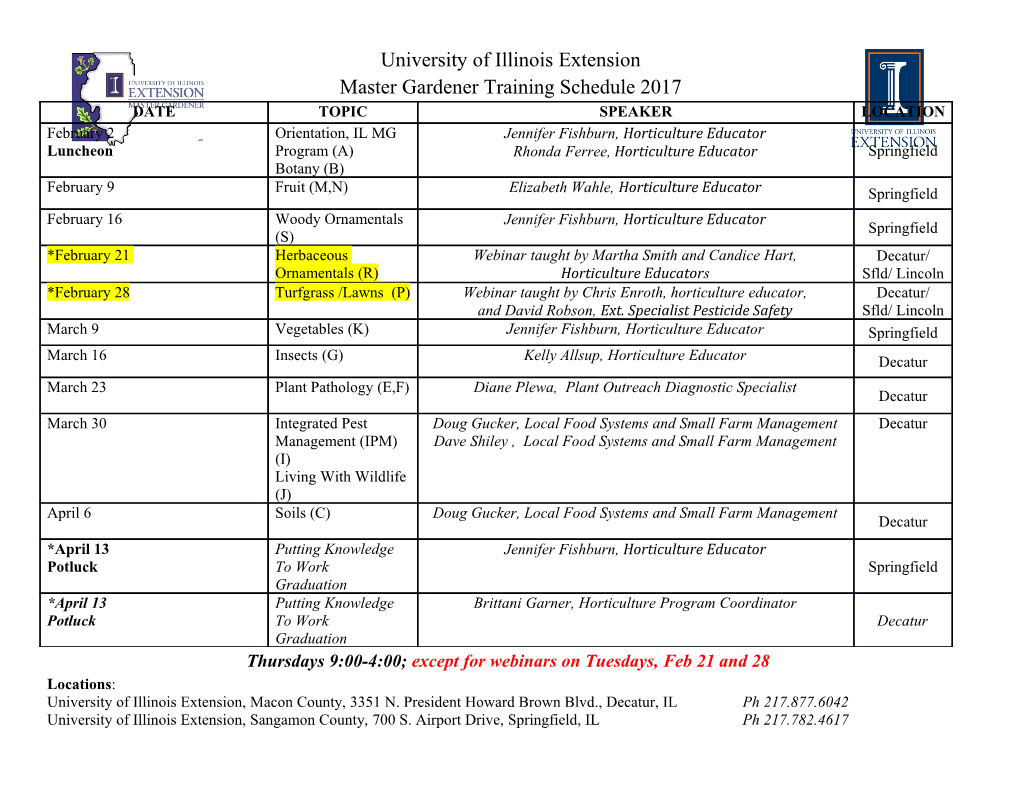
9. Electron Beam Welding 2003 9. Electron Beam Welding 115 The application of highly accelerated electrons as a tool for material processing in the fusion, drilling and welding process and also for surface treatment has high voltage supply been known since the Fifties. Ever n cathode o i t a r control elektrode since, the electron beam welding e n e g anode m process has been developed from the a e b adjustment coil laboratory stage for particular applica- e c n valve to vacuum pump a d i tions. In this cases, this materials u g d viewing optics n stigmator a could not have been joined by any g n i focussing coil m r o f defelction coil industrially applied high-production m a e b joining method. r e The electron beam welding machine b m workpiece a h c workpiece is made up of three main compo- g to vacuum pump n i handling k r o w nents: beam generation, beam manipulation chamber door br-er9-01e.cdr © ISF 2002 and forming and working chamber. Schematic Representation of an These components may also have Electron Beam Welding Machine separate vacuum systems, Figure 9.1. Figure 9.1 A tungsten cathode which has been power supply evacuation heated under vacuum emits electrons chamber evacuation system for gun system control cabinet EB-gun by thermal emission. The heating of valve the tungsten cathode may be carried out directly - by filament current - or indirectly - as, for example, by coiled filaments. The electrons are acceler- ated by high voltage between the cathode and the pierced anode. A modulating electrode, the so-called workpiece working chamber receiving platform workpiece handling “Wehnelt cylinder”, which is positioned control panel between anode and cathode, regu- control desk lates the electron flow. Dependent on br-er9-02e_f.cdr © ISF 2002 the height of the cut-off voltage be- All-Purpose EBW Machine and Equipment Figure 9.2 9. Electron Beam Welding 116 tween the cathode and the modulating electrode, is a barrier field which may pass only a certain quantity of electrons. This happens during an electron excess in front of the cathode where it culminates in form of an electron cloud. Due to its particular shape which can be compared to a concave mirror as used in light optic, the Wehnelt cylinder also effects, besides the beam current adjustment, the electrostatic focus- sing of the electron beam. The electron beam which diverges after having passed the pierced anode, however, obtains the power density which is necessary for welding only after having passed the adjacent alignment and focussing system. One or sev- eral electromagnetic focussing lenses bundle the beam onto the workpiece inside the vacuum chamber. A deflection coil assists in maintaining the electron beam oscillat- ing motion. An additional stigmator coil may help to correct aberrations of the lenses. A viewing optic or a video system allows the exact positioning of the electron beam onto the weld groove. The core piece of the electron beam welding machine is the electron beam gun where the electron beam is generated under high vacuum. The tightly focussed elec- tron beam diverges rapidly under atmospheric pressure caused by scattering and ionisation development with air. As it would, here, loose power density and efficiency, the welding process is, as a rule, carried out under medium or high vacuum. The necessary vacuum is generated in separate vacuum pumps for working chamber and beam gun. A shut-off valve which is positioned between electron gun and working chamber serves to maintain the gun vacuum while the working chamber is flooded. In universal machines, Figure 9.2, the back-scattered electrons x-ray workpiece manipu- thermal radiation lator assembly in- secondary electrons side the vacuum chamber is a slide x convection with working table positioned over NC- controlled stepper y heat conduction motors. For work- z br-er9-03e.cdr © ISF 2002 piece removal, the Energy Transformation Inside Workpiece slide is moved from Figure 9.3 9. Electron Beam Welding 117 the vacuum chamber onto the workpiece platform. A distinction is made between electron beam machines with vertical and horizontal beam manipulation systems. The energy conversion in the workpiece, which is schematically shown in Figure 9.3, indicates that the kinetic energy of the highly accelerated electrons is, at the opera- tional point, not only converted into the heat necessary for welding, but is also re- leased by heat radiation and heat dissipation. Furthermore, a part of the incident electrons (primary electrons) is subject to backscatter and by secondary processes the secondary electrons are emitted from the workpiece thus generating X-rays. The impact of