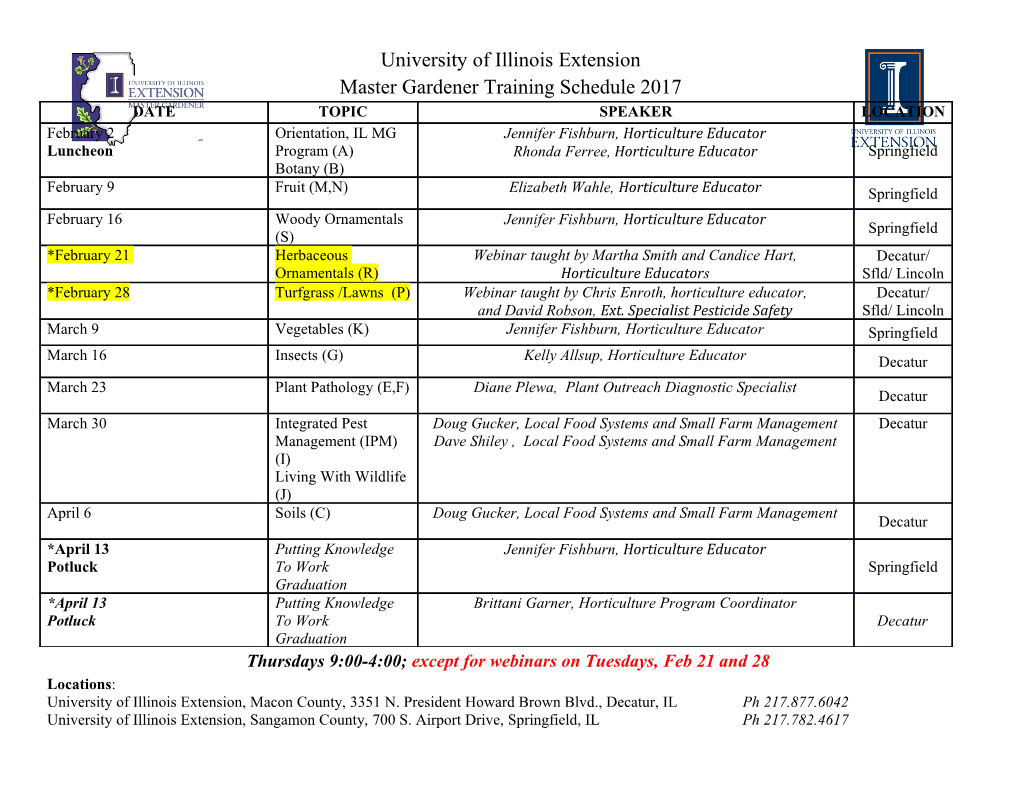
US 20140371494A1 (19) United States (12) Patent Application Publication (10) Pub. No.: US 2014/0371494 A1 Tirtowidjojo et al. (43) Pub. Date: Dec. 18, 2014 (54) PROCESS FOR THE PRODUCTION OF Related U.S. Application Data CHLORINATED PROPANES AND PROPENES (60) Provisional application No. 61/570,028, filed on Dec. 13, 2011, provisional application No. 61/583,799, (71) Applicant: DOW GLOBAL TECHNOLOGIES filed on Jan. 6, 2012. LLC, Midland, MI (US) Publication Classification (72) Inventors: Max Markus Tirtowidjojo, Lake Jackson, TX (US); Matthew Lee (51) Int. C. Grandbois, Midland, MI (US); William C07C 17/013 (2006.01) J. Kruper, JR., Sanford, MI (US); C07C 17/23 (2006.01) Edward M. Calverley, Midland, MI (52) U.S. C. (US); David Stephen Laitar, Midland, CPC ............... C07C 17/013 (2013.01); C07C 17/23 MI (US); Kurt Frederick Hirksekorn, (2013.01) Midland, MI (US) USPC ........... 570/230; 570/261; 570/101: 570/254; 570/234; 570/235 (21) Appl. No.: 14/365,143 (57) ABSTRACT (22) PCT Filed: Dec. 12, 2012 Processes for the production of chlorinated propanes and propenes are provided. The present processes comprise cata (86) PCT NO.: PCT/US12A69230 lyzing at least one chlorination step with one or more regios S371 (c)(1), elective catalysts that provide a regioselectivity to one chlo (2), (4) Date: Jun. 13, 2014 ropropane of at least 5:1 relative to other chloropropanes. US 2014/0371494 A1 Dec. 18, 2014 PROCESS FOR THE PRODUCTION OF made use of catalyst systems and/or initiators that are recov CHLORINATED PROPANES AND PROPENES erable or otherwise reusable, or were capable of the addition of multiple chlorine atoms per reaction pass as compared to FIELD conventional processes. Further advantages would be pro 0001. The present invention relates to processes for the vided if lower cost and/or more widely available starting production of chlorinated propanes and/or propenes. The pro materials could be utilized. cesses are capable of providing useful intermediates with enhanced regioselectivity, while also producing undesirable BRIEF DESCRIPTION byproducts at lower concentrations, than conventional pro 0008. The present invention provides efficient processes CCSSCS. for the production of chlorinated propanes and/or propenes. Advantageously, the processes make use of 1,2-dichloropro BACKGROUND pane, a by-product in the production of chlorohydrin, as a low cost starting material. And, at least one chlorination step of 0002 Hydrofluorocarbon (HFC) products are widely uti the process is conducted with a catalyst that provides a regi lized in many applications, including refrigeration, air con oselectivity of at least 5:1 to one chloropropane intermediate. ditioning, foam expansion, and as propellants for aerosol In Some embodiments, multiple chlorine atoms may be added products including medical aerosol devices. Although HFCs per pass, while in others, the catalyst may be recoverable and have proven to be more climate friendly than the chlorofluo reusable after the process. In some embodiments, further rocarbon and hydrochlorofluorocarbon products that they advantages may be provided by conducting one or more replaced, it has now been discovered that they exhibit an dehydrochlorinations catalytically, rather than with caustic. appreciable global warming potential (GWP). Less waste water is thus produced, and anhydrous