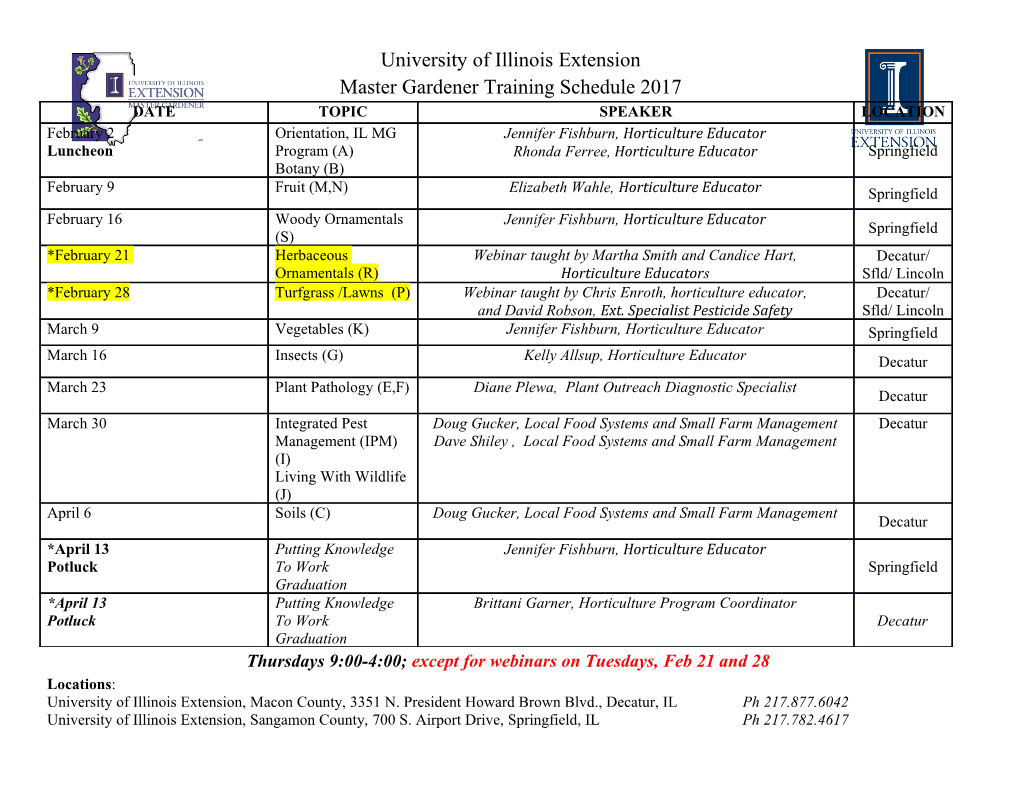
Journal of Industrial Technology • Volume 15, Number 4 • August 1999 to October 1999 • www.nait.org Volume 15, Number 4 - August 1999 to October 1999 Effects of Tool Diameter Variations in On-Line Surface Roughness Recognition System By Dr. Mandara D. Savage & Dr. Joseph C. Chen KEYWORD SEARCH Machine Tools Manufacturing Materials & Processes Quality Control Research Reviewed Article The Official Electronic Publication of the National Association of Industrial Technology • www.nait.org © 1999 1 Journal of Industrial Technology • Volume 15, Number 4 • August 1999 to October 1999 • www.nait.org Effects of Tool Diameter Variations in On-Line Surface Roughness Dr. Mandara D. Savage, CSIT was awarded his doc- toral degree in Industrial Technology at Iowa State University in August 1999. Dr. Savage has a Mas- ters of Science degree in Manufacturing Engineer- Recognition System ing Technology from the University of Memphis and a Bachelor of Science degree in Industrial Tech- By Dr. Mandara D. Savage & Dr. Joseph C. Chen nology specialized in electronics from the Univer- sity of Arkansas at Pine Bluff. Recently, he received the Silvius Wolansky doctoral fellowship award. Surface roughness is harder to attain machining process is taking place. This His research interests are in machine tool dynam- ics, fuzzy control, and human factors engineering. and track than physical dimensions are, vibration information could be a key because relatively many factors affect factor in the development of the on-line surface roughness. Some of these real-time surface roughness recognition factors can be controlled and some system. Therefore, it is important to cannot. Controllable process param- determine whether the tool diameter eters include feed, cutting speed, tool and the interaction of the feed rate geometry, and tool setup. Other affect the surface roughness and factors, such as tool, workpiece and vibration response. machine vibration, tool wear and degradation, and workpiece and tool Purpose of Study material variability cannot be con- The goal of this research is to evaluate Dr. Joseph C. Chen, PE is an associate professor in the Department of Industrial Education and Tech- trolled as easily (Coker & Shin, 1996). the effects of different tool diameters nology at Iowa State University. Recently, he re- The surface parameter used to toward the development of an on-line ceived Early Achievement in Teaching Award from the Iowa State University. His research interests evaluate surface roughness in this study real-time surface roughness recognition are in cellular manufacturing systems, machine is the Roughness Average, Ra. This system. This goal will be achieved in tool dynamics, and intelligent control as it relates to neural networks and fuzzy control. parameter is also known as the arith- three sub-goals. metic mean roughness value, arithmetic 1.The first sub-goal is to determine Introduction average (AA), or centerline average if tool diameter affects the surface Metal cutting is one of the most (CLA). Ra is recognized universally as roughness Ra of machined significant manufacturing processes the commonest international parameter workpieces produced in a vertical (Chen & Smith, 1997) in the area of of roughness, as defined by the follow- machining center. material removal. Black (1979) defines ing equation: 2.The second sub-goal is to deter- metal cutting as the removal of metal mine if tool diameter affects the from a workpiece in the form of chips vibration of the workpiece during in order to obtain a finished product (1) machining. with desired attributes of size, shape, 3.The final sub-goal is to determine and surface roughness. Drilling, where L is the sampling length, and y if the process characteristics of sawing, turning, and milling are some is the ordinate of the curve of the tool diameter and feed rate have of the processes used to remove profile, the arithmetic mean of the an interaction effect on Ra and/or material to produce specific products of departure of the roughness profile from workpiece vibration (Vi). high quality. the mean line (Lou, 1997). The quality of machined compo- The goal of the researchers is to Experimental Setup nents is evaluated by how closely they develop a system that evaluates surface and Signal Processing adhere to set product specifications of roughness on-line and in “real time”; The experimental setup of this study is length, width, diameter, surface finish, however, to develop this system shown in Figure 1. All machining was and reflective properties. High speed precisely, the key factors related to done in a Fadal VMC-40 vertical turning operations, dimensional surface roughness during the machine machining center with multiple tool- accuracy, tool wear, and quality of process must be identified. These change capability. This machine is surface finish are three factors that factors include feed rate, spindle speed, capable of three-axis movement (on x, manufacturers must be able to control depth of cut of the process, tool