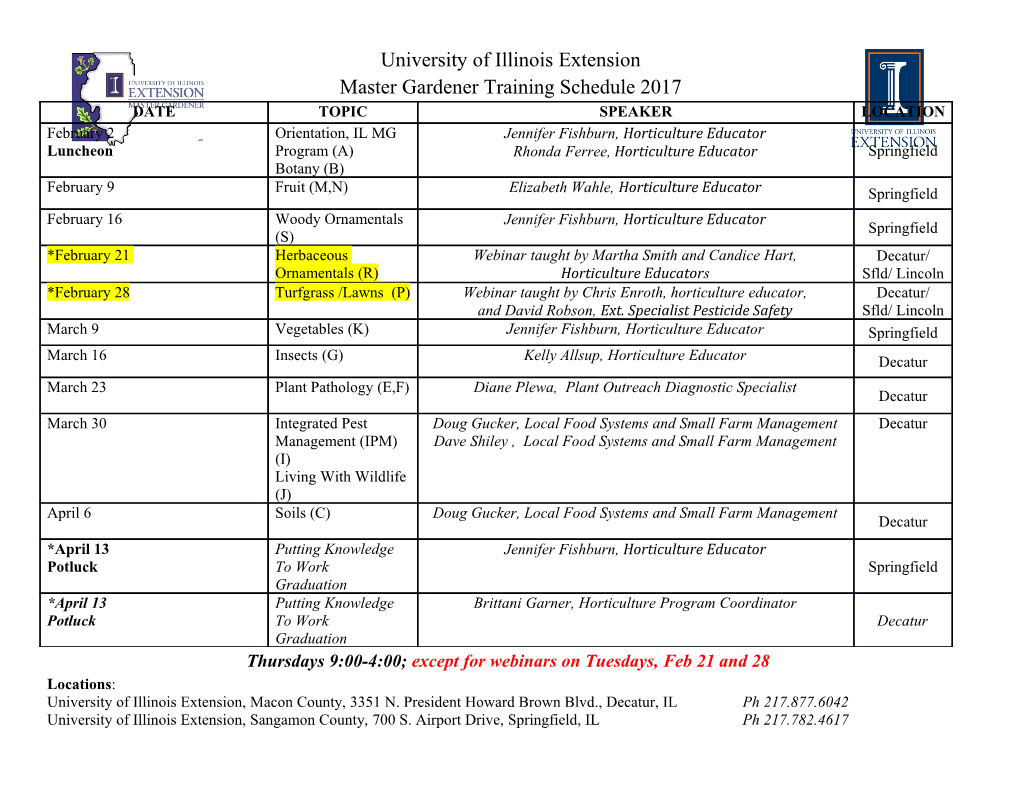
JOURNAL OF PROPULSION AND POWER Vol.17,No.5, September –October2001 Optimum FanPressure Ratio for Bypass Engines with Separate or Mixed Exhaust Streams AbhijitGuha ¤ Universityof Bristol,Bristol, England BS8 1TR, United Kingdom The optimumfan pressure ratiois determinedboth numerically and analytically for separate-stream as well as mixed-streambypass engines. The results are applicableto civil and military engines. The optimumfan pressure ratiois shownto be predominantlya functionof the specic thrustand a weakfunction of the bypassratio. Two simple,explicit equations, one for each type of engine, have been derivedthat specify the optimumfan pressure ratio.The predictionscompare very well againstnumerical optimization performed by a specialistcomputer packageemploying iterative and advanced search techniquesand real gasproperties. The analyticalrelations accelerate the optimizationprocess andoffer physicalinsight. It hasbeen shownthat the optimumfan pressure ratioachieves the condition V /V = ´ ina separate-streamengine and the condition V /V ´ in a mixed- jc jh KE 163 63 ¼ KE streamengine. The condition V163/V63 ´KE applieseven under situations when signi cant departures fromthe normallyassumed condition p /p ¼ 1 can occur. 016 06 ¼ Nomenclature pressor) pressureratio in bypassengines. Separate analysis has been B =bypassratio presentedfor the mixed-stream and separate-stream engines be- c p =specic heatof air at constant pressure causethe owphysics is different in thetwo cases. In bothcases, c pg =specic heatof combustion products at thepresent theory gives results in good agreement with numerical constantpressure optimizationcalculations. ( ) Ek =kineticenergy added by the core engine Determinationof theoptimum fan pressure ratio FPRop is im- FN = net thrust portantbecause, given all other variables such as theoverallpressure F ratio (OPR),bypassratio B,andturbine entry temperature T04 the ON =specic thrust M =Machnumber of the aircraft optimumvalue of FPR simultaneouslyensures maximum speci c m =mass owrate through the bypass duct (cold ow) thrustand minimum speci c fuelconsumption. Thus, the FPR op P c m f =mass owrate of fuel achievesthe two, usually contradictory, goals of jetengine design. mP =mass owrate through the core engine (hot ow) Forcivil engines, particularly for medium to long range aircrafts, P h p =staticpressure the FPRop canbe calculated under cruise conditions. For military p0 =totalpressure engines,optimization may be mission speci c. However,Millhouse R =specic gasconstant of air et al.1 haveshown that, although the most fuel-ef cient values of T =statictemperature suchparameters as bypass ratio and OPR dependon theintegrated Ta =temperatureof ambientair effectsof thevarious ightaltitudes, Mach numbers, and thrust re- T0 =totaltemperature quiredthroughout the mission, it is possible to locateheuristically V = velocity themost ef cient FPR tocomplementother engine parameters in- Va =forwardspeed of theaircraft dependentof themission. Thus, the relations derived in thispaper canbe usedin the design of bothcivil and military engines. V j =jetspeed in a mixedstream engine V j c =fullyexpanded jet speed of the cold bypass stream Thedesign