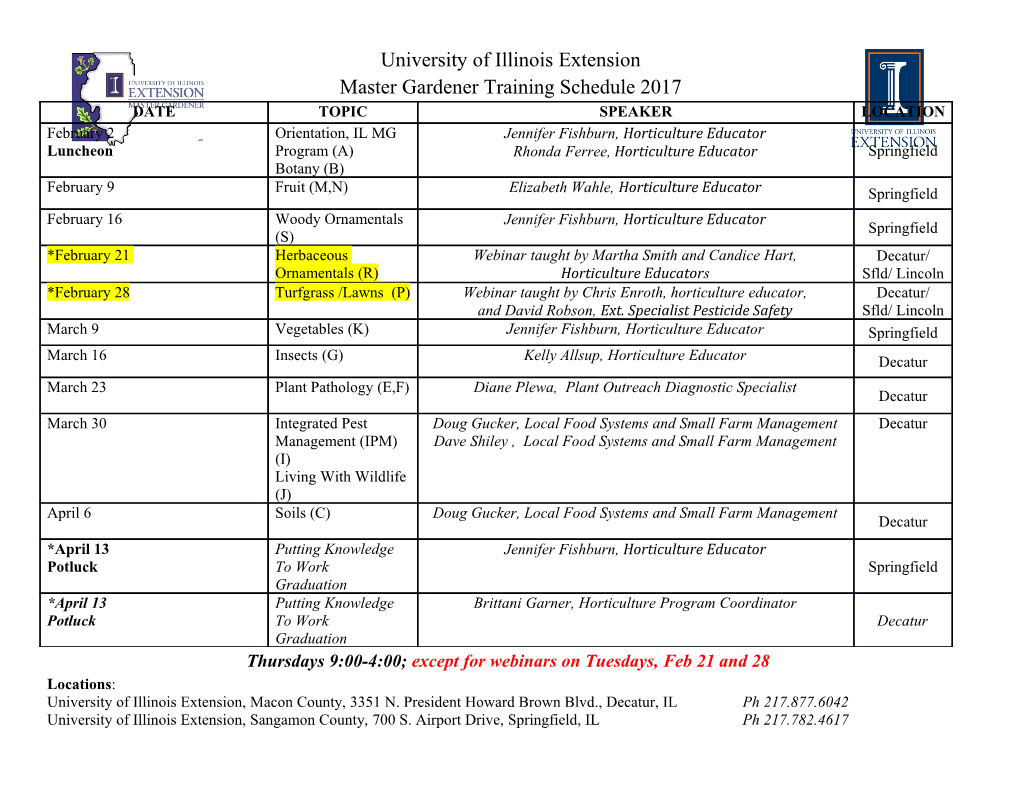
FeInISe himg 0·.f G·-·ears b.yA- __usornungf · Maurice F.. Amateau, Pennsylvania State University and Raymond A. Cellitti,. R.C. Associates GROUND & REFRIG. ( -320 F ) I 0 GROUND AND NOT FEFR IG ( -3201 F l Fig. I-Pitt:ing fatigue of 9310 steel carburized to 0.90% carbon, Abstrad: to minimize noise, vibration and fatigue loading. As these A low temperature thennomechanical finishing process now under requirements become more stringent, the cost of processing development has the potential for producing longer gear life and can increase significan.tiy. The combination o.f mechanical stronger, more reliable and lower cost gears. This process ausforms properties and dimensional control is normally accomplished the carburized surface of gear teeth while in the metastable austenitic by separate manufacturing steps, each of which may partially condition during a gear rolling operation. A high degree of gear nullify one or more of the desirable characteristics induced accuracy is possible by the combined use of interactive forming, in the prior operation. For example, highly loaded precision low temperature processing and precision gear rolling dies. Ther- gears are general1y earburizad to minimize plastic deforma- momechanicalprocessing can eliminate the need for hard gear tion and wear. They are then ground to.achieve the necessary grinding, thus offering substantial reductions in. finishing costs as dimensional control, remove high well as improvements in pitting fatigue life. temperafure transforma- tion products and improve surface finish. The optimum mechanical properties are developed in the as-earburized con- Introduction dition; thus, the finish grinding operation, which is required Almost all machines or mechanical systems contain preci- for achieving dimensional. requirements, precludes achieving sion contact elements such as bearings, earns, gears, shafts, maximum strength and reliability. This point is illustrated by splines and rollers. These components have two important examining the pitting fatigue behavior of carburized 9310 steel common requirements: first. they must possess sufficient subjected to various surface treatments.(1) (See Fig. 1.) The mechanical properties, such as, high hardness, fatigue strength unground.as-carburized finish results in the best fatigue per- and wear resistance to maximize their performance and life; formance compared to the as-ground surfaces, Maximum second, they must be finished to dose dimensional tolerances dimensional stability and resistance to plastic defo.rmation 32 Gear Technology areachieved when. the microstructure of the steel is totally In addition to. ausfonnirtg, other low temperature ther- martensitic, Diffusional transformation products, such as fer- momechanical treatments for precision finishing are p-ssi- rite, lead to low hardness, as does untransformed austenite. ble. low temperature deformation during the decomposition The untransformed or "retained" austenite Isalso detrimen- of metastable austenite to bainite, known as .isoforming, will tal 'to dimensional stability, as it can eventually transform result in significantly different toughness and strength under mechanical stress to martensite. resulting