and y, and z planes). Programs can be (Lahidji, 1997). Among various workpiece materials, and so on. In developed in the VMC cpu, or down- process conditions, surface finish is addition, the dynamics of the machin- loaded from a 3 ½” diskette or a data central to determining the quality of a ing process generate vibration between link. A stylus profilometer was used to workpiece (Coker and Shin, 1996). the tool and workpiece while the measure the surface roughness. This 2 Journal of Industrial Technology • Volume 15, Number 4 • August 1999 to October 1999 • www.nait.org surface roughness measurement device was represented in the circuit during following equation allows the three is the most widely used instrument in the switched phase of the proximity average vibration data to be calculated: industry and research laboratories sensor. This signal was sent to the A/D because it is fast, consistent, easy to board on a channel separate from that interpret, and relatively inexpensive used for the accelerometer signal. (Mitsui, 1986; Shinn, Oh & Coker, A C program was written specifi- (2) 1995). In addition, stylus profilometers cally for calculating vibration and are used as a standard for comparing proximity data produced by the acceler- where k represents the total number of most of the newly-invented surface ometer and proximity sensor. The data in each revolution (as indicated in roughness measuring instruments or program was used to convert the analog Figure 2). For example, if i = 1, then techniques. This instrument uses a binary data from each channel of the the Vi is calculated through the vibra- tracer or pickup incorporating a converter into decimal form. Microsoft tion data points from point number 0 to diamond stylus and a transducer able to Excel was then used to graph and point number k (to have a total of k generate electrical signals as it moves display the decimal data by channel. data in one revolution). Vibration (Vi) across the surface to be measured. The Figure 2 shows an example of the is measured in units of voltage (as is electrical signals are then amplified, proximity and accelerometer data reflected in Figure 2). converted from analog to digital form, collected from a trial process using a A minimum of seven Ra values processed according to an algorithm, 1.00” diameter tool at a feed rate of 20 was collected from each of the nine and then displayed. The measurement inches per minute (ipm). The square workpieces after machining. The has a high resolution and a large range wave line represents the revolution median three values were used in the that satisfactorily measures the rough- proximity data, the erratic line repre- analysis. ness of most manufactured surfaces. sents the vibration data, and the arrow The stylus profilometer does have line indicates the range of one revolu- Experimental Design some limitations. These include long tion. The average of all these absolute As mentioned earlier, this study seeks periods of time needed to scan large values from the vibration data was to evaluate whether difference of tool areas, a restriction to use off-line, and ascertained for statistical analysis. diameter affects the development of a difficulty in measuring non-flat Three average vibration values were surface roughness recognition system. surfaces (Shin, Oh, & Coker, 1995). collected for this experiment. The When determining the parameters for Vibration and proximity data were collected using a 353B33 accelerom- eter and a Micro Switch 922 Series 3- wire DC proximity sensor. The accelerometer was used to collect vibration data generated by the cutting action of the tool. The proximity sensor was used to identify the rota- tions of the spindle during cutting. The proximity information was graphed CNC along with the accelerometer data, Machine allowing for the identification of Center PCB Battery Power Unit vibrations produced during different Proximity Sensor phases of the cutting sequence. Data Vise from both sensors were converted from Accelerometer Workpiece analog to digital signals through an Sensor Omega DAS-1600 A/D converter. The A/D converter-output was connected to a 486 personal computer via an I/O interface. Two power supplies were used. A model 480E09 ICP sensor power unit was used to amplify the signal from the accelerometer. This amplified signal was then sent to the A/D board. The second power supply was used to power the proximity sensor and A/D Board circuitry. The proximity sensor 486 Personal Computer required a minimum of 5 volts for proper operation. The 5-volt signal Figure 1. Experimental Setup 3 Journal of Industrial Technology • Volume 15, Number 4 • August 1999 to October 1999 • www.nait.org testing this effect, spindle speed, depth Accelerometer Vibration/Rotation 1 Rotation of cut, and type of work material 5 0.45 remained constant. Three tool diam- eters were evaluated independently of 4 0.35 tool design.
Details
-
File Typepdf
-
Upload Time-
-
Content LanguagesEnglish
-
Upload UserAnonymous/Not logged-in
-
File Pages7 Page
-
File Size-