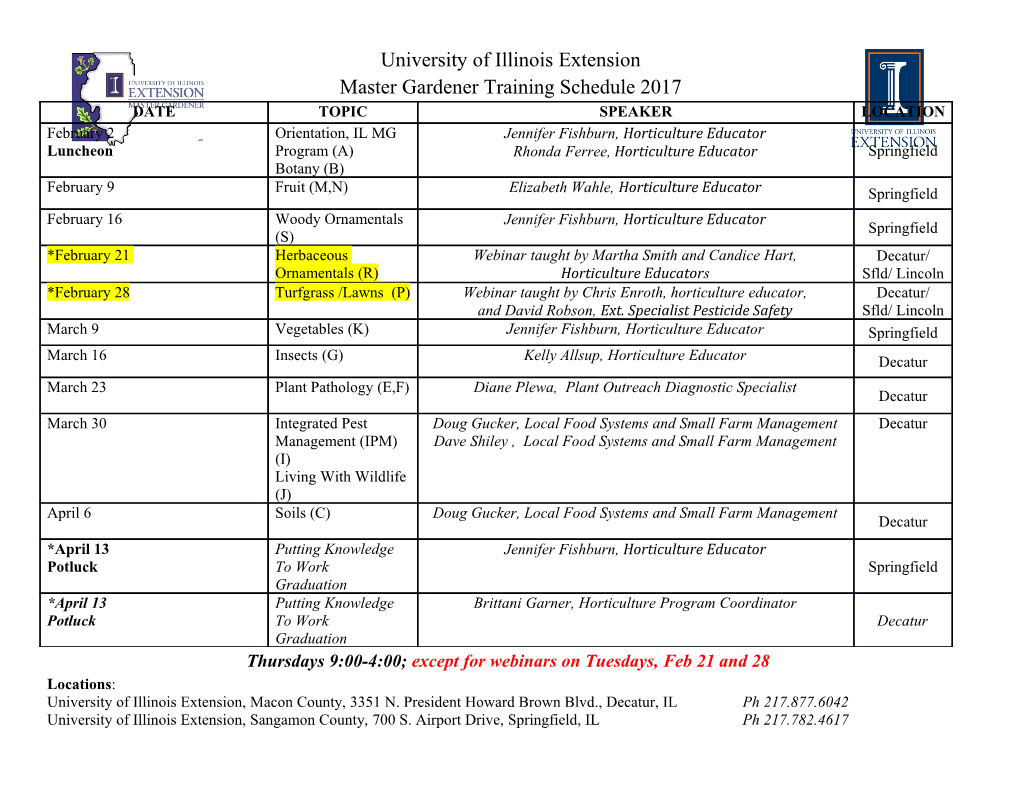
008-0518 Theory of Constraints contributions to outbound logistics Fernando Bernardi de Souza São Paulo State University (UNESP) Av. Eng. Luiz Edmundo C. Coube 14-01 Bauru, SP, 17033-360 - Brazil [email protected] Tel: 55 (14) 3103-6122 Sivio R. I. Pires Methodist University of Piracicaba (UNIMEP) Rodovia do Açúcar, Km 156 Piracicaba, SP, 13400-911 - Brazil [email protected] Tel.: 55 (14) 3124-1515 POMS 19th Annual Conference La Jolla, California, U.S.A. May 9 to May 12, 2008 Abstract This article aims to present the main contributions of the Theory of Constraints (TOC) to outbound (distribution) logistics. It presents the thesis defended by TOC, according to which the current ways of managing outbound logistics, based mainly on sales forecasts, batching policies, and indicators that do not privilege the supply chain performance as a whole, lead to difficulties in handling the trade-off between logistics (stock and transportation) costs and stock-outs levels. This conventional logistics management is labeled by TOC as pushed distribution, in contrast with its defended approach called pulled distribution. Considering the few scientific texts existing on the subject, this article claims to present, based on a theoretical research, the technical aspects of the approach suggested by TOC and discuss the assumptions it is based on, in an attempt to contribute to the expansion of outbound logistics knowledge and widen the analysis of supply chain management. Key words: Outbound logistics; distribution; pull system; Theory of Constraints. 1. Introduction Since its inception about two decades ago, the Theory of Constraints (TOC) has developed quickly and stood its ground as an important model for business management (WATSON et al, 2007). In this sense many management issues have been studied, structured and presented under TOC perspective. Some good examples are the approaches for performance indicators based on the Throughput Accounting (CORBETT, 1998; NOREEN et al., 1994), the study of Drum-Buffer-Rope and Buffer method Management for Production Planning and Control (GOLDRATT, 2004; UMBLE & SRIKANTH 1990; STEIN, 1997), the proposal of the Critical Chain as an alternative for project management practice (GOLDRATT, 1997; CERVENY & GALUP, 2002), and even use of Thinking Process for problem identification, solution and implementation development (GOLDRATT, 1994; DETTMER, 1997). However, there are areas appertaining to operation management in which TOC precepts have been little explored, as in outbound logistics, within the emerging area of Supply Chain Management (SCM). Given the very small number of bibliographical sources on the theme, this study intends mainly to be a conceptual revision, structuring a text gathering the main concepts and information on the contributions brought by TOC on this subject. Given its range, this article is interested especially in some logistic aspects of SCM. As the concepts Logistics and SCM are sometimes mixed up, we should have in mind the work of COOPER et al (1997), who had already reported that executives of leader corporations in their segment, who were implementing the state of art in SCM, understood the wider range of SCM, compared to Logistics processes and functions. The same authors point out that the Council of Logistics Management of the USA had changed their definition of Logistics, classifying it as a subset of SCM, seeing the two concepts not as synonyms, and defining Logistics as “that part of supply chain processes that plans, implements and controls the efficient flow and storage of goods, services and related information between the point of origin and the point of consumption in order to meet customers' requirements. Based on a theoretical research, this article proposes a conceptual rehearsal aiming to identify the main contributions that TOC can bring for distribution management practice in SCM perspective, for the redefinition of the ways of planning and distributing stocks as well as conceiving, evaluating and controlling some of the transactions within the Supply Chain (SC). For such, this text has the following organization: Next topic briefly presents some of TOC basic principles, important for the better understanding of this article. The third topic introduces some views defended by TOC, which challenge some typical presuppositions of distribution management practice and of SCM. In its fourth topic, this article relates some additional points of the TOC methodology. The principal actions proposed by TOC regarding distribution logistics are discussed in the fifth topic of this article. In the sixth topic, final considerations are delineated. 