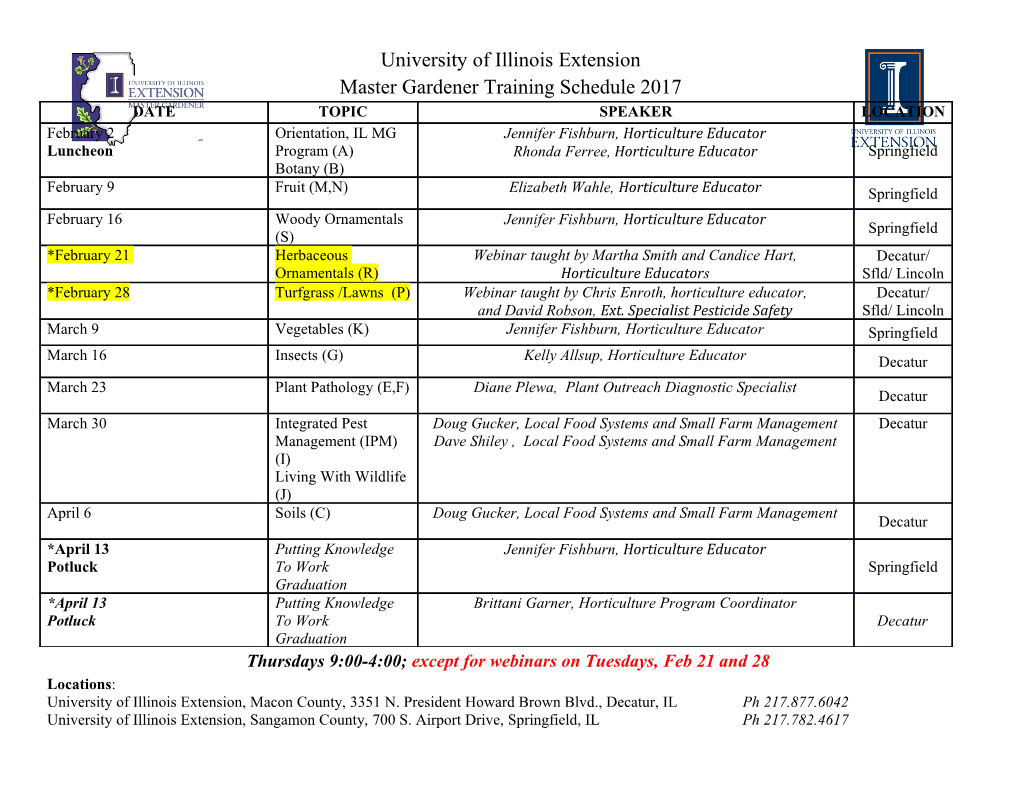
INVESTIGATION OF POWERTRAIN RIGID BODY MODES Basem Alzahabi Arnaldo Mazzei Logesh Kumar Natarajan Associate Professor Assistant Professor Graduate Research Assistant Dept. Mechanical Engineering Dept. Mechanical Engineering Dept. Mechanical Engineering Kettering University Kettering University Kettering University 1700 West Third Avenue 1700 West Third Avenue 1700 West Third Avenue Flint, Michigan, 48504, USA Flint, Michigan, 48504, USA Flint, Michigan, 48504, USA Abstract Nomenclature Powertrain mounting systems serve a number of functions J mass moment of inertia of powertrain with respect for the overall vehicle. First and foremost, the mounting xx to X-axis of powertain inertia co-ordinate system. system maintains the position of the powertrain in the vehicle as it is subjected to inertia and torque reaction loads. In J yy mass moment of inertia of powertrain with respect addition, the mounting system controls the overall motion of to Y-axis of powertain inertia co-ordinate system. the powertrain, preventing the engine, transmission, and mass moment of inertia of powertrain with respect accessories from contacting other components of the J zz vehicle, thereby avoiding damage to any vehicle systems to Z-axis of powertain inertia co-ordinate system. from the potential impact. Introduction The mounting system also plays a role in vehicle ride and handling due to the significant mass of the powertrain that Powertrain mounting systems are required to maintain the can be approximately 15 to 20% of the total mass of a large position of the vehicle’s powertrain with respect to its body car. Finally, the mounting system isolates the rest of the and components as the vehicle is subject to several loads. vehicle and its occupants from the powertrain as a vibration These loads (to name a few) are due to road input, vehicle source. Therefore, investigating the powertrain rigid body acceleration, braking and cornering. Within tolerances, the modes for a particular mounting system is very critical in position of the powertrain is controlled by its mounting determining initial mount locations and spring rates for a new system, so the powertrain does not interfere with the powertrain or vehicle architecture. vehicle’s structure. Also, the mounting system is responsible for isolating engine vibration from the vehicle and from its This paper investigates the design of a powertrain mounting passengers. The amount of isolation and NVH performance system of a front wheel drive vehicle with a transversely of the mounting system will depend on the vehicle design mounted V8 engine and transaxle mounted on an isolated constraints. For instance, if the engine compartment does front sub-frame. A torque strut is attached to the top of the not allow for enough room for powertrain motion, vibration engine and to the body structure with elastomeric bushings isolation may not be best due to high stiffnesses required for with torque reaction as its primary function. The locations of the mounts in order to prevent contact between engine and the powertrain mounts and torque strut cannot be modified vehicle’s body. Therefore the design of powertrain mounting significantly because this would require changes to the front systems is governed by specific vehicle requirements. sub-frame