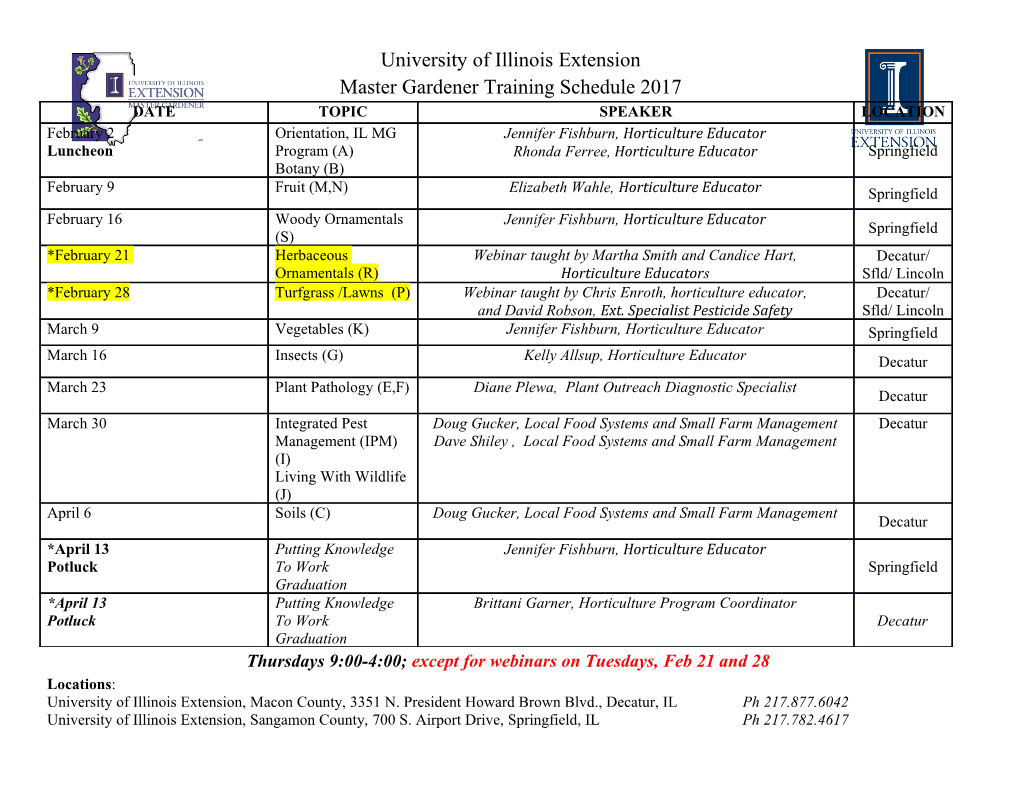
Production of Low-Cost Acetate Deicers from Biomass and Industrial Wastes Shang-Tian Yang and Zuwei Jin, The Ohio State University Brian H. ChoUar, Federal Highway Administration Calcium magnesium acetate (CMA), a mixture of calcium 1 rom 10 million to 14 million tons of road salt are acetate and magnesium acetate, is used as an environmen• I used annually in the United States and Canada. tally benign roadway deicer. The present commercial F Salt is an extremely effective snow and ice con• CMA deicer made from glacial acetic acid and dolomitic trol agent and is relatively inexpensive. However, a lime or limestone is more expensive than salt and other study in New York State showed that although 1 ton of deicers. Also, a liquid potassium acetate deicer is used to road salt cost only $25, it caused more than $1,400 in replace urea and glycol in airport runway deicing. Two al• damage (1). Salt is corrosive to concrete and metals ternative low-cost methods to produce these acetate de- used in the nation's infrastructure, is harmful to road• icers from cheap feedstocks, such as biomass and side vegetation, and poses serious threats to environ• industrial wastes, were studied. CMA deicers produced ment and ground-water quality in some regions (2). from cheese whey by fermentation and extraction were FHWA spends about $12.5 billion annually, a sub• tested for their acetate content and deicing property. The stantial portion of which is used to rebuild and resur• CMA solid sample obtained from extraction of the acetic face highways and bridges damaged by salt corrosion. acid present in a dilute aqueous solution and then back- FHWA has long recognized this problem and has extracted with dolomitic lime to form CMA had about the identified calcium magnesium acetate (CMA) as one same acetate content (70 percent acetic acid or 90 percent alternative road deicer (3). CMA) as the commercial CMA deicer. The sample from CMA is a mixture of calcium acetate and magnesium dried whey fermentation broth contained 50 percent acetate. It is currently manufactured by reacting glacial acetic acid or 63 percent CMA, with the remaining solids acetic acid with dolomitic lime (CaO-MgO) or fime- being other organics and salts present in whey. Deicing stone (Ca/MgCOs). CMA has a deicing ability compara• tests showed that CMA samples from fermentation and ble to salt but is noncorrosive and harmless to vehicles, extraction had an ice penetration rate equal to or slightly highway concrete, bridges, and vegetation. It is bio• better than the commercial CMA. Cost analysis showed degradable and associated with no identified environ• that CMA can be produced at a product cost of $204 to mental concerns (2). CMA is not simply noncorrosive; it $328/ton, less than 30 percent of the current market price inhibits corrosion (2). Thus, CMA can be used in mix• for the commercial CMA, for a plant size of 8,400 tons ture with salt to reduce corrosion caused by salt. The use CMA per year. The lower CMA cost should dramatically of CMA for highway deicing should save millions of increase CMA use in the deicing market. dollars each year just in highway and automobile main- 60 YANG ET AL. 61 tenance costs. Detailed discussions of the comparison Production by Fermentation between salt and CMA