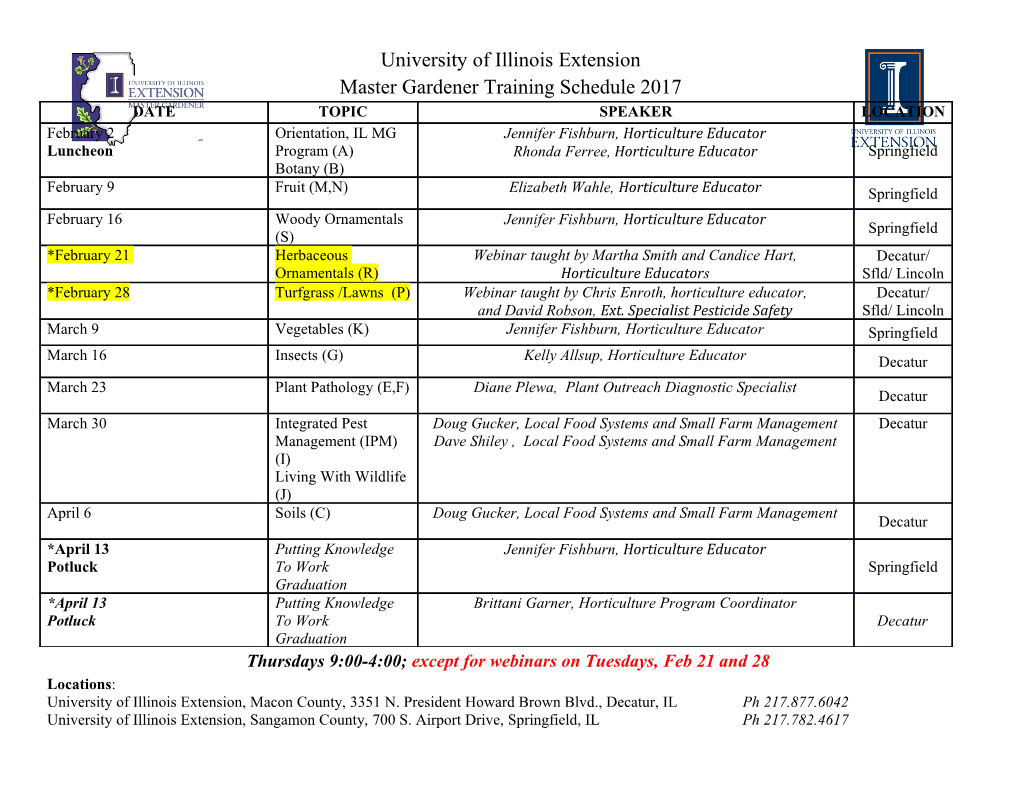
http://www.paper.edu.cn Scripta Materialia 57 (2007) 1036–1039 The addition of lanthanum hexaboride to zirconium diboride for improved oxidation resistance Xing-hong Zhang, Ping Hu,* Jie-cai Han, Lin Xu and Song-he Meng Center for Composite Materials, Harbin Institute of Technology, Harbin 150001, China Received 24 May 2007; revised 20 July 2007; accepted 22 July 2007 Available online 6 September 2007 The oxidation resistance of ZrB2–SiC-based ultrahigh-temperature ceramic (UHTC) is remarkably enhanced by the addition of lanthanum hexaboride, which has demonstrated outstanding oxidation resistance to temperatures up to 2400 °C. The improved oxi- dation resistance is attributed to the formation of a coherent compact scale, which acts as an effective barrier against the inward diffusion of oxygen. Ó 2007 Acta Materialia Inc. Published by Elsevier Ltd. All rights reserved. Keywords: Oxidation resistance; Lanthanum hexaboride (LaB6); Zirconium diboride (ZrB2); Ultrahigh-temperature ceramic (UHTC) Ultrahigh-temperature ceramics (UHTC), including high-temperature SiO2-forming materials, such as SiC, some refractory metal diborides, have been studied and Si3N4 and MoSi2 [7]. Although great efforts have been developed since the 1960s [1,2]. In recent years, great made in this aspect, no effective approach has been re- attention has been paid to ZrB2 and HfB2. Their striking ported up to now. This work highlights the significant thermochemical stability in terms of extremely high improvement in the oxidation resistance of ZrB2–SiC- melting point, resistance to ablation/oxidation at high based UHTC with the addition of 10 vol.% LaB6. The temperatures and thermal-shock resistance represent role of LaB6 is also examined and discussed. key requirements applicable to thermal protection sys- The ZrB2 and LaB6 powders (Northwest Institute for tems for re-entry space vehicles with sharp leading-edge Non-ferrous Metal Research, China) were of the same profiles [3–6]. purity (99.5%) and both had a mean particle size of ZrB2–SiC and HfB2–SiC are currently considered 5 lm. The SiC powder (Weifang Kaihua Micro-powder as the baseline UHTC. Indeed, varying the initial Co., Ltd., China) was predominantly a-SiC, and it had a composition of these UHTC by changing the SiC con- reported purity of 99.5% and a mean particle size of tent has given added flexibility in optimizing specific 2 lm. Batches containing ZrB2–20 vol.% SiC–10 vol.% microstructural designs: adjusting the SiC content in LaB6 were prepared. Powders were milled in a poly- ZrB2 and HfB2 matrices has proved beneficial for mer-coated bucket charged with ethanol using WC balls improving oxidation and ablation resistance, without for 8 h and dried in a rotating evaporator. Milled pow- being detrimental to high-temperature stability [4–6]. ders were uniaxially hot pressed in a boron nitride The significant improvement in oxidation resistance coated graphite die at 2000 °C for 60 min under vacuum of ZrB2 (HfB2)-based UHTC below 1700 °C have been (0.5 mbar) and 30 MPa of applied pressure. Specimens achieved by incorporation of silicides due to the forma- were first polished and ultrasonically cleaned by acetone tion of silica glass layer with low oxygen permeability, and absolute ethanol. The final densities of