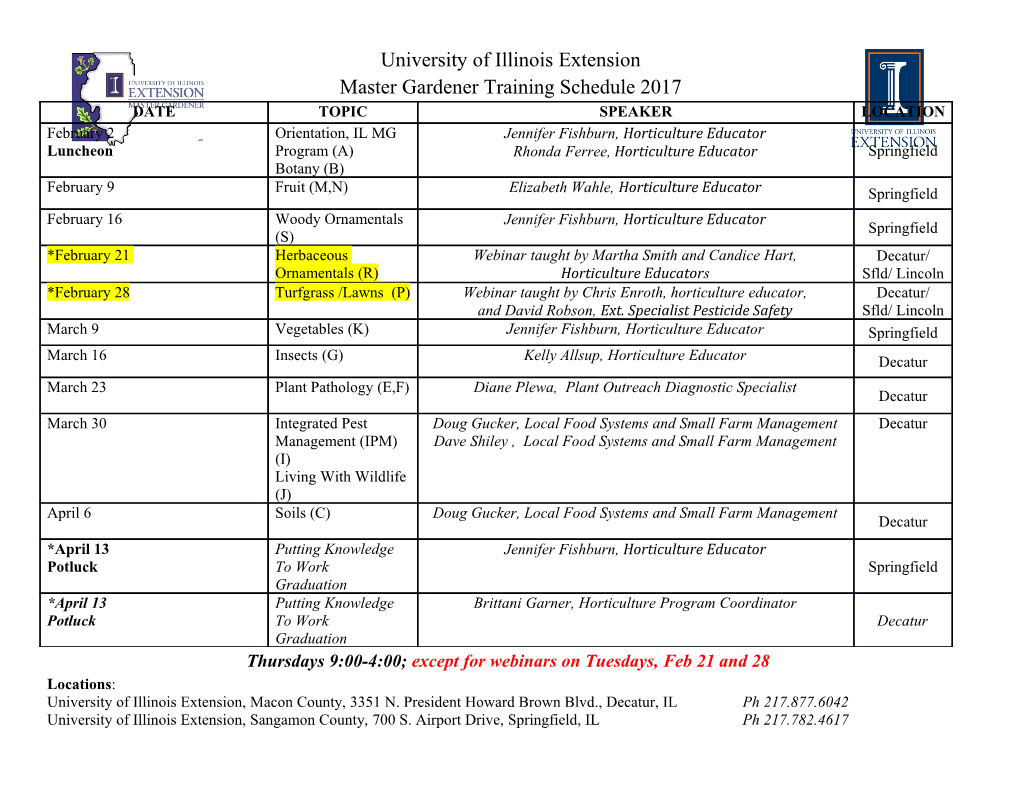
ARTICLE International Journal of Advanced Robotic Systems A Robot for the Unsupervised Grit-Blasting of Ship Hulls Regular Paper Daniel Souto, Andres Faiña, Alvaro Deibe, Fernando Lopez-Peña and Richard J. Duro* Integrated Group for Engineering Research, Universidade da Coruña, Spain * Corresponding author E-mail: [email protected] Received 3 May 2012; Accepted 20 Jun 2012 DOI: 10.5772/50847 © 2012 Souto et al.; licensee InTech. This is an open access article distributed under the terms of the Creative Commons Attribution License (http://creativecommons.org/licenses/by/3.0), which permits unrestricted use, distribution, and reproduction in any medium, provided the original work is properly cited. Abstract This paper describes the design and the control of the robot has been implemented and tested in realistic architecture of an unsupervised robot developed for grit environments, ascertaining that the design and the blasting ship hulls in shipyards. Grit blasting is a very control system are perfectly suited to the functions which common and environmentally unfriendly operation, the robot must carry out. required for preparing metallic surfaces for painting operations. It also implies very unhealthy and hazardous Keywords Autonomous robots, layered robot control, working conditions for the operators that must carry it Climbing robots, safe gritblasting, Shipyard automation out. The robot presented here has been designed to reduce the environmental impact of these operations and completely eliminate the health associated risks for the 1. Introduction operators. It is based on a double frame main body with magnetic legs that are able to avoid the accumulation of Shipyards are a paradigmatic example of a dynamic and ferromagnetic dust during its operation. The control unstructured environment where the real application of system presents a layered structure with four layers that robots presents a very significant challenge. These types are physically distributed into two separate components of environments are very extensive, requiring moving in order to facilitate different operational modes as well robotic platforms, and in constant change, making them as to increase the safety requirements of the system. A very difficult for traditional robotic approaches. The low‐level control component has been implemented on different operators and tools that are required are usually the robotic unit itself, and a mission planning and control carried to the product itself (ship or marine structure) and component has been developed on a base station that is move over it, as opposed to the way things are done in also used for interaction with the operator, when the more traditional assembly lines. Thus, any robot that has monitoring of the robot’s operation is required. This base to work in these settings will be faced with a constantly station component contains three layers of the control changing product that grows as construction proceeds. At system that permit the manual, semiautonomous and the same time, the robot needs to move and operate in an autonomous operation of the whole system. A prototype environment that is filled with all kinds of changing www.intechopen.com Daniel Souto, Andres Faiña, Alvaro Deibe,Int Fernando J Adv Robotic Lopez-Peña Sy, 2012, and RichardVol. 9, 82:2012 J. Duro: 1 A Robot for the Unsupervised Grit-Blasting of Ship Hulls obstacles: other moving robots or humans, scaffolding, texture level for the surface. However, it presents many machinery, etc. As a consequence, shipyards are among drawbacks when considering the environmental those industries with a low degree of robot penetration. implications of the process and the hazards for the human operators performing the task. It obviously Notwithstanding the previous comments, some groups generates a lot of toxic waste, which includes the particles and companies have addressed the introduction of robots themselves as well as any of the materials that have been in these environments since the end of the Eighties [1]. stripped off the surface (paint, metal, oxides, etc.). It also However, these systems have not really been adopted by involves very unhealthy working conditions for the the industry until much more recently, and only for operators carrying it out, as they have to work in an specific and very controlled and simplified operations, environment full of small metal or sand particles that such as inspection [2], welding [3],[4], and hull cleaning bounce off the surface at very high speeds, paint and [5]. The aspect which the authors of the different other toxic particles that are stripped off the surface, as proposals pay the most attention to is how the robots well as being exposed to very high acoustic levels move over the areas they are supposed to work in. In this [12],[13] and [14]. sA a consequence, over the last few line, different approximations are possible, going from years new environmental regulations have led to an wheeled robots to different