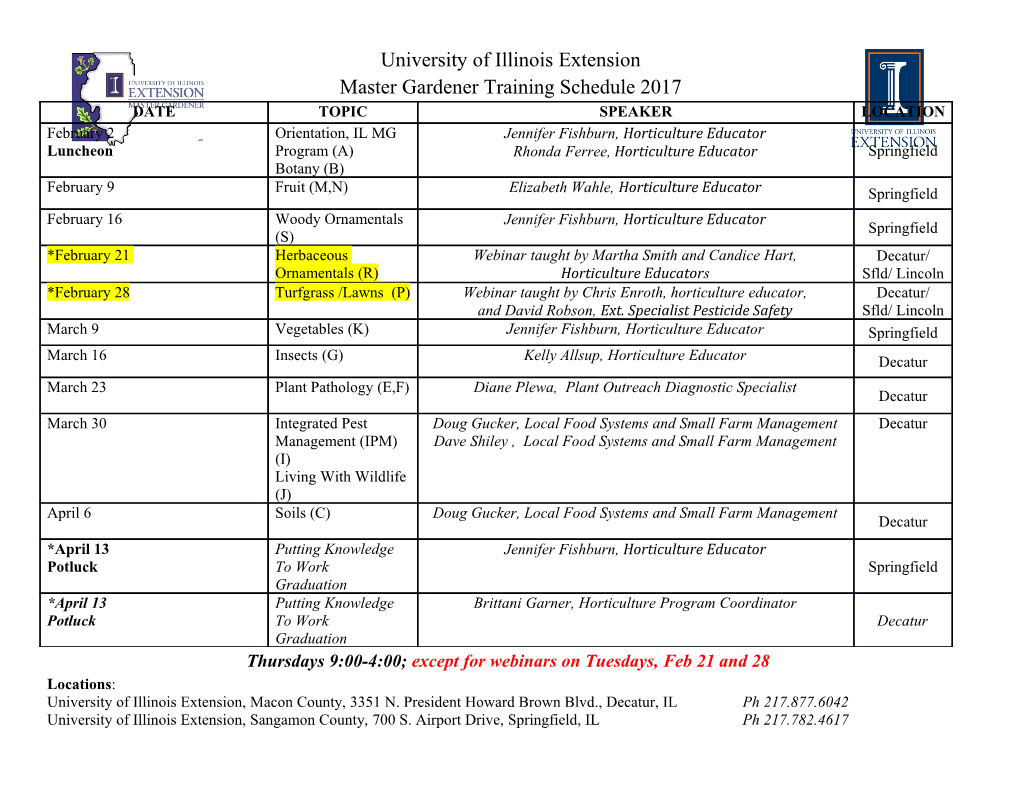
(1) FUTURE TRENDS IN FACTORY AUTOMATION (2) TECHNOLOGY FORECASTS FOR CIM Robert U. Ayres International Institute for Applied Systems Analysis Laxenburg, Austria RR-89-10 August 1989 Reprinted from Manufacturing Review, Volume 1, Number 2, June 1988 and Volume 2, Number 1, March 1989. INTERNATIONAL INSTITUTE FOR APPLIED SYSTEMS ANALYSIS Laxenburg, Austria Research Reports, which record research conducted at IIASA, are independently reviewed before publi­ cation. However, the views and opinions they express are not necessarily those of the Institute or the National Member Organizations that support it. Reprinted with permission from Manufacturing Review, Volume 1, Number 2, June 1988 and Volume 2, Number 1, March 1989. Copyright© 1988 and 1989 American Society of Mechanical Engineers. All rights reserved. No part of this publication may be reproduced or transmitted in any form or by any means, electronic or mechanical, including photocopy, recording, or any information storage or retrieval system, without permission in writing from the copyright holder. Printed by Novographic, Vienna, Austria iii FOREWORD These two papers form a natural package. Both appeared in earlier versions as IIASA Working Papers for the CIM Project. The second one also reflects a major thrust of the project, which culminated in the summer of 1989. (A second paper by J. Ranta reflecting on that effort will appear separately.) F. SCHMIDT-BLEEK Leader Technology, Economy, and Society Program MANUFACTURING PERSPECTIVE Future Trends in Factory Automation ROBERT U. AYRES Department of Engineering and Public Policy, Carnegie-Mellon University, Pittsburgh, PA 15213 This paper is a review of contemporary manufacturing technology. from both a U.S. muf world perspective. It emphasizes the historical background of the current trends toward comp1aerized a:utomation in terms of the increasing societal dem.ands for performance. whic11 in turn genera.Les requirements for ever grea.ter coniplexity and precision. This is the root <~f the "qual.ity cri3is." The author belie·ves thlit the ne.xl industrial revolution ·1.vU.l present a fund a mental sh i}1 from the use of h1.l1nan workers as "micro" decision makers (machine controllers) in fadors lo the use of "smart sensors" for this purpose. The paper elaborates som.e of the more spec~fic implications. DISCRETE MET AL PARTS MAl\TUF ACTURING However, in our diverse economy it is natural that some TECHNOLOGY (c. 1975) items, especially durable goods, are needed in small numbers and seldom replaced, while others are needed in larger he choice of manufacturing technology at present is numbers. The distinction most commonly made is between highly dependent on the scale of production. But batch and mass production. The value added of the U.S. some items, such as connectors, have long been manufacturing sector in 1977 was about equally divided standardized and mass produced in enormous between these two categories, as shown in Fig. 1. Batch numbersT whereas other items, such as auto engine plants or manufacturing can be further divided into one-of-a-kind space shuttles, are virtually custom made. The cost per unit (piece) or very small batches and medium to large batches, of items made