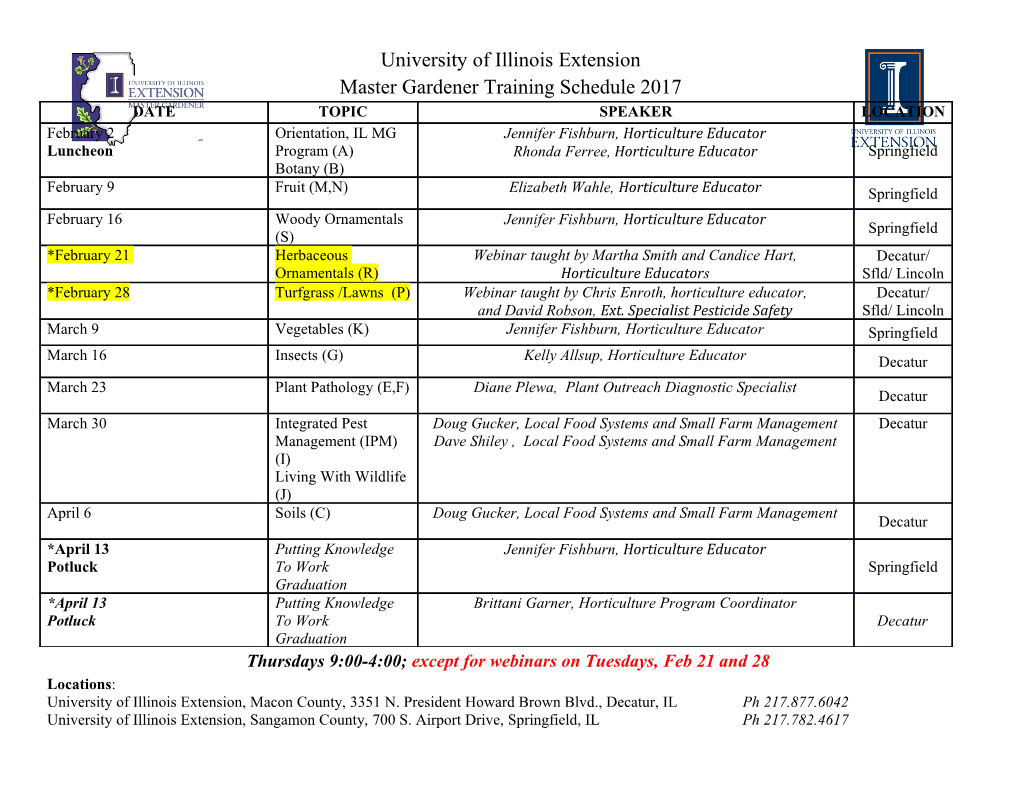
Deformation Control and Countermeasures for Construction Surface When Using Pile-Beam-Arch Method in Confined Water-Rich Sand Cross-Stratification Zhang Xue-gang1, Zhan-ping Song2, Chi-yu Yuan1, Jian-sheng Qu1 1.Shaanxi Railway Institute, Weinan Shaanxi, 714000;2. School of Civil Engineering, Xi'an University of Architecture and Technology, Xi'an 710055, PR China ABSTRACT The Shuangjing Station of the Beijing subway Line 7 is close to the core of the Beijing central business district. Together with the Shuangjing Station of Line 10, it forms a T-type transfer amid many surrounding buildings and underground pipelines. The Shuangjing Station is a two-layer double-column three-span subway station constructed by the pile-beam-arch method. In this study, a numerical simulation of the pipeline deformation that occurred during the construction of the pilot tunnel of the Shuangjing subway station was performed using the ANSYS software. “Eight-pilot-tunnel” excavation was used to consider the multitunnel effect. The deformation characteristics and control mode of the existing pipeline atop the station, caused by the different pilot tunnel constructions, were analyzed. Based on the results of the analyses, an implementation of the principle of pilot tunnel excavation is recommended for such projects. This involves an “up-to-down and crosswise” construction sequence. To avoid mutual interference between the pilot tunnels, longitudinal and horizontal distances of not less than 10 m and a vertical distance of 15 m between adjacent tunnels are recommended. Each small pilot tunnel should be rapidly excavated using the bench method to reduce ground disturbance. This construction technique requires strengthening and enclosing of the primary support as soon as possible. This is done to limit settlement and control the deformation of the existing pipeline during the construction. The proposed construction method has good economic and social benefits and can be used as reference for similar future projects. KEYWORDS: Subway station; Pile-beam-arch (PBA) tunneling method; Pilot tunnel excavation; Multitunnel effect; Construction scheme; Numerical simulation - 8727 - Vol. 19 [2014], Bund. Y 8728 INTRODUCTION China has experienced accelerated urbanization in recent years, and the development of infrastructure for alleviating traffic congestion, such as the construction of subways, has flourished. The construction of subway tunnels in developed metropolis that contain many high-rise buildings inevitably involves underground excavation, with the attendant impact on the surroundings.[1-2] It is particularly important during the tunneling process to effectively control surface settlement and other deformations caused by excavation, and to ensure the intactness of existing underground pipelines. Numerous studies have been conducted in this field by experts from home and abroad, and this has led to a number of findings[3-6]. The pile- beam-arch (PBA) method is often used for underground excavation over a large area[7]. It involves the creation of pilot tunnels to make piles, beams, and arches for forming force transmission structures, and to carry out the excavation of the inner tunnel under the arch cover of the underground excavation. Although this construction method has been