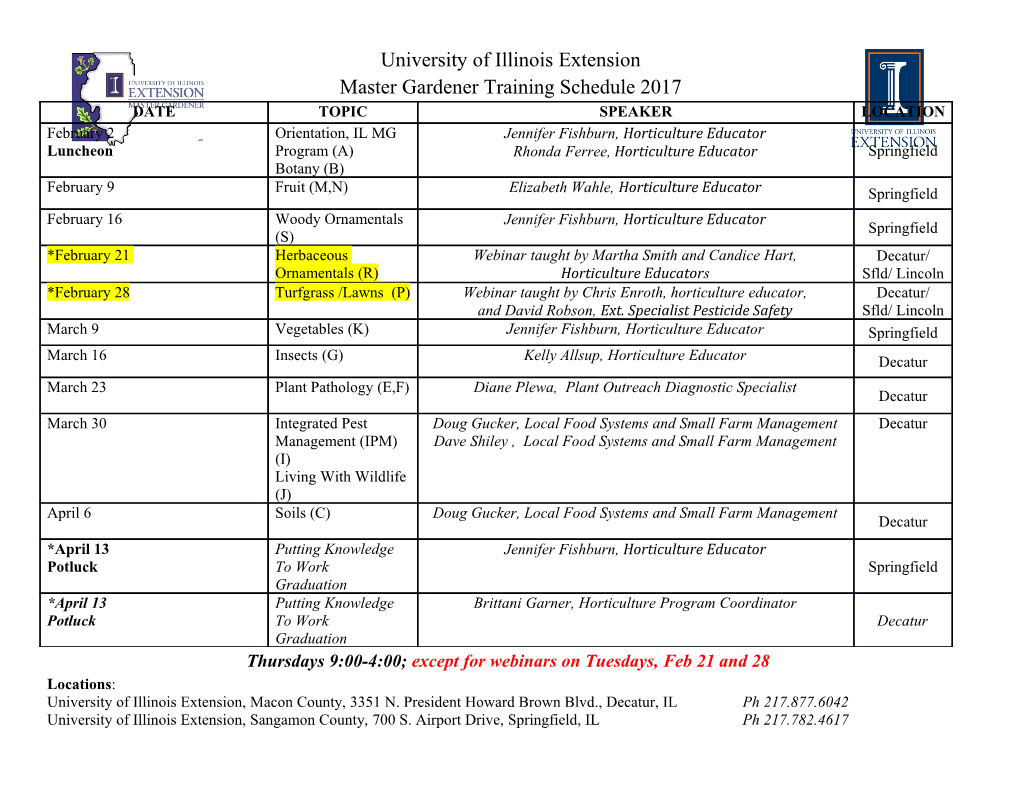
The Use of Physical Models and Demonstrations in Engineering Education Created By: David Flaherty CU Boulder 2017 THIS PAGE INTENTIONALLY LEFT BLANK Table of Contents I. Construction…………………………………………………………………………………………. 1 a. Crane Rigging Angles…………………………………………………………………... 2 b. Excavation and Earthwork Pressure……………………………………………...6 II. Dynamics ……………………………………………………………………………………………...9 a. Collision and Deformation: When Worlds Collide………………………… 10 b. General Planar Motion: Armor Attack…………………………………………..12 c. General Planar Motion: The Helicopter……………………………………….. 14 d. General Planar Motion: The Oil Rig.…………………………………………….. 15 e. General Planar Motion: The Slider.………………………………………………. 17 f. General Planar Motion: The Tank.…………………………………………………19 g. Projectile Motion.………………………………………………………………………… 21 h. Rectilinear Motion.……………………………………………………………………….23 i. Relative Motion: Choo Choo Train.………………………………………………. 25 j. Rotation: No Slip Wheel.……………………………………………………………… 27 k. Rotation and Moment of Inertia: A Day at the Races.………………….. 29 l. Rotational Kinematics: The Ferris Wheel.……………………………………..31 III. Fluids …………………………….…………………………………………………………………….. 33 a. Fluid Properties.…………………………………………………………………………… 34 b. Head Loss.……………………………………………………………………………………. 36 c. Hydrostatics.…………………………………..…………………………………………….38 d. Internal Flow and Losses.……………….……………………………………………. 40 e. Laminar and Turbulent Flow: Smoke Tunnel.……….………………………. 42 f. Shear Stress: The Fish Tank.…………………………………………………………. 44 IV. Heat Transfer ……………………………………………………………………………………….. 47 a. Conservation of Energy: Ice Melting Blocks.………..………………………. 48 b. Radiant Energy: Parabolic Concentrator.……………………………………….51 V. Material Science…………………………………………………………………………………… 55 a. Deformation: Bending a Knife Blade.…………………………………………….56 b. Deformation: Shape Memory Alloys.…………………………………………….58 c. Primary and Secondary Creep: Creepy Plastic.………………………….…. 60 VI. Mechanics.…………………………………………………..………………………………………. 63 a. Axial Strain.……………………………………………………….………………………….64 b. Beam Bending: Foam Beam.……………………..………………………………….66 c. Design of Axial Members.……………………………………….…………………….68 d. Elastic vs. Plastic.…………………………………………………………………………. 72 e. Load Conditions: Rubber Shapes.………………………………………………… 74 f. Paper Stress Concentrations.………………………………….……………………. 80 g. Shear Demonstrator.……………………………………………………………………. 83 h. Stress/Strain: A Strainge Transformation.…………………………….……….87 i. Stress/Strain Transformation: The Big Book of Shear..…………….…….93 j. Thermal Expansion.…………………………………………………………..………….95 k. Thin Wall Pressure Vessels – Balloons.………………………………………….97 l. Thin Wall Pressure Vessels – Hot Dogs.………………………………..……….99 m. Thin Wall Pressure Vessels.……………………………………………………….…. 101 n. Torsion: Tower of Torque.………………………………………………………….…. 105 VII. Statics.………………………………………………………………………………….………………. 111 a. Concentrated Cable Loads: The Ski Gondola.….…………………………….112 b. Coulomb Friction: Fun with Friction.……………………………………………. 114 c. Force Vector: Amazing Weight Loss Program.……………………………….116 d. Frame Demos.……………………………………………………………………………... 118 e. Friction: Belt Friction.……………………………………………………………….…. 120 f. Loading: Distributed Student Loading.…………………………………………. 121 i g. Mechanical Advantage: Pulleys – Equilibrator Challenge.