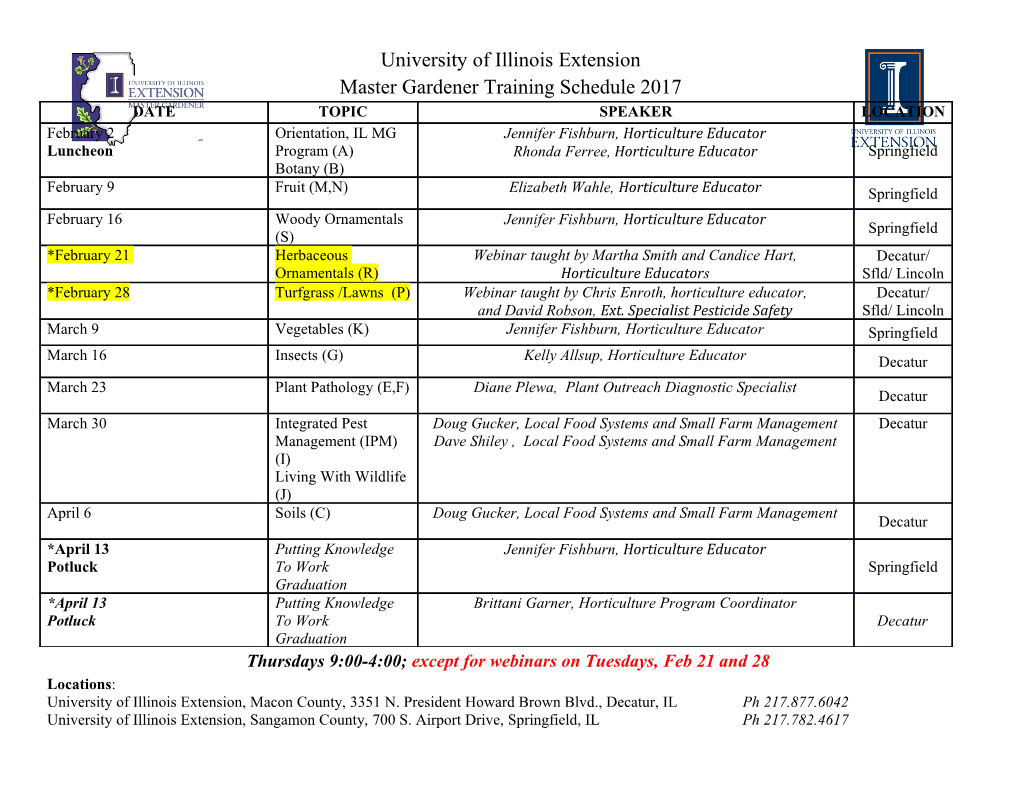
Derivations of the Formulas for Lift in a Centrifugal Drive Robert S. Wilson PhD September 28, 2017 Abstract This is the derivation of the formula for the mean lift in a centrifugal drive This is to go with a patent application for which I have applied. It provides explanatory material for the invention. 1 Definitions If you have a weight on a string and swing it around, the centrifugal force will act from the center of the spin, along the string, out to the weight. A centrifugal drive is one, which will use centrifugal force. The trouble with a centrifugal drive is that, while the weight is on one side of the center, the force will be going in one direction, but when the weight is on the other side, the force will act in the opposite direction, which will result in a net force of 0. The problem is to come up with a scheme where the force on one side will not be cancelled out by the force on the other side. The basic unit in this invention consists of four major parts. The first is mo- tor. There are many possible types of motors available such as: a reciprocating piston internal combustion motor, either gasoline or diesel, an electric motor, which can be energized by such methods as a battery or a generator powered by a gasoline or diesel engine, i.e. a diesel electric or gasoline electric hybrid, or solar among others. If you plug an electric motor into the wall in the US, it will turn at 3600 rpm. For an automobile engine in a car going down a freeway 3000rpm is a common angular velocity, so a motor capable of turning out several thousand rpms would be feasible. The the motor will be in what I will call the center of the figure where there will be a hub. The hub will be a hollow rectangular prism, and, in the hub, a rod will go back and forth as the motor causes the hub to rotate about the center. There will be a closed track, and the ends of the rod will follow the track with the rod stretching from one side of the track to the other. It would be 1 good if there were roller bearings on the ends of the rod as they follow the track around. See the following figure. track rod hub The motor is not shown. It causes the hub to rotate about the center, and the rod moves back and forth through the hub as it follows the track. While I am calling the place, where the motor connects with the hub, the center of the figure, it is not the center of the track, because, if we want there to be net lift, the track will have to move the rod around off center. The next seven illustrations show the rod in the first 6 multiples of 30o, as it moves around the track, and the seventh figure shows the rod returning to its original position. At 2 this point the cycle repeats with the rod being oriented in the opposite direction. 0o 3 30o 4 60o 5 90o 6 120o 7 150o 8 180o And when the rod gets back to 180o, the cycle starts over. A cycle is half of a revolution. Note that, when the rod is at 90o, it does not quite reach from the upper part of the track to the lower. This is because the rod has non zero thickness, so, in order for the rod to avoid contacting the track, the track can not come up to the center. The hub can be offset so that it avoids contacting the track, but since the rod has to follow the track, it can not be offset, so we will need to leave a little space for when the rod is vertical. Also, when the rod 9 is horizontal, the track can not come up to the center, because we need to leave some space for the thickness of the rod. The rod is rectangular in shape. While a cylindrical rod might be possible, a rectangular rod would be stronger and easier to make. The two dimensions which are shown in the figure are the length and the thickness. The third dimension, the width, goes into the page perpendicularly, so does not appear. If the rod has greater thickness, it will contact the track more often, which we want to minimize. Note that we can increase the width of the rod without having to worry about increasing the chances of the rod intersecting the track, and that would result in a stronger rod. A wider rod would be heavier, but that will not be a problem because if the other factors remain constant, the lift is proportional to the mass of the rod. More mass in the rod will result in greater lift. The hub, through which the rod goes back and forth, would be a hollow rect- angular prism. There should probably be bearings where the rod goes through the track. Since the rod is