successfully implemented several times, it still has some deficiencies and shortcomings such as the requirement of multiple pilot tunnels and diverse processes, long blasting times, and extended ground disturbance. This has prompted the present study on the control of the surface deformation caused by PBA construction. In this study, the PBA process that was used to construct the Shuangjing Station of the Beijing Metro Line 7 through a sandy soil artesian aquifer was simulated. The surface settlement and pipeline deformation caused by the different excavation steps were analyzed, and countermeasures for future projects are proposed. PROJECT OVERVIEW The Shuangjing Station of the Beijing Metro Line 7 is close to the center of the central business district, which is characterized by heavy traffic. The station forms a T-type transfer with the Shuangjing Station of Line 10. It has two underground two-column three-span floors and was constructed by underground excavation (PBA method). The station has a principal length of 229.6 m and a standard section 23.1 m wide and 16.25 m high. The baseboard of the structure has a buried depth of about 30.3 m, and the roof is covered by earth 13.89 m thick. The profile contains eight upper pilot tunnels in two rows. The excavation of the station was based on previously excavated pilot tunnels. The pilot tunnels in the main part of the station were created through a very complex stratum that included fine sand, coarse sand, sand and gravel, and silty soil. The upper pilot tunnels were created through a phreatic aquifer, and the lower pilot tunnels through an artesian aquifer. Above the structure of the station was a dense network of 14 important municipal pipelines. A schematic of the location of the main structure relative to the pipelines and the numbering of the pipelines (1 to 14) are shown in Figure 1. Vol. 19 [2014], Bund. Y 8729 Figure 1: Construction profile of Shuangjing Station of Beijing Metro Line 7 NUMERICAL SIMULATION OF PBA METHOD ANSYS model ANSYS finite element program was used to analyze and assess the measures for controlling surface settlement and pipeline deformation during PBA construction in a sandy soil artesian aquifer. Numerical analyses of the three following aspects were carried out: (a) the effects of the first excavation of the four upper and four lower pilot tunnels; (b) the effects of the different excavation sequences of the four upper and four lower small pilot tunnels; and (c) the effects of the main construction works of the station. The size of the 3D computation model is 121 × 50 × 60.5 m (length × width × height). The model is shown in Figure 2. Vol. 19 [2014], Bund. Y 8730 Figure 2: 3D computation model ANSYS parameters All formation parameters Table 1 gives the physical and mechanical parameters of the typical sections of the rock where the station is located, as determined by geotechnical investigations. Table 1: Physical and mechanical properties of the rock at the location of the station Elastic Severe/ Poisson’s Cohesion Friction Surrounding rock modulus [kN·m-3] ratio [kPa] angle [°] [MPa] First layer 16.9 36 0.3 19 28 Second layer 20.1 86 0.27 9.3 26 Third layer 20.3 110 0.27 11.6 27 Fourth layer 20.6 125 0.27 9.6 31 Fifth layer 20.8 132 0.28 10 33 Simulation parameters of grouting reinforcement layer and preliminary