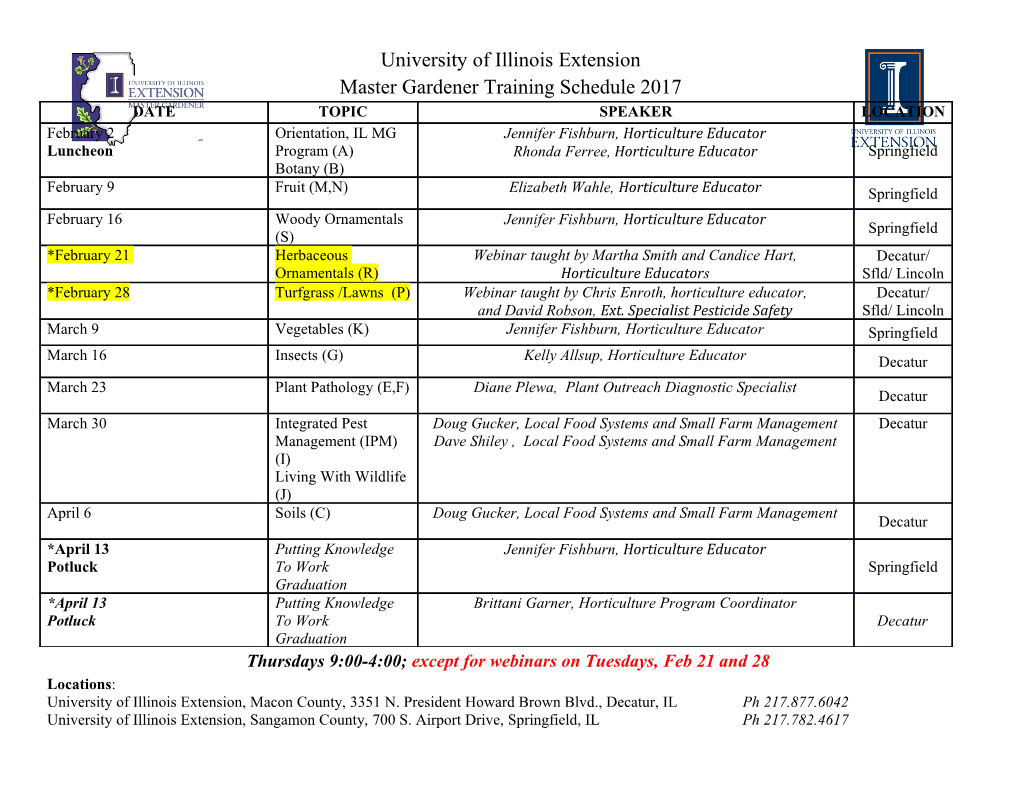
WHEC 16 / 13-16 June 2006 – Lyon France A Development of a High Pressure H2 Gas Injector with High Response by Using Common-Rail Injection System for Direct Injection H2 Fuelled Engines Kimitaka Yamanea, Masakuni Oikawaa, Tomonori Kitauraa, Kouta Mawataria, Takashi Kondoa, Yasuo Takagia, Yoshio Satob, Yuichi Gotob aHydrogen Energy Research Center, Musashi Institute of Technology 1-28-1 Tamazutsumi, Setagaya-ku, Tokyo, 158-8557, Japan [email protected] b National Traffic Safety and Environment Laboratory (NTSEL) 7-42-27 Jindaijihigashimachi, Fuchu-city, Tokyo 182-0012, Japan [email protected] ABSTRACT: The authors have developed a new generation hydrogen gas injector which may overcome the problems brought about by the previous injectors activated hydraulically. The hydrogen gas injector is activated electro-hydraulically by working fluid at 100 MPa fed by the common rail system developed for diesel engines to open the needle valve of the injector. And the hydrogen gas at high pressure of 20 MPa in the injector is directly injected into the combustion chamber. An experiment was carried out concerning the injection flow rates affected by the injection crankangle at two engine speeds such as 1000 and 3000 rpm, the temperature and pressure of the working fluid to obtain the characteristics of the injector. KEYWORDS : Hydrogen Gas Injector, Electro-hydraulic System, Common-Rail 1. Introduction The development of hydrogen gas injectors has been being carried out for direct injection hydrogen fueled engines in Musashi Institute of Technology for many years[1], [2], [3], [4], [5]. Because it has been found theoretically that the direct injection of hydrogen fuel generates about 1.2 times as much output power as that of a gasoline engine and that the direct injection also brings about greater thermal efficiency than that of a hydrogen engine with external mixture formation owing to greater cooling loss than that by hydrogen fueled engines with direct injection. The previous hydrogen gas injectors were activated mechanically or hydraulically by working fluid at 20 ~ 30 MPa fed by a diesel plunger pump to open the poppet or needle valves of the injectors. And the hydrogen gas at high pressure such as 6 ~ 10 MPa in the injectors was directly injected into the combustion chambers. It was found experimentally that the previous injectors needed greater injection duration in crankangle as the engine was operated at higher engine speed. As a result, the thermal efficiency got worse as the engine speed became greater. It is necessary to have the injector activate in as small crankangle as possible to increase the thermal efficiency even at greater engine speed. The required injection crankangle is smaller than 30 deg. during which the piston of the engine seldom moves around the top-dead-center. And the direct injection hydrogen fuelled engine is subject to NOx emission even in totally lean mixture op- eration, namely low load, because of the heterogeneous combustion. It has been found recently that the de-NOx catalyst developed for fossil-fuel lean mixture engines was effec- tive also in hydrogen-fuelled engines when hydrogen gas was injected into the exhaust manifold upstream of the de-NOx catalyst [6]. It is very important to develop an injector with quick response activation by using the common-rail system developed for diesel engines where the pressure of the working fluid is large enough and the system works electro-hydraulically so that a swift and multi-injection control might be available. 