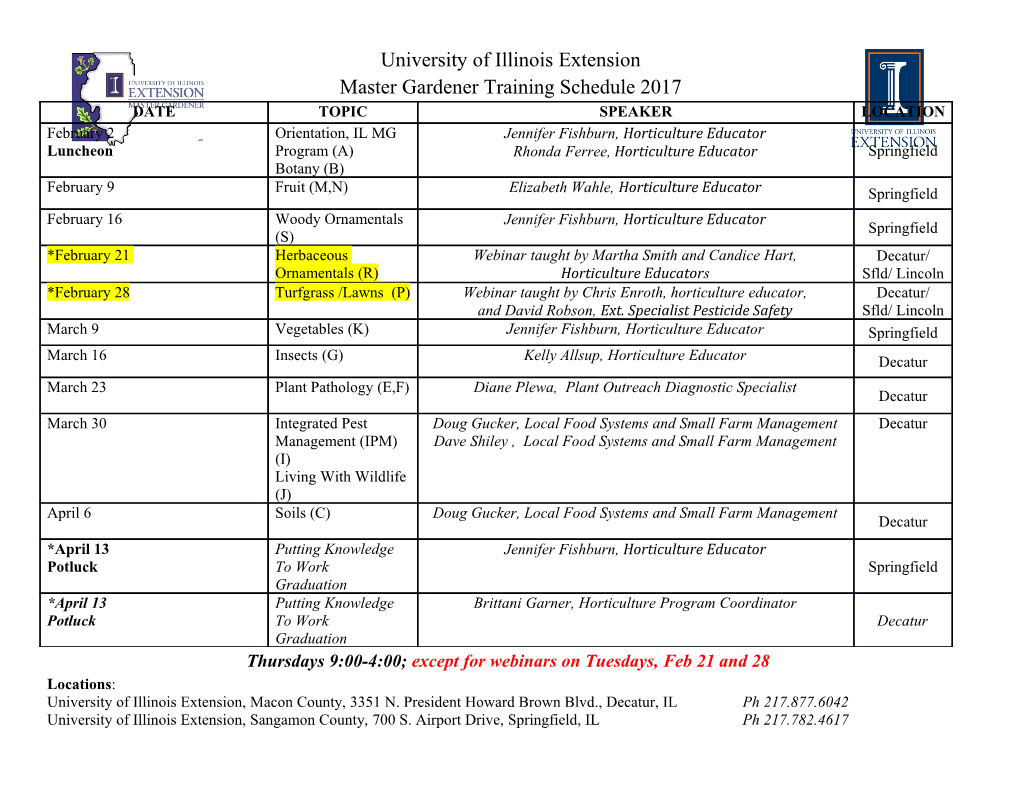
MSEL A 11 ID 3 SEDb^d Materials Science and Engineering Laboratory METALLURGY NAS-NRC Assessment Panel April 6-7, 1995 NISTIR 5582 U.S. Department of Commerce Technology Administration National Institute of Standards and Technology Technical Activities \ 1994 The cover shows the ferromagnetic resonance peaks in a multilayered spin valve. For each curve, the field is applied the plane of the film at angles from 0 to 360 degrees. HSEL Materials Science and Engineering Laboratory METALLURGY E. N. Pugh, Chief S. C. Hardy, Deputy NAS-NRC Assessment Panel April 6-7, 1 995 NISTIR 5582 U.S. Department of Commerce Technology Administration National Institute of Standards and Technology Technical Activities 1994 U.S. DEPARTMENT OF COMMERCE Ronald H. Brown, Secretary TECHNOLOGY ADMINISTRATION Mary L. Good, Under Secretary for Technology NATIONAL INSTITUTE OF STANDARDS AND TECHNOLOGY Arati Prabhakar, Director Certain companies and commercial products are mentioned in this report. They are used to either completely specify a procedure or describe an interaction with NIST. Such a mention is not meant as an endorsement by NIST or to represent the best choice for that purpose. METALLURGY DIVISION CHIEF E. Neville Pugh Phone: (301) 975-5960 DEPUTY CHIEF Stephen C. Hardy Phone: (301) 975-6159 SPECIAL ASSISTANT John H. Smith Phone: (301) 975-5961 GROUP LEADERS Corrosion Richard E. Ricker Phone: (301) 975-6023 Electrodeposition Gery R. Stafford Phone: (301) 975-6412 High Temperature Materials Chemistry John W. Hastie Phone: (301) 975-5754 Magnetic Materials Lawrence H. Bennett Phone: (301) 975-5966 Mechanical Properties and Performance Leonard Mordfin Phone: (301) 975-6168 Metallurgical Processing John R. Manning Phone: (301) 975-6157 Metallurgical Sensing & Modeling George A. Alers Phone: (301) 975-6140 Microscopy Facility Stephen C. Hardy Phone: (301) 975-6159 IV ABSTRACT This report summarizes the FY 1994 activities of the Metallurgy Division, National Institute of Standards and Technology (NIST). These activities center on structure-processing-properties relations of metals and alloys, on methods of measurement, and on the generation and evaluation of critical materials data. Efforts comprise studies of metals processing and process sensors; advanced materials - including metal matrix composites, intermetallic alloys, and superconductors; corrosion and electrodeposition; mechanical properties; magnetic materials; and high temperature reactions. The work described also includes cooperative programs with a professional society (the Corrosion Data Program with the National Association of Corrosion Engineers); with a trade association (the Temperature Sensor Program with the Aluminum Association) and several with industry including the Powder Atomization Consortium with five companies. The scientific publications, committee participation, and other professional interactions of the 53 full-time and part-time permanent members of the Metallurgy Division and its 30 guest researchers are identified. V TABLE OF CONTENTS Page OVERVIEW 1 METALLURGY DIVISION ORGANIZATION CHART 5 RESEARCH STAFF 7 TECHNICAL ACTIVITIES Corrosion 15 Electrodeposition 25 High Temperature Materials Chemistry 43 Magnetic Materials 49 Mechanical Properties and Performance 59 Metallurgical Processing 71 Metallurgical Sensing & Modeling 91 OUTPUTS/INTERACTIONS Publications 99 Industrial and Academic Interactions 113 Technical/Professional Committee Leadership Activities 135 APPENDIX Organizational Chart National Institute of Standards & Technology A1 Organizational Chart Materials Science and Engineering A2 vii OVERVIEW METALLURGY DIVISION (855) E. Neville Pugh, Chief Stephen C. Hardy, Deputy Chief June Toms, Secretary The primary mission of the Metallurgy Division is to assist US industry in improving its competitiveness, and, to meet this objective, the Division brings to bear its traditional strengths in measurement science and materials characterization on industrial problems with significant competitive and economic impact. Major thrusts have grown about these strengths in the areas of materials processing, particularly in casting, powder processing and process sensing, and in nanostructured materials and electronic packaging. Each of these activities benefitted significantly in FY94 from the Division’s growing competence in modeling, which is part of a concerted Materials Science and Engineering Laboratory (MSEL) effort to strengthen and broaden this essential capability. The Division also has maintained strong programs in the traditional NIST areas of standards and data which are essential to maintaining the nation’s technological infratructure. In the former, we have continued to collaborate with the American Society for Testing Materials (ASTM) and manufacturers of hardness measuring machines and hardness