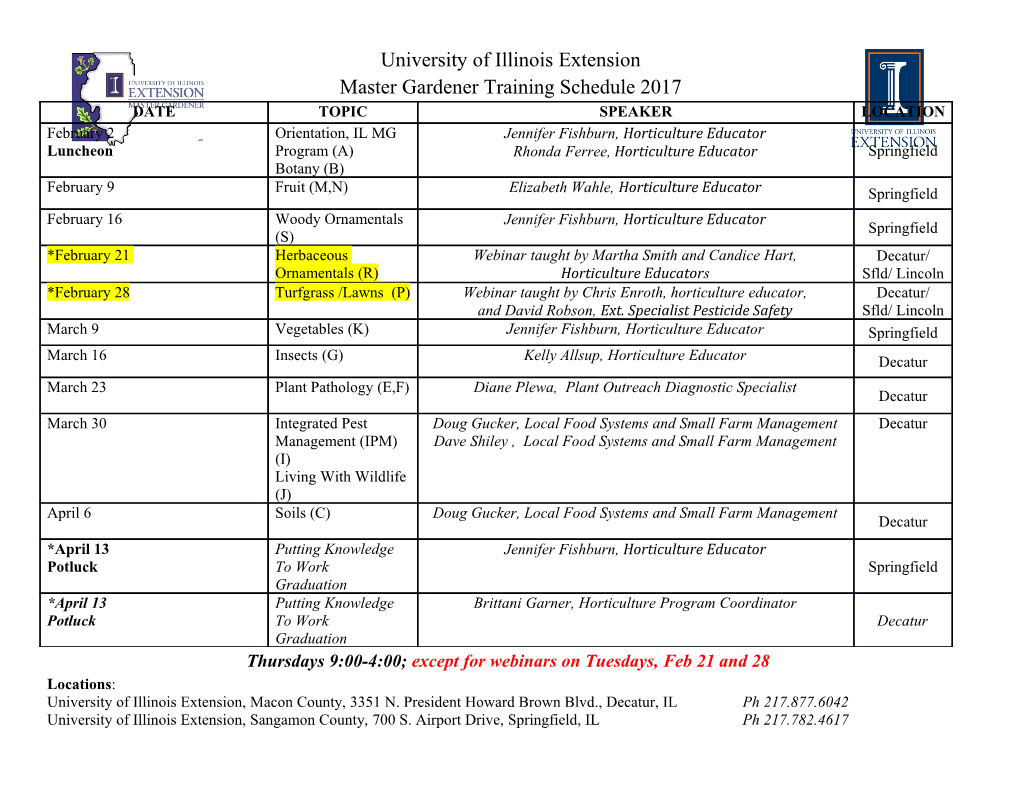
WWER FA modal analysis under vibration force and kinematic excitation V.V. Makarov, A.V. Afanasyev, I.V. Matvienko (OKB “GIDROPRESS”, Podolsk, Russia), Al.A. Tutnov, Alexander S. Kiselev, Alexey S. Kiselev (RRS KI, Moscow, Russia), S.E. Volkov (JSC TVEL) Abstract The approach based on mixed application of calculational and experimental methods is as- sumed for the analysis of WWER FA strength and stability under vibration loads typical as for reac- tor normal operating conditions so seismic effects. Experimental modal analysis is usually provided in air at 20 °С, the results are FA modal characteristics: frequencies, shapes, vibration damping fac- tor, transfer functions. Since FA is a nonlinear structure, modal analysis is provided at various lev- els of vibration excitation. The results of experimental modal analysis are initial data for FA calcu- lational modal model, which are used for the analysis of FA vibration strength and stability during the whole service life in the reactor. The results of experimental examination and numerical modeling of WWER-440, WWER- 1000, and WWER-1500 FA dynamic characteristics and the analysis of design and operational fac- tors influence on FA dynamic characteristics are presented in the report. This work was organized JSC TVEL. 1. Introduction Vibration effects on FA supports (vibration kinematic excitation) and FA components: SG fuel rods (vibration force excitation) were simulated during the experimental tests provided. Kinematic excitation of FA vibration results from FA supports vibration in the reactor, including seismic loads, force impact is transferred to FA from the coolant. Distributed hydrodynamic loads onto FA and fuel rods were replaced by concentrated forces during experimental simulation of vibration ex- citation force mechanism. Calculation analysis of natural frequencies and vibration modes of separate components and FA as a whole is provided using modern numerical methods - finite element method, super cell method. Development and application of numerical methods for proper value analysis allows to provide evaluation of structure proper parameters at the design stage already, when the actual prototype of the design, which can be experimentally tested, does not exist yet. Besides using of numerical methods can require modeling of such operational parameter combination which can not be realized on test rigs. Detailed design features simulation of FA comprising some hundreds of fuel rods, guid- ing channels, spacing grids etc. is necessary for correct results, that requires generation of finite- element models including hundred thousand cells and degrees of freedom. It is known that solution of proper value problems demands an order higher expenses of computer power in comparison with static calculations. Rather high requirements to computer algorithm efficiency are imposed taking into account complexity of the object under examination. 2. Methods of experimental modal analysis Experimental study was provided at 20 °С in air in the vibration test rig (Figure 1). The test rig allows to provide vibration and seismic tests of FA full-scale dummies within the range of frequencies up to 3 kHz with buoyancy force to 9,81 kN in transverse and longitudinal di- rection. Longitudinal compression of dummies in the tests is respective to nominal compression un- der FA working temperature in the reactor. 