1/7 WHEC 16 / 13-16 June 2006 – Lyon France 2. A New Generation Common-Rail Type H2 High Pressure Injector In order to operate the injector electro-hydraulically coupled with engine control units, for the needle valve of φ29 the injector to move up and down as swiftly as possible Receptacle and for practical use for truck engines with 4 valves for Flow Control Electric Magnet each cylinder, a common-rail type hydrogen gas injector Upper Plate Servo-valve was designed to know whether the common-rail system Flow Control Working Fluid was applicable to the high pressure gas direct injection for Lower Plate a hydrogen fueled internal combustion engine of a (Pressure:100 Map) medium-duty truck with the loading capacity of 4 tons by making use of the parts of a common-rail injector (Part No. Hydrogen Supply 23670-39015, Denso) developed for diesel engines. Drain Port (Pressure: 20MPa) Figure 1 shows the cross-section view. And Figure 2 shows the overall photograph of the injector developed. mm The diameter of the valve seat was 4 mm. The tip angle 53 of the needle valve was 90 degrees. The electric magnet 2 servo-valve, the flow control upper and lower plates and the fixtures were removed from the original common-rail Pushing Rod diesel injector to assemble the parts into this new Lift Sensor common-rail type hydrogen gas injector. The others were (Max. Lift:0.3 mm) newly designed for hydrogen gas injection at the design pressure of 30 MPa at the maximum and the design pressure of the working fluid was 200 MPa at the Needle Valve maximum. A rubber O-ring and a doughnut-shape resin sheet made of Teflon were used to seal between the φ4 hydrogen gas and the working fluid. A lift sensor (A φ12 Special Model; Applied Electronics Corp.) was embedded in the injector as shown in Fig. 1 to measure the Fig. 1 Cross-Section View of Common-Rail movement of the needle valve. Type High Pressure Injector The common-rail type high pressure hydrogen gas injector works as follows. Receptacles The command signal has the injector driver generate a large driving electric current. The electric magnet servo-valve moves WF Supply Inlet WF Drain up to open the outlet of the working fluid pressurized in the flow (100Map) control upper and lower plates. The pressure falls down swiftly and the pushing rod moves up together with the needle valve which is forced to move upward by the hydrogen injection pressure. As a result, the needle valve opens and the hydrogen at the pressure of 20 MPa is injected out. Once the command signal and the electric current are off, the electric magnet servo- 約φ64 mm H2 Supply Inlet valve moves down to close the outlet of the working fluid 3 5 (20Map) 2 resulting in building up the pressure