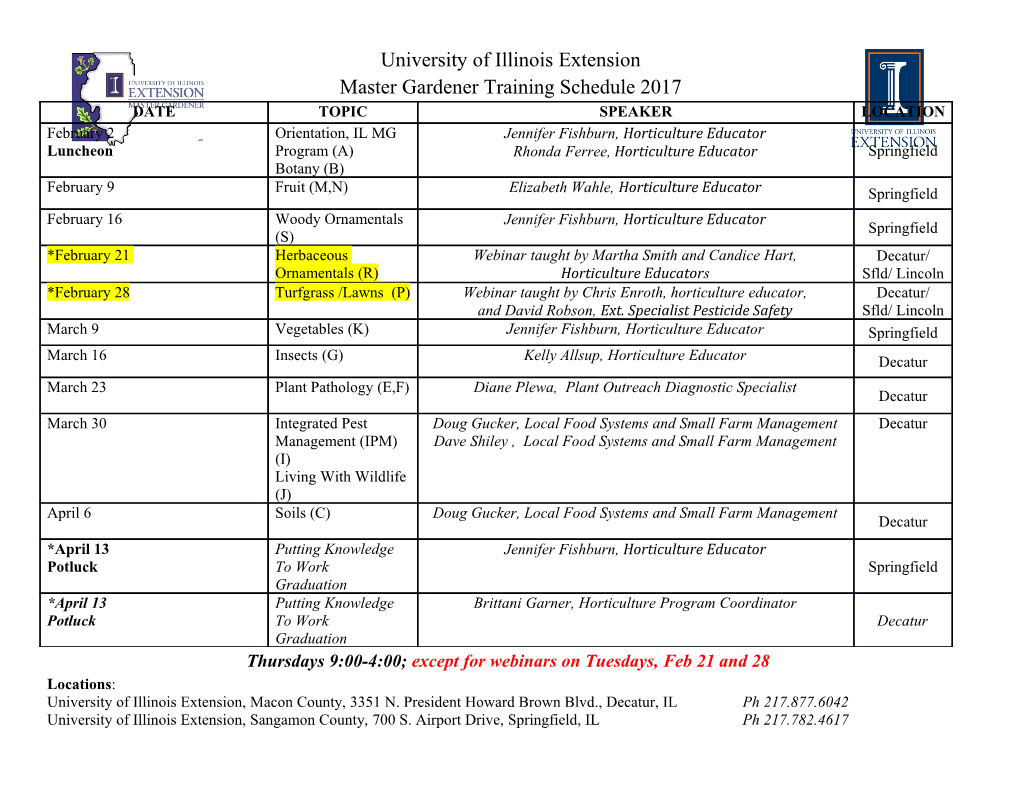
THE AMERICAN SOCIETY OF MECHANICAL ENGINEERS 85-GT-231 345 E. 47 St., New York, N.Y.10017 The Society shall not be responsible for statements or opinions advanced in papers or In discussion at meetings of the Society or of its Divisions or Sections, or printed In its publications. Discussion is printed only if the paper is published in an ASME Journal. Released for general publication upon presentation. Full credit Should be given to ASME, the Technical Division, and the author(s). Papers are available from ASME for nine months after the meeting. Printed in USA. Copyright © 1985 by ASME Downloaded from http://asmedigitalcollection.asme.org/GT/proceedings-pdf/GT1985/79382/V001T01A007/4456674/v001t01a007-85-gt-231.pdf by guest on 23 September 2021 The F-16 Common Engine Bay C. E. PORCHER Manager, Propulsion & Thermodynamics Fort Worth, Texas ABSTRACT subsequent competitive procurement of the engine. THE F-16 COMMON ENGINE BAY In 1979 the United States Air Force elected INTRODUCTION u11der the Engine Model Derivative Pl'."ogram (EMDP) to explore derivative engine concepts The engine cost of modern fighters may run to by the General Electric Company and the Pratt a quarter of the total weapon system cost. and Whitney Aircraft Division of United Since the weapon system may stay in the Technology Corporation with the objective of inventory upwards of 20 years, it is improving engine durability and reducing frequently cost effective to upgrade the engine ownership cost for future procurements engine durability, improve the engine of their first line fighter engines. operability, reduce cost of maintenance or Concurrently, General Dynamics was invited to modify the aircraft propulsion system develop the necessary airframe/engine performance to meet specific or changing interface definition to assure engine weapon system needs. Four engine models have compatibility with the airplane requirements. been installed in the F-16 to date. The This EMDP development culminated in 1981 with Pratt and Whitney FlOO-PW-200 for the the Alternate Fighter Engine (AFE) production airplane; the General Electric J79 competition with General Electric proposing for the F-16FX, a proposed export version; the FllO-GE-100 engine and Pratt and Whitney the General Electric FlOl prototype Aircraft proposing the FlOO-PW-220. Both Derivative Fighter Engine; and the General engines were placed in Full Scale Development Electric FllO-GE-100 'Slimline' production and both met the USAF objectives of 4000 TAC engine in support of the USAF Alternate cycle life and improved engine cost and Fighter Engine program. warranty for application to the F-15 and F-16 fighters. General Dynamics evolved the In 1981 the USAF initiated the Alternate concept of the Common Engine Bay which has Fighter Engine program as a means to improve all aircraft interfaces compatible with the engine durability and cost of ownership either AFE engine and the current Pratt and through a competitive approach for its first Whitney Aircraft PlOO-PW-200 engine. The line fighters, the F-15 and the F- 16. This original F-16 nacelle design , with minor competitive program between Pratt and Whitney modification of the interfaces and engine and General Electric