…….……. 122 h. Mechanical Advantage: The Torque Tester.……………..……………..…….125 i. Moments: Lug Wrench vs. Breaker Bar.…………………….…………………. 126 j. Moments: Moments and Couples.………………………………………………. 128 k. Moments: The Persuader.……………………………………………………………. 130 l. Moments: Varignon’s I-Beam.……………………………………………………….133 m. Truss Design: K’NEX Trusses.………………………..……………………………….134 n. Truss Design: Ruler Truss.…………………………….………………………………. 138 o. Truss Design: Wacky Fun Noodle.…………………..……………………………. 140 p. Truss Design: Wooden Truss 2D.……………………….…………………………. 143 q. Truss Design: Wooden Truss 3D.…………………………….……………………. 146 r. Uniformly Loaded Cables.……………………………………………………………. 150 s. Zero Force Members.……………………………………………………..……………. 153 VIII. Thermodynamics.……………………………………………………………………………..…. 157 a. 2nd Law – Direction.……………………………………………………………………...158 b. 2nd Law – Losses.…………………………………………………………………………..159 c. Boiling Point: The Hand Boiler.…………………………………………….………. 161 d. Boiling Properties.……………………………………………………………….………. 162 e. Closed vs. Open Systems.…………………………………………………….………. 164 f. Conservation of Mass: Molasses Madness.….……………………………….166 g. Density and Buoyancy: The Lava Lamp.………………………….……………. 168 h. Otto Cycle: Engine Knock.………………………………………………….………….170 i. Psychrometry.………………………………………………………………………………. 172 j. Total Energy – Fan Box.………………………………………………………..……….174 k. Total Energy.……………………………………………………………………………..…. 177 l. Vapor Power Cycle: The Little Engine That Could.…………..…………….178 i i CONSTRUCTION 1 CRANE RIGGING ANGLES CONSTRUCTION Keywords: Angle, Crane Pick, Force, Lift, Load, Vector Submitted by: David Flaherty and Matt Morris Model Description: This demonstration depicts the importance of rigging angles during crane lift operations on a construction site. Reducing rigging angles results in a significant amplification of forces in the rigging, potentially leading to failure. By varying the connection points and sling length, students will be able to calculate the predicted forces and analyze the best combination of connection points and sling lengths to successfully complete the critical lift. The demonstration should take 15-20 minutes. Crane Rigging Angle 휽 Engineering Principle: A sling’s working load limit (WLL) is based on a crane lift performed at a straight (90°) angle. The forces in rigging (sling, chain, wire rope, webbing, shackles, etc.) increase substantially as the angle formed by the sling leg and the horizontal becomes smaller. The following chart shows the increased force applied to the rigging when the rigging angle is reduced. The key engineering principle with this demonstration is related to an understanding of statics. Students must comprehend that decreasing the angle creates a horizontal force component that in turn increases the tension in the rigging. This can be derived using the figure below. Fload Angle (휽) Fsling % of Fload 1.0 90 deg 1.0 100% 1.0 60 deg 1.2 115% 1.0 45 deg 1.4 141% 1.0 30 deg 2.0 200% 1.0 20 deg 2.9 292% 1.0 10 deg 5.8 576% +↑ σ 퐹푦 = −푊1 + sin 휃 ∗ 퐹퐴퐶 = 0 , where FAC = Fsling and W1 = Fload 퐹 퐹 = 푙표푎푑 ; for reference, 퐹 = 1Τ 퐹 푠푙푖푛푔 sin 휃 푙표푎푑 2 푙푖푓푡 While increasing the connection angle of a two-point lift may be required to increase the stability of the lift, careful