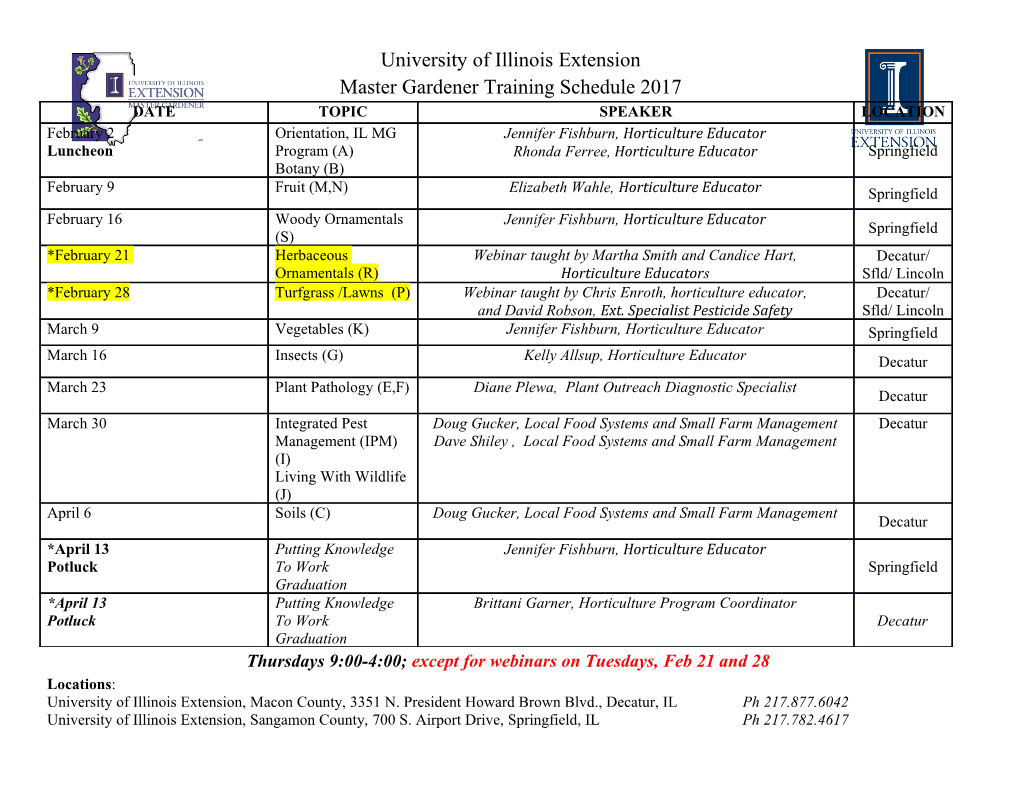
Installation and Maintenance Manual IM 1125-10 Group: Applied Air Systems Part Number: IM 1125 Date: August 2019 Rebel® Commercial Packaged Rooftop Systems Heating and Cooling Models DPS003 – 028A R-410A Refrigerant MicroTech® III Unit Controller Energy Recovery Wheel 3–6 tons 7–15 tons Shown with Energy Recovery 16–28 tons Shown with Energy Recovery Table of Contents Table of Contents Introduction . 3 Optional Outdoor Air Monitor . 75 General Information . 3 Thermal Dispersion Airflow Measurement Technology . 75 Unit Nameplate . 3 ECM Motor . 80 Hazard Identification Information . 3 Unit Options . 82 Mechanical Installation . 4 Economizer Enthalpy Control . 82 Installer Responsibilities . 4 External Time Clock . 82 Receiving Inspection . 4 Exhaust Fan Option . 82 Ventilation Clearance . 4 Proof-of-Airflow and Dirty Filter Switch . 82 Overhead Clearance . 4 Duct High Pressure Limit . 82 Steel Rail Installation . 6 Convenience Receptacle (Field Powered) . 83 Roof Curb Assembly and Installation . 6 Convenience Receptacle (Unit Powered) . 83 Rigging and Handling . 11 Wiring Diagrams . 84 Unit Piping - Condensate Drain Connection . 14 Sequence of Operation . 111 Damper Assemblies . 14 Operating States . 111 Cabinet Weather Protection . 15 Mechanical Cooling . 112 Installing Ductwork . 15 Economizer . 112 Electrical Installation . 18 Preparing the Unit for Start Up . 113 Refrigeration System . 23 Pre-Start of Unit . 113 Piping System . 23 Spring Isolated Fans . 113 DPS Component Description . 25 Servicing Control Panel Components . 114 DPS 016–028 Ton Component Description . 31 Power-Up . 114 VFD Compressor Operation Fan Start-Up . 114 (DPS 016–028 only) . 33 Check, Test and Start Procedures . 115 Variable Speed Scroll Compressor . 37 Economizer Start-Up . 115 Optional Modulating Hot Gas Reheat . 40 Compressor Start-Up . 115 Modulating Hot Gas Reheat . 40 Set Up for Optimum Control . 116 Optional Electric Heat . 43 Air Balancing . 116 Electric Heater Design . 43 Energy Recovery Wheel . 117 Optional Gas Heat . 44 Final Control Settings . 118 Daikin Tubular Heater Series . 44 Final Control Settings . 118 Gas Furnace Design . 44 Maintaining Control Parameter Records . 118 Gas Heating Capacity Data . 45 Maintenance . 119 Maxitrol EXA Star Controller . 49 Performing Service Maintenance . 119 DPS 003–015 Sequence of Operation . 53 Planned Maintenance . 119 DPS 016–028 Sequence of Operation . 54 Unit Storage . 119 Start-Up Procedures . 55 Periodic Service and Maintenance . 120 Operating Procedures . 56 Refrigerant Charge . 121 DPS 003–015 (only) Ignition Control Module for Staged Gas Furnace . 57 Servicing Refrigerant Sensors or Switches . 122 DPS 003–015 (only) Ignition Control Module for Servicing Optional Electric Heater . 122 Modulating Gas Furnace . 58 Servicing the Compressor Ground Fault Interrupter . 122 DPS 003–015 (only) Gas Furnace Ignition and Control Phase Voltage Monitor (PVM) . 122 Troubleshooting . 59 Cleaning Option E Coated Coils . 123 VB-1200 Trouble Shooting Guide . 59 Service and Warranty Procedures . 124 DPS 016–028 Gas Furnace Ignition Troubleshooting . 65 Replacement Parts . 124 Optional Hot Water Heat . 70 Scroll Compressor . 124 Hot Water Heater Design . 