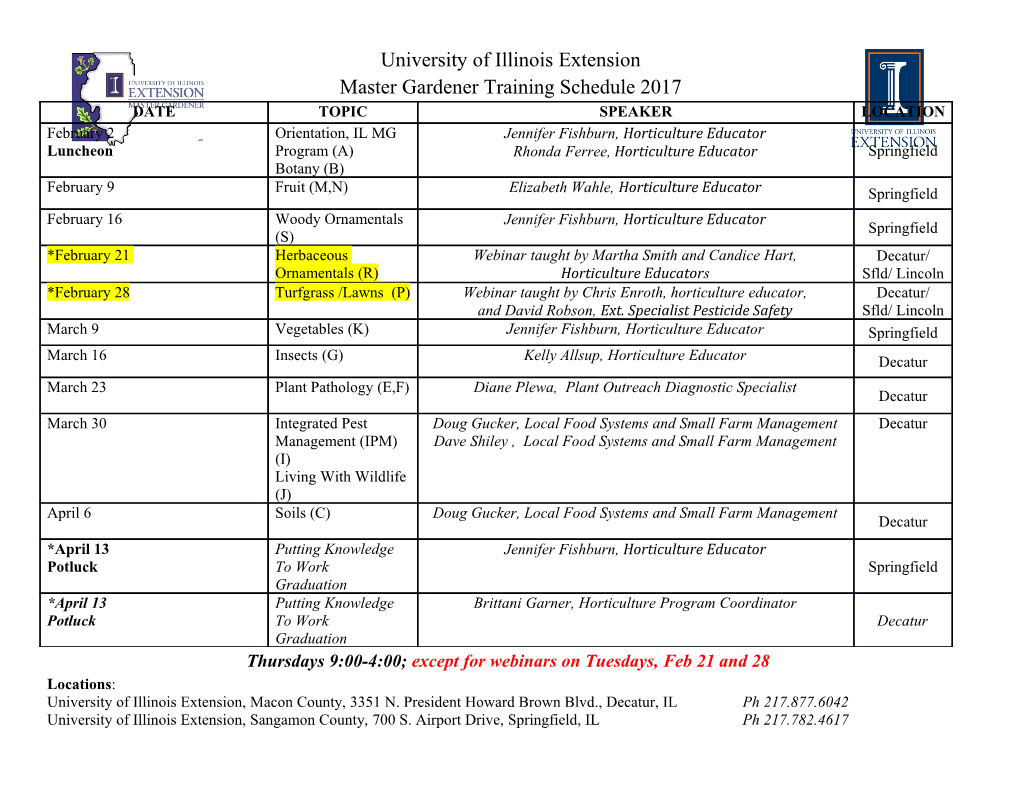
University of Pennsylvania ScholarlyCommons Department of Chemical & Biomolecular Senior Design Reports (CBE) Engineering 4-2012 TWO-STEP PRODUCTION OF 1,3-BUTADIENE FROM ETHANOL Jonathan Burla University of Pennsylvania Ross Fehnel University of Pennsylvania Philip Louie University of Pennsylvania Peter Terpeluk University of Pennsylvania Follow this and additional works at: https://repository.upenn.edu/cbe_sdr Burla, Jonathan; Fehnel, Ross; Louie, Philip; and Terpeluk, Peter, "TWO-STEP PRODUCTION OF 1,3-BUTADIENE FROM ETHANOL" (2012). Senior Design Reports (CBE). 42. https://repository.upenn.edu/cbe_sdr/42 This paper is posted at ScholarlyCommons. https://repository.upenn.edu/cbe_sdr/42 For more information, please contact [email protected]. TWO-STEP PRODUCTION OF 1,3-BUTADIENE FROM ETHANOL Abstract A plant utilizing a two-step reaction process, which takes a 95% ethanol stream (by mass) and produces a 98% 1,3-butadiene stream, was designed for this project. The production goal for this plant was 200,000 tonnes of butadiene with the main motivation behind the project being the recent rise in butadiene prices. The process first passes ethanol through a catalytic dehydrogenation reactor to convert ethanol to acetaldehyde and hydrogen. A kinetic model was used to determine the reaction rates and operating conditions of the reactor. The acetaldehyde intermediate is further reacted with ethanol in a catalytic reactor to form butadiene. A hydrogen byproduct stream is also generated in this design and is purified for sale. This report provides a design and economic analysis for the production of butadiene on the Gulf Coast. Process flow sheets, energy and utility requirements, and equipment summaries are provided and analyzed. Process profitability is sensitive to the cost of both ethanol and butadiene. It is shown that the plant is very profitable for its expected 15-year lifespan with an expected internal rate of return of 40%, return on investment of 34%, and net present value of $172,000,000 (for a discount rate of 15%). The process becomes unprofitable if the price of ethanol increases to over $3.00/gallon. A combination of increased ethanol price and decreased butadiene price will also cause the plant to be unprofitable. Therefore, plant construction is only recommended given an acceptable price of ethanol and butadiene. This working paper is available at ScholarlyCommons: https://repository.upenn.edu/cbe_sdr/42 CBE 459 Senior Design Project: TWO-STEP PRODUCTION OF 1,3-BUTADIENE FROM ETHANOL By: Jonathan Burla, Ross Fehnel, Philip Louie, and Peter Terpeluk Presented To: Mr. Leonard Fabiano, Dr. Warren Seider, and Dr. Talid Sinno April 10, 2012 Department of Chemical and Biomolecular Engineering University of Pennsylvania School of Engineering & Applied Science Letter of Transmittal Burla, Fehnel, Louie, Terpeluk Mr. Leonard Fabiano University of Pennsylvania School of Engineering & Applied Science 220 S 33rd Street Philadelphia, PA 19104 April 10, 2012 Dear Mr. Fabiano, We have analyzed a two-step process of converting ethanol to 1,3-butadiene. Enclosed is our solution to the design problem proposed by Mr. Bruce Vrana. Our plant design involves two reaction sections, both of which use heterogeneous catalysts in fixed bed reactors, and two separation