in large numbers can be as little as one­ as indicated in Fig. 2. Unit cost differences arise from hundredth of the unit cost of the same item made individu­ several factors. In the first place, small volume production is ally. For example, the 600 distinct machining operations inherently much more labor intensive than large volume required for a V-8 cylinder block in 1975 cost around $25 in production because fewer functions are automated. Table 1 a mass production plant and only required 1 min. productive Metalwork ing Machin'!"-' labor time. By contrast, the same 600 machining operations TOTAL VA = $58.S,000 ,000 ( '977$ ) (2 6% of Du,abl€ Bate~.) carried out by skilled machinists in a job shop would have D required 600 min. of machinist labor and cost at least $2500 2 .1f--~ Other Botch-Produc-".". [ l, 2]. One of the ironies of this situation is that the special­ D of Durable aotch) ized machinery typically used in mass production, for exam­ -~ "'\ Other Heavy ple, the large transfer lines and multispindle drilling and Mac hi nery boring machines, are themselves customized, one-of-a-kind D (6 63 al Durable Botch) ~'lk @H u©~®~» \ (T o~ol B::: :ch "' 553 cl Durob l ~s\ investments. 1 If auto engine plants could be mass produced 26.7% as auto engines are, the capital costs would drop by as much 28.8% \ Mo ss Praduc ed Durables as 100-fold. D ( 4o! .77. o f Duroble9 ) A more recent example is instructive: helical rotors for compressors, as first produced in Sweden by hand in the ~ Non-Dura ble Batch 1950s, required up to 200 machinist hours. By 1967 this had ~ (40. 33 of No n -Durables) fallen to 6 h, by 1978 to 65 min. and in 1979 to 26 min. [3]. None of these advances utilized numerical control, which ~ Non - Du ra ble Moss Ll (59.77. of Non-Durables} entered the picture subsequently. 1The design of an auto engine plant , capable of producing 120 units per hour for 20 yea rs, requires about 60,000 engineering man-hours 12]. FIG. I. Distribution of manufacturing value added (Source: Miller, 1983 (11)) © Copyright 1988 American Society of Mechanical Engineers 93 Type o f production : Batch Ma ss 34% - holidays, vacations 0%_j________ J_ _ L__ ___ ___L _ L ________ (a) 1003,~------------------.-~-----~ 44% - incomplete use of 2nd and 3rd shifts 0% ~ ;_arge ,, complex 1-10 10-300 Over 200 _§ part ~ Small "Ci. simple 1-300 300-15,000 Over 10,000 ....> part Typical Aircraft, Mar ine engines, Autos, products large turbines . large electric fasteners, centrifuges motors, tractors small appliances 28% - plant shu td own Typical Manual , NC with auto machines stand·alonc pan.hand li ng, Transfer, NC machining cell, dedicated Hex mfg. svst. special machine FIG. 2. Characlerislics of melal producl manufacluring (Source: (b) American Machinist, 1980 [4]) shows the progressive elimination of manual operations by automated equipment of increasing degrees of sophistication. Another re ason for the big difference in unit cost between mass production and piece production in a job shop is that machines can be utilized much more efficiently in the former case. Differences in typical machine utilization patterns as a function of scale of production are shown in Fig. 3. It is noteworthy that in a typical job shop machines a re only tended