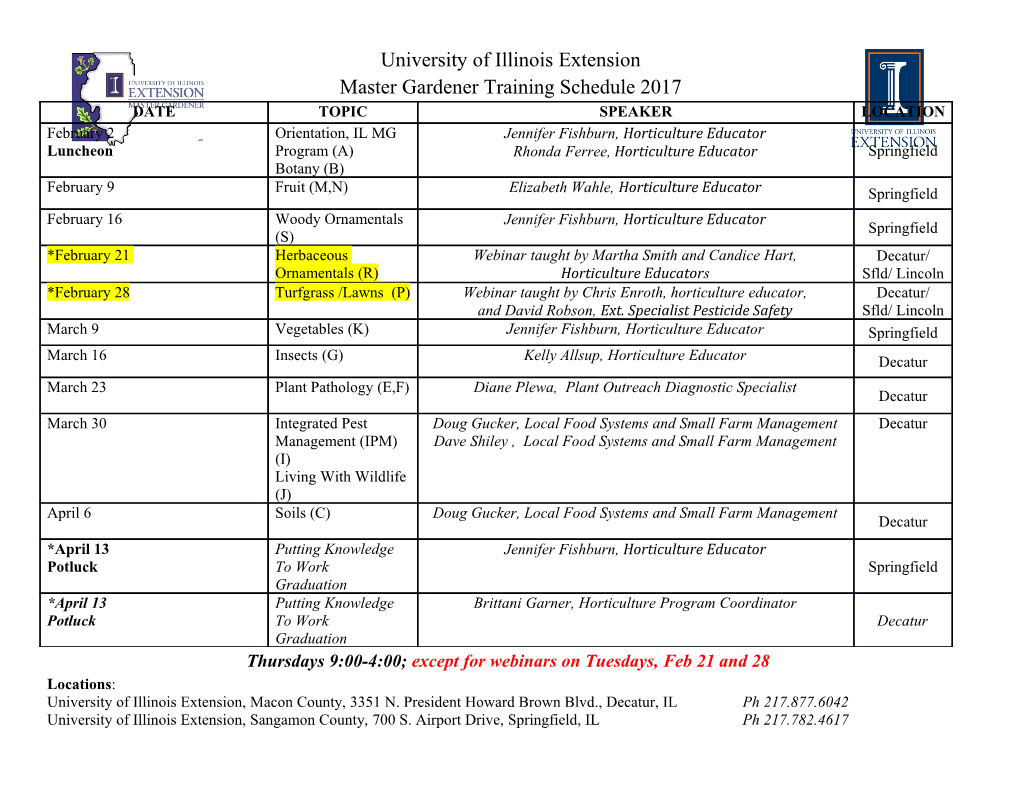
New Method for Evaluating Strength and Ductility of Brazed Joints Advantages of a new universal type of braze specimen are simple design for easy production and good reproducibility. A brazing fixture is not required and the brazing gap is easy to maintain BY E. KLAUSN ITZER Introduction (c) hardness tests; (d) analyses of review is given in Reference 1. The High-temperature brazing has structure; (e) microanalyses; (f) cor­ shapes of specimens have the follow­ found special application in nuclear rosion tests; (g) irradiation tests and ing disadvantages from the point of reactors and best known is the fabri­ post-irradiation tests as per (a) to view of the present objective: (a) cation of brazed spacers for fuel ele­ (d). Brazed specimens are made individu­ ments. Web cross joints of about One and the same shape of speci­ ally. This involves dissimilar brazing 0.016 inch (0.4 mm) stainless steel or men were used in all tests to keep the conditions and high production costs; nickel alloy sheet are usually made. marginal conditions resulting from the (b) The gap is difficult to maintain. Figure 1 as an example shows a manufacture of the brazed specimens This drawback makes itself felt partic­ spacer of Inconel 718 material brazed constant. ularly in high-temperature brazing fol­ with AWS class BNi-7 brazing filler lowed by homogenizing; (c) Speci­ Universally Applied mens are very large as a rule and are metal for use with fuel elements in Brazed Specimen pressurized water reactors. therefore inappropriate for irradiation Initially the stress conditions to tests; (d) A brazing fixture is required The possibility of using stainless in some cases which presents addition­ steel spacers, as shown in Fig. 2 which the brazed joints are exposed permit only the use of high- al difficulties when high brazing tem­ brazed with AWS BNi-5, was to be peratures are involved. These consid­ studied under a sodium-cooled fast temperature brazing filler metals, such as AWS BNi-5. All the following ex­ erations resulted in the design of the breeder research scheme. The joints brazed specimen shown in Fig. 3, are subject to a more severe environ­ planations and discussions should therefore be viewed from this aspect. which largely avoids the above- ment than that which is found in mentioned drawbacks. pressurized-water reactors due to the Brazing was performed without flux higher operating temperature, the under a vacuum. A sleeve is manufactured from the highly corrosive medium and the high Numerous test methods and shapes base metal and a pin is fitted into it. dose of neutrons. of specimens are known. A very good The pin is reduced in diameter over Before the investigations on the brazing filler metal were started, the question of a universal type of braze Forced fit- 1 1 specimen was considered. The results * ' * I'S * I 1 * " ' * , * * 7y\\ •-n "... of these considerations are described - - : _ * •• " J-' - - - - , *:j * ,; •-::, - u in the following paper. * • * •-. • Test Procedures m ., . ~ . *- - - ill To enable brazed joints to be tested li. j . - i »**<. 1 - -. for their useability tinder the an­ i S i 111 81 1 1 » 1 I i ticipated service conditions—tem­ Fig. 1—Spacer made of Inconel 71* 8 is perature: 1200°F (650°C); serv­ brazed with AWS BNi-7 Venting holes--^ Pockets for brazing metal ice medium: sodium; "fluence": p IO23 n/cm2 (E > 0.5 MeV)—the < following tests were carried out: (a) shearing tests at 68°F (20°C), 750°F Brazing gap---^^ / (400°C), 1200°F (650°C); (b) de­ formation tests at 68°F (20°C), 750°F (400°C), 1200°F (650°C); E. KLAUSNITZER is with Siemens Akti- Forced fit- engesellschaft, Erlanger, Postfach, W. Z Germany. Paper presented at the Second Interna­ tional AWS-WRC Brazing Conference held in San Francisco, Calif, during April 27- Fig. 2—Spacer made of stainless steel 29, 1971. is brazed with AWS BNi-5 Fig. 3—Brazed test specimen 454-s I OCTOBER 1971 Fig. 4—Typical appearance of a brazed test specimen (stain­ Fig. 5—Eccentric position of the pin (stainless steel brazed less steel brazed with AWS BNi-5) with CPNM 2) the greater part of its length so that Pockets for brazing metal the desired gap is obtained. The sleeve has several holes in opposite places, Punch- enabling the brazing gap to be vented and the brazing filler metal to be applied. Since the brazed specimen can be turned on a lathe, its manufac­ Sleeve ture is accurate, cheap and easily reproducible. The specimen in this form is still not appropriate for the tests enumer­ Holder ated above. It has to be divided into 0.04-0.08 inch (1-2 mm) thick slices. These slices enabled all tests to be performed. Brazed Test Specimen Sleeve and pin are degreased