1 – suspender 2 – upper plate 3 - strainer 4 – FA dummy 5 – accelerometer 6 – metal structure 7 - lower plate 8 – shaker The diagram of tests for longitudinal vibration 1 – suspender 2 – shaker 3 – upper plate 4 - strainer 5 – FA dummy 6 – accelerometer 7 – metal structure 8 - shaker 9 - lower plate 10 – shaker The diagram of tests for transverse vibration Fig. 1 Vibration of the FA is provided with impact hammer or electrodynamic shakers. The first way of vibration excitation is used for express-analysis of structures or in the case when loading using shakers is not allowed for the item. The second way (using shakers) allows more precisely to assign and control external effects, to determine higher quantity of modes and is applied for detailed analy- sis of structure vibrations. Vibration load can be applied in the course of tests as directly to a dummy (simulation of vibration hydrodynamic excitation force loading) so to dummy supports (simulation of vibration transfer from reactor internals and seismic effect - kinematic loading). Vi- bration impact under force loading is measured using piezoelectric dynamometers, under kinematic excitation - using accelerometers on FA supports, vibration response is measured using accelerome- ters in FA components: SG, cap, fuel rods, etc. Modal analysis of FA dummies is provided using Brüel&Kjær and LMS International vibration test and analysis systems. Experimental modal analysis of five FA full-scale dummies for reactors WWER-1000, WWER-1500 and WWER-440 has been provided to the present time. 3. Experimental modal analysis results Maxims of FA frequency response function are available as in torsion and bending vibration natural frequencies of FA as solid structure (i.e. appear in vibration spectra of all FA components) so in natural frequencies of FA separate components. Vibration natural frequencies of dummies as solid structures shown in Table 1 are mainly de- termined by dummy mass and rigidity under bending and torsion. Rigidities shall be taken at low deflections (several tenth of millimeter) and torsion angles (sev- eral tenth of degree). Table 1 –WWER FA natural frequencies Frequency, Hz WWER- WWER-1500 WWER-1500 FA Vibration mode WWER- WWER-440 1000 FA (start of (end of opera- 1000 AFA RK-3 TVS-2M operation) tion) 1-st bending 4,7 5 4 2 6,9 1-st torsion 6,8 8 5,75 4,5 11,5 2-nd bending 10,5 10,5 8,5 6 16,7 2-nd torsion 16,2 16 13 9 30,4 3-d bending 17,7 16,5 14,25 10 24,7 3-d torsion - 24 20,75 13 45 4-th bending 25,3 23 20 - 36 5-th bending 34 28,5 26 - - 6-th bending - 35,5 32 - - Close vibration natural frequencies of WWER-1000 FA two dummies: AFA and TVS-2M are explained by similar masses and rigidities of the dummies with insignificant displacements and tor- sion angles, though TVS-2M dummy rigidity with deflections of order 10 mm is approximately 1,5 higher than for AFA. Clearances in the units “fuel rod – SG cell” result in decrease of bending ri- gidity and consequently in displacement of dummy natural frequencies to low-frequency area, that follows from the comparison