consideration must be taken in regards to the sling capacity and weight of the lift. 2 REQUIRED ITEMS Cost and Build Item Qty Description/Details Time 2x 2 ft 3/16 in Chain $8 at $2 per foot. These represent the sling for the lift. sections This is smaller than the straight chain and is used to Twist Link 1 foot $1.50 connect the weight plate to the spring link on the Chain lower screw eye. Most pieces come in 8 foot sections. Once cut to 2x6 x 3 feet 1 $6; 20 minutes size, this is the critical lift. These are used for the rigging connection points on 3/4 in x 3 in $5 at $1.25 per 2 7 top and the load connection point on the bottom. Screw Eyes pack 130-pound capacity. This locks and holds the two spring scales along 3/16 in quick each chain. It also is used for the top spring scale 1 $2.25 link to analyze the total weight of the lift. 450-pound capacity. These are used for quick connections of the chains 3 in spring link 3 $1 each to the screw eyes and the weight to the load screw eye. 150-pound capacity. 20-lb spring These scales measure the weight of the lift and 3 $11.50 each scale along each chain. 10-lb weight 1 $11 This increases the weight of the critical lift. plate APPLICATION Before Class: Build and verify your model. The imperfect connections at the screw eyes and the variation in the spring scale as a load is applied make predicting the exact angle difficult. The placement of the screw eyes and the length of the chain are intended to replicate scenarios with the connections at 30°, 45°, and 60°. After cutting the 2x6 to 3ft. length, install the screw eyes along the centerline at the distances shown above. To ensure the spring scale hook remains centered during the lift (and creates an equal force in both scales), use wire or duct tape to prevent its movement. Display the 2x6 at the front of the class, but do not have anything connected to it. Let the students build their answer as they work to solve the problem. 3 In Class: The scenario is as follows; the students are new project engineers on a job site. The project manager is out sick and leaves them in charge for the day. The easy day gets complicated when the crane operator insists on executing the project’s critical crane lift on short notice due to impending weather. However, due to the unscheduled nature of the request, the project engineer is unsure if the slings on hand are capable of safely executing the lift. The project engineer tells the crew that the crane lift will happen in 15 minutes, which buys some time. The project engineer runs back to the trailer to calculate how to use the two (2) 11-ton slings to lift the 15 to 16-ton object worth $2 million. The object has only three “picking eyes” on each side to maintain its balance. The crane operator recommended the connections farthest from the center to help with stability. Theory: Given the fixed connection options, have the students calculate the tensile forces in the sling using the farthest connection (12 inches from center). Ask them what angle they would recommend if they didn’t have time for 퐹 calculations, and why? By adjusting the basic
Details
-
File Typepdf
-
Upload Time-
-
Content LanguagesEnglish
-
Upload UserAnonymous/Not logged-in
-
File Pages183 Page
-
File Size-