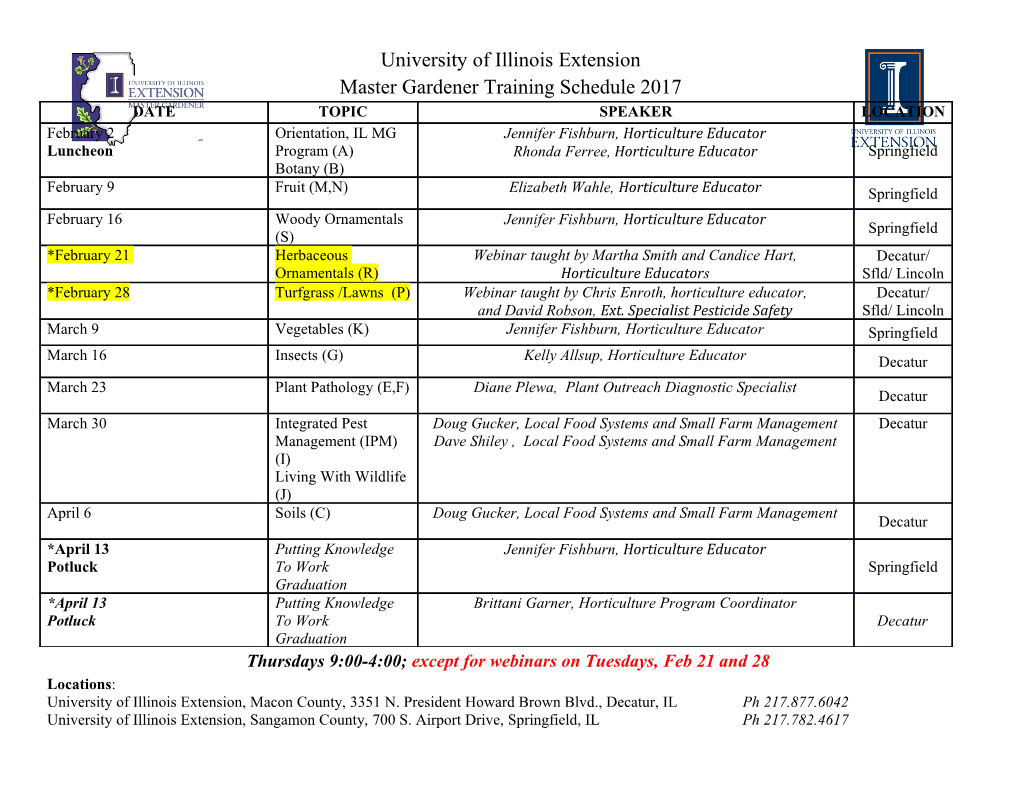
System 3R USA System 3R’s WorkMaster Linear flexible manufacturing system. What’s on Your Pallet? Implementing automated pallet systems in small and medium-size shops can reduce labor costs and increase productivity. By Susan Woods, Contributing Editor ore small and medium-size job to be as efficient or more efficient than ica Corp., Charlotte, N.C., gave this shops are turning to unattended who he is supplying to stay in the game. ROI example: “Say the shop rate is $100 Mmachining to compete effec- A lot of industries, especially the medical an hour and they have a complicated job tively. A key part of many lights-out strat- and aerospace, say, ‘Here is a 5-year con- that takes 10 hours to set up. A 500mm egies is an automated pallet system to tract but we want costs down over that 5 pallet costs around $4,000. If they run load and unload pallets of fixtured parts years.’ How are you going to offer price that job four or five times a year, they into and out of machine tools. By keep- reductions unless you automate in some could save $4,000 to $5,000 worth of ing a machine running through a second way and become more efficient?” setup time.” or third shift without adding personnel, The main obstacle to small and me- shops can increase productivity. dium-size shops taking advantage of auto- A Fit for All Sizes While many consider automated pallet mated pallet systems is the initial up-front Generally, a standard HMC has two systems only suitable for large manufac- investment. “Between the HMC, pallet pallets, which the operator sets up man- turers, lights-out machining is some- system, additional pallets, fixturing and ually. The most common size in the U.S. thing shops with five to 100 employees tooling, it may be overwhelming to some is the 500mm (20") square, followed by can achieve, according to sources inter- shops,” said Cari Vanik, assistant sales 400mm and 630mm square machines. viewed for this article. manager for machine tool builder Kita- The majority of automated pallet systems “A 400mm or 500mm horizontal ma- mura Machinery of USA Inc., Wheeling, are used in conjunction with HMCs with chine center is a big investment for any Ill. “But with proper planning and guid- 3-, 4- or 5-axis motion. job shop, and for a small shop that invest- ance, the return on investment is often Linear-type automated pallet systems ment is magnified,” said Robert Hum- seen sooner than expected because of have a pallet carrier “crane” running on phreys, international sales manager for more efficient practices and unmanned a rail-guided vehicle (RGV). The ma- Fastems LLC, West Chester, Ohio, a machining.” chine tool and load station(s) are on one third-party integrator of flexible manu- Kyle Klaver, product specialist for side with the pallet storage rack on the facturing systems. “So a small shop has machine tool builder Okuma Amer- other. A stacker crane runs in between 72 | JUNE 2013 | CTE PartsHandling.indd 72 5/20/13 2:20 PM What’s on Your Pallet? (continued) pandable capacity to 300 pallets, 10 ma- chines and four workstations. on a linear rail. In addition to linear systems, “pallet There are also systems where the load pool” systems are available. A typical pal- stations can be opposite the machine. The let pool shape is circular, but other shapes RGV crane can move left and right, and are used. These systems can hold eight to has a pallet handling device that moves 40 pallets or more and are dedicated to a CNC CARBIDE TOOLS forward and back. The system brings the single machine tool. Pallet pool systems 1 tool –1 holder –10 functions pallets to the load station and the system often offer shops vertical storage alter- control informs the operator what actions natives, an option for shops that need to to take, such as load, unload and where conserve floor space. to put finished parts. Most metalworking professionals con- IN STOCK These types of systems are expand- sider automated pallet systems as being Over 1,108 miniature reamers able. For instance, Okuma’s Palletace-M for high-production, repetitive work. From .0078 to .5020 automated system is for one or multiple However, they are also good for small Okuma machining centers. It offers ex- shops because they can use them for short SUPERB SURFACE FINISHES! Call or e-mail for catalog today! Toll Free: 800-665-6734 ● Fax: 866-308-7471 [email protected] ● www.magaforusa.com IMPROVED performance ● FEWER tool changes ● LONGER tool life WE KNOW MEDICAL Kitamura Machiney of USA World's Finest Rotary Kitamura’s HX400i FTGA 8APC system is an HMC with an eight-pallet system. Orthopedic, Dental, Aerospace, Automotive