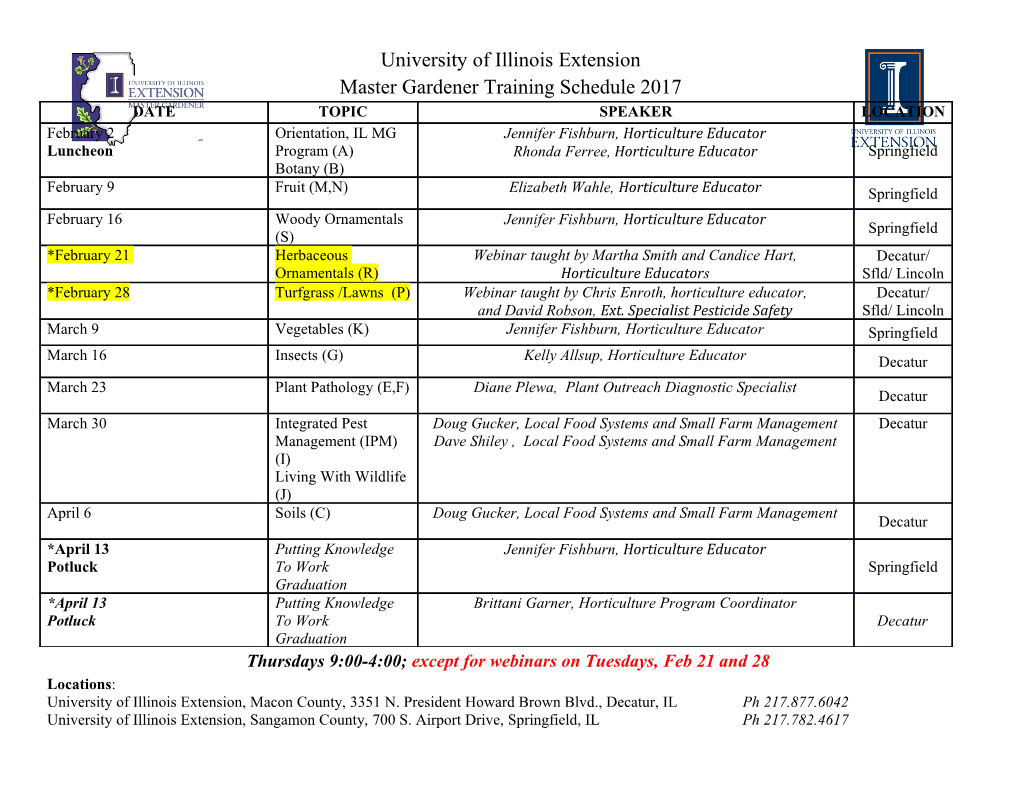
King Abdulaziz University Mechanical Engineering Department MEP 460 Heat Exchanger Design Fouling of heat Exchanger Oct. 2020 Fouling of heat exchangers Introduction Basic consideration Effect of fouling on heat transfer on pressure drop Design of HX subject to fouling Cleanliness factor (CF) & Percent over surface (OS) Cost of fouling Types of fouling Ways to minimize fouling effect Reference: Ch.6 Kakac book, 3ed. Edition Symbols uses ′′ ′′ 1 퐴표 퐴표푅푓푖 1 푅푓표 = + + 푅푤퐴표 + + Incropera 푈표 ℎ푖퐴푖휂푖 휂푖퐴푖 ℎ표휂표 휂표 1 퐴표 퐴표푅푓푖 1 푅푓표 Kakac = + + 푅푤퐴표 + + 푈표 ℎ푖퐴푖휂푖 휂푖퐴푖 ℎ표휂표 휂표 ′′ 2 푅푓푖 is the fouling factor for interior surface [m .K/W] ′′ 2 푅푓표 is the fouling factor for the exterior surface [m .K/W] 휂표 is the outside surface overall efficiency 휂푖 is the inside surface overall efficiency Rw is the wall thermal resistance [K/W] ln (푟 Τ푟 ) 푅 = 표 푖 푤 2휋푘퐿 Inside surface and outside surface fouling Definition of Uc , Ac and Uf and Af Based on outside area If Qc and Qf is the same, then 푄푐 = 푈푐퐴푐Δ푇푚 Clean HX 푈푓퐴푓 = 푈푐퐴푐 푄푓 = 푈푓퐴푓Δ푇푚 Fouled HX 푈푐퐴푐 1 ′′ 1 퐴표 1 퐴푓 = = 푈푐퐴푐 + 푅푓푡 = + 푈푓 푈푐 푈푐 ℎ푖퐴푖 ℎ표 퐴푓 ′′ 푅′′ 퐴 = 1 + 푈푐푅푓푡 1 퐴표 푓푖 표 ′′ 1 1 ′′ 퐴푐 = + + 푅푓,표 + = + 푅푓푡 푈푓 ℎ푖퐴푖 퐴푖 ℎ표 푈푐 퐴푓 > 퐴푐 푚2퐾 푅′′ 푛 푓 푊 ′′ The area of fouled heat 푅푓,푖퐴표 푅′′ = + 푅′′ exchanger is greater than the 푓,푡 퐴 푓,표 푖 area required for cleaned 1 1 ′′ heat exchanger = + 푅푓푡 푈푓 푈푐 Effect of fouling on heat transfer area 퐴푓 ′′ = 1 + 푈푐푅푓푡 퐴푐 ′′ 푅푓푡 As Uc increases the percentage increase of the area will increase Percentage increase in the area is % 푎푟푒푎 푛푐푟푒푎푠푒 = 100 ∗ 푈푐푅푓 Effect of fouling Typical fouling resistance for Shell and tube heat Effect of fouling on heat transfer exchangers For example for liquid to liquid heat exchange 푚2퐾 푅 = 7.9 ∗ 10−4 푓푡 푊 Effect of fouling on heat transfer 1 1 1 ≈ + 푈푐 ℎ푖 ℎ표 Assuming AoyAi and Rwy0 1 1 ′′ = + 푅푓푡 푈푓 푈푐 hi=1000, ho=1000, -4 Rft=6.5*10 Uc=500, Uf=377.4 퐴푓 ′′ = 1 + 푈푐푅푓푡 =1.325 퐴푐 Heat transfer area increase= (Af-Ac)*100=32.5 % Heat transfer area could be doubled or more due fouling Relation between friction factor f and friction coefficient Cf friction factor f friction coefficient Cf 푓 = 4 퐶푓 In kakac Book use of friction coefficient with the symbol f Replace f by f/4 Relation between friction factor f and friction coefficient Cf Kakac symbols Replace f by f/4 We get 퐿 푢2 Δ푃 = 푓 휌 푚 퐷 2 f is friction factor which can be found from Moody diagram Effect of fouling Effect of fouling on pressure drop • more heat exchangers are removed from service due excessive pressure drop than to meet heat transfer requirements. • In tubular heat exchangers, fouling increase surface roughness and reduce inside diameter and increase the outside diameter 2 Pressure drop due 퐿 푢푚 Δ푃 = 4푓 휌 major losses 퐷 2 Effect of fouling on pressure drop Pressure drop due major losses Assume mass flow rate is the same for clean For clean case and fouled case 2 퐿 푢푐 푚ሶ = 푚ሶ Δ푝푐 = 4푓푐 휌 푓 푐 푑푐 2 2 2 For fouled surface 푑푐 푢푐 = 푑푓 푢푓 2 or 퐿 푢푓 Δ푝 = 4푓 휌 2 푓 푓 푢푓 푑 푑푓 2 푐 = 2 푢푐 푑푓 Ratio 2 Then Δ푝푓 푓푓 푑푐 푢푓 = 5 Δ푝 푓 푑 푢 Δ푝푓 푓푓 푑푐 푐 푐 푓 푐 = Δ푝푐 푓푐 푑푓 Effect of fouling