wisdom is that only a single-stagefan is usedfor a civilaircraft engine with large bypass ratios, and so themaximum V j h =fullyexpanded jet speed of the hot core stream Vm =meanjet speed [given by Eq. (8)] FPR isabout 1.8. Engines with low bypass ratios, for example, mil- ° =isentropicindex of air itaryengines, normally use a low-pressure (LP) compressorhaving – °g =isentropicindex of combustionproducts 3 5stages.In this case, the maximum possible FPR canbe much higher.The mixing of the two streams in a mixed-streamturbofan ´ f =isentropicef ciency of thefan or low pressurecompressor engineoffers performance gain (lowerspeci c fuelconsumption andhigher speci c thrust ),eventhough mixing incurs a lossin total ´KE =efciency of energy transfer between the core andbypass ow pressurebecause the enthalpies of the two streams are redistributed. Moreover,only one reheat system and only one variable nozzle ´LPT =isentropicef ciency of thelow pressure turbine ´NB =isentropicef ciency of thebypass nozzle areneeded. A longnacelle can contain the fan/ compressornoise moreeffectively. For the same speci c thrust,the mixed-stream en- Subscript ginehas lower optimum FPR thana separate-streamengine; thus, theLP turbinemay have one fewer stage if bothengines have the op= optimumvalue samebypass ratio. The outer cold stream also protects the jet pipe Introduction fromsevere temperatures resulting from afterburning. Low-speci c- thrust,high-bypass-ratio engines, on the other hand, do notemploy Nthispaper simple, explicit relations have been derived from afterburning,and mixingof thetwo streams would necessitate a long I fundamentalprinciples for determining the optimum fan (com- nacelleincreasing weight, cost, nacelle drag, and interference ef- fects.These engines, therefore, use separate-stream con gurations. Received 30May 2000; revision received 20February 2001; accepted Whena commonnozzle is, however, used for high-bypass-ratio en- forpublication 29 May 2001. Copyright c 2001by Abhijit Guha. Pub- lishedby theAmerican Instituteof Aeronautics ° and Astronautics, Inc., with gines,the small axial extent of themixing zone is usually insuf cient permission. toachievecomplete mixing of thetwostreams. ¤ Lecturer, Aerospace EngineeringDepartment, UniversityWalk; Calculationand analysis of theperformance of turbofanengines [email protected]. arediscussed in detailsin several excellent texts. 2 4 Incomparison, 1117 1118 GUHA theissue of optimized design has received less attention, and an- alyticalsolutions did not exist. The real store house of expertise andknowledgeobviously exists with the aeroengine manufacturers whohave actively pursued the optimization of gasturbine perfor- mancefor the past 60 years. Ruf es 5 showsthat there has been a 50%improvement in the speci c fuelconsumption (SFC) of the bareengine, as theengines evolved from the turbojet of 1958 to the Turbojet high-bypassTrent engines of moderntime. Improvements in propul- siveef ciency, component ef ciency and cycle ef ciency contribute approximatelyone-third each to thisgain in performance. The pub- licationsmade by experts from industry (e.g.,Jackson, 6 Bennett,7 Wilde,8 and Birch9 ) containa wealthof experience, information, andcalculation