the electrons, which are tightly focussed into a corpuscular beam, onto the workpiece surface stops the electrons; their penetration depth into the workpiece is very low, just a few µm. Most of the kinetic energy is released in the form of heat. The high energy density at the impact point causes the metal to evaporate thus allowing the following electrons a deeper penetration. This finally leads to a metal vpourapour cavity cavity which which is is surrounded by a shell of fluid metal, covering the entire weld surrounded by a shell of fluid metal, covering the entire weld depth, Figure 9.4. This deep-weld effect allows nowa- days penetration depths into steel a) b) c) d) materials of up to br-er9-04e.cdr © ISF 2002 300 mm, when Principle of Deep Penetration Welding modern high vac- uum-high voltage Figure 9.4 machines are used. The diameter of the cavity corresponds approximately with the beam diameter. By a relative motion in the direction of the weld groove between workpiece and electron beam the cavity penetrates through the material, Figure 9.5. At the front side of the cavity new material is molten which, to some extent, evaporates, but for the most part 9. Electron Beam Welding 118 flows around the cavity and rapidly solidifies at the backside. In order to maintain the welding cavity open, the vapour pressure must press the molten metal round the va- pour column against the cavity walls, by counteracting its hydrostatic pressure and the surface tension. However, this equilibrium of forces is unstable. The transient pressure and tempera- ture conditions inside the cavity as well as their respective, momentary diameters are subject to dynamic changes. Under the influence of the resulting, dynamically chang- ing geometry of the vapour cavity and motion of the molten metal electron beam with an unfavour- groove groove front side keyhole able selection of melting pool vapour capillary molten the welding pa- welding direction zone rameters, metal F1 fume bubbles may F solidified 2 be included which zone F 3 on cooling turn into F1 F1 : force resulting from vapour pressure F2 : force resulting from surface tension shrinkholes, Figure F3 : force resulting from hydrostatic pressure 9.6. br-er9-05e.cdr © ISF 2002 Condition in Capillary The unstable pres- sure exposes the Figure 9.5 molten backside of the vapour cavity to strong and irregular changes in shape (case II). Pressure variations interfere with the regular b I II III flow at the cavity backside, act upon workpiece movement the molten metal and, in the most br-er9-06e.cdr © ISF 2002 Model of Shrinkage Cavity Formation unfavourable case, press the unevenly Figure 9.6 9. Electron Beam Welding 119 distributed molten groove end crater upper bead metal into different t n e m zones of the mol- ea m f s e h o c t m r ng ea ten cavity back- o le s f of n h i width of seam gt e n r le side, thus forming d l n s e o s i e t e d w h l d k t a n l the so-called va- e r c k p t i e w c blind bead i e e d w h t d t n t h e n a pour pockets. The p e N m molten area e c cavities are not r o f unapproachable gap n i e always filling with r lower bead root weld t o o r molten metal, they br-er9-07e.cdr © ISF 2002 collapse sporadi- Basic Definitions cally and remain as Figure 9.7 hollow spaces after solidification (case Ill). The angle ß (case I) increases with the rising weld speed and this is defined as a turbulent process. Flaws such as a constantly open vapour cavity and subsequent continuous weld solidification could be avoided by selection of job- suitable welding parameter combina- tion and in particular of beam oscilla- tion characteristics, it has to be seen to a constantly of the molten metal, in by accelerating voltage: l high voltage machine (U=150 kV) order to avoid the above-mentioned B l low voltage machine (UB=60 kV) defects. Customary beam oscillation types are: circular, sine, double parab- by pressure: ola or triangular functions. l high vacuum machine l fine vacuum machine l atmospheric machine (NV-EB welding) Thick plate welding accentuates the process-specific advantage of the by machine concept: l conveyor machine deep-weld effect and, with that, the l clock system possibility to join in a single working l all-purpose EBW machine l local vacuum machine cycle with high weld speed and low l mobile vacuum machine l micro and fine welding machine heat input quantity. A comparison with br-er9-20e.cdr the submerged-arc and the gas metal- Classification of EBW Machines arc welding processes illustrates the depth-to-width ratio which is obtain- Figure 9.8 9.
Details
-
File Typepdf
-
Upload Time-
-
Content LanguagesEnglish
-
Upload UserAnonymous/Not logged-in
-
File Pages15 Page
-
File Size-