of natural frequencies of two WWER-1500 FA dummies, which are different in the type of fuel rod seat in SG - with tightness for simulation of FA condition in the be- ginning of fuel life and with clearance for “burnt up” FA simulation. Comparison of natural frequencies of WWER-1500 FA dummy with the prototype WWER-1000 TVS–2M dummy proves that WWER-1500 FA fuel stack increased mass with ap- proximately similar bending rigidity is the cause of lower natural frequencies. Vibration natural frequencies of the dummy of the third generation operating fuel assembly (RK-3) for WWER-440 reactor are higher than for other tested dummies, that is explained by RK-3 lower mass and rather higher bending rigidity. Damping factors of FA dummy modes in air are within 1-7 % of critical damping. Mode shapes of FA as solid structure are shown in Figure 2 for WWER-1500 FA as an example. 1-st bending 1-st torsion 2-nd bending 2-nd torsion 3-rd bending Fig. 2 WWER-1500 FA mode shapes Vibration amplitude influence on FA modal characteristics was tested under kinematic loading of dummy supports with sine-wave vibration load at variation of dummy support acceleration am- plitude within the ranges 0,1-5 m/s2. Test results (Figures 3-5) have shown that dummy vibration resonant frequencies are displaced into low-frequency area at the increase of applied load amplitude and the transfer function amplitude under resonance conditions equal to response-impact amplitude ratio is decreased. Resonance frequency displacement to low-frequency area is practically stopped in some cases after reaching support acceleration amplitudes 1-3 m/s2, and increase of transfer func- tion module begins at resonance. 14 12 SG 4, А=0.1 ms-2 10 SG 4, А=0.3 ms-2 SG 4, А=1 ms-2 1 8 H SG 4, А=3 ms-2 -2 Mag 6 SG 4, А=5 ms 4 2 0 0 10203040 f/Hz Fig. 3 Transfer function under support vibration excitation. The phenomenon specified can be explained as follows. Relative displacement of FA compo- nents is not available under low vibration amplitudes, i.e. FA is characterized as solid. The proc- esses of FA component slipping in friction units (for example, slipping of fuel rods when turning in SG cells, motion of fuel pellets) are initiated with increase of vibration amplitude whereas the num- ber of units where slipping is available is increased when support vibration amplitude is higher. Equation of forced vibrations with viscous strength /1/ is proper for description of FA dummy vibrations with support acceleration amplitudes approximately to 1 m/s2: frequency, Hz frequency, Hz amplitude, m/s2 amplitude, m/s2 а) b) frequency, Hz frequency, Hz amplitude, m/s2 amplitude, m/s2 c) d) а) 1-st mode b) 2-d mode c) 3-d mode d) 5-th mode Fig. 4 Transfer functions of TVS-2M dummy frequency, Hz amplitude, m/s2 Fig. 5 Transfer functions of WWER-1500 TVS dummy (3-d mode) 2 F0 sin(ωt) &x&+ 2nx& + ω0 x = (1) m (where х – displacement; n - inelastic strength factor; ω0 - natural frequency, F0 – constraining force amplitude; ω - constraining force frequency, m – mass), in which inelastic strength factor n is increased when vibration amplitude is higher.
Details
-
File Typepdf
-
Upload Time-
-
Content LanguagesEnglish
-
Upload UserAnonymous/Not logged-in
-
File Pages12 Page
-
File Size-