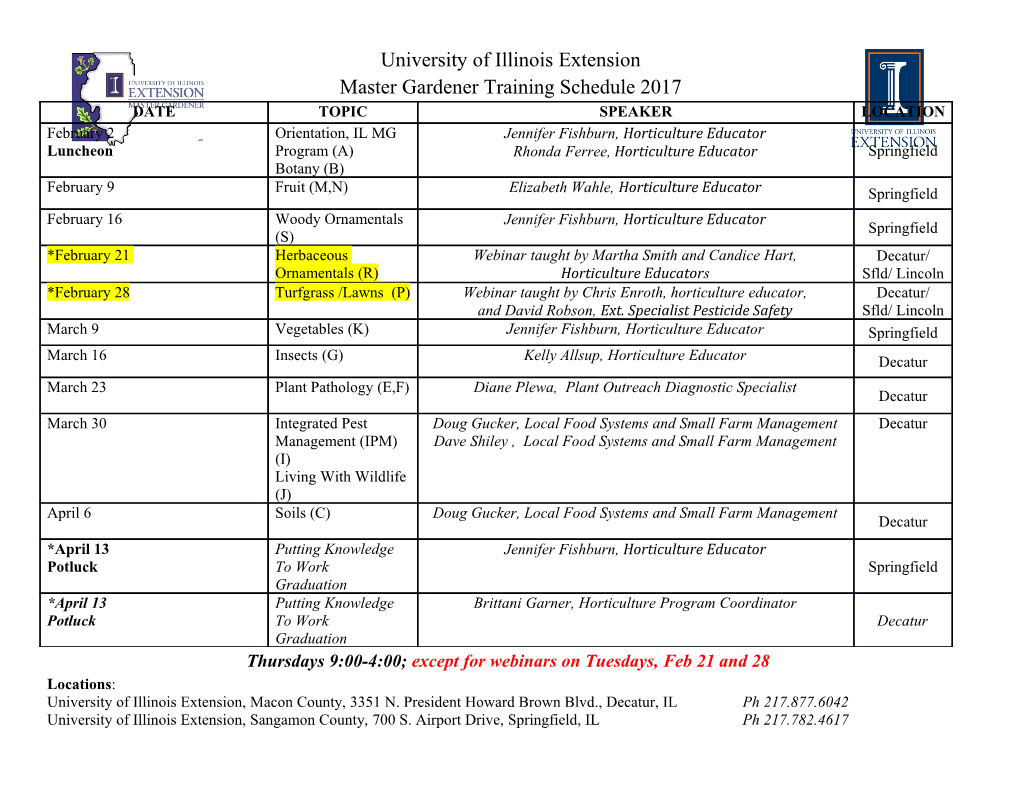
Gordon Food Service® U.S. Stewardship Report 2015 2 A MESSAGE FROM THE GORDON FAMILY Gordon Food Service is a multi-generational family-managed business. TABLE OF CONTENTS Taking care of what we have been blessed with and passing it on to those who come after us embodies the Gordon family philosophy. 2 A Message from the Our company was founded on serving the community. In 1897, Gordon Food Gordon Family Service began as a butter-and-egg delivery business, working with local farmers to ensure a steady supply of quality products to grocers. This brought a deep 3 Environmental appreciation for the land used to grow and produce the food that sustains us. Responsibility It also built personal ties to lives of the people we met along the way—a family that includes everyone connected to the food and products we deliver. • Home Office It’s a relationship-centered way of doing business that has helped our growth • Distribution Centers in a world filled with constant change. We recognize the responsibility we have to care about the people we interact with and employ, as well as protect • Gordon Food Service Stores® the resources we use while conducting our business. • Transportation This responsibility is called stewardship—accounting for how our business practices and decisions impact our customers, employees, vendors, and the • Food communities we serve. In our third annual Gordon Food Service Stewardship Report, we take a look at our 2015 stewardship efforts in three major areas: 7 Social Responsibility • Ensuring Corporate Sustainability • Product Safety • Minimizing Environmental Impact • Local Purchasing • Promoting Social Responsibility • Employees Because stewardship is a long-term commitment, we look at our performance not as an accomplishment, but as progress report. It’s a yardstick we can use • Diversity & Inclusion to measure and improve our accountability and assure the sustainability of • Community our business, our people, and our planet. The 2015 report shares facts and figures about our performance, in addition to presenting stories about our people. We want to show their heart to serve our customers and our communities during a year of unprecedented growth. With five new distribution centers in the U.S. and Canada—Imperial, Pennsylvania; Douglasville, Georgia; Aberdeen, Maryland; Kannapolis, North Carolina; and Calgary, Alberta—our footprint is growing, but our commitment to service, sustainability and stewardship endures. Gordon Family 3 ENVIRONMENTAL RESPONSIBILITY Stewardship is defined as “the careful and responsible management of something entrusted to one’s care.” We believe the planet has been entrusted to all of us to safeguard for future generations. Following are some of the most significant and recent steps we’ve taken to minimize our environmental impact. LEED SILVER CERTIFICATION LEED measures five categories, providing a score based on how well a building’s design and construction meets best-in- class building strategies. The Gordon Food Service Home Office earned a Silver certification. Home Office Gordon Food Service opened its sustainable, energy-efficient, 384,000-square- foot Home Office in 2012. The building was designed to meet LEED New Construction certification standards and in September 2015, the third anniversary of the building’s opening, leadership announced the building 220 had been awarded LEED Silver Certification. GEOTHERMAL WELLS The honor, presented by the U.S. Green Building Council, recognizes the implementation of measurable systems and methods designed to achieve high The Home Office has the performance in five categories. Here are ways Home Office design features largest private geothermal contributed to the Silver certification status in each category: system in Michigan. This Sustainable site development: Bicycle parking and storage; reserved parking enables the 384,000-square- for low-emission vehicles; and vegetated live rooftops. foot building to be heated Water savings: Water-efficient landscaping, including sensors to measure soil without natural gas. moisture and prevent overwatering; and low-flow plumbing fixtures. Energy efficiency: Energy-efficient geothermal wells used for the heating and air conditioning system; parking lot lights that dim during periods of inactivity. Materials selection: Use of recycled material and wood from sustainable forests; local sourcing of construction materials; construction waste routed to recyclers. Abundant natural Indoor environmental quality: High-performance window glass that prevents daylight and individual heat gain in summer and heat loss in winter; lights that dim or shut off when not in climate control ease use; adjustable workstation air-flow vents; automated blinds to adjust to sunlight. workday stress. LEED Silver certification puts the Home Office among an elite group of large buildings, and demonstrates the company’s commitment to promoting a healthy working and living environment. 