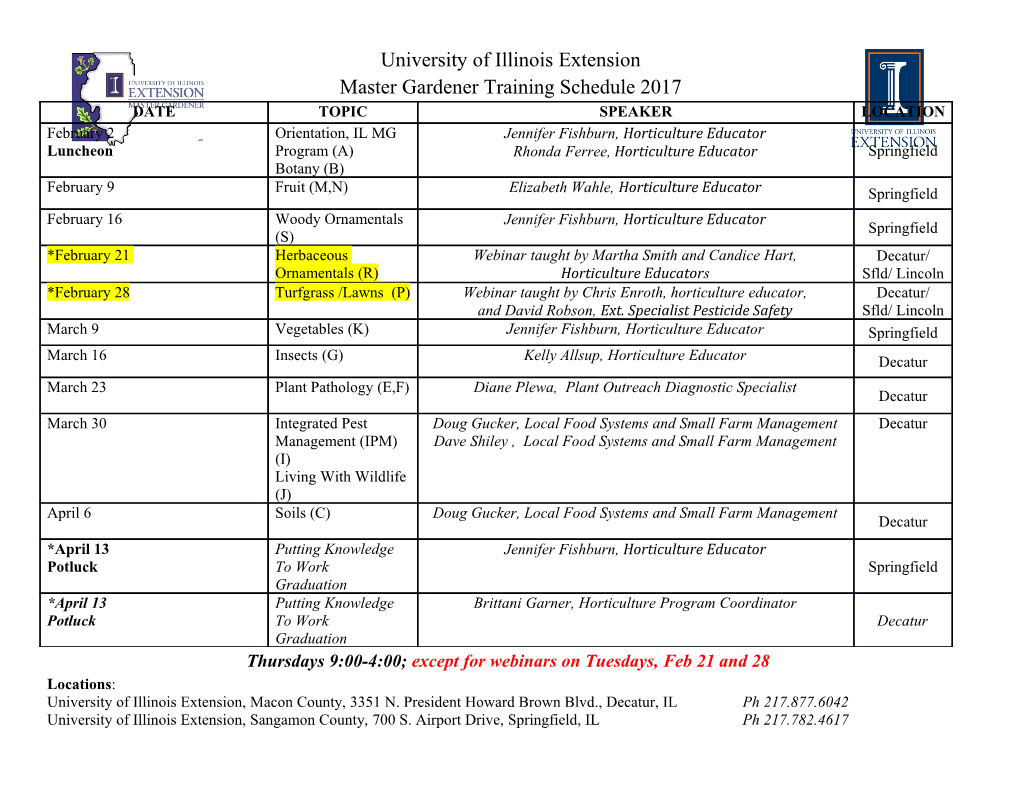
Safety First Strategically Reduce Hand Injuries Using the Hierarchy of Hazard Control In 2012, a steelworker in the declining, hand injuries were on Hazards are ever-present in United States sustained a lacera- the rise. Furthermore, it identi- the steel plant environment, tion on his hand, which subse- fied that several factors contrib- and a heightened awareness quently led to a fall and a head ute to an increased risk of hand and emphasis on safety is injury, ultimately resulting in his injuries, including: lack of aware- a necessary priority for our death. The average manufactur- ness, lack of education, not wear- industry. This monthly column, ing employee often fails to rec- ing required PPE and compla- coordinated by members ognize the potential severity of cency. In response to these find- of the AIST Safety & Health hand injuries, which can lead to ings, U. S. Steel devised a number Technology Committee, focuses a lack of “buy-in” to workplace of strategies under the following on procedures and practices safety practices. Employees do hazard-elimination industry-rec- to promote a safe working not always appreciate how quick- ognized categories: Elimination, environment for everyone. ly these injuries occur and how Substitution, Engineering Cont- life-altering they can be. The rols, Administrative Controls and key to a safer, more efficient and Personal Protective Equipment. more cost-effective workplace is eliminating the hazards alto- gether, including engineered 1. Elimination — Avoiding the solutions. When a hazard can- Hazard or Risk Before It Author not be eliminated, steps must be Occurs taken to improve safety training and personal protective equip- U. S. Steel introduced a compa- ment (PPE). ny-wide Hazard Identification Joanne Zaraliakos In Canada, more than 500,000 and Risk Assessment Program safety supervisor, U. S. Steel hand injuries1 occur in the work- beginning in 2012. Following Canada – Hamilton Works, Hamilton, Ont., Canada place each year. Approximately specific training in hazard [email protected] one-third of these preventable identification, each manager/ injuries are serious enough to supervisor is tasked to pro- become a “days away from work” actively identify, prioritize case. and eliminate hazards in his/ Common types of hand inju- her area. This is achieved ries in the workplace include: by incorporating new engi- Contact neered solutions and re-evalu- • Laceration/abrasion/ ating the Safe Job Procedures, Comments are welcome. puncture. a document that describes If you have questions about • Crush. the details and potential haz- this topic or other safety • Foreign body. ards of a task. To encour- issues, please contact • Avulsion/degloving. age buy-in and widespread [email protected]. Please • Strain/sprain. implementation, a range of include your full name, • Burn/frostbite. incentive programs have been company name, mailing • Fracture/break/ developed to increase safety address and email in all dislocation. awareness and recognition. correspondence. For example, the Chairman’s In 2010, United States Steel Safety Excellence Award is Corporation began a reflective presented to the plant with and investigative process regard- the best safety record and the ing hand safety. This investiga- greatest number of completed tion revealed that, although Hazard Elimination Projects. overall injury numbers were As a result, U. S. Steel as a AIST.org August 2013 ✦ 41 Safety First whole completed 8,685 projects in 2012, effectively injury could profoundly impact their lives. As part eliminating areas of medium to high risk. of this exercise, employees are asked to attempt to perform a variety of tasks without the use of their fingers and/or hands. In addition, injured 2. Substitution — Upgrading Outdated workers are invited to visit U. S. Steel plants across Equipment North America to explain how their hand injuries changed their lives. These stories personalize the U. S. Steel has also found opportunities to replace experience and emphasize that hand injuries can older, heavier and less ergonomically designed easily happen to anyone if proper care is not taken. equipment with newer, ergonomically correct mod- Finally, regular safety conversations between super- els. For example, heavy crimpers used for banding visors and employees are an effective way to remind steel coils are being updated to a lighter, powered, each other to stay focused on doing their respective cordless model. This reduces repetitive strain inju- jobs safely. ries in addition to eliminating an air-hose tripping hazard. Another example