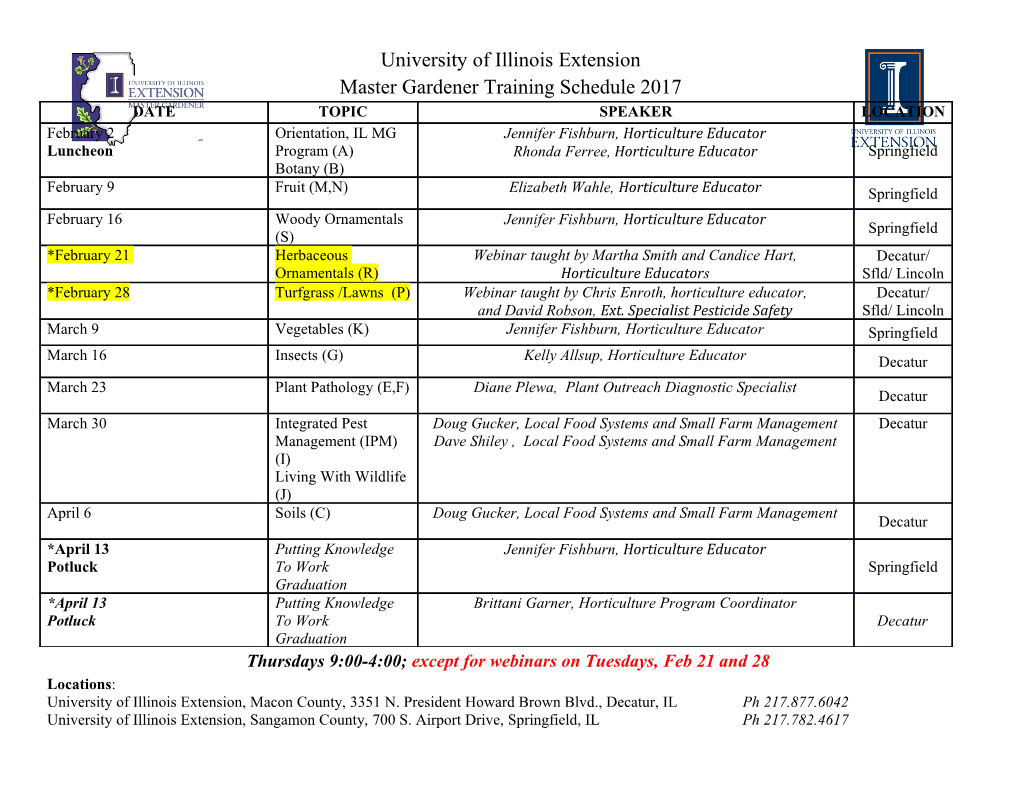
Life Cycle Inventory of Sodium Acetate and Expanded Graphite Short Report Provider Dr. Niels Jungbluth ESU-services Ltd. Kanzleistr. 4, CH - 8610 Uster [email protected] www.esu-services.ch Tel. +41 44 940 61 32; Fax +41 44 940 61 94 Customer Benoit Nguyen HEIG-VD / LESBAT Haute Ecole d'Ingénierie et de Gestion du canton de Vaud Laboratoire d'Energétique Solaire et de Physique du BATiment Route de Cheseaux 1 1401 Yverdon-les-Bains 0041 (0)24 55 76 352 [email protected] Uster, 15. Januar 2008 15.01.08 11:59 C:\Dokumente und Einstellungen\Niels\Eigene Dateien\projekte\200 LCI HEIG material\bericht\200_LCI-material-solar-storage_v2.0.doc Life Cycle Inventory of Sodium Acetate and Expanded Graphite 1 1 Background and Objectives The laboratory LESBAT of the HEIG-VD works at the moment on the solar energy storage issue. They found that the use of sodium acetate (Na(CH3COO)*3H2O), a phase change material (PCM), is a good way to optimize solar heating systems. Actually, the customer uses sodium acetate mixed with expanded graphite (80 à 150 g/l), a chemical product produced by the following company: SGL Carbon located at Meitingen (Deutschland). The product is not commercially available. A similar product, which uses paraffin instead of sodium acetate is marketed by the company SGL Carbon under the brand name Ecophit. This product has been included in the investigation in order to verify the data. The goal of this study is to assess if the energy gain resulted from the use of sodium acetate is balanced or not by its embodied energy. The ecoinvent data v2.0 do not yet investigate sodium acetate and expanded graphite (ecoinvent Centre 2007). Therefore the customer has asked ESU-services to conduct a life cycle inventory analysis of the two materials and to provide some aggregated key indicators for further analysis. The study should investigate sodium acetate with and without expanded graphite. In general the ecoinvent methodology has been followed in order to achieve full consistency with the used background data (Frischknecht et al. 2007a). 2 Life cycle inventory of phase change material for solar energy storage Author: Niels Jungbluth, ESU-services Ltd., Uster Review: Sybille Büsser, ESU-services Ltd., Uster Last changes: 15 January 2008 2.1 Sodium acetate Sodium acetate is produced from acetic acid and sodium hydroxide. Therefore the following reaction takes place: CH3COOH + NaOH + 2H2O = CH3COONa + 3H2O Information about the technical production process was not available. Important issues could be: • Is the product dried and how is this done? • Which amounts of inputs are used and what is the efficiency of the process? • Is there a heat release, how is this used and is cooling necessary? The unit process raw data are based on literature references for similar chemical compounds of sodium salts (Hischier 2007) and own assumptions. These assumptions are described in the GeneralComment column of Tab. 2.1. Life Cycle Inventory of Sodium Acetate and Expanded Graphite 2 Tab. 2.1 Unit process raw data of sodium acetate production i t a Pro