calibration blocks to establish a hardness standardization facility at NIST. Collaboration with other national laboratories has been initiated to ensure that the US national hardness standard is compatible with hardness standards worldwide. In the area of data, the National Association of Corrosion Engineers (NACE)-NIST Corrosion Data Program has continued successful collaborative programs with industry to develop computerized databases and expert systems for use in materials selection and corrosion control. Some indications that the Metallurgy Division is effectivly helping US industry are provided by examining a few mature programs and the results they have achieved. For a number of years the Division has had a collaborative program with the Aluminum Association to develop a non-contact method of measuring the temperature of aluminum sheet during the hot rolling process. This year a prototype eddy current sensor was operated for a four month period at the Alumax Mill Products plant in Lancaster, Pennsylvania. This trial was successful and the commercialization of the device is now being explored. In another long term collaborative program, the NIST/Industrial Consortium on Intelligent Processing of Rapidly Solidified Metal Powders by Inert Gas Atomization has completed its work to develop control systems for atomizers. The Expert System Control Shell (ECSS) technology developed in this program is being transferred to a commercial atomizer at Crucible Research. In a third program which was initiated in FY93, NIST, Xerox Corporation, and Cornell University collaborated in the study of the magnetic nanocomposites of y-Fe3 0 4 and a polymer. As a result of developments in these materials achieved in the collaboration, Xerox Corporation is setting up a pilot plant for large scale production of these nanocomposites. 1 The details of the research in each project in the Division are described in this report under sections corresponding to the Division’s seven groups: CORROSION ELECTRODEPOSITION HIGH TEMPERATURE MATERIALS CHEMISTRY MAGNETIC MATERIALS MECHANICAL PROPERTIES AND PERFORMANCE METALLURGICAL PROECESSING METALLURGICAL SENSING AND MODELING Highlights of the Division’s research activities are summarized below. More extensive descriptions of these and other Division projects may be found in the project summaries. • The NACE-NIST Corrosion Data Program continued to collaborate with industry to produce personal computer based corrosion information and advisory systems. During FY94, three systems were released for public distribution and four more systems were distributed to industrial review committees for evaluation prior to public release. • The Electrodeposition Group has made significant progress in the development of mercury-free dental restoratives. The approach being used is based on the premise that ductile silver and silver coated intermetallics will cold-weld to form a dense filling, under moderate pressure and ambient temperature, if the surface has undergone appropriate treatment to remove the native air formed oxide. The transverse rupture strength of silver which has been consolidated after treatment in 2% fluoroboric acid was six times greater than that of identical silver powder consolidated without treatment. • Measurements on ultra-low carbon, low-carbon, and high-strength-low-alloy indutrial sheet steels has succeeded in establishing an excellent correlation between Vickers hardness and the magnetic Barkhausen signal for these steels. • Ferromagnetic resonance measurements have shown that the magnetic layers in giant magnetoresistance spin valve structures maintained their distictive character after annealing at 400 °C for 30 minutes, but the FeMn pinning layer showed irreversible changes after 20 minutes at 250 °C. • As part of the National Aging Aircraft Research Program, an extensive research project was carried out to study the manner in which cracks propagate in the presence of multiple site damage. The project involved ten tests of the largest structural aluminum panels ever tested in tension. Analyses of the results by two different procedures indicated a reasonably good capability for predicting the critical fracture stresses. 2 • In work with the Consortium on Casting of Aerospace Alloys, crystallographic characteristics of grain defects in single crystal turbine blades were identified. A model was developed to describe dendrite growth in complex containers, identifying some of the conditions leading to formation of these defects. • In other work with the Consortium on Casting of Aerospace Alloys, measurements of unsurpassed accuracy have been made of selected thermophysical properties of Inconel 718 and Ti-6A1-4V alloys at high temperatures
Details
-
File Typepdf
-
Upload Time-
-
Content LanguagesEnglish
-
Upload UserAnonymous/Not logged-in
-
File Pages158 Page
-
File Size-