composites which provide an efficacious protective oxidation were measured by Archimedes’ method, and the relative barrier. However, silicides become invalid at higher density was estimated by the rule of mixture. temperatures, especially above 2000 °C, because of Three sample coupons of U18.8 · 14.2 mm were cut active oxidation and evaporation. Thermodynamics- from hot-pressed plates for oxidation tests. The speci- based calculations have also shown the temperature mens were ultrasonically cleaned in acetone followed limits in oxidizing environments for state-of-the-art, by absolute ethanol, dried and then weighed (to an accu- racy of 0.1 mg). Oxidation tests were carried out with an * Corresponding author. Tel.: +86 13845077148; fax: +86 45186402382; e-mail: [email protected] oxyacetylene torch. Models were placed in graphite holders which enabled test durations in excess of 600 s. 1359-6462/$ - see front matter Ó 2007 Acta Materialia Inc. Published by Elsevier Ltd. All rights reserved. doi:10.1016/j.scriptamat.2007.07.036 转载 中国科技论文在线 http://www.paper.edu.cn X.-h. Zhang et al. / Scripta Materialia 57 (2007) 1036–1039 1037 Oxidation tests were conducted according to GJB323A- samples were exposed to the oxyacetylene torch heater. 96 standard on the oxyacetylene ablation equipment [8]. Specifically, the surface temperature rose dramatically The pressure and flux of acetylene were 0.1 MPa and to 2000 °C and then began to rise gradually, reaching 1.15 m3 hÀ1, and for oxygen 0.5 MPa and 2.30 m3 hÀ1, a maximum temperature of over 2400 °C, as can be seen respectively. The emissivity was determined by a two- in Figure 3. A high thermal stress will occur in the tested color radiation pyrometer and the temperature of spec- sample due to the large temperature gradient. However, imen surface was measured using a one-color pyrometer no cracks were observed on the sample. This fact sug- (Mikron Instrument Co., Inc., Oakland, NJ). Two gests that the composite exhibits good thermal-shock ZrB2–20 vol.% SiC sample coupons were also tested un- resistance. A total weight loss only of 0.2% was mea- der the same conditions for comparison. sured. The measured weight loss is primarily ascribed An influence of oxidation was investigated by mea- to the active oxidation of SiC and volatilization of some suring the mass change and thickness of the scale. X- oxidation products such as B2O3 and SiO2. Figure 4 ray diffraction and scanning electron microscopy/energy shows the macrograph and cross-sectional micrograph dispersive spectroscopy (FEI Sirion, Holland) were used of oxidized ZrB2–20 vol.% SiC after testing under the to characterize the phase composition and microstruc- same conditions. However, extensive damage was ob- ture of the surface and cross section of the samples after served at the external surface and the outer oxide scale oxidation experiments. was abscised. Cross-sectional examination showed that The bulk density of the hot-pressed material was the oxide scale is incompact and not adherent to unal- 5.93 g cmÀ3, which corresponds to 99.2% of the theoret- tered material, as shown in Figure 4(b). Moreover, the ical density estimated with the rule of mixture. Figure 1 total weight change for ZrB2–20SiC (3.1%) is far higher shows scanning electron micrographs of the polished than that for