n re yType o sodium acetate, i tu nt dDevi Name c trihydrate, at GeneralComment ai Unit t tru on95% s plant Locat andar fra St Uncer In Location RER InfrastructureProcess 0 Unit kg product sodium acetate, trihydrate, at plant RER 0 kg 1 technosphere sodium hydroxide, 50% in H2O, production mix, at plant RER 0 kg 5.13E-1 1 1.30 (4,na,1,1,1,5); Stoichiometric calculation with 95% yield acetic acid, 98% in H2O, at plant RER 0 kg 7.72E-1 1 1.30 (4,na,1,1,1,5); Stoichiometric calculation with 95% yield transport, freight, rail RER 0 tkm 7.71E-1 1 2.09 (4,5,na,na,na,na); Standard distance 600km transport, lorry >16t, fleet average RER 0 tkm 1.28E-1 1 2.09 (4,5,na,na,na,na); Standard distance 100km heat, natural gas, at industrial furnace >100kW RER 0 MJ 2.00E+0 1 1.30 (4,na,1,1,1,5); Rough estimation with literature data for chemicals electricity, medium voltage, production UCTE, at grid UCTE 0 kWh 3.33E-1 1 1.30 (4,na,1,1,1,5); Rough estimation with literature data, range (.017-.33) chemical plant, organics RER 1 unit 4.00E-10 1 3.09 (4,5,na,na,na,na); Standard assumption treatment, sewage, unpolluted, to wastewater treatment, CH 0 m3 1.20E-2 1 1.30 (4,na,1,1,1,5); Rough estimation with literature data class 3 resource, in water Water, unspecified natural origin - - m3 1.20E-2 1 1.30 (4,na,1,1,1,5); Rough estimation with literature data Water, cooling, unspecified natural origin - - m3 2.40E-2 1 1.30 (4,na,1,1,1,5); Rough estimation with literature data emission water, Sodium, ion - - kg 1.40E-2 1 5.10 (4,na,1,1,1,5); Calculation 5% river Ethyl acetate - - kg 3.66E-3 1 3.09 (4,na,1,1,1,5); Calculation 5% BOD5, Biological Oxygen Demand - - kg 6.39E-3 1 1.62 (4,na,1,1,1,5); Calculation, 90% removal in treatment COD, Chemical Oxygen Demand - - kg 6.39E-3 1 1.62 (4,na,1,1,1,5); Calculation, 90% removal in treatment DOC, Dissolved Organic Carbon - - kg 2.00E-3 1 1.62 (4,na,1,1,1,5); Calculation, 90% removal in treatment TOC, Total Organic Carbon - - kg 2.00E-3 1 1.62 (4,na,1,1,1,5); Calculation, 90% removal in treatment emission air, high Heat, waste - - MJ 1.20E+0 1 1.30 (4,na,1,1,1,5); Calculation with electricity use population density Carbon dioxide, fossil - - kg 4.83E-2 1 1.30 (4,na,1,1,1,5); Calculation, 90% from waste water treatment 2.2 Graphite mining Data for graphite in ecoinvent data v2.0 are a very rough assumption with the assumption that mining is the same as for lime (Hischier 2007). Thus, the inventory for this material has been updated. The following information has been found on http://en.wikipedia.org. Graphite is mined around the world by both open pit and underground methods. While flake graphite and amorphous graphite are both mined open pit and underground, lump (vein) graphite is only mined underground in Sri Lanka. The open pit mines usually employ equipment (i.e. bulldozers) to scoop up the ore, which is usually put in trucks and moved to the plant. Since the original rock is usually lateritized or weathered, this amounts to moving dirt with flecks or pieces of graphite in it from the pit (blasting is seldom required). The underground graphite mines