and other components. Engine mounting for a heavy duty vehicle has been studied A finite element model and an optimization scheme are by Iwahara and Sakai [1]. The best mounting layout to discussed for the response of this passenger vehicle produce vibration isolation and to support engine dynamic powertrain / powertrain mounting system. The vibration of torque was investigated by using an eigen-analysis and FEM the standard powertrain configuration is analyzed through its simulation. The rigid body modes, frequency response and rigid body mode shapes and an optimization scheme is transient response were obtained and several mounting suggested. The scheme aims to improve the performance of layouts were discussed. It was found that it is possible to the mounting system in order to produce better powertrain attain a mounting layout that will give best performance for overall NVH performance. idling engine vibration and shock due to engine torque. In reference [2], Li-Rong et al. presented a finite element model of a lumped parameter model for a hydraulic damped ® engine mount. The FEM model can be used in ADAMS PART X (MM) Y (MM) Z (MM) simulations to determine mounting effect on vehicle ride. Front mount 1238.6 67.0 487.2 Rear mount 1829.8 282.2 416.4 Sakai et al. discussed mounting system optimization for Transmission mount 1614.7 -442.6 412.6 vibration isolation and interference avoidance in reference TS bushing – engine 1360.1 499.4 942.7 [3]. An optimization method was presented which allowed for the inclusion of engine packaging as part of the design TS bushing – body 1620.2 499.4 892.2 objectives. This inclusion aimed to reduce the issue of increased stiffness at certain vehicle travel conditions. (Good Table 3 – Baseline powertrain mount locations vibration isolation at low engine amplitudes and poor isolation at high engine loads.) PART X (N/mm) Y N/(mm) Z (N/mm) In the present work, a powertrain mounting system for a large passenger automobile is investigated and an Front mount 205 365 469 optimization scheme for better performance is derived. Rear mount 112 456 456 Transmission mount 160 320 480 Powertrain and Powertrain Mount Specification TS bushing – engine 80 16 80 TS bushing – body 250 250 25 The rigid body mode shapes for the powertrain are obtained through an FEM simulation approach [4]. The resulting frequencies and modes shapes can then be analyzed and Table 4 – Baseline powertrain mount stiffnesses changes can be applied to the stiffnesses of the mounts, as well as their locations, in order to obtain better performance. The vehicle utilized for this study is a front wheel drive with a Figure 1 shows a sketch of the sub-frame and powertrain transversely mounted V8 engine. The engine is mounted on mounting system. an isolated sub-frame that is attached to the vehicle’s body via six elastomeric bushings. The engine is attached to the front sub-frame via three mounts. A torque strut is attached to the engine and to the body of the vehicle also through elastomeric bushings. Table 1 summarizes the powertrain mass and inertia properties in the powertrain inertia coordinate system (Table 2). CENTER OF MASS (MM) X=1544.9; Y=22.2; Z=603.4 Mass (Kg) 360 2 7 J xx (Kg mm ) 1.74 x 10 2 7 J yy (Kg mm ) 2.48 x 10 2 7 J zz (Kg mm ) 3.10 x 10 Table 1 – Powertrain properties Figure 1 – Sub-frame