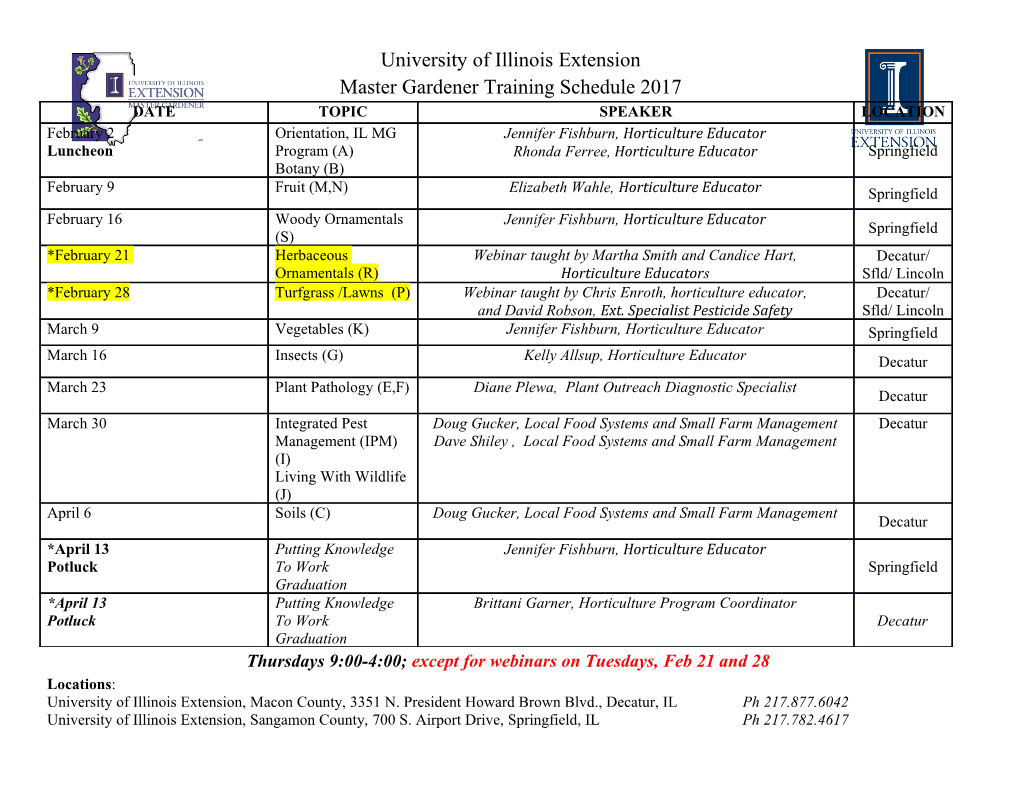
Wang, Bulbul & McCoy 2015 A Comparative Case Study for Using COBie in Project Turnover A Comparative Case Study for Using COBie in Project Turnover Zhulin Wang, [email protected] Virginia Tech, United States Tanyel Bulbul, [email protected] Virginia Tech, United States Andrew McCoy, [email protected] Virginia Tech, United States Abstract The planning, design, construction, and commissioning processes of buildings are rich with project information created in various formats and stored in different locations. Such information contains specific project details helpful for understanding, operating and maintaining a facility properly. Yet not all information created during the production stages are in a usable format or even accessible to the owner. Currently, new information needs to be generated and recorded by an owner to track a facility’s status. Therefore, the need exists for a mechanism to capture the necessary information at the right time, filter out unnecessary information, and reorganize the information for an owner’s use. This paper will focus on COBie as an existing effort to capture and deliver facility information to the owner, in terms of its usability for project turnover and facility management. We provide a comparative analysis between a COBie process and a BIM-supported project turnover process without COBie to evaluate benefits and challenges involved in both. Keywords: COBie, Project Turnover, Facility Management, Comparison 1 Introduction and Background The traditional way of storing and transmitting facility information is document-based, either in paper or electronic format. The architecture, engineering and construction (AEC) industry has welcomed benefits from building information modeling (BIM) in visual presentation and conflict detection for more accurate design and construction coordination. On the other hand, BIM’s ability to become a repository for project information for owners during the operation of a facility has not been utilized yet. BIM’s potential to enable a data-rich facility management has been studied before (Turkaslan- Bulbul et al 2006; Lucas et al 2013; Wang et al 2015) and the benefits to the owner are well documented (Akcamete et al 2010; Arayici et al 2012; Becerik Gerber et al 2011). However, there are barriers for the AEC industry in adopting a process for BIM-based project turnover. The challenges to adoption can be summarized as follows: − Design and construction teams involve multiple participants. Depending their work scope, they use different terminology, naming conventions and specialized software that are not always interoperable with each other. − If there is not a specific procedure defined by the design and construction team at the beginning of a project, the quality of the final handover deliverable to the owner is hard to control. − Multiple sources of information in different formats cost the owner’s personnel much time for locating the information they are looking for. This causes the facility management (FM) teams to create their own set of information. Proc. of the 32nd CIB W78 Conference 2015, 27th-29th 2015, Eindhoven, The Netherlands ްޭޭ Wang, Bulbul & McCoy 2015 A Comparative Case Study for Using COBie in Project Turnover − Owner’s FM team does not usually have the software and the expertise to extract the facility information when handed with a BIM based as-built model, causing the populated data in it untapped. − Even if the owner has the ability to use the model or export the data in the model to an FM system, the benefits from this still depend on the (1) quality of the model, which requires the organizational support by all project participants developing the facility and (2) the interoperability between the BIM systems and FM systems. The building delivery process needs to have a mechanism to capture the necessary information at the right time along the lifecycle of a facility. Such a mechanism needs to: filter out unnecessary information; reorganize the information for owner’s convenience; resolve interoperability problems among different software systems with the assistance of open standard formats and data-based communication; and finally extend the benefits of BIM to a facility’s operation. Since the transition to a data-rich process involves reforming both technical and organizational structure, the AEC industry might resist adoption if benefits do not outweigh the effort or challenges involved. In this paper, we will study COBie (the Construction Operations Building Information Exchange, a data schema and a data capturing process) as an existing effort to capture facility information during the design and construction process and deliver it to the owner. In order to gain a better understanding of how using COBie impacts current BIM-supported turnover process and how COBie can be utilized in practice, we have conducted a case study based on the data from a real world turnover process. The COBie based turnover is then compared to the project’s actual BIM-supported turnover process regarding the benefits and challenges of each with implications from the comparison summarized. 