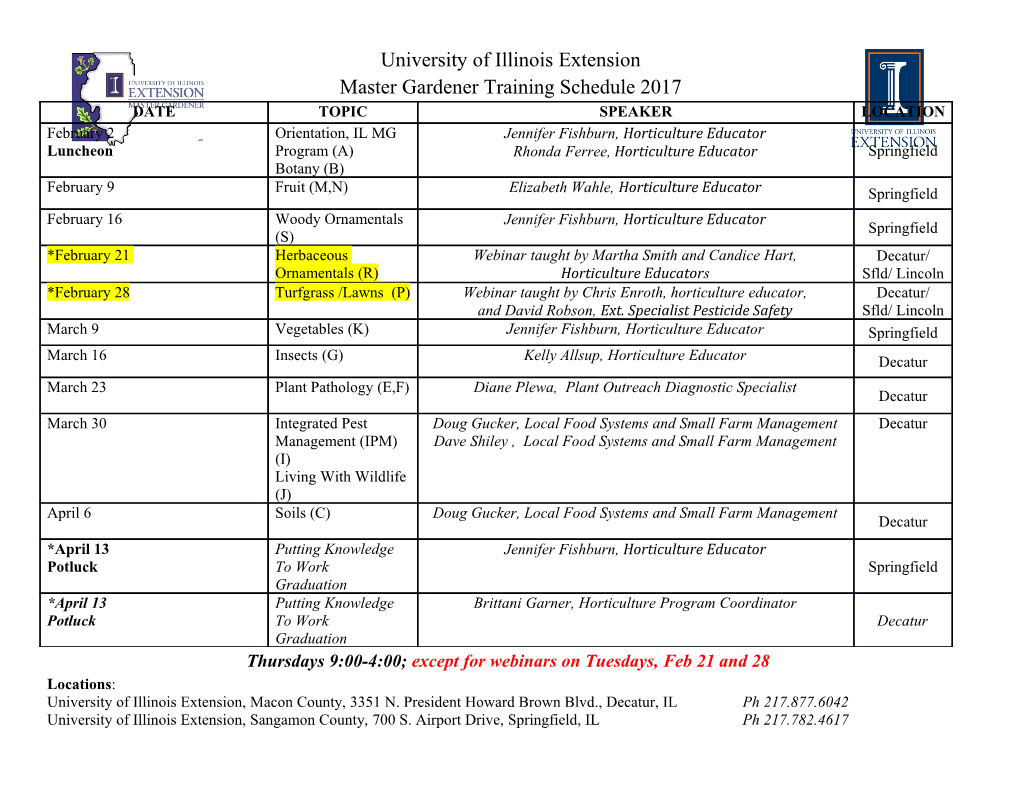
3,826,610 United States Patent Office Patented July 30, 1974 1. 2. 3,826,610 As component (c) of the mixtures according to the PULVERULENT MIXTURE FORTANNING RAW invention there may especially be mentioned the adducts ANMAL HIDES AND LEATHER of about 20 to 70 moles of ethylene oxide to higher Ernst Komarek, Leverkusen, and Heinrich Spahrkas, (C-C16) alkylphenols such as nonylphenol, dodecylphe Bergisch-Neukirchen, Germany, assignors to Bayer Ak nol and hexadecylphenol, to aralkylphenols, such as phe tiengesellschaft, Leverkusen, Germany nol, C1-C4-alkylphenols, o- and p-hydroxydiphenyl substi No Drawing. Filed June 15, 1972, Ser. No. 263,076. tuted by benzyl, methylbenzyl, dimethylbenzyl, or-methyl Claims priority, application Germany, July 8, 1971, benzyl or g-phenylethyl radicals, e.g. di-benzylphenol or P 21 34 070.5 the reaction product of o-hydroxydiphenyl with 1-3 moles Int, C. C14c 3/06, 9/02 O of styrene or higher (Co-C2) fatty alcohols, such as U.S. CI. 8-94.26 5 Claims lauryl alcohol, stearyl alcohol and oleyl alcohol. In the adducts, a small percentage of the ethylene oxide, say up ABSTRACT OF THE DISCLOSUIRE to about 5% by weight, can be replaced by propylene A pulverulent mixture for tanning hides and leather oxide. n the tanning mixtures of the invention these comprising (a) a chrome tanning agent, (b) a product of 5 adducts function as non-ionic emulsifiers. the chlorination of paraffin hydrocarbons of about 8-24 In some cases it has proved advantageous to employ carbon atoms and having a chlorine content of about 20 anionic auxiliaries (emulsifier), such as paraffinsulfonic 50% by weight, and (c) an adduct of about 20 to 70 moles acids, especially alkylbenzenesulfonic acids, for example of ethylene oxide to one mole of an alkylphenol, arylalkyl dodecylbenzenesulfonic acid, or their salts, additionally to 20 the non-ionic emulsifiers in the mixtures according to the phenyl or fatty alcohol. The mixture disperses, readily in invention. The ratio of the amounts of anionic auxiliaries water to form stable tanning emulsions which yield leath to the amounts of non-ionic emulsifiers is appropriately ers characterized by softness, smoothness and superior 1:1-0. grain characteristics. The use of the tanning mixtures according to the inven 25 tion provides a simplified procedure and results in tanning . The present invention relates to a new tanning mixture batches of constant quality being obtained. The chrome for animal hides and leather, to its production, and to its leathers obtainable by means of the tanning mixtures Se according to the invention are distinguished by outstand Chlorinated paraffins in the form of aqueous emulsions ing properties, especially by very soft handle, excellent have already been used in chrome tanning. In these known 30 smoothness and superior grain characteristics. Further processes, however, the aqueous emulsion of the chlori more, the chrome leathers manufactures in this way give nated hydrocarbons was first manufactured and was added particularly good evenness during subsequent aniline dye to the tanning bath separately from the tanning material, ing. Apart from the tanning, uniform fat liquoring over before or during the chrome tanning. Apart from the fact the entire