HCl may 0003. The search for more acceptable alternatives to cur be produced. Further cost savings are provided in that low rent fluorocarbon products has led to the emergence of intensity process conditions, e.g., low temperatures, low pres hydrofluoroolefin (HFO) products. Relative to their predeces Sure and liquid phase reactions, are utilized. Finally, multiple sors. HFOs are expected to exert less impact on the atmo chlorinations, involving multiple catalysts, may be conducted sphere in the form their lower GWP. Advantageously, HFOs in the same reactor, providing capital and operating cost also exhibit low flammability and low toxicity. savings. 0004 As the environmental, and thus, economic impor 0009. In one aspect, the present invention provides a pro tance of HFOs has developed, so has the demand for precur cess for the production of chlorinated propanes and/or pro sors utilized in their production. Many desirable HFO com penes from a feedstream comprising 1,2-dichloropropane. At pounds, e.g., Such as 2.3.3.3-tetrafluoroprop-1-ene or 1.3.3. least one chlorination step of the process is conducted in the 3-tetrafluoroprop-1-ene, may typically be produced utilizing presence of a catalyst that provides a regioselectivity of at feedstocks of chlorocarbons, and in particular, highly chlori least 5:1, or at least 10:1, or at least 20:1, to one chloropropane nated propanes, e.g., tetra- and pentachloropropanes. intermediate. In some embodiments, the catalyst may com 0005. Unfortunately, these higher chlorides have proven prise a Lewis acid, a nonmetallic iodide, an inorganic iodine difficult to manufacture using acceptable process conditions salt, less than 10,000 ppm elemental iodine or combinations and in commercially acceptable regioselectivities and yields. of these. The source of chlorine atoms may comprise either For example, conventional processes for the production of chlorine gas, sulfuryl chloride or both. The chlorinated pro pentachloropropanes provide unacceptable selectivity to the pene may comprise from 3-4 chlorine atoms. desired pentachloropropane isomer(s), i.e., 1,1,2,2,3-pen tachloropropane, require the use of high intensity process DETAILED DESCRIPTION conditions and/or catalyst systems that are difficult to utilize in large scale production processes and/or that are not recov 0010. The present specification provides certain defini erable once used. Other conventional processes may be lim tions and methods to better define the present invention and to ited to the addition of a single chlorine atom per reaction pass, guide those of ordinary skill in the art in the practice of the and so must be repeated until the desired number of chlorine present invention. Provision, or lack of the provision, of a atoms has been added, with each additional step requiring definition for a particular term or phrase is not meant to imply additional capital, energy, and other cost investment. Still any particular importance, or lack thereof. Rather, and unless others require starting materials that are either cost prohibi otherwise noted, terms are to be understood according to tive, have limited availability or both. conventional usage by those of ordinary skill in the relevant 0006 Further, the dehydrochlorination steps required to art create alkenes from a feedstream comprising alkanes conven 0011. The terms “first', 'second’, and the like, as used