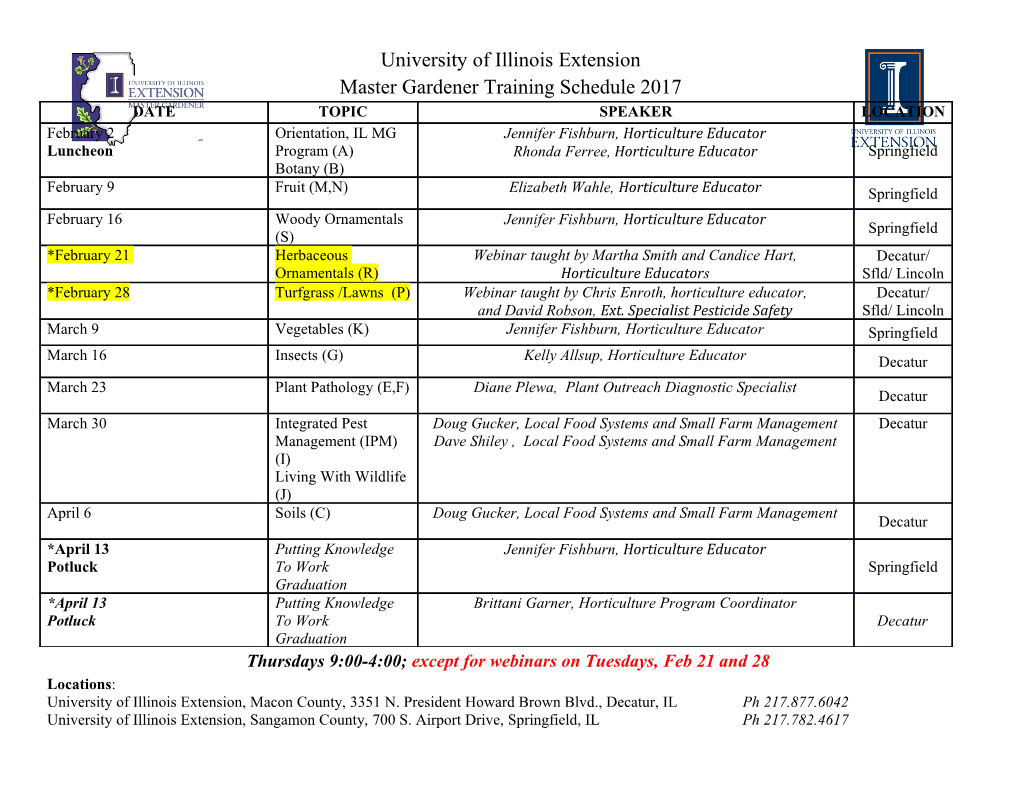
Proceedings of ASME Turbo Expo 2017: Turbomachinery Technical Conference & Exposition GT2017 June 26-30, 2017, Charlotte, North Carolina, USA GT2017-63776 ANALYTICAL MODEL FOR THE PERFORMANCE ESTIMATION OF PRE- COOLED PULSE DETONATION TURBOFAN ENGINES Carlos Xisto, Fakhre Ali, Olivier Petit and Andrew Rolt Tomas Grönstedt Cranfield University Department of Mechanics and Maritime Sciences Bedfordshire, UK Chalmers University of Technology Gothenburg, Sweden Anders Lundbladh GKN Aerospace Trollhättan, Sweden ABSTRACT 퐷CJ Velocity of the detonation wave, m/s. This paper proposes a pulse detonation combustion (PDC) 푓 Fuel-to-air mass ratio (local). model integrated within Chalmers University’s gas turbine 퐹푠 Specific thrust, m/s. simulation tool GESTPAN (GEneral Stationary and Transient 푔 Mass flow rate, kg/s. Propulsion ANalsysis). The model will support the development 퐿 Length of the PDC chamber, m. of novel aircraft engine architectures exploiting the synergies MCJ Propagation Mach number of detonation wave. between intercooling, aftercooling and PDC. The proposed M푓 Fill and purge Mach number. engine architectures are based on a reference high bypass ratio 푝 Static pressure, Pa. geared-turbofan engine model with performance levels 푃 Total Pressure, Pa. estimated to be available by year 2050. Parametric studies have 푇0 Stagnation temperature, K. 푇 Static temperature, K. been carried out for each proposed advanced architecture, t Time, s. providing engine cycle mid-cruise design point parameters. 푡CJ Detonation wave propagation time, s. Design sensitivity studies related to intercooling technology in 푡 Exhaust time, s. combination with a PDC are further explored for a number of 푒푥 푡푑푒푐푎푦 Pressure decay time, s. heat-exchanger design effectiveness values and associated 푡푓 Fill time, s. pressure loss levels. The acquired results suggest that the 푡푝 Purge time, s. incorporation of PDC technology within a conventional core has 푡푝푙푎푡푒푎푢 Plateau state time, s. the potential to significantly improve engine thermal efficiency. 푈 Fill velocity, m/s. Incorporating intercooling improves the cycle performance for 푓 푈푝푔 Purge velocity, m/s. any pre-combustion OPR above 10 and contributes to an 훽 Purge fraction. increase in specific power over the entire range of OPR. Finally, 휀 Intercooler effectiveness the results demonstrate that aftercooling the high pressure 휂푏 Combustion efficiency compressor delivery air further improves core specific power, but 휂푝, Component i polytropic efficiency cancels out any SFC and thermal efficiency benefits arising from 휂푠, Component i isentropic efficiency pulse detonation. 휙 Local equivalence ratio. 훾 Ratio of specific heats. NOMENCLATURE 휋 Pressure ratio. 3 푐푏 Speed of sound of products, m/s. 휌 Density, kg/m . 푐푓 Speed of sound for fuel-air mixture, m/s. 휏 Cycle period, s. 