in a volume characteristies than ausfcrmiag, Numerous other low change. Cryogenic treatments after normal quenching are temperature treatments are also possible. providing a large often used to control the amount of retained austenite. as seen. range of processing options and resulting effects. in Fig. 1. Such treatments can also have a.detrimental effect on fati-gue life. Cu:rre.nl Status of Ithe Technology Improvements in performance, reliahility and manufactur- The strengtheningeffect of ausfermingisanributed to the ing costs could be realized i.Esurface finishing and strength- inheritance of-much of the dislocation structure and carbide ening were accomplished in a single process. Certain low temperature thermo mechanical treatments. such as aus- forming. have this potential. AusEorming treatment is applied to the steel whil.e it is in the metastable austenitic condition tlN>'[NTItx..At fiNISHING prior to quenching to martensite. The principal benefit of this treatment is that i't can produce significant improvements in strength without degrading teughnessand ductility. In some steels, toughness is adually improved simultaneously with strength. The low temperature nature of this treatment pro- duces very Iiule thermal distortion. thus making it ideally suited for precision finishing operations, The ausformlng pro- cess can he directly substituted for groups of ccnventional finishing processes, saving considerable cost while optimiz- ing mechanical performance. Fig. 2 compares the processing steps for finishing gears by conventional methods with those required for ausfonning. Ausform finishing can eliminate grinding. shaving, shot peening. honing and cryogenic treat- ments. The import.ance of eliminating grinding for optimized Fig. 2: - Comparison of manufacturing steps - conventional versus ausfonn- rolling conta t fatigue l:ife is illustrated in Fig. 3. Removal. ing fLnishJng of precision gears. by grinding of more than 1 mil of surface material from 8620 steel carburized 'to. 1.2e can. severely reduce fatigue strength. This phenomenon can originate from two sources. First. the 40 fatjgue resistant compressive layers of carburized material are 1. 2 "loC, REHfAf removed, and, second, incipient grinding damage in the form of micrecracksand transformation products is generated. 20 • AlffHORS: DR. MAURICE F. AMATEAU.is Head of tIle Engineering Materials Dept .. Applied Research Lab. tmd Prof. of Engineering Science & 10 - Mechtmics, Pennsyl'vtmw State University. Prior to his work at Perin State. Dr. Amateau held research positions at Batt.elle Memon'alln- stiMe «rid TRW ll1c .• 1711(:1· was Director of Materials fngineeriPlg ,at 1»temmio,utl Harvester Co. He lIas sertied on various committees of 5 the National Research Coundllmd is cummtly an advisor to the Com- miltee· on Recommendations for U. S. Army Basic Scientific Research. He is the author of numerous technical papers on fatigue, fracture. wear and tribjology of .structural materials and composites. He holds " masters degree from Ohio State University and a Ph.D. in metallurgy from Case Western Rese.roe University. RAYMOND A. CELlrrn is president of R. C. Associates, a11 engineering and' manufacturins cOrlSulting firm. He has 34 yearsu.