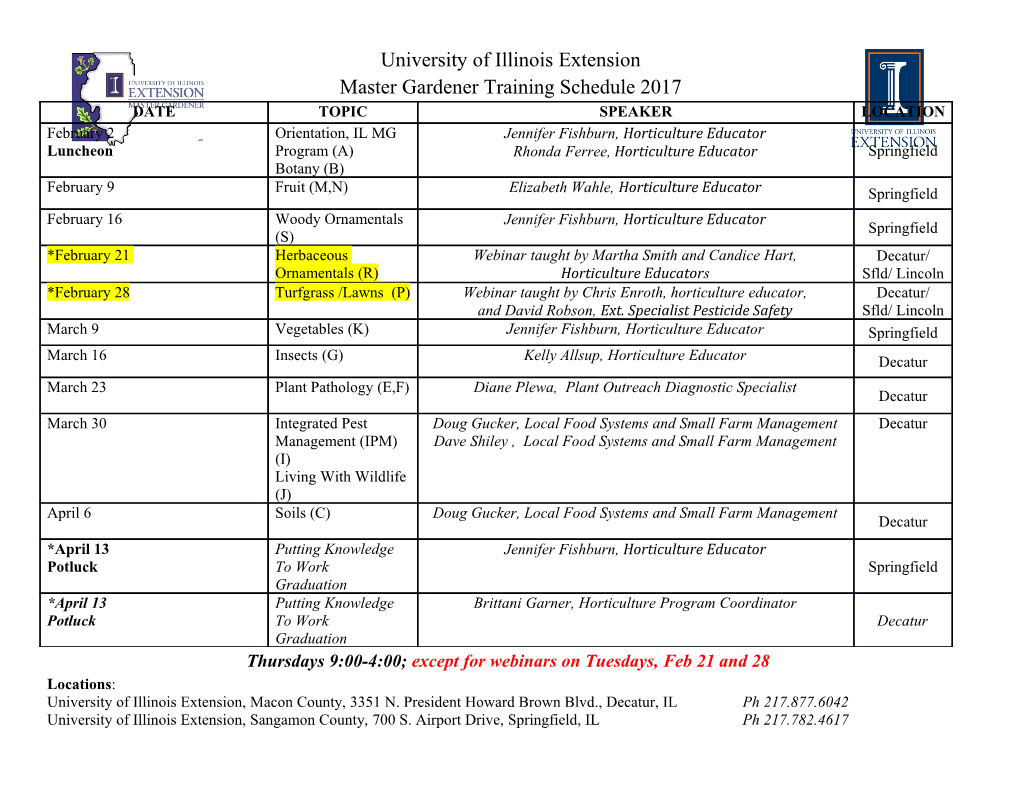
polymers Article Durability and Electrical Conductivity of Carbon Fiber Cloth/Ethylene Propylene Diene Monomer Rubber Composite for Active Deicing and Snow Melting Shuanye Han , Haibin Wei *, Leilei Han and Qinglin Li College of Transportation, Jilin University, Changchun 130025, China; hansy18@mails.jlu.edu.cn (S.H.); hanll18@mails.jlu.edu.cn (L.H.); liql1150142@163.com (Q.L.) * Correspondence: weihb@jlu.edu.cn Received: 8 November 2019; Accepted: 6 December 2019; Published: 10 December 2019 Abstract: To reduce the impact of road ice and snow disaster, it is necessary to adopt low energy consumption and efficient active deicing and snow melting methods. In this article, three functional components are combined into a conductive ethylene propylene diene monomer (EPDM) rubber composite material with good interface bonding. Among them, the mechanical and electrical properties of the composite material are enhanced by using carbon fiber cloth as a heating layer. EPDM rubber plays a mainly protective role. Further, aluminum silicate fiber cloth is used as a thermal insulation layer. The mechanical properties of EPDM rubber composites reinforced by carbon fiber cloth and the thermal behaviors of the composite material in high and low temperature environments were studied. The heat generation and heat transfer effect of the composite were analyzed by electrothermal tests. The results show that the conductive EPDM rubber composite material has good temperature durability, outstanding mechanical stability, and excellent heat production capacity. The feasibility of the material for road active deicing and snow melting is verified. It is a kind of electric heating deicing material with broad application prospects. Keywords: thermal behavior; multifunctional composites; mechanical properties; electrothermal properties; active deicing and snow melting; temperature durability 1. Introduction In most parts of the world, road ice and snow problems occur in winter, and various methods are adopted for snow melting and deicing, but the results are unsatisfactory. Every year, a large number of traffic accidents are caused by snow and ice disasters. At present, artificial and mechanical salt spraying are the main measures to protect against road icing. Various salt chemicals such as NaCl, MgCl2 [1] and potassium acetate [2] are used on the road. The method of salt spraying can melt snow and ice at the beginning of use. However, most of the salts used contain chloride ions, which have serious corrosive effects on steel [3] and concrete [4,5] in road infrastructure. Simultaneously, salt chemicals have a serious impact on the ecological environment around the road and groundwater [6–8]. In view of the problems of chemical deicing, to achieve the purpose of rapid and effective road deicing and snow melting that will not affect the ecological environment around the road, scholars have developed active snow and ice removal technologies. Existing active deicing and snow melting technologies mainly include the conductive asphalt mixture method, heat pipe method, geothermal energy deicing method, and the electric heating method. The conductive asphalt mixture method mainly adds conductive fillers such as steel fiber [9], steel slag [10], graphite and carbon fiber [11,12] to the asphalt mixture. In this way, the purpose Polymers 2019, 11, 2051; doi:10.3390/polym11122051 www.mdpi.com/journal/polymers Polymers 2019, 11, 2051 2 of 17 of reducing the electric resistance of the asphalt mixture is achieved. Then, the conductive asphalt concrete is heated by electric current or infrared heating [13,14], thereby realizing active deicing of the road. However, the mechanical properties of asphalt mixtures decrease due to the addition of conductive fillers. In addition, the electrical resistance value of the asphalt mixture with conductive filler is greater than that of conductive filler, resulting in low thermal efficiency. A faster heating rate can only be achieved when the input power is relatively large. This method takes a long time to achieve road snow melting and deicing, resulting in serious energy waste and a high cost of use. Heat pipe technology realizes the active snow melting and deicing of the road by embedding pipes in the road structure and introducing a heat flow into the pipes. Chen et al. [15] conducted a snowmelt test after laying heat pipes on the airport runway. The results proved that the heat pipe technology can achieve snow melting and deicing, which provided certain support for the actual construction design. Liu et al. [16] studied the effects of various factors such as wind speed, heating power, and buried spacing on the melting of electric heating tubes. However, pipeline laying had a certain impact on the structural layer of the road. There were high requirements for heat flow control and road construction during use. Geothermal energy is a clean energy source. Han et al. [17,18] controlled the geothermal heat pump system and the thermoelectric system to study the use of geothermal heat to achieve snow melting and the deicing of roads. Due to the