rectangular, the roller bearings at the ends of the rod will be cylindrical. Again, a rectangular rod with cylindrical bearings on the ends would be stronger and easier to make than a cylindrical rod with spherical bearings. If we look at a picture which shows the rod in various positions (without the hub), 10 we see that there will be generally more mass above the center than below. Since the rod stays within the track, the net acceleration will be 0, but force is mass times acceleration, so the fact that there is more mass above the center than below will result in positive lift. Actually, when the rod is close to horizon- tal, there will be slightly more mass below the center than above, but when the rod is close to vertical, practically all of the rod will be above the center. When the rod is close to horizontal, the difference between the amount of mass below the center and the amount of mass above is quite small, and so the centrifugal forces will be close to being balanced; whereas when the rod is close to vertical, 11 there will be much more mass above the center than below, resulting in positive net lift. I am not claiming any particular shape in this patent application. I am merely presenting an example of a shape for the track which will provide lift. The significant new contribution in this application is the track. The track is very important. It is the load bearing element of the device. The lift will come from the top of the rod pushing up against the top part of the track, so the rod pushing against the track has to bear the load. As a result , the track and the rod need to be very strong. The rod could be made from cast aluminum or titanium. The rod could be steel, or any other materials which would have the necessary strength. The track is symmetrical about the vertical line through the center. The rod, which goes through the center of the hub, stretches from one side of the track to the other. Let us describe points on the track using the Cartesian coordinate system. There are many shapes possible for the track. One feature which all of the shapes, which we will be considering, is that when the rod is horizontal, it will stretch from (−L=2; 0) to (L=2; 0), where L is the length of the rod. One important feature of the track is that as the rod stretches from one side to the other, contacting the track at both ends as much as much as possible. In this example, the top part of the track is part of the upper half of an ellipse. In the examples, which we will consider, the top of the track is at (0;L). Stretching the top of the track vertically, so that the top is at a distance greater than L from the center, is a possibility. This will result in increased lift, but bottom of the rod would lose contact with the track over a greater interval. One of the purposes of the bottom part of the track is to keep the top end of the rod in contact with the upper part of the track. This is very important because the top end of the rod contacting the track is the load bearing element of the device. If the top of the rod loses contact with the track, there will be no positive lift, which could be serious if the device is in a vehicle traveling several thousand feet above the ground. If we want to have the interval where bottom part of the rod loses contact with the track to be as small as possible, we will want the thickness of the rod to be as small as possible, while still providing enough strength to lift a payload. Over that interval, the top of the rod will stay in contact with the track because of centrifugal force. Actually, since the negative lift, and we will see how there is some negative lift during a cycle, comes from the bottom of the rod contacting the lower part of the track, when the bottom of the rod loses contact with the lower part of the track, there will be no negative lift. That is not very significant, because the interval when the bottom of the rod loses contact with the lower part of the track is when the negative lift from the bottom of the rod contacting the lower part of the track is when the negative lift is smallest., Once we have the part of the track which is above the horizontal line through the center, the bottom part of the track is determined as the curve which the bottom end of the rod will trace as the top end follows the upper part of the track.
Details
-
File Typepdf
-
Upload Time-
-
Content LanguagesEnglish
-
Upload UserAnonymous/Not logged-in
-
File Pages36 Page
-
File Size-