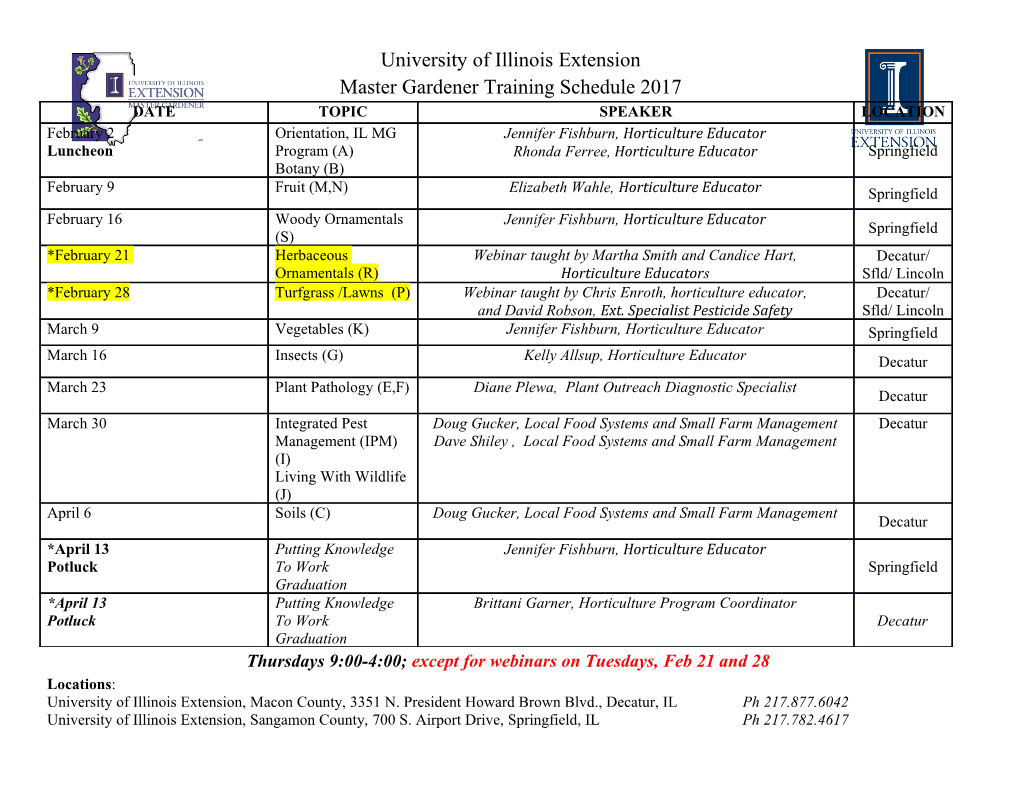
! XJ9900001 OBbEflMHEHHbM MHCTMTYT flflEPHbIX MCCJlEflOBAHMM flyoHa D13-98-146 V.F.Boreiko, V.M.Bystritsky, V.I.Datskov, A.N.Fedorov, V.N.Pavlov, V.A.Stolupin, A.Del Rosso1, R.Jacot-Guillarmod1, F.Mulhauser1, L.A.Rivkis2 NEW TARGET CRYOSTAT FOR EXPERIMENTS WITH NEGATIVE MUONS Submitted to «Nuclear Instruments and Methods* 'institute of Physics, University of Fribourg, Switzerland 2A.A.Bochvar All-Russia Research Institute of Inorganic Materials, Moscow, Russia 30-07 1998 Introduction The study of processes yielding charge nonsymmetric muonic molecules like pxZ (z = p,d,t and Z = He, Li, Be) and nuclear fusion started about fifteen years ago. Theoretical and experimental interest have increased these past five years [1-13]. Due to some experimental difficulties, the muon catalyzed fusion (pCF ) is essentially measured in deuterium-helium mixtures. The nuclear fusion from the charge nonsymmetric molecule pd 3He may occur via two different channels, pd3He -4 a + p(14.7 MeV) + p (1) -4 psLi +7(16.4 MeV), (2) whereas the pd4He molecule fuses via a single channel pd*He -4 p6U + 7(1.48 MeV). (3) The proposed apparatus should be able to easily detect those fusion products. In addition, the 6.85 keV soft X rays resulting form the decay of the pd4He and pd3He molecules should be measured, as well as the muon decay electrons. The detection of so many different types of particles, with totally different paths in matter, is a non-trivial constraint in the design of the apparatus. The different processes which occur when a muon enters a deuterium-helium mix­ ture are strongly dependent on the mixture density. Hence, the gas mixture pressure and temperature are essential parameters. A special temperature control system is required to keep them as stable as possible. In addition, the level of impurities (N2, 0a, H20 and C02) in the deuterium-helium mixture has to be very low, to avoid competing processes. The total amount of impurities should not exceed 500 ppb. A gas filling system has been constructed to allow such a purity. The study of pCF in a deuterium-helium mixture requires an integrated set of devices (target, gas supply, detectors and temperature control system) that provide the optimal conditions [12]: a pressure range of 0-10 atm and a temperature range of 21-300 K. The set-up presented in this paper was tested at the Paul Scherrer Institute (PSI), Switzerland, during a two weeks measurement. Pure deuterium and a mixture of deuterium-helium at pressures of 5.6-6.4 atm were used at a temperature of about 32 K. The cryostat Experimental studies of muon catalyzed fusion in deuterium-helium mixtures re­ quire some special cryogenics and vacuum design for the development of the target. Figure 1 shows a general view of the cryostat. The cryogenic gas target (1) is enclosed inside a vacuum chamber (2) made of 2 mm thick stainless steel. The target body is made of the aluminium alloy ADI (Al> 99.3%, Fe< 0.3%, Si< 0.3%, 1 Cu< 0.05%, Mn< 0.025%, Zn< 0.1%, Ti< 0.05%, Mg< 0.05%). It is a sphere of internal diameter of 66 mm, which gives a volume of % 250 cm3. The use of this aluminium alloy is important to suppress almost completely background from characteristic X rays. Aluminium X-ray energies substantially differ from the energy of the 6.85 keV line, whereas stainless steel X rays have an energy very close to this line. There are 5 Kapton windows around the target (1). The choice of window diam­ eters is due to the size of the detectors located behind them. The window thickness was chosen after several tests with varying gas pressure and temperature. A high pressure in the target allows a good stopping rate of the incident muons and high experimental rates. Construction constraints have lead to a maximum pressure of the deuterium-helium mixture below 10 atm at a temperature of about 32 K. The muon beam entrance window has a 40 mm diameter and is 135 pm thick. The four re­ maining windows are in the planes perpendicular to the muon beam. Three windows. 