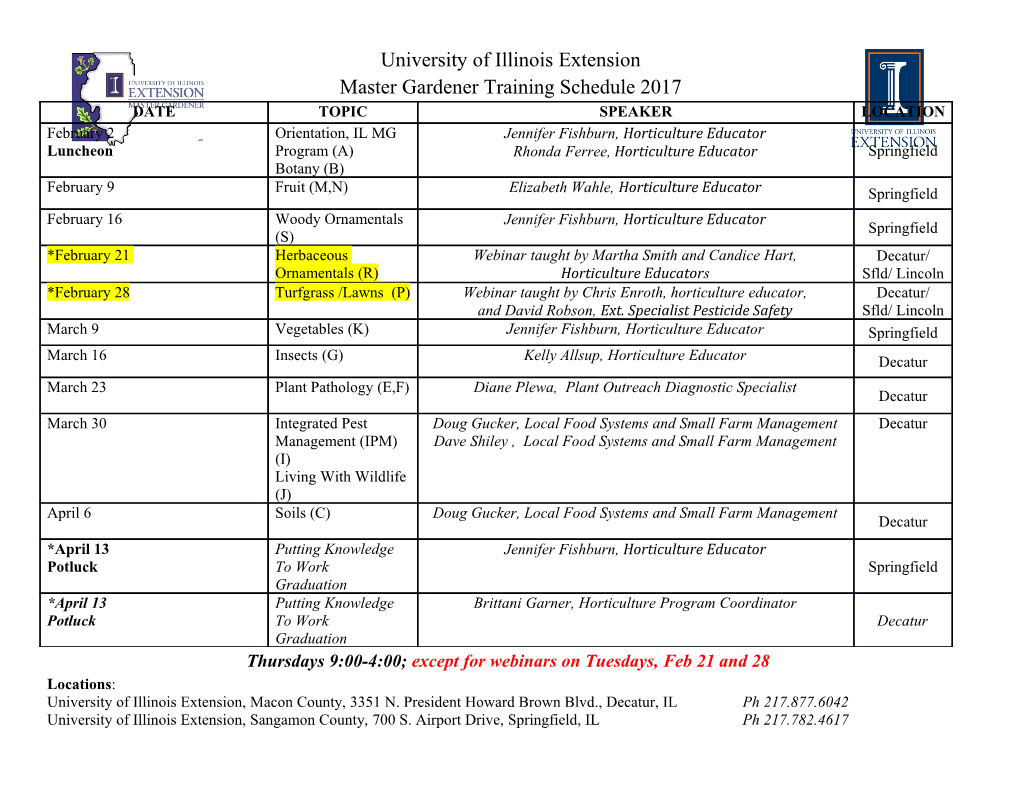
Surface Finishing ‘Flash free’. That’s the main goal to accomplish with all our products. There are many ways to ensure a flash free finish, but when needed, our secondary operations will ensure a clean component ready to accept an applied surface finish. Surfaces of die casting may be classified as one of 5 grades. Where customers specify their requirements, this provides assistance to Alumess in the selection of appropriate tooling and process design. Choose from one of the many finishes offered at Alumess: Decorative Finish Conductivity Protection Electroplating Design od Components for Electroplating Electroplating of Copper from Cyanide Solutions Electroplating of Nickel Electroless Nickel Electroplating of Chromium (Chrome) – Types: Bright, Satin and Black Electroplating of Brass Antique Finishes Hex-free Chromate Treatments Painting Anodizing Impregnation Wear Resistance Cataphoretic Painting Passivating Powder Coating Decorative Finish All decorative finishes require a good quality surface and internal die cast structure to yield the desired effect. The reason for this is that during plating and painting processes, the die casting is heated, which may expose and highlight blemishes on the surface. These effects may be minimized by good component and tooling design. During the assessment of visual impact during component design, requirements are sometimes over- specified, leading to higher costs. These can be avoided through a greater understanding of the finishes www.alumess.com | [email protected] and textures available from Alumess and their likely impact on the final product. Texturing applied to the tooling cavity can dramatically improve the repeatability and yield of plated components. All castings exhibit small levels of internal porosity, so for components requiring decorative finishes, designs and processes that produce denser castings are necessary. Alumess has developed proprietary gating and overflows designs resulting in reduced levels of porosity. The smoother and shinier the surface requirements, the denser the die casting will need to be. For the most mirror-like finishes, such as chrome plating, buffing operations may be required between plating stages (first copper, then nickel and finally chrome in this case). Satin finishes can be achieved by brushing the die casting. Other effects may be achieved by designing them into the tooling or additional operations. Special considerations must be included in part design for electroplating and painting of components. Sharp corners, edges and posts increase electrical current, producing thicker coverage, while blind holes, deep channels and internal features receive less current and therefore less coverage. Another design consideration related to blind holes and deep channels, is that they restrict drainage, which could lead to excess coverage and restrictions in features. The temperature of the process must be known during the design process so that component and tooling design are matched to it, minimizing potential porosity and surface finish problems. Conductivity For some electrical and electronic applications, increased electrical conductivity is required. This is achieved by plating such as nickel, tin, silver or gold. To insure adhesion of precious metals to the die casting surface, an initial copper 'strike' is applied. This process is critical to the success of the plating operation Nickel is then applied, occasionally followed by another appropriate conductive metal. Appropriate design considerations are outlined in Decorative Finishes. Protection Zinc, aluminum and magnesium alloys are relatively active metals that react chemically with the atmosphere. This potential weakness is actually a great strength, as the oxidation forms a formidable barrier coating against further deterioration. Most die cast applications need no further surface treatment to function in their environment. One vital factor in keeping corrosion resistance of untreated parts low is the purity of the alloys from suppliers and subsequent internal housekeeping. Alloy composition must be controlled tightly, as the presence of out of specification material will affect not only corrosion resistance, but also many other mechanical and physical properties. Where components are exposed to an external environment, salt spray tests are often specified. A common treatment for these instances is Hex-Free chromate. www.alumess.com | [email protected] Electroplating Electroplating is a relatively inexpensive and very effective means of obtaining good corrosion protection while at the same time enhancing the appearance of a component. Die castings are usually electroplated for corrosion resistance, decorative purposes, electrical conductivity, solder ability and for wear resistance. The most frequently applied