Specimen (methanol in an ultrasonic bath) and then fitted together. The holes lying on one line parallel to the axis of the sleeve are then filled with brazing filler Brazing gap metal. The number and size of the holes should be chosen so as to ensure the brazing gap being completely filled with brazing filler metal. A vacuum induction furnace for indirect heating by means of a susceptor has proved Fig. 7—Schematic of shearing tool suitable for the brazing operation. Brazing was carried out under the (1.2 mm) thick can be obtained from Venting slot' conditions prescribed by the manufac­ the specimen in Fig. 3. turer of the brazing filler metal or About 40 test specimens have been according to our own experience made with different brazing filler met­ (heating rate, brazing temperature, als and no rejects were found. holding time and cooling rate). The first examination after brazing is a Basic Studies of Slices visual test. If the specimens are metal­ A few basic studies were carried lically bright and the braze metal is out to check whether the brazed visible both in the holes and at the specimen had the desired properties. ends of the sleeve and pin, then the It was found that the gap usually is Fig. 6—Improved design of brazed test specimens have been properly brazed. constant over the entire length of the specimen The specimen is then sliced, making specimen. Figure 4 shows a typical occasionally encountered, as Fig. 5 sure that the cuts are taken exactly at brazed joint made with AWS BNi-5. shows. right angles. About 20 slices 0.05 inch An eccentric position of the pin was This inaccuracy presumably is due WELDING RESEARCH SUPPLEMENT] 455-s Punch Specimen -fJ8,05 Fig. 10—Brazed test specimen after shearing test with re- Fig. 8—Details of shearing tool mains of braze metal on the sheared faces to the small pin diameter of 0.16 then screwed on to prevent the slice TaB = shearing strength in ps inches (4 mm) and to the horizontal from bending upward during the test. (or kgf/mm2) position in which brazing was done. The lower end of the punch has a Utilizing larger specimens, however, centering pilot to fit the hole in the Pmax, = maximum load exerted by was impossible within this research slice. In diffusion brazing, the gap the testing machine in program since the space for the usually is very small and it is of pounds force. planned irradiation tests was limited. particular importance therefore that F0 = cross section under test in A larger specimen will be used in the both the brazed specimens and the inches or (mm2). future to take account of the experi­ shearing tool should be made with ence gained. This is shown in Fig. 6. close tolerances. Details are given in Numerous metallographic examina­ The new position of the brazing filler Fig. 8. tions made on tested slices revealed that shearing always takes place in the metal pockets and venting slots makes The shearing tool is shown in Fig. brazed joint. Figure 10 shows a typi­ a vertical brazing position possible. A 9. It is made of Nimonic 90 and has cal case where residues of braze metal greater number of slices is also proven itself well in about 100 tests at are distributed at random over the achieved in this way. 68°F (20°C), 750°F (400°C) and sheared faces. 1200°F (650°C.) For the test, the Determining Shear Strength shearing tool with the slice inserted is Determining Ductility placed in a testing machine and the A shearing tool (Fig. 7) is used for load is raised until the specimen As stated initially, the brazed joints determining the shear strength of the breaks. The shearing strength is calcu­ considered are subjected to a high slices. This tool comprises a die, a lated from the following formula: degree of "fluence" so that embrittle­ holder and a punch. The slice is ac­ ment is liable to occur. It is therefore commodated in a depression of the die most important that a coefficient where it is centered. The holder is Tali F„ denoting the ductility should be estab- +*? I 19 20 21 22 23 24 25 26 27 28 29 Fig. 9—Photo of shearing tool made of Nimonic 90 456-s | OCTOBER 1971 lished. No acceptable suggestions were the deformation. Any other quantita­ the brazed joints. The hardness test found in the technical literature. To tive criteria are impossible to give results (Vickers test using a load of avoid any misunderstanding it should since, as the degree of deformation 0.050 kgf) are also shown. be pointed out that the proposition rises, increasingly disturbing factors All tests were carried out on slices described in the following section is due to friction tend to develop.
Details
-
File Typepdf
-
Upload Time-
-
Content LanguagesEnglish
-
Upload UserAnonymous/Not logged-in
-
File Pages7 Page
-
File Size-