- perienawitll Intmrati01U1JHlH'Vester Co. in applied mechanics. fatiguJ! , testing. process control. metalworking and materials. engineering. He --- is the author of numerous technical papers and co-author of o 0.5 1 1.S 3 5 10 '~Bihliography on Residual Stresses," SAf Fatigue Design Handbook. He was awarded the patent Or! the ausTolling process that fO",115the DEPTH BElOW SURFACE, MilS basis for tllis article He holds a masters degree in physics from Loyola University. Chicago. and one in'metallurgialJ engineerir:Jgfrom Illinois Fig. 3-Fatigue life as a function of the amount of rnaterial removed. 8620 1l15titute of Technology. teel carburized 10 1.2%C and reheat treated from 15S06F. All test5 al347 ksi. NovemberjDeoem'ber l,987 33 DID IG «l'025-Q'05Imm AUSTENHE zlllll- • C~RB IOE 1100 iam I1«11 ~ ' (0'06-11· 2lmm >- 1100 1600 1500 0 2S 75 100 l I I I SECrtiDS M!NU!J[ IIJUI D~¥ 1110£ n:oc SCAlEI DEAJlMAnON BY ROlliNG IfoI Fig. 6 - Schematic illustration depicting ausrolling time-temperatur regime FIg. 4 - Effect of amoWit of deformation al S10~C on the yield ~trength of quench from austenitizing temperature, a O.32C-3.0Cr-l.SNi-1Si -a,SMa steel, A range of martensite plate sizes (in brackets) was investigated at each deformation .IS) associated witha.change in carbide composition. (6) The change in hardness and carbide form over the range between o to 60% de.fonnationisseen in Fig. 5. The two principal requirements fora. steel to respond ef- fectively to the .ausforming treatment are the presence of some carbide forming elements and the persistence ofthe austenite in the metastable form -that is, the existence of a deep austenite bay region in the isothermal time-temperature-trans- formation (T-T -T) curve - fora sufficient period of time to permit the required amount of deformation. Fig. 6 is the 150 T-T-T curve for a 1.0C-1.2Cr-3.ZSNi-O.13Mo steel (carbur- ~ III ized 9310) exhibiting such 3. bay region. This steel has been III I successfully surfaceausfcrmed. Numerous highly alloyed I steels are potentially ausformable; however, for low alloy steels, alloy modification or careful selection may be required. cr 1C3 m- Some existing through-hardened steels that may prove to be satisfactory are 51870, 4370 and 1580. There are also, several 750 -- - low-alloy steels specifically developed for ausforming, one 0 10 Cl 60 of which is the Si-Mn-Mo- V-Cu steel developed at RARDE over ten years ago. ('7) Fig. 5 - Carbide and hardness chang by allSforming.'I>' At the present time, it is not dear that thennomechanical Forming near the martensite start 'temperature (Ms) is distribution generated in the metastable austenite during detrimental to the final properties. For conventional ausfor- deformation to the final, martensite after quenching~2J A fine ming, working dose to the M, is not common practice since dispersion of carbides occurs during the working of austenite, deformation can raise the effectiv,e martensitetransformation stabilizing not only the grain size, but 'the subgrain size as temperature and promote the transformation reaction. In this well. (3) Ausfonning
Details
-
File Typepdf
-
Upload Time-
-
Content LanguagesEnglish
-
Upload UserAnonymous/Not logged-in
-
File Pages6 Page
-
File Size-