bracing The details of the grouting reinforcement layer and the primary support parameters in the design of the station are given in Table 2. Vol. 19 [2014], Bund. Y 8731 Table 2: Physical parameters of initial support and reinforcement Severe/ Elastic modulus Poisson’s Cohesion Friction [kN·m-3] [MPa] ratio [kPa] angle [°] Primary 23 26 0.2 - - support Reinforced 23 0.495 0.25 0.3 50 area Material parameters of station structure The main structural parameters of the station based on its design and the current “code for design of railway tunnel” are given in Table 3. Table 3: Structural parameters of the station model Severe Elastic modulus Cohesion Friction Poisson’s ratio [kN/m3] [GPa] [MPa] angle [°] Grouting reinforcement 22 0.495 0.3 0.3 50 Backfill C20 concrete 25 25.5 0.25 - - Initial lining 26 20 0.2 - - Second lining 27 32.5 0.25 - - side piling 23 20 0.2 - - Top beam 25 32.5 0.25 - - Steel pipe pile 25 33.5 0.25 - - Steel tie rod 79 200 0.25 - - Effects of different excavation sequences of pilot tunnels Simulated condition Based on the specific circumstances of the small pilot tunnels in the main structure of the Shuangjing Station, the following three schemes were simulated: Scheme 1: Stagger skipping excavation of the upper pilot tunnels. In this scheme, the upper pilot tunnels were first excavated till the hole-through was completed, after which the lower pilot tunnels were excavated. The specific excavation order was ① - ③ - ④ - ② - ⑤ - ⑦ - ⑧ - ⑥. The numbers of the pilot tunnels are shown in Figure 3. Scheme 2: Stagger skipping excavation of the lower pilot tunnels. In this scheme, the lower pilot tunnels were first excavated till the hole-through was completed, after which the Vol. 19 [2014], Bund. Y 8732 upper pilot tunnels were excavated. The specific excavation order was ⑤ - ⑦ - ⑧ - ⑥.- ① - ③ - ④ - ②. Scheme 3: Stagger excavation of the upper pilot tunnels beginning with the outer pilot tunnel. The excavation order of this scheme was ① - ④- ② - ③ - ⑤ - ⑧ - ⑥ - ⑦. In all the excavation schemes, a distance of 8 m was left between adjacent pilot tunnels. The step method was used for the excavation of each pilot tunnel, with a gap of 3 m between successive steps. The excavation footage cycle of the pilot tunnel was 1 m. The primary supporting of the excavated soil mass was done in a further step. Figure 3: Numbering scheme of the tunnels Numerical simulation results and analysis Four typical construction steps were selected to clarify the impact of the pilot tunnel excavation on the ground deformation and pipeline displacement: (1) the excavation of Pilot Tunnel 1 (or Pilot Tunnel 5) by 25 m up to the middle of the model; (2) execution of the hole- through of the upper pilot tunnels (lower pilot tunnels); (3) excavation of Pilot Tunnel 5 (or Pilot Tunnel 1) by 25 m up to the middle of the model; (4) execution of the hole-through of all the pilot tunnels. Surface movement and deformation To reduce the boundary effect on the calculated results, the Y = 25 m section was used to analyze the surface deformation. By numerical simulation, the surface subsidence of the four typical construction steps and three schemes were analyzed as presented in Table 4.
Details
-
File Typepdf
-
Upload Time-
-
Content LanguagesEnglish
-
Upload UserAnonymous/Not logged-in
-
File Pages13 Page
-
File Size-