푐푔 Speed of sound for purge air, m/s. 1 Copyright © 2017 by ASME Acronyms AC Aftercooler BPR Bypass ratio CEA Chemical Equilibrium with Applications FPR Fan Pressure Ratio HPC High Pressure Compressor IPC Intermediate Pressure Compressor IC Intercooler LHV Lower Heating Value OPR Overall Pressure Ratio (compression) PDC Pulse Detonation Combustor SFC Specific Fuel Consumption, mg/(N ⋅ s) TET Turbine Entry Temperature, K Subscripts 1-138 Station designation shown in Fig. 5 4 PDC Cycle averaged properties 푏 Plateau state s Scavenge state CJ Chapman-Jouguet state FIGURE 1 – ILLUSTARTION OF A PULSE DETONATION 푛 Initial condition (prior to detonation) CORE (CHALMERS UNIVERISTY). b-c) Detonation and propagation, the valve closes and a INTRODUCTION detonation wave is initiated near the closed end of the In Europe the H2020 ULTIMATE (Ultra Low emission tube. The wave will then travel towards the open end Technology Innovations for Mid-century Aircraft Turbine of the tube; Engines) project [1] is exploring synergistic combinations of d-e) Blowdown, a rarefaction wave propagates towards the radical technologies to target reductions in all three major loss closed end of the tube, starting the exhaust process, sources in a state-of-the-art 2015 aero-engine [2]: i) combustor until the initial (purge) pressure is reached. During irreversibility; ii) core exhaust heat rejection; and iii) excess of blowdown the valve is still closed; kinetic energy in the propulsive jets. To address loss source iii), high bypass ratio geared f) Purging, the valve is opened and HPC air is used to turbofans are being investigated [3] as well as counter-rotating completely or partially purge the tube of the hot open rotors [4]. With regards to loss source ii), introducing products of detonation. cooling within the compression system has been a widely To be able to operate in such conditions, a basic PDC typically adopted approach to enable higher overall pressure ratios (OPRs) comprises a set of straight channels of constant cross-section for a given turbine entry temperature (TET) [5, 6]. This can be area arranged in a can-annular configuration around the engine seen as an indirect means of targeting the loss from core exhaust core annulus, as illustrated in Fig. 1. Each channel includes a heat rejection, since higher turbine expansion ratios lead to valve that controls the intake of working gas during purge and reduced core exhaust temperatures. Intercooling in gas turbine fill. A plenum/buffer volume (not visible in Fig. 1) is located aero-engines has been the subject of extensive research in several between the high pressure compressor (HPC) and PDC. This EU research projects with recent results revealing that volume serves to damp the pressure fluctuations arising from the improvements in fuel burn efficiency of the order of 3-5% are unsteady operation of the detonation cycle, and it could also achievable [5, 7]. accommodate an aftercooler before combustion. In terms of addressing loss source i), the entropy generation A fundamental thermodynamic analysis revealed that a PDC of a conventional combustor can be reduced by adding a topping core has the theoretical potential to improve the thermal cycle [8] or a pressure-rise combustion system such as a pulse efficiency of a gas turbine cycle by 10 to 15% [9]. However the detonation combustor (PDC) [9], see Fig. 1. A PDC is an unsteady nature of a pulse detonation cycle results in strong unsteady combustion device that burns fuel through the variations in mass flow, thermodynamic quantities and rotor inlet propagation of axial intermittent detonation