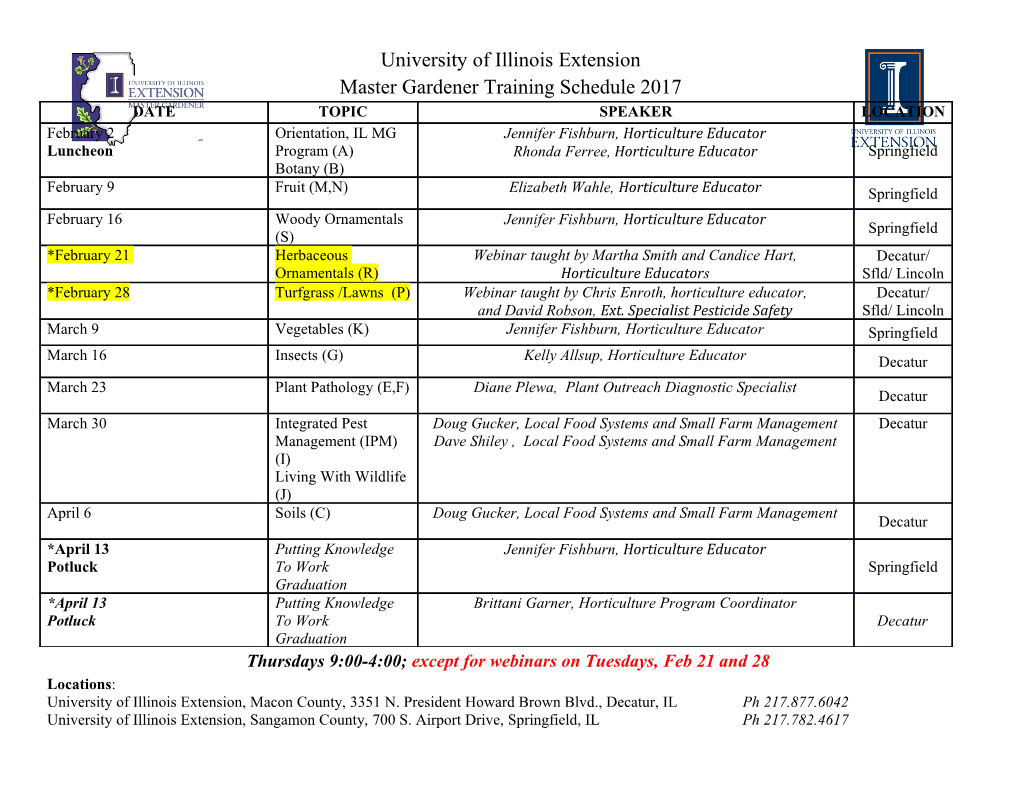
INNOVATIVE HIGH THROW COPPER ELECTROPLATING PROCESS FOR METALLIZATION OF PCB Maria Nikolova, Ph.D. and Jim Watkowski MacDemid, Inc. Waterbury, CT, USA [email protected] and [email protected] ABSTRACT It is shown in this paper that utilizing an innovative DC Copper electroplating is widely used in the electronic copper plating system a reliable copper metallization of high industry for fabrication of electronic devices. It is aspect ratio PCB can be achieved. Two high throw formulas particularly explored for fabrication of printed circuit boards have been developed. The first one allows for plating in the and semiconductors. High throwing power copper CD operating range of 10 – 45 ASF. The MD measured is = electrolytes are becoming increasingly important due to the > 85% for the AR 8:1. This formula in particular is suitable electronic industry requirements for manufacturing of high for VCP applications where the plating times are restricted. aspect ratio circuit boards. The second formula is developed for plating especially at low CD to meet the requirement for high AR PCB using a Utilizing an innovative DC plating technique a reliable DC process. The operating CD range is 5 – 25 ASF. MD of copper metallization of through holes can be achieved. The = >90% for AR 8:1 is achievable. Various plating parameters of this plating technique have been studied and parameters were studied in order to plate through holes with are presented in this paper. Excellent Throwing Power in improved micro-distribution and improved mechanical PCB through holes, and blind micro-vias are achieved. Two properties of the plated metal such as tensile strength and formulas are developed. The copper distribution is superior elongation. The structure and the thermal characteristics of across the PCB for the two formulations. Plated copper is the deposits were examined. Panel and pattern plate were bright, smooth, and leveled, especially inside the through tested. holes, including at low CD, 5ASF. Plated copper exhibits excellent ductility and tensile strength. The process is easily ACID COPPER PLATING PROCESS controlled be CVS analysis and Hull cell tests and can be Sulfuric acid copper bath are now dominating the industry. applied to both panel and pattern plate. A plating solution contains copper sulfate, sulfuric acid, chloride ions, and organic additives that control the Key words: Copper electroplating, PTH, PCB metallization. deposition process and the quality of the plated coatings. Typically the organic additives include brightener (grain INTRODUCTION refiner), suppressor, and leveling agents [3-8]. Throwing Electronic industry mass production utilizes acid copper power of an electroplating bath depends on solution plating in fabrication of printed circuit (PCB) boards and conductivity, electro-deposition kinetics (the slope of the semiconductors. A uniform deposition of copper is required polarization curve), cell geometry, and temperature. The for the development of complex conductor structure, plating uniformity is influenced by the solution chemistry especially for the high aspect ratio through hole plating. and solution agitation conditions. With smaller