types of walking machines. increasing use of ultra‐high pressure water jetting as an General introductory reviews of climbing and walking alternative to abrasive blasting in certain operations. In robots in the marine industry, as well as of cooperative this case, no particles are used ‐ it is just the water itself, robots, may be found in [6],[7] and [8]. Just to cite some of projected at extremely high pressures, which performs the most recent applications in this line, we should the stripping of the surface. Unfortunately, these mention those of Fei, Zhao and Wan [9] who developed a techniques, although much more environmentally climbing inspection robot with four magnetic wheels, and friendly, are generally slower and more costly than Lee et al. [10] whose proposal is very specialized for a abrasive blasting and, more importantly, cannot really certain type of environment, namely that of double hulls. prepare steel surfaces for optimal paint adherence, like in They have designed a rail runner mechanism that carries the case of sand or grit blasting. They basically remove a robotized arm for welding in double hull structures. only the coating that is present. It is for this reason that the most commonly used systems in shipyards are still Surface preparation is a very important operation in based on manually operated hoses that project grit at shipyards. It involves removing any surface coating high speeds by injecting pressurized air at a pressure of (paint or oxides) as well as providing a surface with a around 8 kg/cm2. given texture that is adequate for the subsequent painting operations [11]. This is a process that is carried out just With the aim of reducing the environmental and health before painting in order to prepare the metal surfaces. impact of these operations, over the last decade some When this operation is performed during the construction inroads have been made in their automation [2] and in of the ship, the objective is for the surfaces to conform to the development of robots for hull stripping and surface a given texture standard before applying the paint preparation. Most of the work carried out in this line, coatings in order to improve durability and coverture. On however, has considered water jetting to be the main the other hand, when this operation is carried out during stripping technique [15],[16] and [17]. A clear example of ship maintenance, the objective is usually to first remove this is the Ultrastrip series of Robots developed at the the old paint coats and prepare the surfaces for new ones Carnegie Mellon University Robotics Institute [15] and when it is repainted. In both cases, it is an later commercialized by Ultrastrip Systems. These 200+ environmentally problematic process, with all kinds of kg remote controlled robots are based on air gap magnets health‐related risks, which is usually carried out by for fixation and wheels for motion, and they carry around human operators. a water jet head within an enclosure for vacuuming the residue in order to reduce the environmental impact of Different technologies exist for cleaning and stripping the system. The results obtained by this system were metal surfaces, the two most relevant being abrasive quite successful but, as indicated above, water jetting blasting and ultrahigh pressure water‐jetting [2]. does not achieve the same level or steel surface Abrasive blasting is a traditional technique and has been preparation as grit blasting systems and, thus, is not around for more than a century. It consists in blasting the appropriate for all cases. It is for this reason that some hull with small particles of sand (sand blasting) or metals groups have devoted great efforts to the development of (grit blasting) using a high pressure jet of fluid, generally robotic systems capable of safely performing grit blasting air or water, to project these particles onto the surface at operations on ship hulls. One of the main problems here very high speeds. It is a very effective technique in terms lies in the adherence of the robots to the metallic surfaces, of the final surface results as, in addition to removing as blasting produces ferromagnetic particles or dust that whatever coating is present, it is able to provide a given tends to collect on the fixation magnets, rendering them 2 Int J Adv Robotic Sy, 2012, Vol. 9, 82:2012 www.intechopen.com useless. The authors of [18] tried to solve this problem by cleaning an 80 cm wide path as it moves. It is attached to using vacuum‐based adhesion and moving the robot the surface of the hull by means of a NdFeB permanent using four wheels. Others, like Ortiz and his collaborators magnet‐based fixation system whose individual elements [19], have addressed the problem through a remote can be demagnetized, as needed by means of internal controlled robot arm with a blasting head positioned on demagnetizing coils.
Details
-
File Typepdf
-
Upload Time-
-
Content LanguagesEnglish
-
Upload UserAnonymous/Not logged-in
-
File Pages16 Page
-
File Size-