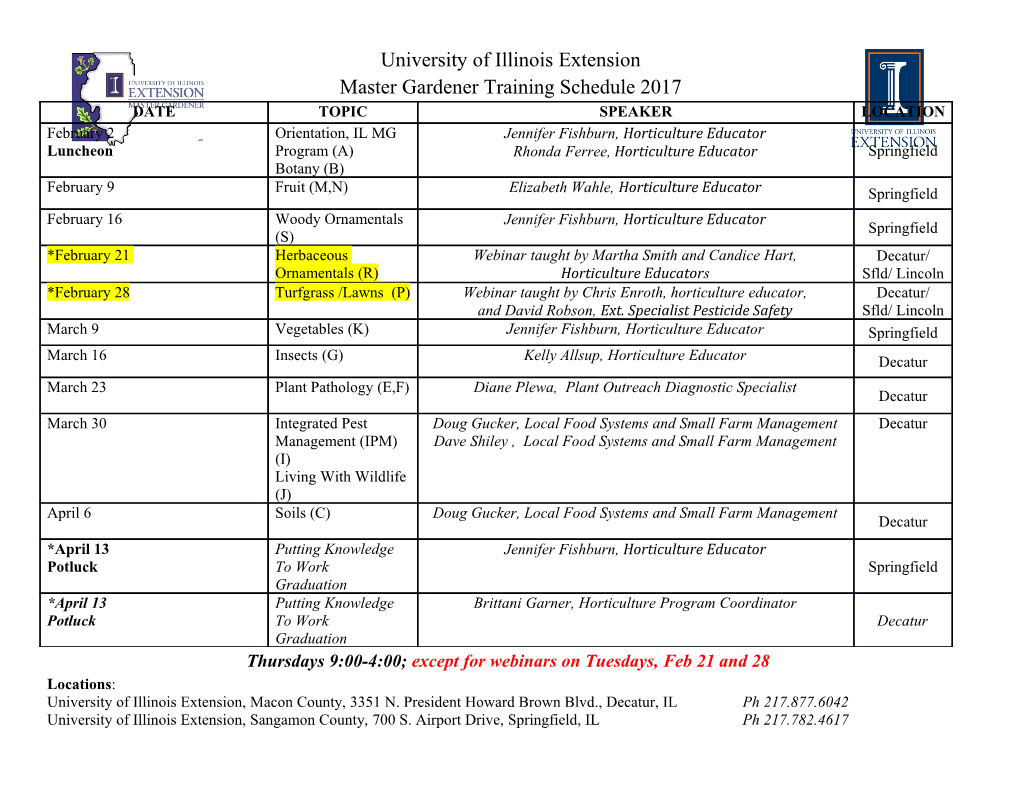
Super-resolution and ultrahigh-throughput of focused-ion-beam machining Andrew C. Madison1 John S. Villarrubia1 Kuo-Tang Liao1,2 Joshua Schumacher3 Kerry Siebein3 B. Robert Ilic1,3 J. Alexander Liddle1 and Samuel M. Stavis1,* Abstract Recent studies have demonstrated lateral super-resolution of focused-ion-beam machining by sacrificial masking films. However, the experimental limits of this process are unclear and lack a theoretical basis. We report the first comprehensive study of the super-resolution effect, integrating several new concepts. First, we present chromia as an advantageous masking material, characterizing its nanometer roughness, uniform structure, and amorphous state. Second, we develop an efficient method of in-line metrology of ion-beam focus by scanning electron microscopy, characterizing resolution and enabling reproducibility. Third, we mill complex nanostructures through chromia and into silica, characterizing the response of the bilayer system to a focused beam of gallium cations. Fourth, we derive a theoretical model that predicts lateral super-resolution across experimental studies and evaluates temporal efficiency. Our study elucidates the resolution-throughput tradespace of focused-ion-beam machining, demonstrating surprising trends and dramatic improvements of volume throughput that enable a paradigm shift from prototyping to manufacturing. Introduction Focused-ion-beam machining is a powerful method to fabricate complex nanostructures with critical dimensions in both the lateral and vertical directions. This method of nanoscale milling enables direct formation1 of electronic2-5, mechanical6,7, photonic8-11, and fluidic12-15 devices, among others. A narrow focus of an ion beam enables patterning of fine features, whereas a high current enables rapid milling of deep features across wide areas. Although the de Broglie wavelength of gallium cations in a conventional focused-ion-beam system is at the femtometer scale, aberrations intrinsic to electrostatic lenses and space-charge effects from Coulomb interactions broaden the focus of such an ion beam into an approximately Gaussian profile at the nanometer scale16. For dielectric substrates, exposure to an ion beam results in electrostatic charging and repulsion of ions from the surface, further complicating the process of focusing the ion beam and degrading lateral and vertical resolution. The lateral extent of the ion-beam profile generally follows a power-law dependence on ion-beam current, with effective lateral resolution requiring characterization17 for specific ion sources and substrate materials. Accordingly, reducing the lateral extent of the focused ion beam, simply by decreasing the current, generally improves lateral resolution and decreases the accumulation of surface charge. However, a lower current also increases the time to mill through the vertical range, prolonging any drift of the system and wear of the aperture that limits current, impairing lateral resolution18,19 and accruing operating cost. Depending on the materials and dimensions, a single device can take tens of hours to mill. This inherent coupling of lateral resolution and volume throughput yields a tradespace of spatial and temporal constraints. An explicit description of this tradespace is absent from the literature, although there is a general tendency to consider the focused ion beam as being more useful for prototyping than for manufacturing, with excursions into the latter domain often relying on pattern replication15,20. In contrast, previous studies have described a tradespace for lithographic processes, finding a relation of a power law of lateral resolution and areal throughput21,22 and extending this analysis into the commercial domain of manufacturing23. These studies explicitly excluded the focused ion beam from analysis for several reasons. First, direct machining conventionally involves a volume throughput rather than an areal throughput, without a separate process of pattern transfer. Second, focused beams of metal ions implant remnants of the machine tool in the workpiece, requiring additional study of the milling process. Third, conventional focused-ion-beam machining is slow and costly, being useful for research but limiting commercial viability to editing devices of only the highest value. Constraints on lateral resolution have motivated the use of sacrificial films11,13,24-27 to dissipate charge from insulating substrates28-32, reduce redeposition and damage along the edges of features13,25, and to super-resolve external edges of patterns down to the scale of one to ten nanometers13. In this approach, a sacrificial film functions as a physical barrier that masks the workpiece from the diffuse periphery, or tail, of the focused ion beam, effectively reducing the radius of the ion beam near