is the substitution of open blade knives with rounded-end box cutters 5. Personal Protective Equipment — The Last that do not directly expose employees’ hands to Line of Defense the blade. Gloves — Employees often start a task without putting on their gloves because they fail to recog- 3. Engineering Controls — Re-Engineering nize that gloves make a marked difference in hand Older Equipment safety. A Liberty Mutual study2 has demonstrated that at least 60% of hand injuries are caused by not Ensuring that equipment is properly identified and wearing gloves or by wearing the wrong gloves for guarded is an important method of keeping hands the task. away from danger zones. One example would During incident investigations, employees some- be the installation of two-handed safety control times stated that they could not properly perform interlocks and light curtains to stop equipment a particular job with the glove options they had from running when hands are in a danger zone. available. Most frequently, employees complained Every day, new tools are being engineered with employee input to promote correct posture and healthy movement while performing tasks. These efforts are critical to preventing repetitive motion Figure 1 injuries and reducing the need for employees to do “restricted work.” 4. Administrative Controls — Revising Training and Policies Part of an effective plan is ensuring that all policies, safety conversation procedures, and training pro- grams have been updated to specifically place an emphasis on hand safety. Three policies specific to hand safety are used as part of the U. S. Steel safety training program, including: • No-Touch Tool policy. • No Jewelry policy. • 100% Glove policy (U. S. Steel Canada only). These policies help promote a positive safety culture in which employees are encouraged to be more aware of workplace hazards and how to protect themselves. To further emphasize this point, employees are asked to simulate how a hand Cut- and puncture-resistant rigger’s glove. 42 ✦ Iron & Steel Technology A Publication of the Association for Iron & Steel Technology Figure 2 that the gloves did not provide the dexterity they needed to do the task. The resulting reluctance to wear gloves greatly increases the potential for hand injury. In each of these cases where employees are reluctant to wear gloves, U. S. Steel has conducted research to find a better-suited glove for the task. Innovative glove technology offers products with A no-touch tool should be used to hold a chisel or punch, increased protection, comfort, breathability and to keep hands and fingers out of the impact zone. dexterity. In addition, employees are given greater access to PPE through the use of new on-site PPE cabinets or vending machines. Glove clips are also provided to allow employees to carry more results. Eliminating hazards before an injury occurs than one pair with them in case the type of work is key to attaining the goal of zero injuries. The changes. use of appropriate gloves and training is also essen- tial. Companies can promote buy-in from employees, No-Touch Tools — Most hand injuries involving achieve success and improve safety collaboratively by pinch points can be eliminated by using no-touch valuing workers’ feedback. tools. U. S. Steel continues to design no-touch tools in many shapes and sizes and provide hands-on References training to demonstrate the ease of use of no-touch 1. Human Resources and Skills Development Canada, “Our tools as well as promote their use. Hands at Work!” 28 February 2012. Accessed on 31 January 2013, www.hrsdc.gc.ca/eng/labour/publications/health_ safety/hands/page00.shtml. U. S. Steel believes that all incidents and injuries 2. T. Christensen and T. Braun, “Preventing Hand Injuries in can be prevented. Safety is a personal responsibility Construction,” Construction Executive, July 2006, pp. 40–41. of all employees, and management is accountable for ✦ Custom standard The indusTry’s firsT and only 2-year WarranTy. A promise of performance. • Quality assurance • Decreased maintenance • Safety • Peace of mind • Increased productivity • Cost savings Caldwell quality. Guaranteed. Learn more about our full line of products and services at caldwellinc.com. Or call our team of experienced engineers and technicians at 800.628.4263 to discuss the optimal lifting solution for your application. The Caldwell Group • 5055 26th Avenue, Rockford, Illinois 61109 • 800.628.4263 • caldwellinc.com AIST.org August 2013 ✦ 43.
Details
-
File Typepdf
-
Upload Time-
-
Content LanguagesEnglish
-
Upload UserAnonymous/Not logged-in
-
File Pages3 Page
-
File Size-