for highway deicing can be found elsewhere (4,5). Several fermentation routes have been widely studied for At the present cost of $l,000/ton, versus $35/ton for their potential to produce acetic acid or acetate from salt, CMA is too expensive for widespread use, although biomass. A comparison of various fermentation routes is some studies have shown that all its material costs may given in Table 1. be offset by the savings in infrastructure replacement costs (2). Consequently, CMA is used only in limited Aerobic Acetic Acid Fermentation areas where corrosion control is required or in environ• mentally sensitive areas to protect vegetation and ground Acetic acid (vinegar) traditionally has been produced water from salt contamination (6). The use of CMA as a from ethanol derived from sugar fermentation. This deicer, however, will be cost-effective and better accepted process generally involves two steps: (a) fermentation if its price can be reduced to $300 to $400/ton (7). It is of sugar to ethanol by yeasts such as Saccharomyces thus desirable to produce low-cost CMA deicers from cerevisiae and Kluyveromyces fragilis, and (b) oxida• alternative feedstocks such as biomass and industrial tion of ethanol to acetic acid by species of Acetobacter. wastes (8). The reactions are as follows: Several alternative methods to produce acetic acid and CMA by fermentation of biomass and extraction of CgHiiOe ^ 2 CO2 T + 2 C2H5OH ^ 2 CH3COOH acetic acid from dilute aqueous solutions are reviewed. An anaerobic fermentation process to produce CMA This process has two major disadvantages. First, the from cheese whey, a dairy waste, is examined in detail. acetic acid yield is, at most, only two-thirds of the sugar Deicing performance and cost analyses of this new, al• source, since up to one-third of the organic carbon is lost as carbon dioxide (CO2) during the ethanol fer• ternative CMA deicer from whey were also studied and mentation. In practice, the yields of ethanol and acetic are discussed. acid are rarely more than 90 percent and 85 percent of the theoretical value, respectively. With an overall effi• ciency of 75 percent, only 0.5 g of acetic acid can be PRODUCTION OF ACETIC ACID AND CMA produced per gram of sugar used. Second, strict aera• tion is required for the growth of Acetobacter to con• Acetic acid is an important raw material in the chemical vert ethanol to acetic acid. Improper aeration may industry. In the last several years, the yearly production cause serious damage to the acetic acid bacteria or re• of acetic acid in the United States has continuously sult in overoxidation of acetic acid to CO2 and water. increased to 1.8 million tons in 1995. Current commer• As a result, the conventional aerobic vinegar fermenta• cial glacial acetic acid is exclusively produced from tion process suffers from low yield and high production petrochemical routes (9,20) and costs $0.7/kg. The high cost, and thus cannot compete well with the natural price of glacial acetic acid contributes to the major gas-based synthetic process (9). cost of CMA deicer. Thus, there has long been an inter• Earlier studies conducted by Stanford Research In• est in producing low-cost acetic acid and acetate from stitute concluded that CMA production via aerobic fermentation (2 2). vinegar fermentation of glucose or