about 20 % of the time and only 6% of the 'fablf' I. Comparison of manual manufaduring steps elimination by various dP.grees of automation 27% - plant shut­ (Sour<~: General Ac•:ount.ing Office 197.6: p. 38) down (2 week shut­ down, Sundays, Production Methods 13 holidays) Stand- alone Machining Step Conventional NC center FMS (c) I. Move workpiece M M M c 22% - productive cuning to machine 2.. [.oad and affix M M M c workpie-ce on machine 3. Select an.d M M c c insert tool 4. Estab"llsh, and M c c c set speeos 5. Control cutting M c c c FI G . 3 (a) Low-volume manufacluring, (b) mid-volume manufacluring, 6. Sequenee tools M M c c (c) high-volume manufacluring (Adapled from: American Machinist, and motions 1980 [4]) 7. Unload part M M M c from mac~ine time is used for productive cutting. This contrasts to 22% M = manual op-eration C = computer-controller operation productive cutting in a mass production facilit y [4] . 94 Manufacturing Review vol I, no 2, June 1988 The key characteristic of mass production is that it macri •n.n9wste,., achieves low unit cost by extreme specialization of equip­ woo .-_ y~--T ment. For automobile engine or transmission production, the heart of the plant would consist of a set of giant multiple­ spindle machines, generally with between l 00 and 1000 tools, mainly drills, cutting simultaneously. The spindles are "" ·· ~Cns1 oe• clustered in groups (or stations). v; un•t Con$!rucnor> m~ch •n r r v 0 u The mechanical requirements are exacting. Each of the Q.> 10 • .2' spindles in each station must be permanently positioned very ;;; precisely with respect to all the others. All the spindles in 1! each group must also be exactly synchronized, so that the 1 0 . resulting holes are not only parallel but also drilled to the Sm• ll t•uc l.. s exact same depth. Drill speeds must be precisely predeter­ t> •c vr l ~ mined for the same reason. The necessary simultaneity can 01 - f -t· 1···· 1 be achieved by mechanically linking all the spindles at each 10 1 10:? 103 104 105 106 107 station, via elaborate gear trains, to a single drive shaft. Or, number of products per month batch production mass production separate drive motors can be subject to a common controller. Workheads are either ON or OFF. Machines are designed to FIG. 4. Costs and automation versus volume (Source: Author, operate at a fixed speed over a fixed cycle that is optimum adapted from various sources) for the design application. Large groups of machines (sections) are also synchron­ ously linked together mechanically via indexing transfer lines. solid-state monolithic integrated circuits and large-scale They are not individually controllable, hence not easily integration (LSI, VLSI) modern computers are of the order adaptable to other design specifications. If the product being of 100,000 times less error prone than human workers [8]. In manufactured becomes obsolete the custom-built manufactur­ effect, the direction of technological change (in the industri­ ing equipment is likely to be scrapped, since adaptation is alized countries, at least) is inexorably toward the substitu­ difficult or impossible.
Details
-
File Typepdf
-
Upload Time-
-
Content LanguagesEnglish
-
Upload UserAnonymous/Not logged-in
-
File Pages28 Page
-
File Size-