on pressure drop 1 퐴표 퐴표푅푓푖 1 푅푓표 We have = + + 푅푤퐴표 + + 푈표 ℎ푖퐴푖휂푖 휂푖퐴푖 ℎ표휂표 휂표 Wall thermal resistance 퐴표ln(푟표Τ푟푖) 푑표 ln 푑표Τ푑푖 푅푤퐴표 = = 2휋푘퐿 2푘 2푘푓푅푓 = ln(푑푐Τ푑푓) 푑푐 For fouling of diameter df (−2푘푓푅푓Τ푑푐) Thermal resistance due 푑푓 = 푑푐푒 to fouling (internal flow) Fouling thickness tf 푑푐ln(푑푐Τ푑푓) 푅푓 = 2푘 2푘푓푅푓 푓 푡 = 0.5 푑 1 − exp − 푓 푐 푑 kf is the thermal conductivity 푐 of the fouling material Inside the pipe fouling Clean pipe diameter dc Fouled diameter df Due to less flow area, the velocity will increase 2 2 퐴푟 휋푑푓 Τ4 푑푓 = 2 = 2 퐴푐 휋푑푐 Τ4 푑푐 2푡푓 = 푑푐 − 푑푓 푑 A is the 푑푐 푓 r 푡푓 = − remaining area 2 2 5 푑 = 푑 푒(−2푘푓푅푓Τ푑푐) Δ푝푓 푓푓 푑 푓 푐 = 푐 Δ푝푐 푓푐 푑푓 2푘푓푅푓 푡푓 = 0.5 푑푐 1 − exp − 푑푐 Effect of fouling on pressure drop 2푘 푅 푓 푓 퐴 휋푑2Τ4 푑2 푡푓 = 0.5 푑푐 1 − exp − 푟 푓 푓 푑푐 = 2 = 2 퐴푐 휋푑푐 Τ4 푑푐 2 5 −4 푚 퐾 Δ푝푓 푓푓 푑푐 푅푓 = 4 ∗ 10 = 푊 Δ푝푐 푓푐 푑푓 Correct Equation (6.10b) in your textbook In the book Correct form 푑 ln(푑 Τ푑 ) 푐 푐 푓 6.10b 푅푓 = 2푘푓 Typical value for fouling resistances involving use of water Kakac Book, 2nd edition Corrections for Table 6.11 Cleanliness Factor CF 푈푓 4 퐶퐹 = 푅푓푡 ∗ 10 푈푐 1 1 = + 푅푓푡 푈푓 푈푐 푈푐 = 1 + 푈푐푅푓푡 푈푓 푈푓 1 퐶퐹 = = 푈푐 1 + 푈푐푅푓푡 1 푈 푅 = − 1 푐 푓푡 퐶퐹 1 − 퐶퐹 푅푓푡 = 푈푐퐶퐹 Percent Over Surface In a shell-and-tube heat exchanger, the additional surface can be provided either by increasing the length of tubes or by increasing the number of tubes (hence the shell diameter). Such a change will affect the design conditions such as flow velocities, number of cross passes, or baffle spacing. Therefore, the new design with the increased surface should be related to achieve optimum conditions Kakac, 3ed edition, Ch.6 Example 6.1 continue Example 6.1 continue Example 6.1 continue Example 6.1 continue Cost of fouling Added cost due to fouling: 1-Increased capital expenditure 2-Increased maintenance cost 3-Loss of production 4-Energy losses Increased of capital cost due to : ❖Increase of heat transfer area required ❖Duplicate heat exchangers may have to be installed in order to ensure continuous operation ❖High cost materials such as titanium, stainless steel graphite may be required. Types of fouling No Type Examples 1 Particulate Accumulation of solid particles Unburnt fuel ashes. Dust on Fouling air cooled condenser 2 Crystallization Crystal formation of salt due Calcium and magnesium fouling heating and cooling of a stream carbonate, silicates and phosphates 3 Corrosion Heat transfer surface interaction Fuel sulfur and vanadium fouling with the stream producing corrode oil fired boilers corrosion on the surface 4 Bio-fouling Due to growth of material of Micro-organisms such as biological origin on heat transfer bacteria, algae and molds. Or surface. sea weed and water weeds(macrobial fouling) 5 Chemical Chemical reaction not with heat Polymerization and cracking reaction fouling transfer surface but within the and coking of hydrocarbons stream In practice fouling can take place due to several types or may complement each others 1- Particulate/Sedimentation Fouling: Sedimentation occurs when particles (e.g. dirt, sand or rust) in the solution settle and deposit on the heat transfer surface. Like scale, these deposits may be difficult to remove mechanically depending on their nature. 