diameter holes and thicker panels more difficult task is faced with respect to plating distribution. If The purpose of this work was to determine the effect of the deposited copper is insufficient at the walls of the various organic additive species and their concentration on through holes, the result will be rejection of the entire PCB. the throwing power. The suppressors (high molecular Organic compounds are added to copper plating bath during weight polyether compounds and polyoxyalkylene glycols) the production of PCBs, chip carriers, and semiconductors in the presence of chloride ion have a strong polarizing [1-2]. They act as levelers and brighteners enabling as influence producing a large decrease in the exchange current uniform a deposition of copper as possible on different density. Addition of brightener such as sulfopropyl sulfides regions of the PCB including through holes and BMVs. In to an acid copper electrolyte acts as a depolarizer producing general, copper plating processes that provide better an increase in exchange current density. As an example, the leveling of the deposit across the substrate surface and maximum depolarization effect for SPS (disodium bis inside the through holes tend to worsen the throwing power (sulfopropyl) disulfide) was observed at a concentration of 5 of the electroplating bath. Plating through holes, PTH with ppm. Above this concentration of the brightener, the surface various aspect ratios, including high AR presents challenge blocking effect of the adsorbed brightener mitigates the for the PCB manufactures. High throwing power depolarizing effect to some degree. The brightener spices electrolytes are becoming increasingly important, due to the are much smaller molecules than the wetter molecules and electronic industry requirements of manufacturing high so the adsorption of the wetter does not appear to aspect ratio circuit boards. significantly interfere with the adsorption of the brightener. Leveler adsorbs preferentially near the most negatively low current densities allowed for reliably plating of higher charged sites of the cathode (PCB), thus slowing down the AR through holes. plating rate at high current density areas. The organic additives affect the secondary current distribution and Table 1. High Throw 100 Bath Constituents control the physical mechanical properties of the metal COMPONENT MacuSpec HT 100 deposits considerably important being tensile strength and Target Range elongation. CuSO4x5H2O 50 g/l 45 – 80 g/l Sulfuric Acid 250 g/l 220 – 300 g/l In this study a low organic additive system was combined Chloride 60ppm 45ppm – 85ppm with a high free acid to copper ratio electrolyte. Wetter 10 ml/l 8 - 20 ml/l TEST VEHICLES Brightener 0.6 - 1.0 ml/l 0.5 – 1.2 ml/l The test vehicles used in the process evaluation were 1.6 Leveler 1.5 ml/l 1.2 – 2.0 ml/l mm, 2.4 mm, and 3.5 mm thick boards with various sized Temperature 72 – 73 F 68 – 80 F o o through holes. The through holes diameters were 0.2 mm, (22 - 23 C) (20 – 27 C) 0.25 mm, 0.35 mm and 0.5 mm. The through holes AR Current Density 10 ASF – 45 ASF varied from 3.2 to 17.5. All geometries incorporated in the (1.1 ASD – 4.9 ASD) test vehicles were simultaneously