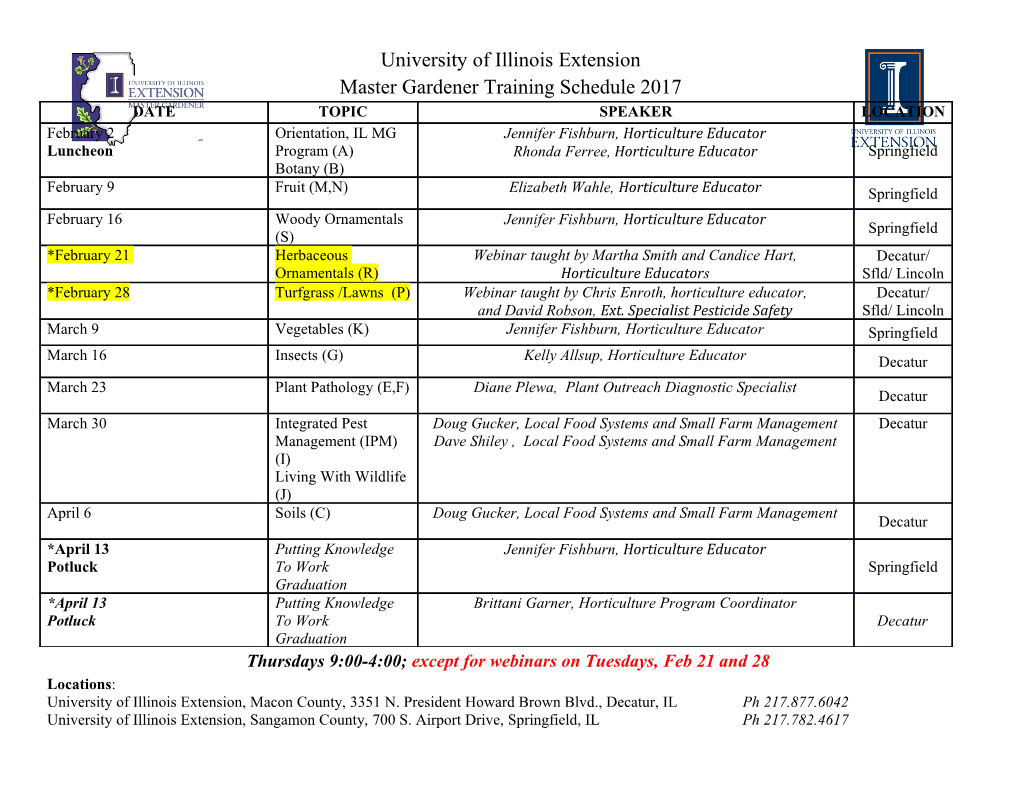
A HYBRID COMPUTER MODEL OF TIRE SHEAR FORCE GENERATION Hans B. Pacejka December 1971 A Study Sponsored by the Automobile Manufacturers Association LIST OF CONTENTS Introduction 2. Brush-Type Tire Model 3. Model with Flexible Carcass Instabilities 5. References,. Appendix I List of Terminology Appendix I1 Non-Dimensional Quantities Non-Dimensional Equations Appendix I11 Digital Programs ~naloiand Logic Circuits Appendix IV Functions and Parameters 1. INTRODUCTION In this report a technique will be discussed which offem hope for investigating and simulating tire models which can be considerably more complex than existing models used in connection with the study of tire shear force generation. The simulation of the behavior of two different tire models will be discussed :in this report. Reference [l] gives a concise description of this i:nvesti- gation. As often is the case, tackling a problem becomes easier when using a method which comes closer to the way nature "solves" the problem. Frank (Ref.'[2]) was the first to recognize the potentials of following a material element of the tire in its motion through the contact range and the rest of the tire circumference. The material element he elected to follow was part of the beam or string. The differential equation governing this motion has an unstable solution and a special iterative method was devisedl for obtaining a solution ';hr;t fits the boundary conditions, Fr~~nk restricted himself to pure sideslip (no braking or driving force) and a constant friction coefficient, In his doctoral thesis, Trlilluneit proposed follo;h;ing a certain element of tread during its motion through the cogtact patch (Ref. [3]). The base of the elastic elennelzt is asscs:ed to move alcng a straight line and the tire model that is assumed is essentially a brush type with rigid carcass. The friction coefficient \vas considered in Willumeitls st,:tdy to -ri3r:; :.:ith ~lldii:~~c~3zda~5both lon~ltudinaland lateral zi~F- -,-7q ~~1-~~~~e.1ifi~;~ ~CCOL~Y?~. The resultins equations of motion . ' ' 1 C -. ?-. - ,, 2;-?L- ,\I' 2 L- . - ?L .-. D The "tread element following" method has been adopted in modified form for our investigation and it has been extended to a model exhibiting carcass elasticity. The hybrid computer appears to be the computational device best suited to solve the problem. In addition to steady-state motions, transient motions may be considered. First, a relatively simple model which is identical to .the model developed in Reference [4:] and which will be designated as tIhe brush type model, will be considered. In the present study the pressure distribution and friction coefficient can be chosen according to experimental findings. By proper selection of parameter values the model is expected to give satisfactory results. These parameters mag be taken as functions of vertical load, speed of travel, and road contamination state. This relatively s imp :le mode 1 thought to be useful mainly in cormectio n with the sirnulistion of the motion of a complete vehicle. The relatively slowly var:ying motions of the automobile may be calculated by the digital computer wh.en the hybrid configuration is used. The rapid motions of the tread element when running through the contact area the analog computer. Some of the functions usea in the latter simulation may also be computed by the digital the vertical pressure distribution and thus with load transfer. When the speed of travel varies -7 ccr-,,,-aey2.z p,-,L,--~~:_ y3 -. CI-.:?sic;ulati.sr: ?:A;?, also the coefficient of , + *- , . , ., - -- 7, P.,>.. -4.; -.,, -< . .,: (., 1'7 :> 187,- . -- -i v...i .. ,,,,, - lc: oe ug>nt?,?.du:'i;:g th3.t rur~. parameters. The effect of such parameters as carcass zeometry and aaterial properties is represented by an influence or Green function. It will also be demonstr3ated that the response to camber angle can be sirnu1at;ed by this model in a natural manner. ?4oreover, the introduction of carcass compliance creates the possibility of examining the response to time-varying wheel-axle motion inputs. The wavelength should be chosen large with respect to the contract length. By increasing the numbzr of tread ele- ments which are followed simultaneously during one passage and by consid2ring more than one row of tread elements each exhibiting different contact lengths and pressure distributions (functions of vertical loa6, slip ang:Le, camber angle, etc.), the model approaches the nearly perfect representation of the real tire. Note, however, that mass and hysteresis of the tire b0d.y has not been included. High flqequency motions are as yet dis- regarded. The approximate theory of high frequency response de- veloped in Reference [5] may give an indication in which direction the