in the flow control upper and lower plates. Consequently the pushing rod moves down while pushing the needle valve to the valve seat. In the end, the hydrogen injection stops. Injector Body 2. Experimental Apparatus and Method Figure 3 shows the schematic diagram of the experimental apparatus. The common-rail driving system developed for a 4- Injection Nozzle cylinder, water-cooled diesel engine was utilized for the injector test rig in this experiment. The pump was driven by a AC motor and diesel fuel as the working fluid was fed to the common-rail, Fig. 2 Photograph of the injector then to the injector. The reason why diesel fuel was used as the working fluid was that all the parts to control the flow of the working fluid were originally made for diesel fuel. The pressure of the working fluid of 100 MPa was used in principle except for the experiments for the influence of the working fluid pressure on the injection flow rate. The pressure was adjusted by the relief valve in the line. The working fluid then went back to the tank. The temperature of the working fluid was measured at the working fluid tank. The temperature was, in principle, kept from 50 to 53 ℃. except for the experiments for the influence of the working fluid temperature on the injection flow rate. On the other hand, hydrogen gas stored at 35 MPa in the hydrogen high pressure tank was reduced by the pressure regulator to 20 MPa upstream of the mass flowmeter. The flow rate of the hydrogen injected out by 2/7 WHEC 16 / 13-16 June 2006 – Lyon France Oscilloscope Relief Valve Readout Outlet Cooling for Pressure Unit Water Control Pressure Current Probe Sensor Pressure Guage Injector WF Micro- WF Filter Driver Tank Processor Constant Current Common-rail DC 12V AC 3-Phase Supply Amp. 200V Readout Injector Unit Motor Pump Silencer Pressure Sensor Mass Pressure Temp. Sensor Data Logging PC Regulator Flowmeter WF: Working Fluid AC: Alternate Current Surging Tank Surging Tank DC: Direct Current PC: Personal Computer H HP Tank 2 HP: High Pressure Fig. 3 schematic diagram of the experimental apparatus the common-rail type hydrogen gas injector was measured by a mass flowmeter (Model 1.25 No. F-1238-A-12-11N, Oval Corp.) 1.20 calibrated in advance by injecting the hydrogen gas at 20 MPa by the tested 1.15 0 injector. The temperature and the pressure V) ( 1.10 Lift Rubber O-Ring of the hydrogen gas were measured by a E t x H2 pressure sensor and thermocouple u Leading p 1.05 t Wire upstream of the injector respectively. u O The lift sensor employed in this experiment 1.00 H was an inductance type one. The 2 0.95 Pushing Rod H Valve Seat calibration was carried out identically in the Electric 2 Needle Coil Ball Bearing Joint Valve same manner as the injector works in the 0.90 experiment. Figure 4 was the calibration 0.0 0.1 0.2 0.3 0.4 0.5 0.6 0.7 0.8 0.9 1.0 curve obtained. It is found from Fig. 4 that Lift x (㎜) there is the maximum output at 0.4 mm Fig. 4 Calibration Curve : Needle lift vs Output from the zero lift.
Details
-
File Typepdf
-
Upload Time-
-
Content LanguagesEnglish
-
Upload UserAnonymous/Not logged-in
-
File Pages7 Page
-
File Size-