employ drilling and blasting to break up the hard rock (ore), which is then moved by mine cars pulled by a locomotive, or moved by automotive vehicles, to the surface and then to the plant. In less-developed areas of the world, the ore can be mined by pick and shovel and transported by mine cars pushed by a laborer or by women carrying baskets of ore on their heads. Graphite usually needs beneficiation, although thick-bedded amorphous graphite and vein graphite is almost always beneficiated, if beneficiated at all, by laborers hand-picking out the pieces of gangue (rock) and hand-screening the product. The great majority of world flake graphite production is crushed and ground if necessary and beneficiated by flotation. Treating graphite by flotation encounters one big difficulty: graphite is very soft and "marks" (coats) the particles of gangue. This makes the "marked" gangue particles float off with the graphite to yield a very impure concentrate. There are two ways of obtaining a saleable concentrate or product: regrinding and floating it again and again (up to seven times) to obtain a purer and purer concentrate, or by leaching (dissolving) the gangue with hydrofluoric acid (for a silicate gangue) or hydrochloric acid (for a carbonate gangue). In the milling process, the incoming graphite products and concentrates can be ground before being classified (sized or screened), with the coarser flake size fractions (above 8 mesh, 8 mesh to 20 mesh, 20 mesh to 50 mesh) carefully preserved, and then the carbon contents are determined. Then some standard blends can be prepared from the different fractions, each with a certain flake size distribution and carbon content. Custom blends can also be made for individual customers who want a certain flake size distribution and carbon content. If flake size is unimportant, the concentrate can be ground more freely. Typical final products include a fine powder for use as a slurry in oil drilling; in zirconium silicate, sodium silicate and isopropyl alcohol coatings for foundry molds; and a carbon raiser in the steel industry (Synthetic graphite powder and powdered petroleum coke can also be used as carbon raiser). Rough Life Cycle Inventory of Sodium Acetate and Expanded Graphite 3 graphite is typically classified, ground, and packaged at a graphite mill; often the more complex formulations are also mixed and packaged at the mill facility. Environmental impacts from graphite mills consist of air pollution including fine particulate exposure of workers and also soil contamination from powder spillages leading to heavy metals contaminations of soil. Dust masks are normally worn by workers during the production process to avoid worker exposure to the fine airborne graphite and zircon silicate. The unit process raw data of graphite production in Tab. 2.2 are based on an LCA study (Pehnt 2002). Missing data have been assessed with data provided in the ecoinvent database for lime production (Hischier 2007).
Details
-
File Typepdf
-
Upload Time-
-
Content LanguagesEnglish
-
Upload UserAnonymous/Not logged-in
-
File Pages14 Page
-
File Size-