ZrB2–20SiC–10LaB6 (0.2%). surfaces of the ZrB2–SiC–LaB6. The microstructure of There are three kinds of oxidants, namely, H2O, CO2 the composites is regular, with a mean grain size is about and O2, in the present case. H2O and CO2 were not 5 lm, and the residual porosity is very scarce. The SiC taken into account for the sake of simplicity. Therefore, particulates (dark phases) are distributed homoge- the main expected reactions during oxidation process neously in the diboride matrix and no agglomeration are as follows: was detected. 5 Figure 2 shows the photographs of ZrB2–SiC–LaB6 ZrB2ðsÞþ O2ðgÞ!ZrO2ðsÞþB2O3ðlÞð1Þ during (left) and after (right) oxyacetylene torch testing. 2 21 1 The macromorphology of the oxidized surface of the LaB6ðsÞþ O2ðgÞ! La2O3ðsÞþ3B2O3ðlÞð2Þ specimen oxidized for 600 s with an oxyacetylene torch 4 2 shows a mechanical scour in the surface center zone, B2O3ðlÞ!B2O3ðgÞð3Þ resulting from blowing by the airflow. The surface layer 3 SiCðsÞþ O ðgÞ!SiO ðlÞþCOðgÞð4Þ appears compact and adherent, and no cracks or spalla- 2 2 2 tion were detected there. The surface temperature in- creased drastically in a very short time when the 2600 2400 2200 C) ° 2000 1800 1600 Temperature ( 1400 1200 1000 0 100 200 300 400 500 600 Time (s) Figure 3. Measured results of temperature curves of the ZrB2–20 vol.% Figure 1. SEM micrograph of the polished surface of a ZrB2–20 vol.% SiC–10 vol.% LaB6 sample. SiC–10 vol.% LaB6 sample. Figure 2. Photographs of ZrB2–20 vol.% SiC–10 vol.% LaB6 (a) Figure 4. Photograph and cross-sectional micrograph (the outer loose during and (b) after oxyacetylene torch testing. The oxidized surface scale has been removed) of oxidized ZrB2–20 vol.% SiC after testing layer appears compact and adherent, and no cracks or spallation were under the same conditions. Spallation and cracks (arrows) were detected there. observed after testing. 中国科技论文在线 http://www.paper.edu.cn 1038 X.-h. Zhang et al. / Scripta Materialia 57 (2007) 1036–1039 SiCðsÞþO2ðgÞ!SiOðgÞþCOðgÞð5Þ Figures 6 and 7 show the SEM micrographs and EDS SiO ðlÞ!SiO ðgÞð6Þ of the surface of oxidized ZrB2–SiC–LaB6 at 2400 °C for 2 2 600 s at low and high magnifications. The surface ap- La2O3ðsÞþZrO2ðsÞ!La2Zr2O7ðsÞð7Þ peared compact, with only a few small microcracks The main reaction products from the oxidation of and pores. EDS analysis of the surface of a oxidized ZrB and LaB are zirconia, lanthana and amorphous sample shows that zirconium, oxygen and lanthanum 2 6 are present as the primary elements, and silicon and bor- boric acid (B2O3). The last compound has an unusually low melting point (450 °C) and a high vapor pressure on are almost undetectable by the apparatus (Figs. 6 and 7). It is significant to note that the surface-oxidized sam- (Figure 5). Therefore, at high temperature B2O3 quickly vaporizes (Reaction (3)) resulting in increased oxidation ple consists of two distinctly different scales, namely, the bright and gray phases. The bright phase was distributed of ZrB2. The introduction of remarkably improves the oxidation resistance of the UHTC in the temperature at the grain boundaries of the gray phase and sealed the ranging from 1200 °C to approximately 1700 °C.
Details
-
File Typepdf
-
Upload Time-
-
Content LanguagesEnglish
-
Upload UserAnonymous/Not logged-in
-
File Pages4 Page
-
File Size-