cross-section of the leather, and optimum dis ... that these processes are complex, they display the dis 35 tribution of the natural grease of the hides to be tanned is advantage that because of the differences in batches of the achieved. chlorinated paraffin emulsions, caused by temperature and It was surprising that it is possible to manufacture, from time factors during the manufacture of the emulsions and chrome tanning materials and chlorinated paraffins pull especially during the compounding of the emulsions, varia verulent mixtures which on simple addition in the undis tions occurred in how the individual tanning batches 40 solved form to tanning liquors give stable tanning emul turned out. sions, because it would have been expected that as a result It is accordingly an object of the invention to provide of the extremely high electrolyte concentrations which tanning emulsions which produce uniform tanning results. occur when dispersing these mixtures in water no stable A further object of the invention is to provide a com emulsions would be produced, but rather that the high salt position which can readily be formed into a tanning emul 45 content would cause the chlorinated paraffins to separate sidin giving leathers characterized by softness and out immediately. Only through the conjoint use of the spe smoothness. cial highly ethoxylated emulsifiers are mixtures obtained These and other objects and advantages are realized in which yield stable emulsions despite the high electrolyte accordance with the present invention pursuant to which content. there is provided a pulverulent mixture for tanning animal 50 The parts indicated in the Examples which follow are hides and leather, the mixture comprising (a) a parts by weight: chrome tanning agent; (b) a chlorination product of par EXAMPLE 1. affin hydrocarbons of about 8-24 carbon atoms and hav ing a chlorine content of about 20-50% by weight; and 100 parts of pulverulent chromium-III sulfate (CrOs (c) an adduct of about 20 to 70 moles of ethylene oxide content: 26%; SO content: 27%; NaSO content: 23%) with an alkylphenol, aralkylphenol or fatty alcohol. 55 are mixed with 20 parts of sodium bicarbonate. This mix The mixture comprises preferably. (a) 100 parts by ture is subsequently treated with a mixture of 15 parts of weight of the chrome tanning agent; (b) 5-25 parts by n-chlorinated paraffin (Co-C8-paraffin; chlorine content weight, optionally 10-20 parts by weight of the said chlor 35%) and 3 parts of an adduct of 30 moles of ethylene ination product; and (c) 1-15 parts by weight, optionally oxide to 1 mole of nonylphenol, produced by stirring the 2-5 parts by weight of the said adduct. 30 nonylphenol-polyglycol-ether, warmed to 60° C., into the The invention also provides an advantageous method of chlorinated paraffin. producing the tanning mixture of the invention comprising The resulting mixture is outstandingly suitable for the mixing the chlorination product and the adduct to forman manufacture of soft side leather (grained upper leather, intermediate mixture, and then admixing the chrome tan suede leather and nubuck). ning agent with the said intermediate mixture. 