and powertrain system Mounting System FEM Model POWERTRAIN INERTIA CO-ORDINATE SYSTEM (MM) The powertrain with its mounting system is modeled using Origin X=1544.9; Y=22.2; Z=603.4 MSC NASTRAN finite elements software package. In the X-Axis X=1544.514; Y=23.045; Z=603.751 finite element model, the powertrain mass and inertia Z-Axis X=1544.612; Y=22.398; Z=602.498 properties are included via a concentrated mass element ‘CONM2’ at the grid point for the center of mass co-ordinate. Table 2 – Powertrain location The mounts are modeled using scalar spring elements ‘CELAS2”, and the mounts are connected to the grid point of the center of mass using rigid elements ‘ RBAR’ or ‘RBE’. A Table 3 gives the locations for the powertrain mounts and schematic representation for the FEM of the overall Table 4 shows the mount stiffnesses of the baseline design. powertrain system is shown in Figure 2. Design Objectives The modal characteristics of the powertrain system show the six rigid body modes and their corresponding natural frequencies [6]. Identifying these rigid body modes of the powertrain is one of the main factors in determining powertrain suspension design. Automotive powertrain suspension design is a compromise between isolation of powertrain rigid body modes from vehicle rigid body mode targets and packaging constraints. So, it is very important to decouple the rigid body modes and design the mounting system for frequencies that could prevent amplification. Amplification is caused when a powertrain vibration frequency matches a vibration frequency of some other vehicle assembly. The main design criteria for optimizing the mounting system are [7]: • Decoupled vertical mode with a frequency between 8 to 9 Hz together with at least 90% of the kinetic energy in the vertical direction. These requirements keep the vertical mode below the suspension wheel hop frequency and avoid amplification. • Decoupled pitch mode frequency between 10.5 to 11.5 Hz with 80% of the kinetic energy in the pitch direction. Figure 2 – Powertrain FEM (top view) This requirement is mainly to avoid pitch-fore/aft coupling and to prevent the frequency range from falling between the cold and warm idle engine speeds, so that Analysis of Baseline Design vibration from any first order engine imbalance is not amplified. The modal characteristics of the powertrain system of the • The remaining rigid body modes, i.e. fore-aft, lateral, baseline design were obtained using MSC NASTRAN. The roll, and yaw should have around 75% kinetic energy in natural frequencies of the rigid body modes are listed in their primary direction. Table 5 and the distribution of the modal kinetic energy [5] is shown in Table 6. • Roll and yaw frequency should lie between 7 to 15 Hz. This requirement is to ensure that the lower end of the range is above human sensitivity, while the high end of FREQUENCY (HZ) PREDOMINANT MODE TYPE the range is below any body structure flexible body 5.21 Fore / Aft mode. 7.37 Lateral 9.63 Vertical Design Optimization 10.12 Yaw 11.40 Pitch The baseline design does not satisfy all design objectives for 14.60 Roll the powertrain rigid body mode requirements in terms of frequencies and decoupling.
Details
-
File Typepdf
-
Upload Time-
-
Content LanguagesEnglish
-
Upload UserAnonymous/Not logged-in
-
File Pages5 Page
-
File Size-