61 16 T O N S 342, 6 of electronic waste water bottles prevented from parking spaces parking spaces recycled or refurbished going to the landfill in one year due to our refrigerated, filtered for low-emission for electric instead of taken to landfills. vehicles (LEVs). vehicle charging. drinking water system. 4 ENERGY USED PER CASE Distribution Centers DELIVERED ENERGY AND WATER CONSERVATION In 2010, we began working with third parties to perform comprehensive energy analyses of our U.S. and Canadian distribution centers. The reviews evaluated -5.2% -5.5% buildings, processes, automation, refrigeration, lighting, and employee -9.5% -4.1% behaviors. A series of Energy Conservation Measures (ECMs) were identified to guide our progress. Focusing on these measures, we have taken steps to appreciably reduce 2012 2013 2014 2015 energy consumption at a number of facilities. 1.03 0.97 0.88 0.84 kwh/case kwh/case kwh/case kwh/case 3 distribution centers and 1 Store added in 2015. We use high- Sensors turn Refrigeration units have efficiency fluorescent lights off when been equipped to cycle and LED lights. not needed. down during utilities’ 27.2% peak-demand periods. Continuous improvement through standard practices already has significantly reduced the number of kilowatt-hours the company uses to ship a case of product. This effort will be an ongoing focus for all facilities for years to come. We’ve made advances in water conservation and refrigeration efficiency in 2015. Water treatment systems on refrigeration evaporator condensers have resulted in operational and environmental savings. The system extends the life of the condensers and reduces water usage during operation. cumulative reduction in kwh/case from 2011-2015. Our distribution centers in Plant City, Florida; Kannapolis, North Carolina; and Taunton, Massachusetts, implemented VFD (variable-frequency drive) technology to efficiently control refrigeration fans, compressors, and pumps. This process varies the speed of motors based on demand of the load, maximizing the effectiveness of our energy and water usage. We recycle cardboard, plastic, steel, aluminum, wood pallets, and waste oil, diverting tons of Our newest distribution material from landfills in 2015. center in Kannapolis, NC, utilizes VFD technology to maximize energy and water usage. 929 PROVIDING FOOD HANDLING PEACE OF MIND Our distribution centers earned high marks in five-point inspections conducted by AIB International. The AIB audit is not mandatory, but one we enter voluntarily—a third-party analysis that assures customers of our food handling integrity. The AIB gives an overall grade based on our methods and AIB International practices, maintenance, cleaning, pest management, and overall management. yearly average score on A perfect score is 1,000. Among the high points, our Pottsville Distribution food handling at our Center earned its highest score ever—960. distribution centers. 5 SPOTLIGHT ON IMPERIAL Gordon Food Service employees practice stewardship daily. It is our practice to avoid landfills and reduce energy through technology and sensible employee behaviors. The following are several ways our Imperial Distribution Center is working to be a good steward to the environment. Construction Material Landscaping Lighting Almost 25% of all materials were Native plants were used to LED lighting is being used extracted and manufactured minimize the need for irrigation throughout the facility—in the within 500 miles, and 19% of the after becoming established. warehouse, vehicle maintenance products used contained recycled Refrigeration facility, and offices—to dramatically content. More than 86% of all As part of the refrigeration system, reduce the number of kilowatt hours wood products used were Forest we are using variable frequency used compared to similar facilities. Stewardship Council certified. drive (VFD)-controlled compressors Stretch Wrap (Plastic) Recycling to reduce electrical usage as All wrap is collected, baled, 73% of all construction-related well as using VFD controls on the and recycled. debris was diverted from landfills condenser fans to reduce energy. Roofing and recycled. Water Usage A white roof reflects sunlight, Cardboard The building’s baseline water usage reducing the building’s heat All loose cardboard cases or slip was set at 549,110 gallons, but the island effect. sheets are collected, baled, and use of efficient fixtures cut that sold on the commodity market to amount by 36% to 350,040 gallons. be remade into other cardboard boxes or containers. Gordon Food Service Stores From Marquette,
Details
-
File Typepdf
-
Upload Time-
-
Content LanguagesEnglish
-
Upload UserAnonymous/Not logged-in
-
File Pages12 Page
-
File Size-