Keyway, hex, spline, hexalobe, CNC push and strip broaching tools Custom broaching solutions Call or e-mail for catalog today! Toll Free: 800-247-2024 ● Fax: 413-863-2714 [email protected] ● www.hassay-savage.com 74 | JUNE 2013 | CTE PartsHandling.indd 74 5/20/13 2:20 PM runs while changing the tooling for the job that just ran or is going to run. “The real strength of small shops is they can and will do a little bit of every- Rough Around thing, so if someone comes with a rush job and they do a great job, it can lead to other jobs,” Klaver said. “With auto- mated pallets, because all of your setups the Edges? are taken offline, you can fit that rush job and keep the machine running to make other parts. As the shop realizes the ben- efits, it starts to migrate more work into that cell to take advantage of the spindle utilization.” He added that eight to 10 pallets would be enough capacity for a small to medium-size shop starting with pallet au- tomation. “Most companies have a 1- to 2-hour cycle time on a HMC for a four- sided tombstone on a pallet, so if you load the system with 10 pallets, at even an average of 1 hour machining time per pallet, you would have 10 hours of unat- tended machining, which could be your unmanned third shift,” Klaver said. In general, a two-pallet system can run unat- tended for 3 hours, an eight-pallet system can run for 8 to 12 hours, and a 40-pallet system can run an entire weekend. For small shops with short runs, the real benefit to having more pallets is being able to leave complex jobs with long setup times permanently set up to run on de- mand rather than having to reset them for each run. contributors Fastems LLC (513) 779-4614 www.fastems.com Kitamura Machinery of USA Inc. (847) 520-7755 www.kitamura-machinery.com Okuma America Corp. Front and Back hole deBurring in a single pass (704) 588-7000 www.okuma.com E-Z Burr saves you time and money! Our long lasting patented tools deburr holes in tough materials in System 3R USA Inc. just seconds! Tools are available in all metric and (847) 439-4888 www.system3r.com fractional sizes from .040” through 2.0” and custom Easy. Fast. Built to Last deburring tools can be produced in 2 to 3 weeks. West Valley Precision Inc. www.ezburr.com View our complete list of products, sizes, specs and (408) 519-5959 800.783.2877 www.wvpi.com capabilities at ezburr.com. Plymouth, MI ctemag.com | 75 PartsHandling.indd 75 5/20/13 2:20 PM What’s on Your Pallet? (continued) “If you set the job up again, you have to make a new prove out and validate it,” Fastems’ Humphreys said. “Whereas if you have it set up and haven’t changed anything and have all the tools in the magazine, you can load the pallet and be confident that the first-off part will be a good part—the same as the last part from Okuma America the previous batch. When introducing Okuma’s MB-5000H HMC with a base Palletace C1000 10-pallet system. It is expandable to new work to the pallet system and while three MB-5000H machines and two additional C1000 extensions for a 30-pallet system. first-article inspection is happening, you can run another proven part while wait- Super Pallets “The automated system has a huge tool ing. When you get the green light that One smaller shop that is utilizing pallet library on it, so all of the tools you need the new first-off part is good to run, it is automation for unattended machining is to machine a setup pallet are on that ma- easy to release the part for production.” West Valley Precision Inc., San Jose, Calif. chine,” said Dane Madsen, WVPI presi- That is the challenge with a stand- The 35-man shop produces Invar, stain- dent. “Being able to use the same tool on alone machine—proving out parts. While less steel, aluminum and plastic parts for many different jobs is a function of your waiting for the first-article inspection, medical instruments. tool library. Every time that job comes up, typically the machine is just sitting there, WVPI has about 20 machine tools, you just pull that program and it will grab Humphreys added. including a Kitamura HX500i horizon- that pallet with the material on it just like And that is where shops can use a less- tal machining center with 150-tool ca- it was the next part on the machine, even skilled operator. “All the operator has to pacity and eight pallets, which it has had a couple of months later.” do is load and unload the parts in the pal- for about 3 years, and a Kitamura Super- As for unattended machining, the let.
Details
-
File Typepdf
-
Upload Time-
-
Content LanguagesEnglish
-
Upload UserAnonymous/Not logged-in
-
File Pages7 Page
-
File Size-