drove the requirements mount structure, was adapted to permit full for a common engine installation interface in interchangeability for the FlOO-PW-200, the F-16. General Dynamics' response was to FlOO-PW-220, or the FllO-GE-100 engines. evolve a Common Engine Bay (CEB) concept Design requirements were set to permit a which would accept either the P&WA. or GE AFE common airplane with no break in the derivative engines as well as the current production line or aircraft model change and P&WA production engine. with appropriate simple kits to permit interchangeability of any of the three This paper discusses the CEB concept and engines in the field at the organizational design approach. level. This manufacturing capability allows the USAF the flexibility to conduct Presented at the Gas Turbine Conference and Exhibit Houston, Texas - March 18-21, 1985 DISCUSSION F-16C/D engine buy in 1986, General Dynamics developed the Common Engine Bay approach which provides the production F-16 with the F-16 BACKGROUND capability for utilizing either AFE engine. Small kits will permit future base changeout The F-16 evolved from the YF-16 prototype of any of the FlOO-PW-200, FlOO-PW-220, or GE demonstration program from 1972 to 1974. The FllO engines if required. contract was awarded in 1975 for an intent to buy 1377 aircraft with the objective to be Figure 1 compares the physical characteris­ co-produced by a four country European tics of the three engines. The most Downloaded from http://asmedigitalcollection.asme.org/GT/proceedings-pdf/GT1985/79382/V001T01A007/4456674/v001t01a007-85-gt-231.pdf by guest on 23 September 2021 Participating Group (EPG): Belgium, Denmark, significant difference being the hig�er �etherlands and Norway. As of August 1984, weight of the GE FllO. Both AFE engines met some 1200 F-16's have been produced and 11 the safety criteria for single engine countries now, or will, employ the fighter as aircraft, i. e. , back-up control for adequate their first line of defense. The airplane is "get home thrust", prime reliable main fuel powered by the Pratt and Whitney FlOO-P\·/-200, gear pump, and automatic altitude spool-down an afterburning turbofan engine in the 25, 000 airstart capbility, on pilot command. pound thrust class. DESCRIPTION •AUGM!NTl!llUH611tAN ;y""·, F.1.00-PW.-2.00 _ '\ - Although originally conceived as a light • VAHIA�l I 1111 fI t; IJllll VAN l> . • J >lAGt f AN 10 >I AG� I OMPHt >>UH weight 'day' air-to-air fighter, the USAF • VAHIABl [ ARl A fXHAUST NO/ll \ ! •HYUHAUll(fNLINt LllNIHUl Wlllj tltlTHUNll . moved the primary role to air-to-ground for WPfHVIS\lHY - ..\.. 'j •'-". the production F-16. With a 'dual role' o I "HU�,] LL ASS z; OUO l� S JllllHS �- mission of A-G, or A-A, the engine cyclic usage is very high and as experience has aptly demonstrated, is very severe on engine ,��---- ·�IMllAH TU fIUO f'W IUO durability. This leads to high maintenance 1 •UIOllAlll!lTHUNll!N l>INlCOr.THUL ancl. over11aul costs. Due to the multiple •INlHI A>tU l H l lU Ht l�UUU l Yl ll mission requirements, engine operability, compatibility and mission matching became essential to engine selection and the mission severity requires durable engines. r---fW>l�1--------- • AULM! Nlt U I IJH�IJI AN F110-GE-100 •VAHIAet!INtl!GUllJIVAt.ll> •l>lALl IAN 9>TAGl lOMPHl>>UH USAF ALTERNATE FIGHTER ENGINE PROGRAM •VAHIABl t AIUA l �HAU>l NOlll t •fltllflUlllll tPIGIJHUlr<IHUl WllH HYUHAULllfllllUNUAIOCY IOIHIU!BS • '\... The USAF ASD Engine SPO, under the Engine JBJUIBS Model Derivative Program, initiated a _1.l­ competitive program with the objective of at � least doubling the engine cyclic durability Figure and opening the way for a more beneficial warranty plan. Pratt ancl. Whitney's entry was Engine installation versatility i3 shown in the FlOO-P\•/-220, a derivative of the Figure 2 by the formation of F-16's powered FlOO-PW-200; and General Electric proposed by the FlOO-PW-200 (top), the GE FlOlDFE, and the GE FlOlDFE, a derivative of the FlOl the GE J79. The afterbody and nozzle engine. configurations are an interesting study. The FlOO and FlOlDFE are comparable length DEVELOPMENT PLAN engines, but the older technology J79 engine is considerably longer requiring a longer low In 1978, General Dynamics was given a angle afterbody fairing to interface with the development contract to conduct interface and nozzle. As can be seen, the FlOlDFE nozzle compatibility studies for the GE FlOlDFE has a slightly steeper boattail angle than which led to a prototype-engine flight test the FlOO in a compromise to keep nozzle program in F-16A#l at EAFB in early 1980. weight low by using shorter external nozzle This flight test demonstrated compatibility leaf segments. with the engine/nacelle physical interfaces; inlet-engine compatibility for the complete aircraft maneuver envelope; and, mission matching for engine/airframe perfornance requirements. In addition, preliminary engine cyclic usage data was obtained to aug­ ment engine usage field data from the F-16/FlOO tactical aircraft. Following a successful 55 flight test program of the GE FlOlDFE in Fl6A-l both the GE FllO (redesigned from the FlOlDFE) and the FlOO-PW-220 were placed in full scale development. Both engines subsequently successfully demonstrated in Accelerated Mission Testing (AMT) durability in excess of 4000 TAC cycle life. Notified by the USAF of its intention to compete the engines for the Figure 2 2 The inlet on the F-16/J79 differs from inlets F-16A-1/F101 OFE FLIGHT SUMMARY for the FlOO and FlOlDFE in that a fixed •FIRST FLIGHT-19DEC1980 compression ramp was added to the basic F-16 •58 FLIGHT HOURS FllGHTS/75 normal shock inlet. The ramp helps to reduce •NO TRIM RUNS •ENTIRE P.ROGRAMFLOWN WTH ENGINE drag due to the increased spillage of a lower S/N-003 FIRST F101 OFE EVER BUILT engine ci.irflow and improves supersonic acceleration by improving inlet recovery. Figure 3 compares the maximum power airflow (ratioed to the inlet flow capacity) of the PILOT VIEW Downloaded from http://asmedigitalcollection.asme.org/GT/proceedings-pdf/GT1985/79382/V001T01A007/4456674/v001t01a007-85-gt-231.pdf by guest on 23 September 2021 four engines versus Mach number. The lower "Pu11he throttle where you wan1 anywhere m the flight airflow of the GE J79 all0ws the installation envelope and nothing bad happens." - THAT'S OPERABILITY of the ramp in the same basic capture area.
Details
-
File Typepdf
-
Upload Time-
-
Content LanguagesEnglish
-
Upload UserAnonymous/Not logged-in
-
File Pages8 Page
-
File Size-