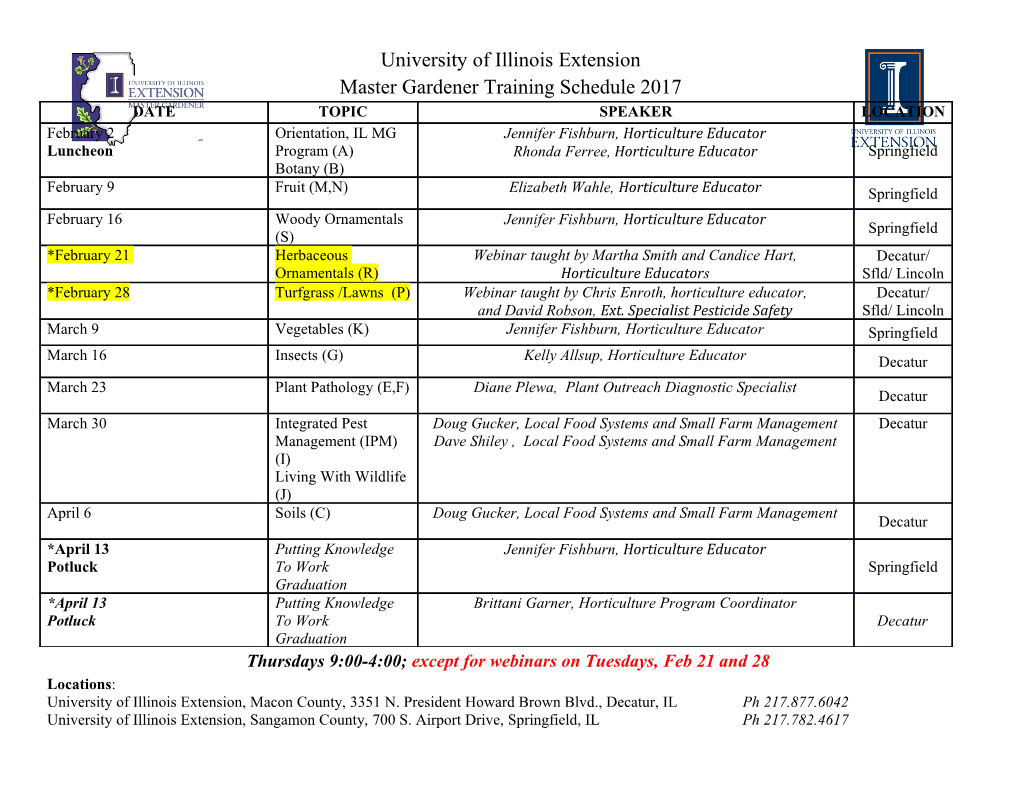
NASA CR-145192 STUDY OF ADVANCED COMPOSITE STRUCTURAL DESIGN CONCEPTS FOR AN ARROW WING SUPERSONIC CRUISE CONFIGURATION Task III Final Report Boeing Commercial Airplane Company Preliminary Design Department January 1978 - STUDY OF ADVANCED jl 2O112- [(NA-SA-CR-145192)!COMPOSITE STEUCTUAL t-ESIGNCONOETS FOE- AN ARROW WING SUPEESONIC;CRUISE CONFIGURATIOt4,­ 3 .Final Report- (Boejhg4 Commetcil UncIas TASK 11905 Airplane Co..'S'eattie) 381" P HC.-4A-17/MF. A;O1 G3i/-5 Prepared under contract NAS1-1 2287 for Langley Research Center NATIONAL AERONAUTICS AND SPACE ADMINISTRATION Hampton, Virginia 23665 1A -'s Rig, 1 Report No 2. Government Accesston No 3 Recipient's Catalog No NASA CR-145192 1 4 Title and Subtitle 5 Report Date STUDY OF ADVANCED COMPOSITE STRUCTURAL DESIGI January 1978 CONCEPTS FOR AN ARROW WING SUPERSONIC 6 Performing Organization Code TRANSPORT CONFIGURATION D6-42438-4 7. Author~s) 8 Performing Organization Report No Preliminary Design-Department 10 Wok ura No­ 9. Performing Organization Name and Address Boeing Commercial Airplane Company I Contract or Grant No. P.O. Box 3707 ' Seattle, Washington 98124' NAS 1-12287 13. Type of Report and Period Covered 12. Sponsoring Agency Name and Address National Aeronautics and Space Administration Task III Eil Report Langley Research Center 14 Sponsoring Agency Code Hampton, Virginia 23665 IS. Supplementary Notes Contract Monitors: James C. Robinson.and E. Carson Yates, Jr. NASA Langley Research Center, Hampton, Virginia 16 Abstract A structural design study was-conducted to assess the relative merits of structural concepts using advanced composite materials for an advanced supersonic aircraft cruising-at Mach 27. The configuration and structural arrangement developed during Task I and II of the study, previously reported in NASA CR-i32576, was used as the baseline configuration. Allowable stresses and strains were established for boron and advanced graphite fibers based on projected fiber properties available in the next decade. Structural concepts were designed and analyzed using graphite polyinide and boron polyimide, applied to stiffened panels and conventional sandwich panels. The conventional sandwich panels were selected as the structural concept to be used on the wing structure. The upper and lower surface panels of the Task I arrow wing were redesigned using high-strength graphite polyimide sandwich panels over the titanium spars and ribs. The ATLAS computer system was used as the basis for stress analysis and resizing the surface panels using the loads from the Task II study, without adjustment for change in aeroelastic deformation. The flutter analysis indicated a decrease in the flutter speed compared to the baseline titanium wing design. The flutter speed was increased to that of the titanium wing, with a weight penalty less than that of the metallic airplane. 17. Key Words (Suggested by Author(sl) 18. Distribution Statement Arrow Wing, Supersonic Cruise SCAR Technology Unclassified - Unlimited NASA SCAT 15-F Advanced Composites 19. Security Classil. (of this report) 20. Security Classif. (of thts page) 21. No of Pages 22 Price' Unclassified Unclassified 383 $13.00 'For sale by the National Technical Information Service. Springfield. Virginia 22161 CONTENTS Page INTRODUCTION .1............................ I-1 1 MATERIAL PROPERTIES ..... ..................... .......... 1' 2 ALLOWABLES .......... .................. ......... 25 3 CONCEPT DESIGN AND MATERIAL SELECTION ..... ............... ... 49 4 PANEL DESIGN .............. ............................. 95 5 THEORETICAL-TO-ACTUAL MASS FACTORS ...... ................ .. 139 6 COMPOSITE ANALYSIS AND DESIGN ....... ................... .. 157 7 REVISION OF MATHEMATICAL MODEL.......... .. ........... ... 188 8 FLUTTER ANALYSIS ........... .......................... .. 261 9 FINAL WEIGHT ANALYSIS ................ ... .............. ... 323 10 AERODYNAMIC HEATING ANALYSIS ......... ................... 338 ii INTRODUCTION This document presents a detailed account of Task III of a study conducted by the Boeing Commercial Airplane Company as a part of the NASA Supersonic Cruise Aircraft Research program. The principal overall objectives of the study were to assess the relative merits of various concepts and materials suitable for an advanced supersonic aircraft cruising at Mach 2.7, to select the structural approaches best suited for the Mach 2.7 environment, and to provide construction details and structural mass estimates based on in-depth structural design studies of representative wing and fuselage structures. Earlier work in Tasks I and II of this study comprised the following activities: (1) detailed analysis and refinement of the aircraft configuration; (2) evaluation of alternate structural arrangements and selection of an arrangement for detailed