45 mm diameter and 135 pm thick, have been designed to install the Si detectors (4) in order to measure the 14.7 MeV protons. The last window, 15 mm diameter and 55 pm thick, was set-up to install a Ge detector (Ge) to measure the 6.85 keV X rays. With the above mentioned dimensions a gas pressure of 13 atm was reachable at a temperature of 77 K. The diffusion of deuterium or helium through the windows is negligible. So, no corrections for the target density variations are necessary during the measurements. The Kapton windows are sealed with indium gaskets and stainless Steel flanges (3). The silicon detectors (4) (diameter 42 mm, thickness 4 mm), which record the. fusion protons, are attached to the target body immediately behind the Kapton win­ dows. Air-tight connectors are provided in the vacuum chamber wall for high voltage power supply of the Si detectors and read-out of their signals. The temperature of Si detectors will never be lower than 40 K [14]. Below this temperature the output signal for a given energy decreases by about a factor five compared to the same energy for temperatures above 40 K. To decrease the heat flow to the target due to the thermal radiation of the vacuum chamber walls, a thermal shield (5) has been installed inside the chamber. The shield is made of copper with a thickness of 1 mm. Behind the Si detectors the shield (6) is made of 0.3 mm aluminium. The shield on the muon beam path and in front of the Ge detector, is made of 12 pm thick Mylar with 1 pm A1 coating. The vacuum chamber (2) has two Kapton windows: one along the muon beam axis (40 mm diameter, 55 pm thick) and the second in the direction of the Ge detector (20 mm diameter, 25 pm thick). These windows are glued with epoxy and scaled with stainless steel flanges. In addition, 0.5 mm thick aluminium windows (6) are placed in the vacuum chamber walls in front of the outer detectors. These windows are sealed with flanges and viton gaskets. The external detectors are plastic scintillators for the detection of the muon decay electrons as well as neutron detectors, BGO, and Ge detectors. 2 The target is filled with deuterium, helium, or their mixture through a small stainless steel tube (7). The target is cooled by liquid helium (for a temperature range between 21-70 K) or liquid nitrogen (70-300 K), flowing through the target heat exchanger (8). A second heat exchanger (9) is placed on the mounting flange (10), to cool the shield and thus, the different parts of the cryostat are cooled by the same coolant flow. Coolant is evacuated by a vacuum pump of throughput 20 1/s. The temperature control system A temperature monitoring and control system was implemented to regulate the target, the thermal shield and the Si detectors. The regulation is based on the com­ pensation method. The target temperature is periodically measured and compared with the preset value. If any noticeable difference is detected, the target heating power increases or decreases depending on the variation of the temperature. The temperature is measured by calibrated carbon TVO thermometers [15], mounted di­ rectly on the different devices. To increase the measurement accuracy, the current and voltage leads of all thermometers have thermal anchors, which are glued1 to the appropriate points. The thermometers were calibrated with a special tester in the temperature range 4-300 K by the method described in Ref. [15]. The calibration accuracy is ±0.02 K in the temperature range 4-70 K and ±0.1 K in the range 70-300 K. At our coolant evacuation rate, the target temperature is regulated by an electric heater made of 0.15 mm diameter constantan. The contact between the heater and the target is ensured by the use of the thermally conducting glued1. The heater resistance is 92 ft at a temperature of 32 K. Figure 2 shows the diagram of the thermal stabilization of the system. The tem­ perature read-out information, i.e., the voltage at the sensor (TS), is fed into the PC through a CAMAC crate. The temperature corresponding to a given sensor voltage results from the following series expansion: T = fC ± 7G x (1000/A) ± ... ± #7 % (1000/R)* ± ..., (4) where K, are the polynomial coefficients found from the calibration of the thermome­ ter and R is the thermometer resistance at that temperature. When the target tem­ perature is above or below the preset level, the target heating power changes by increasing or decreasing the voltage at the heater (H), using a digital-to-analog con­ verter (DAC). The measuring system works via a four cycles process. The first cycle activates the shield sensor (SS) and measures the voltage. The second and third cycles operate the same way on the target (TS) and detector (DS) thermometers. The fourth cycle measures the target pressure gauge (PG) voltage. Therefore the target pressure and temperature are obtained and determine correctly the experimental conditions during 1 Sty cast 1266 3 the measurement. The multiplexer (M) has several other input possibilities which are used to measure the pressure at different locations in the gas supply system, e.g., in the deuterium-helium mixing volume (MV). The multiplexer (M), the stabilized power supply (not shown in Fig. 2), and the amplifier (A) are located directly on the cryostat external wall, in one single unit.
Details
-
File Typepdf
-
Upload Time-
-
Content LanguagesEnglish
-
Upload UserAnonymous/Not logged-in
-
File Pages15 Page
-
File Size-