limitation of geothermal energy and the low efficiency of thermoelectric conversion, it was impossible to melt snow in real time. Because the above active deicing methods have some defects, they have not been widely used. Conductive composite materials have developed rapidly in recent years, so the application of conductive composite materials on roads is considered. Active road deicing and snow removal can be realized by power on. In order to achieve efficient and fast road deicing and snow melting, the effective reduction of resistance value has been proven to be one of the key ways to improve electrical heating performance [19,20]. Carbon series materials have good electrical conductivity. Therefore, Chu et al. applied materials with excellent conductivity such as carbon nanotubes [21] and graphene-paper [22,23] to deicing applications. The effect of actual deicing is obvious, but materials such as carbon nanotubes and graphene are expensive. Currently, coverage of the large areas occupied by roads is not easy to achieve. In comparison, carbon fiber cloth is a material that has developed rapidly in recent years. The cost of carbon fiber cloth has been greatly reduced due to the improvement of carbon fiber preparation technology. Since carbon fiber cloth has the characteristics of low resistance and good durability, it has been studied in the preparation of electrodes [24] and in 3D printing heating materials [25]. Furthermore, the mechanical strength of carbon fiber cloth is high. It has been widely used in the mechanical properties of reinforced composite materials [26] and the reinforcement of bridges [27]. In view of the excellent mechanical and electrothermal properties of carbon fiber cloth, Lim et al. [28–31] added carbon fiber cloth directly to the concrete, and then heated concrete by electricity. The heat production rate of the carbon fiber cloth and the effect of ambient temperature on heat production efficiency were investigated. The results showed that the carbon fiber cloth can quickly heat up when the input power is small, and achieve the purpose of rapid deicing and snow melting. Previous studies proved that carbon fiber cloth has broad application prospects in road deicing and snow removal. However, the protection of carbon fiber cloth and the durability of carbon fiber cloth composite material were not considered. In this paper, a conductive ethylene propylene diene monomer (EPDM) rubber composite material with a three-layer structure was prepared using carbon fiber cloth as heat producing layer and sandwiched between a heat conducting layer of EPDM rubber and heat insulating layer of aluminum silicate fiber cloth. The effects of carbon fiber cloth on the mechanical and electrical properties of EPDM rubber were investigated. Combined with the environment in which the composite material was used on the road, the thermal behaviors of the composite material under a high temperature 60 ◦C environment and the durability of the material after cycling at 20 C and normal temperature were − ◦ analyzed. The heat generation uniformity and heat production effect of the composite material were studied. The results showed that the conductive composite material based on carbon fiber cloth has Polymers 2019, 11, 2051 3 of 17 the characteristics of high efficiency, reliability, durability, high mechanical strength and low cost in deicing and snow melting. It is a potential electric heating deicing material in many fields. 2. Materials and Methods 2.1. Materials Carbon fiber cloth used in this study was purchased from Shanghai Yuezi Industrial Co., LTD (Shanghai, China). The carbon fiber cloth is woven from 12 K carbon fiber precursors, with a carbon content of more than 98%, a thickness of 0.167 mm and a density of 300 g/cm3. Because of the good electrical conductivity of carbon fiber cloth, it was used as an electrical heating layer. Ethylene propylene diene monomer (EPDM) rubber (Sanhe Great Wall Rubber Co., LTD., Sanhe, China) with a density of 0.90 g/cm3 was used as a protective and bonding material for carbon fiber cloth. To transfer heat rapidly, graphite (Tianjin Dengke Chemical Co., LTD., Tianjin, China) with high thermal conductivity was added to EPDM rubber. The carbon content of graphite is more than 99.93% and the particle diameter is 6.5 µm. The addition of carbon black with a particle size of 40 nm and auxiliary materials (Kaiyin Chemical Co., LTD., Kaiyin, China) such as vulcanizing agent dicumyl peroxide to EPDM rubber improve the mechanical properties and durability of the composite material. The obtained thermally conductive EPDM rubber composite material was used as a heat transfer layer. The heat insulation layer was composed of aluminum silicate fiber cloth (Dacheng North Sealing Products Factory, Dacheng, China) with a low thermal conductivity of 0.035 W/(m K) and EPDM rubber. Finally, · the three-layer structure was vulcanized at high temperature and high pressure to obtain a conductive EPDM rubber composite material.
Details
-
File Typepdf
-
Upload Time-
-
Content LanguagesEnglish
-
Upload UserAnonymous/Not logged-in
-
File Pages17 Page
-
File Size-