results. However, the details of calculation method arenot known to the readers. The industry would typically have its own,sophisticated computer packages to whichthe public does not haveaccess. Moreover, the published results often would involve an adoptedfamily of enginedesigns. It is then not always obvious to thegeneral reader how to generalize the results or howto proceed onaclean-sheetanalysis. Separate-streambypass engine Inthis paper analytical relations have been derived for calculating FPR .Theanalytical results not only accelerate the optimization Fig.1 Schematicdescription of a separate-streamturbofan engine op andan equivalent turbojet engine used for analysis; energy is the same processbut also offer valuable physical insight. It is shown that at point inboth engines. the FPRop ispredominantly a functionof the speci c thrustand ­­ onlyweakly depends on the bypass ratio. The FPR op monotoni- callyincreases with increasing speci c thrustat two different levels ticularvalue of fuel consumption rate, a jetwith speed V j;ref in the correspondingto the separate-stream and mixed-stream turbofan absenceof anybypass ow.Thekinetic energy added by the gas engines. generatoris then,neglecting the fuel mass owrate which is usu- Thetheory has been veri ed bycomparingits predictions with allya verysmall proportion of theair mass owrate in a jetengine, calculationsperformed by thecomputer program GasTurb, 10 which equal to isageneralpurpose commercial package for the calculation of de- E 1 m V 2 V 2 (1) signand off-design performance of varioustypes of gas turbine en- k D 2 P h j;ref a gines,turbojet, turboshaft, separate- or mixed-stream turbofan, and Inthebypass engine, the whole ¡of thiskinetic ¢ energy is, of course, gearedturbofan, all with single- or twin-spoolcon gurations. It uses notpresentin the core jet. The LP turbineextracts a portionof this realgas properties with dissociation and has several features includ- energyand turns the fan, which, in turn,adds kinetic energy to the ingoptimization, iteration, transient, and Monte Carlo simulation. bypass ow.Theef ciency ´KE ofthisenergy transfer between the Eachnumerical point subsequently illustrated has been calculated coreand bypass owdepends on the component ef ciencies of byGasTurbby alengthyoptimization process that uses advanced theLP turbine,the fan, and the bypass nozzle and also on the ow searchtechniques to ndtheoptimum FPR thatminimizes the SFC lossesin theducts and mechanicalef ciency of theshafts. Assuming while,at each trial, the primary variables are iterated to give the themechanical ef ciency is close to 1, prescribedspeci c thrust.This numerical optimization is used not onlyto verify the theoretical prediction, but also to discover what ´ ´ ´ ´ (2) KE ¼ LPT f NB exactlyhappens to the many variables when the FPR op isachieved. 4;9 Basedon the principles discussed in the present paper, a new At thecurrent level of technologies, ´LPT 0:9, ´ f 0:9, and ¼ ¼ methodologyfor the thermodynamic optimization of bypassengines ´NB 1. Equation (2),therefore,suggests that ´KE 0:8. ¼ ¼ (turbofanor advanced propulsors
Details
-
File Typepdf
-
Upload Time-
-
Content LanguagesEnglish
-
Upload UserAnonymous/Not logged-in
-
File Pages6 Page
-
File Size-