2 Case Study The project in this study is real; a 10000-square-foot 3-storie institutional building with sustainability features. The facility contained virtual design and construction processes, which were utilized throughout the project, and serves as an appropriate lens through which to view COBie. Since owner is promised a BIM-based project turnover, the contractor provided a mobile BIM tool, BIManywhere (BIManywhere 2015) during the turnover for as-built building information visualization and inquiry. For this study, we used the same resources (available design models, construction models, submittals, O&M documents, etc.) to populate COBie data for owner’s FM. All the steps for both processes are recorded and the differences and similarities are analyzed and evaluated in order to inform for future projects for digital building turnovers. 2.1 The non-COBie-based turnover process The handover package was completed by the contractor with the subcontractors’ involvement in the construction model development, the submittal approval and the O&M documents’ collection. The designer’s model and drawings were referenced in the process. The following tools were used during this process: Autodesk Revit, Autodesk Navisworks, Autodesk AutoCAD, Microsoft Excel, BIManywhere Navisworks extension, BIManywhere AutoCAD extension, web browsers, Microsoft OneDrive (optional) and Bluebeam (Optional). Figure 1 shows a process map of the non-COBie- based turnover. The process that is conducted by the contractor and, supported and observed by our team for this research is described in the following sections. 2.1.1 Creating the Record Specification Library 1. Using Autodesk Revit, equipment, room and area schedules are exported as spreadsheets from design team’s 100% completed models (both architecture and MEP). 2. These extracted schedules are used to create tables for the equipment list. New columns are added to the table to store data for the tags (e.g., VCB-1, VCB-2), types (e.g. Volume Control Box (VCB), Variable Refrigerant Fan Coil (VRF)), sub-types under a certain type (e.g. VRF wall-mounted unit, VRF vertical air handler, and VRF 4-way discharging ceiling-mounted cassette), location, and related specification number of each piece of equipment that maps them to design drawings. 3. The final construction model is generated by integrating the designer’s and subcontractors’ models in Navisworks. This model is used to verify the equipment location and catching inconsistencies due to post-design phase project changes. Proc. of the 32nd CIB W78 Conference 2015, 27th-29th 2015, Eindhoven, The Netherlands ްޭޮ Wang, Bulbul & McCoy 2015 A Comparative Case Study for Using COBie in Project Turnover 2.1.2 Selection Set and Saved Viewpoint setup in Navisworks for exporting the model to BIManywhere 1. During the verification of the equipment list and locations in the previous step, the corresponding objects in the construction model are identified and used to create a Navisworks Selection Set. A selection set is created for each piece of equipment on the equipment list. Each selection set is named under a convention that recognizes both its equipment tag and location, and then organized into folders with a 3-level hierarchy (1. specification number and name, 2. equipment type and abbreviation, 3. equipment subtype under a certain type) in the Selection Set window. An extra number is added as a suffix to the name of a selection set, to prevent the conflicts if more than one piece of equipment share the same tag on the schedules in the design drawings. 2. A viewpoint is created for each room or area and for each piece of equipment. The room viewpoints are created using a view angle that looks at the room or area from a door or an entrance to the space. If the room or area is large with multiple doors or entrances, multiple viewpoints are created. The room viewpoints are named by “room number + room name”, and organized in folders with a 2-level hierarchy (1. “Room Views”, 2. Different levels). The equipment viewpoints are created using a view angle that shows each piece of equipment in the center, but excludes most unrelated equipment. The equipment viewpoints are named by “equipment tag @ equipment location” and add the same suffix as the corresponding selection set to differentiate pieces with the same name. The equipment viewpoints are then organized into folders with a 2-level hierarchy (1. “Equipment Views”, 2. Equipment type and abbreviation). 2.1.3 Document preparation and upload to cloud folder 1. Approved submittals and O&M documents have a distributed association with various equipment types, and a scattered approval process. The electrical submittal review system can be used to track submittal approval status. However, since required submittals under the same specification number are usually approved as a complete package, an optional solution is used to create separate submittal tracking lists to break them down into detailed requirements within a specification.
Details
-
File Typepdf
-
Upload Time-
-
Content LanguagesEnglish
-
Upload UserAnonymous/Not logged-in
-
File Pages10 Page
-
File Size-