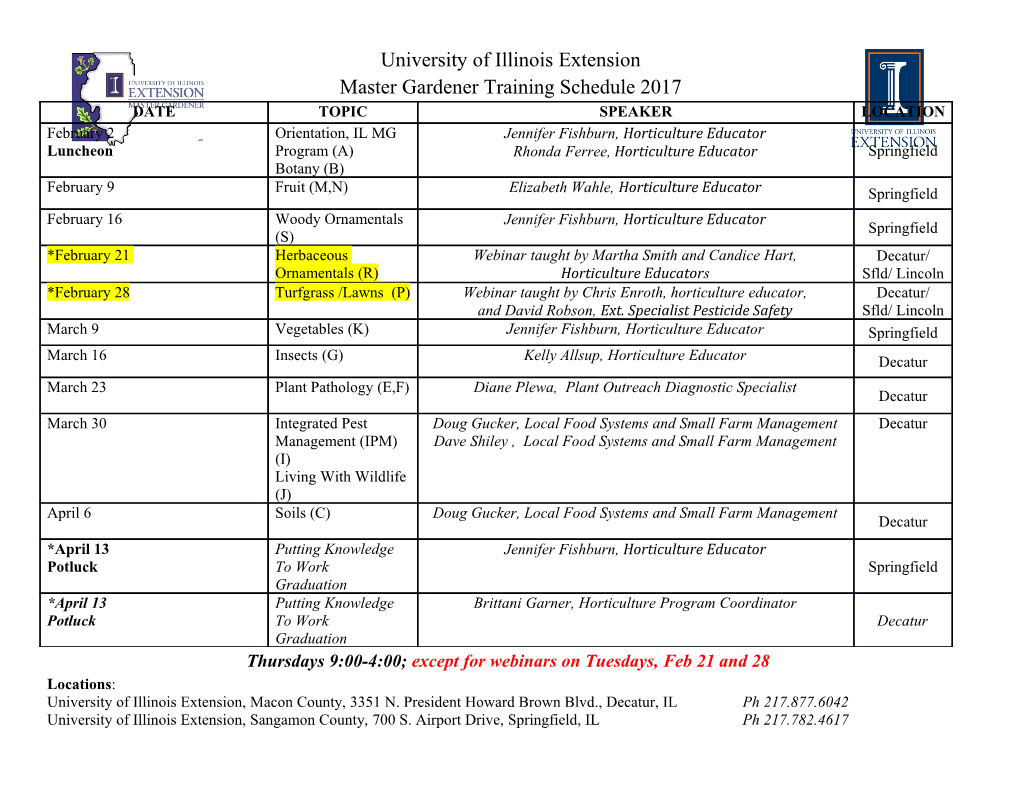
Short circuiting the electrodes, the inductance of the system was 872 nH. A Rogowski loop around one electrode was used lor current measurement as well as a discharge monitor. The plasma radiation was collected by a quartz lens set on the major axis of the system (figure 1). The spectroscopic measurements were carried out with a 2m focal length. Ebert montage. Cari-Zciss spectrograph. The Fig. 2 - Rogowski loop signal (hor. 5 usecdiv. instrument dispersion was 7.4 vert. 5mV-drv. Ãmm. X-ray film was used successfully to record the near UV spectra. A usual spectrogram has 80 shots with an 80 ^ m entrance slit. Lines from Aril and Arm were used as standard Iines[S]. The films were measured in a MEM 00 Carl-Zeiss microdensitometer. 3. RESULTS AND DISCUSSIONS Initial observations without pre-ionization showed typical delayed discharges behavior for fixed pressure within operation range. On the other hand vanishing delays were observed when the radio frequency source for the pre ionization was applied. The previous production of this resistive plasma show to be important to obtain reproductive discharges with precise control on their start up. Typical discharge cunent is shown in figure 2. Within the operation pressure range the period of the ringing discharge and peak current remain around 16 usec and 14 kA. respectively. The decay time of the discharge was around LR- 165 .usec. The maximum current density was 3.0 kAcm- and total charge was 0.33 C. Results from magnetic probe measurements at 27 mTorr show a hollow plasma colunr -n T/dplar.; of the electrodes with 1.2 cm diameter and 1.7 kA cm*- current density at t- 2.Í nscc (t=Q is the beginning of the discharge). A fine powder of electrode material was produced by the discharge due to electrode erosion. This powder appeared as a thin layer deposited over the inner surface of discharge tube. Small spots, due to incidence of eroded material, were observed on the electrode support out of the discharge region. The contamination of the plasma by the impurities was clearfy observed with the spectroscopic measurements. 24 Fig. 3 - Emission spectra of Ar at different tilling pressures: 200 mTorr (upper) and 80 mTorr (lower/Inwer)l The figure 3 shows a recorded film at 200 and 80 mTorr filling pressure. From residual gas we obsenrd lined of Mü (3514.38A. 3491.54.4. 3476.75Â. 3249.80A, 3243.68A) and Arm (3318.88A. 3285.85.A. 3480.55.Ã). Stronger lines of Cul ( 3247.54A. 3273.96A) and Znl (3382.33A. 3302.59.4. 3344.38A) were observed as well. At these pressures, these lines are present in both spectrograms with small changes in their intensities. The lines of metallic elements are stronger at low pressure regime. The concentration of excited metallic species shows to be enhanced by energetic electron. 