tionally are conducted with the use of caustic, resulting in herein do not denote any order, quantity, or importance, but large quantities of waste water including low value by-prod rather are used to distinguish one element from another. Also, ucts Such as Sodium chloride. Conventional processes rely on the terms “a” and “an do not denote a limitation of quantity, many such dehydrochlorination steps, thus multiplying the but rather denote the presence of at least one of the referenced amount of waste water that must be treated prior to disposal. item, and the terms “front”, “back”, “bottom', and/or “top”, 0007. It would thus be desirable to provide improved pro unless otherwise noted, are merely used for convenience of cesses for the production of chlorocarbon precursors useful as description, and are not limited to any one position or spatial feedstocks in the synthesis of refrigerants and other commer orientation. cial products. More particularly, such processes would pro 0012. If ranges are disclosed, the endpoints of all ranges vide an improvement over the current state of the art if they directed to the same component or property are inclusive and provided a higher regioselectivity relative to conventional independently combinable (e.g., ranges of “up to 25 wt.%, or, methods, required low intensity process conditions, and/or more specifically, 5 wt.% to 20 wt.%, is inclusive of the US 2014/0371494 A1 Dec. 18, 2014 endpoints and all intermediate values of the ranges of “5 wt. and higher, and/or the use of vapor phase reactions. Such % to 25 wt.%.” etc.). As used herein, percent (%) conversion conditions may be undesirable not only because of the cost is meant to indicate change in molar or mass flow of reactant associated with the same, but also because they can result in in a reactor in ratio to the incoming flow, while percent (%) reactor fouling due to product decomposition. selectivity means the change in molar flow rate of product in 0019. In contrast, the present processes utilize tempera a reactorin ratio to the change of molar flow rate of a reactant. tures of less than 100° C. or less than 90° C., or less than 80° 0013 Reference throughout the specification to “one C., or less than 75°C., or less than 70° C., or even less than 65° embodiment' or “an embodiment’ means that a particular C., or 60°C. Ambient pressures or pressures of at least 100 psi feature, structure, or characteristic described in connection greater than ambient may be utilized. And, one or more reac with an embodiment is included in at least one embodiment. tions may be conducted in the liquid phase, so that evapora Thus, the appearance of the phrases “in one embodiment” or tion of the reactants is not required, and thus reactor fouling “in an embodiment' in various places throughout the speci may be minimized fication is not necessarily referring to the same embodiment. 0020. In some embodiments, a Lewis acid catalyst may be Further, the particular features, structures or characteristics utilized to provide the desired regioselectivity to the chloro may be combined in any suitable manner in one or more propane intermediate. In Such embodiments, the Lewis acid embodiments. catalyst may be utilized alone, and yet provide the desired 0014.
Details
-
File Typepdf
-
Upload Time-
-
Content LanguagesEnglish
-
Upload UserAnonymous/Not logged-in
-
File Pages7 Page
-
File Size-