electroplated finishes on die castings are: Copper-Nickel Copper-Nickel-Chromium Copper and Antique Copper Brass and Antique Brass Tin There are 2 common electroplating methods: barrel plating and rack plating. Barrel plating is a bulk method limited to relatively small and light castings. Components produced using Alumess's multi-slide process and small-sized conventional die castings are ideally suited to this method. This is the most effective method of plating parts that do not require individual handling. The components, in effect, become part of the plating equipment as they are in electrical contact with the other parts in the load. This feature greatly contributes to the higher efficiencies attained in barrel plating since the entire surface of the workload is in cathode contact. This relatively large cathode contact allows faster, larger volume production when ample current is supplied. The barrel is a closed drum with perforated walls into which the work is placed. The barrel is then immersed in the plating bath and mechanically rotated. Inside the barrel, at each end, is an electrode called a 'dangler'. This is mingled with the tumbling workload, making electrical contact and forming the cathode. Control of the tumbling speed, plating time and current determine the plating thickness for a load of given surface area. Rack plating differs from barrel plating in that the die castings must be attached to racks or fixtures before plating. This requires either some form of universal rack or construction of special fixturing, depending upon the shape and complexity of the part. The rack becomes the cathode when it is immersed in the plating bath. Rack plating is suited to large, heavy or complex parts, which cannot be bulk tumbled without causing damage. Before plating thicknesses are specified, customers must give consideration to environmental and service conditions. These factors include atmospheric, thermal, corrosive, moisture and any other factors, which could adversely affect the integrity of the casting. www.alumess.com | [email protected] Design of Components for Electroplating When die castings are to be plated, the design constraints imposed by the plating process must be considered. Alumess has developed design guidelines and standards to minimize finishing and plating costs, promote an even distribution of plating metals and ensure adhesion. Departures from these may impose cost penalties and reduce performance. The configuration of the casting significantly affects plating costs because electric current is not distributed equally throughout the plating tank, but is concentrated along paths of least electrical resistance. The complexity and shape of the casting influences the current density, and hence the build- up of plating material. Good uniformity of plating thickness is obtained only on gently curving, convex surfaces. Corners, edges, fins, ribs and other protruding features attract more than an equal share of electrodeposited material. Conversely, grooves, serrations, holes, cavities and deep recesses are starved of their share of electrodeposited material. The area that receives the thinnest electroplate is commonly the area of first failure. Specifications for exterior automotive parts recognize this fact, by requiring a minimum thickness of electroplate on any area exposed to view during service. Specific features that influence the distribution of electroplate are illustrated in our website section dealing with component design. Electroplating of Copper from Cyanide Solutions The first step in the electroplating of zinc die castings, is the deposition of copper from a copper cyanide solution to cover the surface sufficiently, so that the substrate is not attacked in the later processing in more corrosive solutions. Although copper is also electroplated from acid solutions, zinc die castings should never be immersed in acid electrolytes without first covering them with a deposit from a copper- cyanide solution. The acid attacks the zinc die castings as soon as they enter the solution and they become badly corroded. A thin layer of copper deposited from a copper-cyanide solution is essential for the protection of zinc die castings prior to further plating in an acid copper or bright nickel plating solution. Electroplating of Nickel Nickel is deposited onto zinc die castings after they have been plated with sufficient thickness of copper. Nickel deposition can be followed by chromium electroplating to obtain a decorative finish and improve resistance to corrosion, wear and tarnishing under indoor and outdoor service conditions. Other decorative finishes on zinc die castings utilizing nickel plating include nickel/copper, nickel/bronze,
Details
-
File Typepdf
-
Upload Time-
-
Content LanguagesEnglish
-
Upload UserAnonymous/Not logged-in
-
File Pages6 Page
-
File Size-