4. CONCLUSIONS A gas discharge in Z-Pinch with brass electrodes in .Argon was characterized by visible spectroscopy on the condition of current density and charge up to 3.0 kA cm- and 0.33 C. Reproducible discharges without delay were observed in the pressure range of 22-200 mTorr when radio frequency pre-ionization was used. Fine brass powder was produced by electrode erosion. In this condition, atoms ot Copper and Zinc were present in the plasma Spectral lines of residual gas indicated ions of .Ar- and .Ar*- in the plasma core. References 1 - Drawin. H.W.. Physica Script* 24. p:622-655, 1981: 2 - Bedilov. M.R. et all. Plasma Physics, ed. Skobel'tsyn. D.V.. Consultants Bureau, New York. p:84-91. 1968: 3 - Arad. R. et all. Rev. Sci. Instrum. 63 (10). p:5127-5131. 1992: 4 - Kayama, ME. et all. Proceeding of 1st Brazilian Conference on Plasma Physics. vol.m, p:205-209, 1991. 5 - Striganov. A.R. and SventitskiL N.S.. Table of Spectral Lines of Xeutral and Ionized Atoms. Plenum. New York. 1968. 25 A LOW ENERGY VACUUM ARC FOR COATING PURPOSES ll.Kellv#, A.Marquez*. A.Libertun, J.F.Martinez Laboratório lie Física del Plasma - INFIP (CONICET) Ciudatl Universitária Pab. I 1428 Buenos Aires Argentina # Member of the CONICET * Fellow of the CONICET Abstract Preliminary results on the coating characteristics produced with a low energy (3.3 kJ) pulsed plasma arc are reported. Introduction Since a long time ago. low pressure (or vacuum) plasma arcs have been employed to produce coatings' l\ In these devices a high current electrical discharge is generated between metal electrodes located in a vacuum (or low pressure) chamber, the current being conducted by a plasma consisting of ionized vapor of the electrode material. For currents typically below several kA. the production of plasma is concentrated in one or more minute "cathode spots". Each cathode spot produces an energetic plasma jet. which flows from the cathode surface with typical flow velocities of * 10 km/s. The material transfer of the cathode is considerable, typically 30 pg per coulomb. Coatings can then be produced by placing the substrate in any location where it will intercept part of the plasma jet. Although these devices (operating for long periods of time, -minutes, and with relatively low currents. -100 A) have already been developed to a commercial scale, it has been recently proposed the use of pulsed high current arcs'2-*\ in which extremely high deposition rates (for Al. - 100 fini/s) can be achieved. In this work preliminary results on coating characteristics obtained with a small energy pulsed plasma arc. which has been recently built, are reported. In this device the geometrical arrangement is such that, at the same lime, the substrate is the anode of the discharge. Experimental Apparatus and Procedure The arc was run hy discharging an electrolytic capacitor bank with C = 0.075 F. connected to a series inductor-resistor which critically damped the discharge. Two set of values were employed: a) L = 2 mH. R = 0.33 Q; and b) L = 0.091 mH. R = 0.1 £1 The vacuum chamber was a 25 cm long and 10 cm diameter stainless steel cylinder, through whose bases were introduced and facet! (he electrodes. The Ti or Al cathode was 15 mm in diameter and contained a central trigger electrode (1 mm titanium wire) for arc ignition. The anode was usually formed by three 1010 stainless steel rectangular pieces (15 mm long. 7 mm width and I mm (hick).which were fixed on a circular