70 In-Warranty Return Material Procedure . 124 Optional Energy Recovery Wheel . 71 Warranty Registration Form . 125 System Description . 71 Quality Assurance Survey Report . 129 CORE® Construction . 74 Appendix – Keypad/Display Menu Structure . 130 IM 1125-10 • REBEL ROOFTOPS 2 www.DaikinApplied.com Introduction Introduction General Information Unit Nameplate This manual provides general information about the “A” The unit nameplate is located on the outside of the main vintage Daikin Rebel Commercial Packaged Rooftop Unit, control box door. It includes the unit model number, serial model DPS. In addition to an overall description of the unit, number, electrical characteristics, and refrigerant charge. it includes mechanical and electrical installation procedures, commissioning procedures, sequence of operation information, and maintenance instructions. Hazard Identification Information ® The MicroTech III rooftop unit controller is equipped on DANGER “A” vintage rooftop units. For a detailed description of the Dangers indicate a hazardous situation which will result in death or serious MicroTech III components, input/output configurations, field injury if not avoided. wiring options and requirements, and service procedures, see OM 1141. For operation and information on using and programming the MicroTech III unit controller, refer to the WARNING appropriate operation manual (see Table 1) . Warnings indicate potentially hazardous situations, which can result in For a description of operation and information on using property damage, severe personal injury, or death if not avoided. the keypad to view data and set parameters, refer to the appropriate program-specific operation manual (seeTable 1) . CAUTION Table 1: Program Specific Unit Operation Literature Cautions indicate potentially hazardous situations, which can result in Rooftop unit control configuration Manual bulletin number personal injury or equipment damage if not avoided. Rebel Quick Start Guide OM 1164 DPS Unit Controller Discharge Air Control (VAV or CAV) OM 1141 Space Comfort Control (SCC) WARNING Rooftop and Self Contained Warning indicates potentially hazardous situations for PVC (Polyvinyl Unit Controller Protocol ED 15112 Chloride) and CPVC (Clorinated Polyvinyl Chloride) piping in chilled water systems. In the event the pipe is exposed to POE (Polyolester) oil used in the refrigerant system, the pipe can be chemically damaged and pipe failure can occur. Nomenclature (DPS 003–028) DPS – 010 – A H H G 4 Daikin Packaged System Line voltage 2 = 208 volt power supply Nominal capacity 3 = 230 volt power supply 003 = 3 tons 016 = 16 tons 4 = 460 volt power supply 004 = 4 tons 018 = 18 tons 5 = 575 volt power supply 005 = 5 tons 020 = 20 tons 006 = 6 tons 025 = 25 tons Heat medium 007 = 7 .5 tons 028 = 28 tons Y = None (cooling only) 010 = 10 tons G = Natural gas heat 012 = 12 tons E = Electric heat 015 = 15 tons W = Hot water heat Design vintage Unit style A = Vintage 1 C = Cooling only H = Heat pump (3–20 ton only)- Cooling efficiency H = High (exceeds ASHRAE 92) M = Cooling-only microchannel www.DaikinApplied.com 3 IM 1125-10 • REBEL ROOFTOPS Mechanical Installation Mechanical Installation Installer Responsibilities Ventilation