65 100 parts of cow pelts are pickled with sodium chloride The chrome tanning agents used in the mixtures accord and sulfuric acid in a tanning vat in the usual manner, 12 ing to the invention are especially basic chromium-III sul parts of the tanning mixture described above are added to fates, masked basic chromium-III salts, and mixtures of the pickle. The time in the tanning vat is 8 hours, the ini these salts with acid-binding substances, such as sodium tial temperature 20° C. and the final temperature 40 C. bicarbonate, sodium carbonate, dolomite, calcium carbon O The leathers are subsequently neutralized, dyed and fat ate or sodium sulfite. liquored in the usual manner, the amount of grease being 3 reduced by 30%. The finished leathers are very soft and described above, for 1 hour at 40° C. in a tanning vat, very supple and can be dyed very evenly with aniline dyes. The leathers are further processed into suede in the usual Side leathers of the same quality were also obtained if manner, with or without intermediate drying before dye instead of the indicated tanning mixture the same amount ing. The resulting leathers are distinguished by a very of one of the tanning mixtures A or B described below was uniform color and a velvety sheen. employed. - Tanning Mixture A EXAMPLE 4 100 parts of pulverulent chromium-(III) sulfate (CrO 100 parts of pulverulent chromium-(III) sulfate (Cr2O3 content: 26%; SO content: 27%; Na2SO4 content 23%) content: 26%; SO content: 27%; Na2SO4 content: are mixed with 8 parts of ground dolomite and 14 parts O 23%) are mixed with 15 parts of sodium carbonate in of sodium bicarbonate. A mixture of 17 parts of n-chlori 20 parts of sodium formate. This mixture is subsequiently nated paraffin (Co-Ca-paraffin; chlorine content: 45%), treated with a mixture of 16 parts of n-chlorinated 4 parts of an adduct of 50 moles of ethylene oxide to 1 paraffin (Co-C18-paraffin; chlorine content: 40%) and 4 mole of dodecylphenol and 2 parts of dodecylbenzene parts of an adduct of 60 moles of ethylene oxide to sulfonic acid, which was manufactured by stirring the 5 one mole of di-(phenylethyl)-phenol, which was prepared dodecylphenol-polyglycol-ether, warmed to 60° C., and by stirring the di-(phenylethyl)-phenol-polyglycol-ether, the dodecylbenzenesulfonic acid into the chlorinated warmed to 60° C., into the chlorinated paraffin. paraffin, is subsequently added to the former mixture. The resulting mixture is outstandingly suitable for the re-tanning of napa leather. Tanning Mixture B 100 parts of side leather which has been chrome-tanned 100 parts of chromium-(III) sulfate containing formate and shaved in the conventional manner are re-tanned in groups (Cr2O3 content: 28%; SO content: 13%; formic 100 parts of water with 8 parts of the tanning mixture acid content: 10%; Na2SO4 content: 30%) and a mixture described above, for 1 hour at 40° C. in a tanning vat. of 15 parts of n-chlorinated paraffin (Co-C18-paraffin; 25 The leathers are further processed in the usual manner chlorine content: 38%) and 3 parts of an adduct of 50 for napa side leather. The resulting leathers are very soft moles of ethylene oxide to oleyl alcohol, which was pre and very supple and are dyed very uniformly by aniline pared by stirring the oleyl alcohol-polyglycol-ether, dyes.
Details
-
File Typepdf
-
Upload Time-
-
Content LanguagesEnglish
-
Upload UserAnonymous/Not logged-in
-
File Pages2 Page
-
File Size-