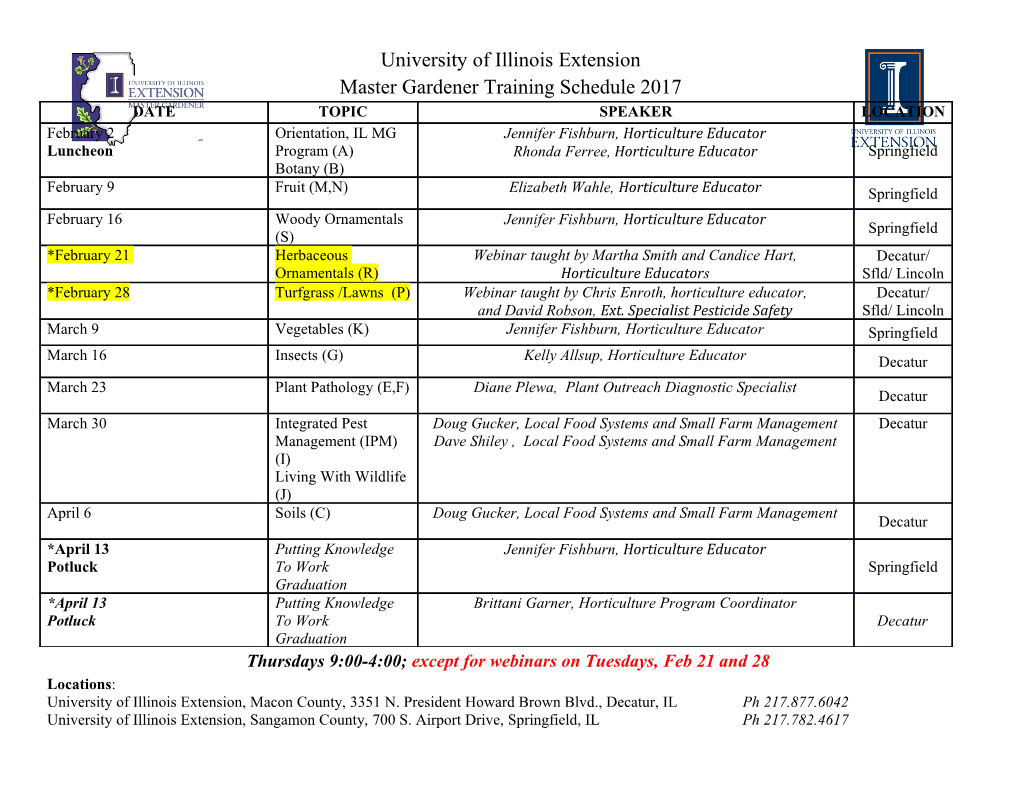
APPLICATION OF CONJUGATE HEAT TRANSFER (CHT) METHODOLOGY FOR COMPUTATION OF HEAT TRANSFER ON A TURBINE BLADE A Thesis Presented in Partial Fulfillment of the Requirements for the Degree Master of Science in the Graduate School of The Ohio State University By Jatin Gupta, B.Tech. ***** The Ohio State University 2009 Master’s Examination Committee: Approved by Prof. Seppo Korpela, Adviser Dr. Ali A. Ameri, Co-adviser Adviser Prof. Sandip Mazumder Graduate Program in Mechanical Engineering c Copyright by Jatin Gupta 2009 ABSTRACT The conventional thermal design method of cooled turbine blade consists of inde- pendent decoupled analysis of the blade external flow, the blade internal flow and the analysis of heat conduction in the blade itself. To make such a calculation, proper interface conditions need to be applied. In the absence of film cooling, a proper treatment would require computation of heat transfer coefficient by computing heat flux for an assumed wall temperature. This yields an invariant h to the wall and free stream temperature that is consistent with the coupled calculation. When film-cooling is involved the decoupled method does not yield a heat transfer coefficient that is invariant and a coupled analysis becomes necessary. Fast computers have made possible this analysis of coupling the conduction to both the internal and external flow. Such a single coupled numerical simulation is known as conjugate heat transfer simulation. The conjugate heat transfer methodology has been employed to predict the flow and thermal properties, including the metal temperature, of a particular NASA tur- bine vane. The three-dimensional turbine vane is subjected to hot mainstream flow and is cooled with air flowing radially through ten cooling channels. The passage flow and heat transfer, internal coolant flow and heat transfer, and conduction within the metal are solved simultaneously using conjugate heat transfer methodology. Unlike ii the decoupled approach, the conjugate simulation does not require thermal boundary conditions on the turbine walls. It is believed that turbulence has a large influence on heat transfer and hence in the present study, a modified k-ω model by Wilcox [26] was used for the external flow and it was compared to Wilcox’s standard k-ω model [25] to see if the new model provided any improvement in predicting the heat transfer on the blade surface. Results here have shown that, for the present geometry, the standard model [25] is still much better in predicting temperature and hence the heat transfer over the blade surface than the modified model [26]. A thermal barrier coating (TBC) “system” is used to thermally protect turbine engine blades and vanes from the hot gases in gas turbine engines. The overall results from this study, including turbulence modeling and the use of TBC, are encouraging and indicate that conjugate heat transfer simulation with proper turbulence closure is a viable tool in turbine heat transfer analysis and cooling design. iii This is dedicated to all those who supported me in this effort. iv Acknowledgements Current work is the outcome of the rewarding research in my graduate study and I would like to express my gratitude to my mentors, friends, and family who helped me with their advice and support during these years. I am truly and extremely grateful to my mentor, Dr. Ali A. Ameri, without whom the success of this study would be impossible. His consistent presence in the times of need and his guidance and advice have helped me through the obstacles, improved the quality of my work, and trained me to be a successful researcher. I was privileged to have a continuous learning experience during my work under his supervision. I am extremely grateful to my advisor Prof. Seppo Korpela for his valuable support throughout the year. He provided an excellent research environment and great freedom to carry out research. I’ll always remember the intellectual discussions I had with him from time to time and his great foresight in world oil issues. Despite his position, his priorities have always been to guide his students and travel an extra mile if that means giving practical experience to his students. I would also want to thank Dr. David L. Rigby, at NASA Glenn, who has been a great inspiration giving valuable comments, especially with setting up the test case and generating the required files for different cases. I must acknowledge his knowledge and experience in this area which has saved me many times from getting at a problem. Finally, I would like to express my sincere gratitude to all those people who have been constantly around me, have supported me and helped me when I needed them. To them, I dedicate this work. v TABLE OF CONTENTS Page Abstract . ii Dedication . iv List of Tables . viii List of Figures . ix Chapters: 1. Introduction . 