2. Theory of Constraints The TOC approach initially recognizes that every organization must be understood as a system, that is, a set of elements among which there is an interdependence relation. Next step emphasizes the widespread accepted notion that every system has a purpose or goal, and so, every action taken by any part of the system must be judged by its impact on the whole system. For this reason, it is imperative to define measures that allow the evaluation of the impact of any subsystem, and any local action in this subsystem (GOLDRATT, 1990a). If companies are formed by interrelated elements with a common goal, the system constraint must be defined as anything that significantly prevents a system from achieving a better performance considering that goal. Moreover, every system has to present at least one constraint. Otherwise, the system performance would have to be infinite. Likewise, there will always be very few constraints, as there is always a single weaker link in a chain (GOLDRATT, 199b). The constraint may be physical, such as a machine with limited capacity, or lack of raw material, but more often it is either a policy or behavior constraint. Policy constraints often arise when the company environment changes, while the company policies remain unchanged. Most significantly, policy constraints are usually within the control of the organization management. Behavioral constraints occur when performance measures or policies, even after been changed, lead into behaviors that are ingrained and constrain a system’s performance. TOC contains a range of tools and techniques for addressing physical, policy and behavioral constraints (MABIN & BALDERSTONE, 2003). Based on this, TOC provides 5 focusing steps that must be followed in order to assure an effective ongoing improvement (GOLDRATT, 1990a): a) Identify the system constraint (s); b) Decide how to explore the system constraint (s), that is, increase the system throughput, completely eliminating any kind of waste in the system constraint; c) Subordinate everything else to that decision, which implies in ensuring that all other system elements work towards exploring the constraint, and should be evaluated in function of how well they are accomplishing that objective; d) Elevate the system constraint(s), that is, increase the system throughput by means of increasing the investment volume towards the constraint, for example, investing in new market segments to elevate a market constraint; e) If in a previous step a constraint was broken, return to the first step, but prevent inertia from becoming the system’s constraint. Goldratt (2004) affirms that the target of a capitalist enterprise is to make money in the present as well as in the future. It must be evaluated in terms of its Net Profits (NP) and Return On Investment (ROI). In order to judge the impact a local action has on the NP and the ROI, TOC uses three performance measures: - Throughput (T): rate at which the system generates money by means of sales; - Investment (I): all the money captured by the system; - Operating Expense (OE): all the money that the system spends transforming investment into throughput. Goldratt (1990a) comments that Throughput can be understood as all the money entering the company minus the amount paid to suppliers. That would be the money the company generated. The amount paid to the suppliers is the money generated by other companies. According to Corbett (1998), the throughput has two sides: the Revenue and the Total Variable Costs (TVC). The use of the terms cost and variable may lead to a confusion regarding cost accounting measurements. TVC is the cost that varies for every extra unit produced (in most cases its only raw material). This will tell us how much money the company generates with the sale of one unit of the product. All other costs are included in the OE category. Schragenheim and Dettmer (2001a) reinforce that the definition of throughput does not include the direct (or even indirect) labor costs, unless they are returned by piece. According to Goldratt (1991), the relation between the three financial measurements (T, I and OE), the NP and the ROI becomes immediate. NP is T minus OE, while ROI is T minus OE, divided by I. An important aspect of TOC regards its orientation towards improvement efforts. For TOC, it is more sensible to focus improvement efforts on increasing Throughput than reducing Operating Expense. The reason being that there is no theoretical limitation for Throughput increases - and even practical limits are in the vast majority of times very far from the actual Throughput. Efforts towards Operating Expense reduction would have a theoretical zero limit, while the practical limit would be well above that, limiting a true process of continuous improvement (GOLDRATT, 1990a). Throughput orientation is an organization-wide focus on increasing throughput,
Details
-
File Typepdf
-
Upload Time-
-
Content LanguagesEnglish
-
Upload UserAnonymous/Not logged-in
-
File Pages40 Page
-
File Size-