Clearance Below are minimum ventilation clearance recommendations. CAUTION The system designer must consider each application and Sharp edges on sheet metal and fasteners can cause personal injury. This provide adequate ventilation. If this is not done, the unit may equipment must be installed, operated, and serviced only by an experienced not perform properly . installation company and fully trained personnel. Unit(s) Surrounded by a Screen or a Fence: The installation of this equipment shall be in accordance 1 . The bottom of the screen or fence should be at least 1 ft. with the regulations of authorities having jurisdiction and all (305 mm) above the roof surface. applicable codes. It is the responsibility of the installer to 2 . The distance between the unit and a screen or fence determine and follow the applicable codes. should be as described in Figure 1 . Receiving Inspection 3 . The distance between any two units within a screen or fence should be at least 120" (3048 mm). When the equipment is received, all items should be carefully checked against the bill of lading to be sure all crates and Unit(s) Surrounded by Solid Walls: cartons have been received. If the unit has become dirty 1 . If there are walls on one or two adjacent sides of the unit, during shipment (winter road chemicals are of particular the walls may be any height. If there are walls on more concern), clean it when received . than two adjacent sides of the unit, the walls should not All units should be carefully inspected for damage when be higher than the unit. received. Report all shipping damage to the carrier and file a 2 . The distance between the unit and the wall should be at claim. In most cases, equipment is shipped F.O.B. factory and least 96" (2438 mm) on all sides of the unit. claims for freight damage should be filed by the consignee. 3 . The distance between any two units within the walls Before unloading the unit, check the unit nameplate to make should be at least 120" (3048 mm). sure the voltage complies with the power supply available. Do not locate outside air intakes near sources of contaminated air. Service Clearance If the unit is installed where windy conditions are common, install wind screens around the unit, maintaining the CAUTION clearances specified (see Figure 1). This is particularly Location . Care should be taken for the installation location to minimize important to maintain adequate head pressure control when snow drifts on the outdoor coil. mechanical cooling is required at low outdoor air temperatures. Allow service clearances as approximately indicated in Figure Overhead Clearance 1. Also, Daikin recommends providing a roof walkway to the 1 . Unit(s) surrounded by screens or solid walls must have rooftop unit as well as along each side of the unit that provides no overhead obstructions over any part of the unit. For access to most controls and serviceable components. heat pump models overhead obstructions could allow the Refer to NEC and local for minimum clearances around the formation of dangerous icicles. unit and control panel. 2 . The area above the
Details
-
File Typepdf
-
Upload Time-
-
Content LanguagesEnglish
-
Upload UserAnonymous/Not logged-in
-
File Pages142 Page
-
File Size-