1 1.1 Gas Turbines . 1 1.2 Increasing efficiency through cooling . 3 1.3 Flow phenomena inside turbine blades . 6 1.4 Background . 6 1.5 Thermal Barrier Coating . 10 1.6 Project Description . 13 2. Fluid Motion and Heat Transfer . 15 2.1 Governing Equations . 15 2.1.1 Continuity . 15 2.1.2 Momentum . 16 2.1.3 Energy . 16 2.2 Computational Fluid Dynamics . 18 2.2.1 Governing Equations . 19 2.2.2 Turbulence Models . 20 2.3 Mathematical formulation . 26 2.3.1 Modeling for h and bulk temperature boundary conditions . 26 2.3.2 TBC Modeling . 27 vi 3. Code Description . 29 3.1 CHT Calculation using Glenn-HT . 30 4. Analysis . 31 4.1 Model Geometry . 31 4.2 Numerical Methodology . 33 5. Results and Discussion . 38 6. Summary and Conclusions . 48 7. Future Work . 50 Bibliography . 52 vii LIST OF TABLES Table Page 4.1 Geometry Parameters for C3X vane . 33 4.2 Cooling Channel’s Property . 35 4.3 Hot gas path flow details . 35 viii LIST OF FIGURES Figure Page 1.1 RM12, Gas Turbine . 2 1.2 Turbine Entry Temperature,(Copyright Rolls Royce plc) . 4 1.3 A schematic illustration of a modern thermal barrier coating system consisting of a thermally insulating thermal barrier coating, a ther- mally grown oxide (TGO) and an aluminum rich bond coat. The tem- perature gradient during engine operation is overlaid [20]. 11 2.1 Boundary conditions across solid-fluid interface . 27 2.2 Boundary conditions across thermal barrier coating . 28 4.1 C3X Vane with Cooling Holes . 32 4.2 C3X Grid . 34 5.1 Experimental and predicted data of P/P0 . 39 5.2 Contours of Mach number at midspan . 40 5.3 Experimental and predicted data for Twall/T0 under different b.c. 42 5.4 Experimental and predicted data for Twall/T0 under different turbu- lence models . 43 5.5 Experimental and predicted data for normalised heat transfer coeffi- cient under different turbulence models . 44 5.6 Static Temperature at 50% of blade’s height . 45 ix 5.7 Wall temperature on the pressure side and the suction side of C3X blade 46 5.8 Effectiveness of TBC . 47 5.9 Temperature variation across TBC . 47 x CHAPTER 1 INTRODUCTION 1.1 Gas Turbines Gas turbine engine is one of the excellent means of producing either thrust or power. Its main advantages are: exceptional reliability, high thrust-to-weight ratio, and relative freedom from vibration. The work from a gas-turbine engine may be provided either as torque in a shaft rotating at a certain speed, or as thrust in a jet of certain velocity. A gas-turbine consists of the following main parts: an inlet, a compressor, a combustor, a turbine and an exhaust, as shown in the cutaway in Figure 1.1. The inlet section may involve filters, valves and other arrangements to ensure a high quality of the flow. The pressure of the air is increased in the compressor, usually consisting of several stages. Depending on the design of the engine the compressor may be of radial type in which the air enters axially but exits radially, or the more common, an axial compressor may be used, in which the flow enters and leaves axially. The rotation of the compressor blades increases the velocity of the air which then undergoes a diffusion process in which its dynamic pressure (velocity) is converted to static pressure. The compressor and turbine, and the shaft connecting them, is called a spool in which the output power of the turbine exceeds the power requirement needed to drive 1 Figure 1.1: RM12, Gas Turbine the compressor. The compressed air enters a combustor in which fuel is burned and the temperature of the combustion products leaving the combustor is a key variable in the design of the engine. The design and operation of these burners are vital to yield low emissions in a high efficiency engine. The highly energetic gas from the combustor is expanded through a turbine, which drives the compressor in the front of the engine. After the turbine the gas still contains a significant amount of energy which can be extracted in various forms. In aircrafts the surplus energy is transformed into a high velocity jet in the nozzle which is the driving force that propels the vehicle through the air. The jet velocity and hence thrust could be further increased, through re-heating the gas in an afterburner. This is common in high performance aircraft, especially for military applications. For stationary, power generating gas turbines, the extra energy is converted into shaft-power in a power turbine [1]. 2 1.2 Increasing efficiency through cooling Increased environmental awareness and rising fuel costs has been forcing designers to strive towards enhanced efficiencies for all propulsion systems.
Details
-
File Typepdf
-
Upload Time-
-
Content LanguagesEnglish
-
Upload UserAnonymous/Not logged-in
-
File Pages66 Page
-
File Size-