analysis and design studies; (3) evaluation and-selection of materials and concepts representative of a 1975 technology level; (4) detailed structural analysis and design and structural mass analysis utilizing the 1975 materials and concepts. In Task III the detailed structural analysis and the design and mass analysis have been repeated with advanced concepts and materials that are expected to be available in the 1986 time'period. The airplane configuration on which the structural analysis was conducted is an arrow-wing concept representative of a 1975 technology level. It was derived from a configuration presented by NASA (see reference 1-1), and is similar to the'Model 969-336C that was studied during the National SST Program (ref. 1-2). A detailed multidisciplinary analysis-of the configuration was conducted during Task.I of the study, and further modifications and refinements were introduced. The resulting con­ figuration,designated as Model 969-512B is shown in figure,-l. Geometric data and other characteris­ tics are listed in table -1. The wing structure that was selected for detailed analysis and design in Task II consisted of a multispar internal structure with aluminum brazed titanium sandwich panels for the wing surfaces, except for a machined skin concept on the lower surface of the main wing box. The fuselage structure consisted of skin stringer construction. Ti-6A1-4V alloy was used as the primary structural material throughout. A single basic finite element model of the structure was developed for aeroelastic loads, stress and flutter analyses, containing approximately 2000 nodes, 4200 elements and 8500 active degrees of freedom. Analyses were performed by an integrated structural analysis and design system interfaced with loads and flutter analysis systems. The elements in the wing covers were resized using an automated resizing module in the integrated system, with, convergence, measured in terms of total mass change, occurring in three cycles. Nine flutter analyses were conducted to evaluate a series of stiffness changes to remedy a flutter deficiency in the strength design. Stiffness changes were based on engineering judgment and experience from the National SST Program. The resulting configuration has a maximum taxi gross mass of 340 200 kg (750 000 lbm) and a pay­ load of 22 200 kg (49 000 Ibm), representing 234 passengers in tourist accommodations, and a cruise -Machnumber of 2.7. The structure, stability and control characteristics, and systems meet the appropriate requirements of Federal Aviation Regulations, Part 25, and the Tentative Airworthiness Requirements for Supersonic Transports. A detailed account of the work performed in Tasks I and HIis presented in reference I-1; for a more condensed summary see reference 1-3. I-1 The configuration and structural arrangement developed for the titanium structure were used without modification in the subsequent investigation discussed in this report. Allowable stresses and strains, based on estimated fiber properties to be available in the next decade, were established for advanced composite materials using boron and graphite fibers. Stiffened panel and conventional sandwich panel concepts were designed and analyzed, using graphite/polyimide and boron/polyimide materials, and the conventional sandwich panel was selected as the structural concept to be used in the modified wing structure. Upper and lower surface panels of the arrow wing structure were then redesigned, using high strength graphite/polyimide sandwich panels, retaining the titanium spars and ribs that had been designed in the prior study. The ATLAS integrated analysis and design system was used for stress analysis and automated resizing of surface panels, using the design loads that were developed in the prior study of the metallic structure. For the present study properties of candidate advance composite materials were estimated for a 1986 time period, based on assumptions regarding development work to be accomplished in the intervening time period. Estimated material properties were then used in structural concept design studies, and in concept and material evaluation and selection. Following material and concept selection, a finite element model of the complete structure was defined retaining the structural arrangement and finite element geometry from the prior study of the metallic structure. Since supersonic cruise aircraft tend to be large and flexible, aeroelasticity is a major design considera­ tion, and realistic aeroelastic considerations based on analysis of finite element structural models and sophisticated aerodynamic loading analysis are required, even in a preliminary design study of such a vehicle. Strong interaction
Details
-
File Typepdf
-
Upload Time-
-
Content LanguagesEnglish
-
Upload UserAnonymous/Not logged-in
-
File Pages340 Page
-
File Size-