sections to purify the products and recycle the unreacted feed. We have also designed a Dowtherm heating system for our process, which will supply heat to the reactor sections. This report provides details on the process equipment required and the potential profitability of the plant. The design determined a liquid feed flow rate of 155,000 lb/hr of ethanol and a production rate of 56,000 lb/hr of butadiene. Production was assumed to operate 24 hours a day for 330 days out of the year. The main capital investments for this project are the pressure swing adsorption unit, the reactors, and the multi-stage compressor, and the main variable investments are ethanol, steam, and natural gas. Overall, our process appears to be very profitable, with a return on investment of 34%. However, this analysis is very sensitive to both the price of ethanol and butadiene. Uncertainties lie in the cost for purification of hydrogen and the selectivities of the reactions, both of which were based on estimates from industry. Furthermore, no research has been done in recent years on the kinetics of the second reaction. Detailed kinetics would allow further optimization to be achieved. Sincerely, ________________ _______________ ______________ _______________ Jonathan Burla Ross Fehnel Philip Louie Peter Terpeluk Table of Contents Burla, Fehnel, Louie, Terpeluk 1.0 ABSTRACT 1 2.0 INTRODUCTION 2 3.0 PROJECT CHARTER 4 4.0 CONCEPT ASSESSMENT 5 4.1 MARKET AND COMPETITIVE ANALYSIS 5 4.2 CUSTOMER REQUIREMENTS 6 4.3 INNOVATION MAP 7 4.4 PRELIMINARY PROCESS SYNTHESIS 8 4.5 ASSEMBLY OF DATABASE 9 4.6 BENCH-SCALE LABORATORY WORK 9 5.0 PROCESS FLOW DIAGRAMS & MATERIAL BALANCES 10 5.1 SECTION 100 11 5.2 SECTION 200 13 5.3 SECTION 300 15 5.4 SECTION 400 17 5.5 SECTION 500 21 6.0 PROCESS DESCRIPTION 23 7.0 REACTOR DESIGN 34 6.1 REACTION ONE 34 6.2 REACTION TWO 36 6.3 REACTION VESSEL CALCULATIONS 37 6.4 REGENERATION OF CATALYST 42 8.0 ENERGY BALANCE & UTILITY REQUIREMENTS 44 9.0 UNIT DESCRIPTIONS 50 9.1 COMPRESSORS 50 9.2 DISTILLATION COLUMNS 50 9.3 DECANTERS 52 9.4 HEAT EXCHANGERS 52 9.5 PRESSURIZED VESSELS 56 9.6 FIRED HEATERS 58 9.7 PUMPS 58 9.8 PRESSURE SWING ADSORPTION UNITS 61 9.9 REACTION VESSELS 61 9.10 REFLUX ACCUMULATORS 62 9.11 MIXERS AND SPLITTERS 63 9.12 STORAGE TANKS 63 9.13 VALVES 64 10.0 COST SUMMARIES 65 10.1 EQUIPMENT COST SUMMARY 65 Table of Contents Burla, Fehnel, Louie, Terpeluk 10.2 FIXED CAPITAL SUMMARY 67 10.3 VARIABLE COST SUMMARY 69 10.4 FIXED COST SUMMARY 71 11.0 ECONOMIC ANALYSIS 73 12.0 OTHER IMPORTANT CONSIDERATIONS 79 12.1 PLANT STARTUP 79 12.2 PROCESS SAFETY 79 12.3 ENVIRONMENTAL CONCERNS 79 12.4 PROCESS CONTROLLABILITY 80 13.0 CONCLUSIONS 81 14.0 ACKNOWLEDGEMENTS 83 15.0 BIBLIOGRAPHY 84 APPENDICES 86 APPENDIX A: DISTILLATION TOWER OPTIMIZATION 86 APPENDIX B: MATLAB CODE FOR R-101 OPTIMIZATION 89 APPENDIX C: SAMPLE DESIGN AND COST CALCULATIONS 90 APPENDIX D: UNIT SPECIFICATION SHEETS 96 APPENDIX E: SAMPLE ASPEN SIMULATION RESULTS 140 APPENDIX F: MATERIAL SAFETY DATA SHEETS 160 APPENDIX G: EXCEL SHEETS FOR ECONOMIC ANALYSIS 185 APPENDIX H: PROBLEM STATEMENT 189 1.0 Abstract Burla, Fehnel, Louie, Terpeluk 1.0 ABSTRACT A plant utilizing a two-step reaction process, which takes a 95% ethanol stream (by mass) and produces a 98% 1,3-butadiene stream, was designed for this project. The production