internal boundaries of the mask and yielding edge profiles that differ in shape from those resulting from direct milling. Despite its routine use, current understanding of this spatial masking technique is incomplete. Milling rates of polymeric masks25,26 exceed those of common substrates such as silica33,34, resulting in soft masks with low values of physical selectivity, a fundamental property of the mask–substrate bilayer. Yet, metallic masks11,13,24,27, such as aluminum, platinum, and chromium, have lower milling rates but tend to be polycrystalline, with grain sizes ranging from tens to hundreds of nanometers. Additionally, milling rates depend on grain orientation35,36, transferring surface and line-edge roughness into the substrate27 and degrading lateral and vertical resolution. These effects also limit the accuracy of models of ion transport to understand the bilayer response. 1 Although reductions of electrostatic charging and edge defects are obvious advantages of a sacrificial mask, it is nonobvious that a sacrificial mask presents any fundamental advantage to super-resolve nanostructure edges, in comparison to simply reducing ion-beam current to improve lateral resolution. To answer this open question, we analyze the resolution–throughput tradespace of focused-ion-beam machining, discovering that a sacrificial mask enables patterning to occur with an effective resolution of a low value of ion-beam current but with a volume throughput that is several orders of magnitude higher. In this way, the dominant advantage of the super-resolution effect occurs in the temporal domain, rather than in the spatial domain. To substantiate this surprising finding, we perform the first systematic study of this topic, integrating four new concepts for the most widely available type of electron–ion beam system (Fig. 1). First, we introduce a chromia, Cr2O3, film for electron microscopy and sacrificial masking of silica, characterizing its advantageous properties (Fig. 1a). Second, we demonstrate a new method for in-line metrology of effective lateral resolution, enabling new efficiency and reproducibility (Fig. 1b). Third, we pattern complex nanostructures through chromia and into silica, measuring and simulating responses of the bilayer to ion exposure (Fig. 1c). Fourth, we develop a model of super-resolution, which we define as a multiplicative factor that quantifies the extent to which an unconventional resolution surpasses a conventional resolution limit, achieving good agreement with experimental data and elucidating the temporal efficiency of the process (Fig. 1d). Our study yields new capabilities of super- resolution and ultrahigh-throughput, which we define to be an unconventional volume throughput that can surpass conventional volume throughput by orders of magnitude, demonstrating a temporal advantage that is so decisive as to enable a paradigm shift of focused-ion-beam machining from prototyping to manufacturing. Figure 1. Overview schematic and representative data. (a) Scanning electron microscopy (SEM), transmission electron microscopy (TEM), and X-ray diffraction characterize the structure and solid state of a sacrificial mask of chromia on silica. (b) Scanning electron microscopy enables in-line resolution metrology through imaging with secondary electrons (SE) for reproducible and optimal focus of a beam of gallium cations. (c) The chromia masks the diffuse periphery of the ion-beam profile during milling of complex test-structures. Atomic force microscopy (AFM) elucidates milling responses and quantifies vertical resolution and lateral super-resolution. (d) Elucidation of the resolution–throughput tradespace of focused-ion-beam machining demonstrates both spatial and temporal advantages of masking the tail of the ion beam with a sacrificial film. Results and discussion Sacrificial mask The semiconducting behavior37-39, nanometer roughness40,41, gigapascal hardness41-43, and chemical selectivity of chromia against silica make this material a good candidate for our application. We form a silica film by thermal oxidation of a silicon substrate, over which we form a chromia mask by sputter deposition44. To comprehensively characterize our bilayer and provide input quantities for theoretical models, we combine atomic force microscopy, scanning electron microscopy, transmission electron microscopy and X-ray diffraction. These measurements show that the mask is generally smooth, uniform, and amorphous. Surface structure The silica surface has a subnanometer root-mean-square roughness and sparse asperities with a height of 1.6 nm ± 0.2 nm (Fig. S1). We report all uncertainties as 95 % coverage intervals, or we note otherwise. Atomic force micrographs provide estimates
Details
-
File Typepdf
-
Upload Time-
-
Content LanguagesEnglish
-
Upload UserAnonymous/Not logged-in
-
File Pages42 Page
-
File Size-