2- Scaling/Crystallization Fouling: Scaling is the most common type of fouling and is commonly associated with inverse solubility salts such as calcium carbonate (CaCO3) found in water. Reverse solubility salts become less solute as the temperature increases and thus deposit on the heat exchanger surface. Scale is difficult to remove mechanically, and chemical cleaning may be required. http://www.hcheattransfer.com/fouling1.html 3- Corrosion Fouling: Results from a chemical reaction which involves the heat exchanger surface material. Many metals such as copper and aluminum form adherent oxide coatings which serve to passivate the surface and prevent further corrosion. Metal oxides which are corrosion products exhibit quite a low thermal conductivity and even relatively thin coatings of oxides may significantly affect heat exchanger performance. 4- Biological Fouling: Occurs when biological organisms grow on heat transfer surfaces. It is a common fouling mechanism where untreated water is used as the coolant. Problems range from algae to other microbes such as barnacles and zebra mussels. During seasons when these microbes are said to bloom, colonies several millimeters deep may grow across the surface within hours, impeding circulation near the surface wall and impacting heat transfer. 5- Chemical Fouling: Fouling from chemical reactions in the fluid stream which result in the deposition of material on the heat exchanger surface. This type of fouling is common for chemically sensitive materials when the fluid is heated to temperatures near its decomposition (degradation) temperature. Coking of hydrocarbon material on the heat transfer surface is also a common chemical fouling problem Freezing Fouling: Occurs when a portion of the hot stream is cooled to near the freezing point of one of its components. An example in refineries is when paraffin solidifies from a cooled petroleum product. Another example is freezing of polymer products on the heat exchanger surface. Predication of fouling 푑푅푓 = 휙 − 휙 d is the deposit rate 푑푡 푑 푟 r is the removal rate A-Linear behavior If (d -r) is constant then 푅푓 = (휙푑 − 휙푟) 푡 B-Falling rate When the deposition rate is inversely proportional with the fouling layer thickness C-Asymptotic behavior Fig. 6.3 When d is constant and r is proportional to the fouling thickness. Soft fouling D-Periodic This behavior occurs in cooling towers due to changes in operation and blowdown C-Asymptotic behavior Assuming the deposit to be constant and the removal to be proportional to the fouling ∗ −푡Τ휃 푅푓 = 푅푓(1 − 푒 ) θ is the time constant which shows how quickly ∗ the fouling reaches the asymptotic value 푅푓 Rf ∗ 푅푓 ∗ 0.63 푅푓 휃 t Tables for fouling factors Tables for fouling factors Tables for fouling factors Ways to Minimize fouling effects Fouling tendencies depends on the type of heat exchanger and the fluids.
Details
-
File Typepdf
-
Upload Time-
-
Content LanguagesEnglish
-
Upload UserAnonymous/Not logged-in
-
File Pages66 Page
-
File Size-