nrodel must be modified in order to cover also this aspect of tire response. The first mod21 to be treated consists of a rigid czrcass provided xith a row of el~stictread ele~entsv13ich contact the road surface over the length where the vertical pressu-e possesses a positive value. Of the large number of elements present in the contact range only one ':ii:Ll be follo7red during its passage through the contact pzitch. Fcr steady-state notions the deflections and shear forces at a x-coordinate (i.e., at a certain distance behind or ahead of the vertical plane through the wheel-axle) do not change 'dith time. Consequentl-y , the integral of shear forces encountered by one element when rur-ning through the contact patch produces $he total forces and moment acting from ground to tire. Under the influence of longitudinal and lateral slip, the element (Figure 1) which may show different stiffnesses in lateral (8) and longitudinal (x) directions, undergoes a complex variation of deflections. The decaying friction soefficient function (Fi~ure2) causes the motion to become unstable. in practice, this is reflected in the often observed slip-stick phenomenon. The model's tread eleinent exhibits both mass (necessary for ar: oscillating rno'cion) and damping (for stabilizing the not lo^.). For the sake of simplicity, it is assumed that u is a continuoss function of sliding splaed, V s ' and approaches zero when Vc+O. u The base point, E, of' the elastic element which is the point ., .A :r? ?. 2 (2; <-P-c-,,L 2 - *..- -- -l.~-C zt~acr:ec! to tr,c cc~c2:: 171;dz.e 3), xoves ill 7 ?..A? -. \ 1 L .-. - , .-' -- - p 1- -', 1- m , 2 7- ?. u - -. , "-.. ,- A- - -. --- 5 L., - . - . ~21~?-e cfO-2t . ,- . - -. - -iL- ." A %2 1 L~~~ :..- . -. 1- . ~OYY?S?O'?C:~.I? c . , -- - # ,. "- , T.*-. -, < - . - 7 -.., :+ I longitudinal shift 5, of the contact length may occur due to a driving or braking force. The influence of these shifts is felt - in the resulting aligning torque (aboif the vertical axis through the wheel center). These uniform carcass deformations will be held constant during each run of the element through the contact patch and-- updated at the end of each run. Only an,effective fraction of the carcass deflection (cc, ?)c may be taken into account due to the fact that the center of vertical pressure is not shifted over the same distance. ,- - _ - _ ^ . , __ -._"I. 4, - - 7- - Figure 1. Tread Element. Figurle 2. Coefficient of Friction. 5 Figure 3. The Rigid Carcass r rush-Type) Tire Model The center of the wheel has a speed V. Slip angle a indicates the angle between speed di.rection and (vertical) wheel center plane. We have a lateral speed, VY' which is equal to the lateral slip or creep speed, V : cY The longitudinal speed of the wheel center becomes: = cx v X v cos The wheel rotates about its axle (y-axis) with a speed -R Y . When under free rolling conditions and a=O the effective radius i.s denoted by Reo = V//nyol, we define the speed of rolling under general conditions: and the longitudinal slip speed: We introduce the two quantities which define the state of slip under straight line rolling, viz., the longitudinal slip sx and the lateral or side slip s Y: s Y = Vcy/Vx = tan a In general, also a turn slip due to a rotational speed QZ about the verticai z-axis will occur. Ir - l*".*i 1 The base point B of the tread element (Figs. 1,3) has speed components : v~~ = v CY + (x+ac)nz (8) I / I The sliding speed of the contact point (tip of element relative I to the road) is given by: I I For motions with relatively long wavelengths, the terms with QZ may be neglected. Henc:eforth we shall di-sregard the influence of the rotational speed artd use the equations: The tread element moves through the contact range with a speed equal to the rolling speed VT. The contact length is denoted by L = 2a and the time for one run through the contact patch becomes Note that the run time tends to infinity when the wheel is locked. This limits the analog simulation to sx values smaller than unity. As soon as the element has reached the end of the contact length (trailing edge) a new element is assumed to enter at the' leading edge. The i-th run starts at the instant ti-l and ends at + At. Coordinate x of the base of the element is determined by: The element has stif'fnesses kx and k and damping coeffi- " Y cients cx and c in x and y direction, respectively. At the tip Y of the element a concentra.ted mass, m, is considered to be present. The quantities kx and ky, cx and c and rn are taken per unit Y' length of circumference. TEe same holds for the shear force components qx and q and the vertical pressure distribution qZ.
Details
-
File Typepdf
-
Upload Time-
-
Content LanguagesEnglish
-
Upload UserAnonymous/Not logged-in
-
File Pages73 Page
-
File Size-