holder of diameter 25 mm. The anode was spaced 2 or 5 mm from the cathode. The chamber was pumped to a base pressure - 10s mbar with an oil diffusion pump. In several tests, where the aim was to synthesize TiN, the chamber was filled with nitrogen gas at a pressure in the range 0.2-4 mbar. The samples were usually polished and then degreased in CI4C prior to mounting in the chamber. In Fig. 1 a schematic drawing of the experimental apparatus is shown. The arc was ignited by applying a short (- us) high voltage pulse to the trigger electrode. The operating voltage was 300 V (= 3.4 kJ of stored energy), giving a current pulse with an 26 • Trigger Gas Inlet Cathode Anode Resistance Inductance HI- Capacitor Bank Pump —1 V Source Figure 1: Schematic diagram of the apparatus 1.2E+03 1.0E+03 8.0E+02- § 60E+02-|! 4.0E+02 2.0E+02 0.0E+00 10 20 30 40 50 60 70 time (ms) Figure 2: Arc current as a function of time for both sets of discharge parameters: a) L=2mH, R=0.33 rt,; b) L=0.091rnH, R=0.1/X 27 amplitude of 500 A. ami half-amplitude full-width duration of 35 ms for the case a), and 1000 A. 10 ms for the case b) (see Fig. 2). After arcing the samples were inspected visually. Some were subjected to a primitive adhesion lest employing an adhesive tape, in order to determine whether the coating could be easily detached. In several experiments the sample was weighted prior to and after arcing. The cathode was also weighted, but after 10-20 shots. To obtain the thickness of the obtained films, some of the samples were analyzed with a profiler, with a height resolution of = 0.005 |im and a scanning length of 6 mm. As this instrument determines thickness by comparing height differences, the samples were partially masked from the discharge to get a transition between the original and the coated surface. Results Although the samples had a rectangular shape, the coated region resulted almost circular, according to what it was expected from the apparatus geometry. For the longer discharge, employing the titanium cathode, ami for a 2 mm inter electrode gap, a series of shots varying from test to test the nitrogen pressure were performed. For pressures less than 0.2 mbar, no signs of TiN deposition were observed. At 0.2 mbar the outer rim of the anode was coated with TiN. which could be readily discerned by its gold colour. At 0.4 mbar the lateral extent of the TiN-coated region increased, forming an annular region of = 5 mm thickness encircling a plated central zone of diameter * 19 mm. For increasing pressures (0.6, 0.8. 1, 1.5 mbar) Jhe central zone was shifted into a inner golden region (whose intensity increased with the pressure) surrounded by a plated ring whose thickness tended to decrease with the pressure. Besides, the gold colour of the outer annulus was dimmed, until for the higher pressures it turned to be violet-like. At a pressure of 2 mbar the best coating was obtained: an intense golden circle of diameter 17 mm surrounded by I mm thick plated and violet-like rings.
Details
-
File Typepdf
-
Upload Time-
-
Content LanguagesEnglish
-
Upload UserAnonymous/Not logged-in
-
File Pages226 Page
-
File Size-