waves. The unsteady angles [10], and it can even lead to periods of reversed flow [11]. cyclic operation comprises several phases. An illustrative This unsteady behavior poses numerous technical challenges example of a typical PDC cycle is shown in Fig. 2: when designing an effective combustor-turbine system and also a) Filling, the valve opens and the tube is filled with a when developing an effective system level model capable of uniform mixture of fuel-air at a given local modelling the behavior of a PDC under different operating equivalence ratio. conditions. 2 Copyright © 2017 by ASME FIGURE 2 - DIFFERENT PROCESSES OCCURRING IN THE PDC. A) FILLING ENDS; B-E) DETONATION PROPAGATION AND BLOWDOWN; F) PURGE STARTS Several models were developed to analyze the performance The work presented in this study proposes an integrated of pulse detonation engines. These included analytical aero-engine performance evaluation model, developed for the formulations, which are based on time and mass averaged conceptual design assessment of novel intercooled and thermodynamic properties over a PDC cycle [12, 13], or derived aftercooled pulse detonation turbofan engines. The implemented using classical thermodynamic steady state analysis with environment is constructed by integrating an analytically derived features of pulse detonation flow incorporated [9, 14]. Another PDC model within Chalmers University’s in-house aero-engine class of models [15] utilized time-accurate CFD analysis performance simulation tool called GESTPAN (GEneral including combustion reactions to generate performance maps Stationary and Transient Propulsion ANalsysis) [19]. The that could easily be integrated into an engine performance mathematical formulation of the developed PDC model is based tool [16]. These approaches were extensively validated for on the work of Endo et al. [13] and Wintenberger and different operating conditions and shown to offer an efficient and Shepherd [12]. The model caters for the chemical equilibrium robust way of predicting the performance of pulse detonation relations and gas dynamic theory to predict the PDC behavior in based engines. all phases of the pulse detonation cycle, and provides evaluation Pulse detonation combustion offers a natural synergy with of the associated key parameters (i.e. pressure rise, outlet intercooling and aftercooling of the compression system. In temperature, fuel mass flow and purge fraction). In previous constant volume combustion, reducing the combustor inlet studies the proposed methodology has been successfully applied temperature improves the volumetric efficiency of the to estimate the performance of single-tube air-breathing pulse system [17], allowing for more air-fuel to be combusted per detonation engines [12, 13] and to perform an exergy analysis on engine cycle. Moreover, precooling the flow results in higher a stationary gas turbine architecture powered by a pulse combustion pressure ratios [18], reduces the risk of pre- detonation combustor [20]. In this study, the application of the detonation and reduces the cooling requirements of
Details
-
File Typepdf
-
Upload Time-
-
Content LanguagesEnglish
-
Upload UserAnonymous/Not logged-in
-
File Pages14 Page
-
File Size-