plated. Table 2. High Throw 200 Bath Constituents The process flow includes the following operations: COMPONENT MacuSpec HT 200 • Acid cleaner: Wets the hole and removes light soils. Target Range • Rinse CuSO4x5H2O 30 - 50 g/l 30 – 75 g/l • Micro-etch: Etches undercuts and remaining debris and Sulfuric Acid 270 - 250 g/l 220 – 300 g/l ensures excellent copper to copper adhesion. Chloride 60ppm 45ppm – 85ppm • Rinse Wetter 6 ml/l 5.5 - 8 ml/l • Acid dip: Acidifies copper surface prior to plating. Brightener 1.0 ml/l 0.8 – 1.2 ml/l • Deposition of copper in acid copper bath Leveler 6 ml/l 5.5 – 8 ml/l Starter 2.5 ml/l 2.0 – 3.5 ml/l MICRODISTRIBUTION Temperature 72 – 73 F 68 – 80 F The Microdistribution is defined as the ratio of the deposit (22 - 23oC) (20 – 27oC) copper thickness in the center of the through hole to its Current Density 5 ASF – 25 ASF thickness at the surface. It is calculated according to the (0.5 ASD – 2.7 ASD) equation: (C+D)*100 / 2 RESULTS Microdistribution in % = --------------------- (A+B+E+F) / 4 Micro-Distribution Measurements The difficulties for plating through holes depends not only Figure 1 shows a cross section of a through hole indicating on the aspect ratio but on the particular board thickness and the points of thickness measurements. hole vehicle design (thickness & hole diameters). The graphs show diameter, e g. at the same aspect ratio it would be easier to plate the thinner board with a smaller diameter, A B than a thicker board with a larger diameter. The difficulty of plating (IR drop in the hole) is influenced by the thickness C D of the board or length of the hole by a squared term and it is inversely proportional to the though hole size (diameter). We included in our study plating at various current densities, CD depending on test the data obtained from the E F Microdistribution measurements. Figure 1. Cross Section of Plated Panel BATH CONSTITUENTS The bath constituents for the two formulas studied and the plating parameters are given in Tables 1 for MacuSpec HT 100 and in Table 2 for MacuSpec HT 200. The process can be used at varying basic electrolyte compositions to optimize performance. The best results were achieved with a low copper, high acid concentration solution. Plating at Microdistribution MacuSpec HT 200, 1.6 mm Panel 100 5 ASF 95 10 ASF 90 25 ASF 85 MD, % MD, 80 75 Figure 5. Cross Section of 0.20 mm Through Hole in 1.6 0.50 0.35 0.25 0.20 mm Panel Plated at 10 ASF, AR = 8 Hole Diameter, mm Figure 2. Microdistribution for 1.6 mm Thick Panel Aspect Ratio: 3.2, 4.6, 6.4, and 8 Microdistribution MacuSpec HT 200, 2.4 mm Panel 100 90 5 ASF 10 ASF Figure 6. Cross Section of 0.50 mm Through Hole in 1.6 80 25 ASF mm Panel Plated at 10 ASF 70 MD, % MD, 60 50 0.50 0.35 0.25 0.20 Hole Diameter, mm Figure 3. Microdistribution for 2.4 mm Thick Panel Aspect Ratio: 4.8, 6.9, 9.6, and 12 Microdistribution Figure 7. Cross Section of 0.25 mm Through Hole in 1.6 MacuSpec HT 200, 3.5 mm Panel mm Panel Plated at 15 ASF 100 90 5 ASF 80 70 10 ASF MD, % MD, 60 50 40 0.50 0.35 0.25 0.20 a) Hole Diameter, mm Figure 4.
Details
-
File Typepdf
-
Upload Time-
-
Content LanguagesEnglish
-
Upload UserAnonymous/Not logged-in
-
File Pages6 Page
-
File Size-