hydrolyzed corn TABLE 1 Comparison of Various Fermentation Routes for Producing Acetate from Biomass Aerobic Vinegar Anaerobic Homoacetic Fermentation Anaerobic Fermentation' Digestion' C. thermoaceticum C. formicoaceticuni' Substrate Glucose / Ethanol Glucose Lactate Cellulosics Acetate yield <60% >80% >95% 30% - 80% Acetate cone, (w/v) 6% - 10% 2% - 10% 3% ~ 7.5% <3% Fermentation time 1~ 3 days 1-7 days 2-7 days 6-15 days Energy requirement high in medium low high in product fermentation recovery 'requires ethanol fermentation of glucose first; ethanol is the substrate for acetic acid fermentation, ^lactate can be obtained from carbohydrates through homolactic acid fermentation, 'methanogenic activities are suppressed to allow acetate accumulation. 62 SNOW REMOVAL AND ICE CONTROL TECHNOLOGY Starch was not economically competitive and did not Acetogenium kivui. Ljungdahl et al. (15) studied three warrant further consideration (12). This prompted the thermophilic acetogens—C. thermoaceticum, C. thermo• search for anaerobic homoacetogens for acetic acid and autotrophicum, and A. kivui—for their abilities to pro• CMA production. duce CMA from glucose. It was concluded that although C. thermoaceticum was the most desirable, none would Anaerobic Homoacetogenic Fermentation have successful industrial applications. Recently, Parekh and Cheryan (16) reported a mu• There has been increasing interest in producing acetic tant strain of C. thermoaceticum that could produce ac• acid from renewable resources by using anaerobic etate concentration as high as 10 percent (weight per homoacetogens because of the high product yield from volume) in a fedbatch fermentation with cell recycle. anaerobic fermentation. In contrast to the aerobic The reactor productivity was 0.8 g/L/hr and the acetate vinegar process, nearly 100 percent of the substrate yield from glucose was 80 percent. However, the results carbon can be recovered in the product, acetic acid, by were obtained with a synthetic medium with a high anaerobic fermentation. The reaction is as follows: yeast extract content. Efforts to use inexpensive indus• trial feedstocks for acetate production by using this CgHiiOg ^ 3 CH3COOH strain have not been as successful. None of the homoacetogenic bacteria can ferment The actual acetic acid yield from glucose is usually lactose; however, several of them can readily convert greater than 80 percent (weight per weight). With a few lactate to an equal amount of acetate. Among all the exceptions, the final concentration of acetic acid pro• homoacetogens, only A. woodii, A. carbinolicum, and duced from the anaerobic process is usually low, only C. formicoaceticum can ferment lactate to acetate. about 2 percent, as compared with 6 to 10 percent A. woodii can grow at temperatures below 32°C and at obtained from the aerobic process. This low product a pH between 4.5 and 6.8. C. formicoaceticum can grow concentration leads to a prohibitively high energy at a temperature around 35°C and a pH between 6.6 requirement for the recovery of the acetic acid pro• and 9.6 (17). Both organisms are inhibited by acetic duced in the anaerobic process (13), although the over• acid, but C.
Details
-
File Typepdf
-
Upload Time-
-
Content LanguagesEnglish
-
Upload UserAnonymous/Not logged-in
-
File Pages10 Page
-
File Size-