goal for this plant was 200,000 tonnes of butadiene with the main motivation behind the project being the recent rise in butadiene prices. The process first passes ethanol through a catalytic dehydrogenation reactor to convert ethanol to acetaldehyde and hydrogen. A kinetic model was used to determine the reaction rates and operating conditions of the reactor. The acetaldehyde intermediate is further reacted with ethanol in a catalytic reactor to form butadiene. A hydrogen byproduct stream is also generated in this design and is purified for sale. This report provides a design and economic analysis for the production of butadiene on the Gulf Coast. Process flow sheets, energy and utility requirements, and equipment summaries are provided and analyzed. Process profitability is sensitive to the cost of both ethanol and butadiene. It is shown that the plant is very profitable for its expected 15-year lifespan with an expected internal rate of return of 40%, return on investment of 34%, and net present value of $172,000,000 (for a discount rate of 15%). The process becomes unprofitable if the price of ethanol increases to over $3.00/gallon. A combination of increased ethanol price and decreased butadiene price will also cause the plant to be unprofitable. Therefore, plant construction is only recommended given an acceptable price of ethanol and butadiene. 1 2.0 Introduction Burla, Fehnel, Louie, Terpeluk 2.0 INTRODUCTION 1,3-butadiene is a chemical compound that is frequently used as a monomer in the production of synthetic styrene-butadiene rubber (SBR). It is also used to make adiponitrile, an intermediate of nylon, as well as acrylonitrile-butadiene-styrene (ABS), vinylcyclohexene, cyclooctadiene, cyclododecatriene, cycloalkanes, cycloalkenes, polybutadiene, hexamethylene diamine, styrene-butadiene latex, chloroprene, and nitrile rubbers (Sun, 1992). Currently, the most widely used technique for production of butadiene is extraction from the unsaturated hydrocarbon mixture produced from steam cracking of saturated hydrocarbons. This process is practiced primarily in the United States, western Europe, and Japan. Butadiene extraction usually involves large-capacity plants and consequently requires a high capital investment. Furthermore, in recent years ethane has become less expensive and more common, and is being used increasingly as a feed in steam cracking. The increase of ethane as a feedstock has resulted in lower production rates of butadiene, which in turn has raised the price of butadiene from $0.60/lb to over $1.60/lb today. Currently, the demand for butadiene is very high due to its diminished production, increased price, and many uses; thus an alternative large-scale production process of this chemical could be very profitable. During World War II, a common method of producing butadiene was the two-step Ostromislensky process, in which ethanol is oxidized to acetaldehyde which then reacts with additional ethanol over a tantala-promoted silica catalyst to yield butadiene. (2.1) CH CH OH CH3CHO + H2 3 2 (2.2) CH CH OH +→CH CHO CH CHCHCH + 2H O 3 2 3 2 2 2 Before and during World War II, this process→ was used in the United States and the Soviet Union.
Details
-
File Typepdf
-
Upload Time-
-
Content LanguagesEnglish
-
Upload UserAnonymous/Not logged-in
-
File Pages197 Page
-
File Size-