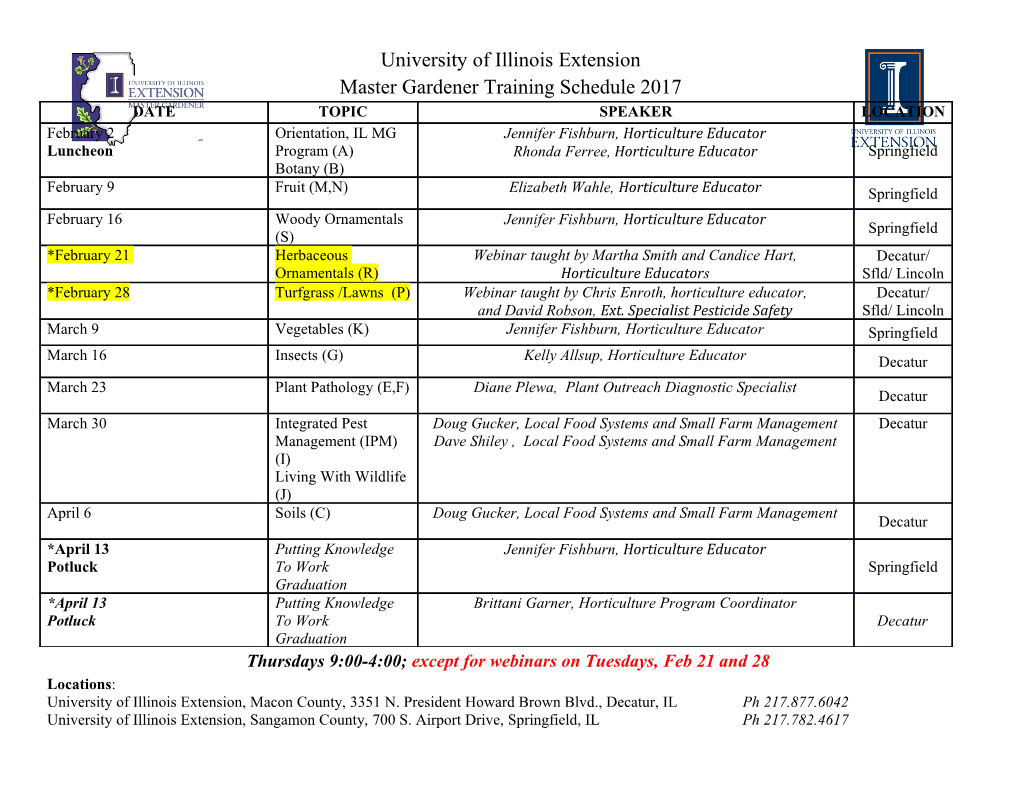
T. SICE Vol.E-2, No.1 (2002) Trans. of the Society of Instrument and Control Engineers [ Vol.E-2, No.1, 42/53 (2002) ] Suppression Control Method of Torque Vibration for Brushless DC Motor Utilizing Repetitive Control with Fourier Transform Satomi Hattori*, Muneaki Ishida** and Takamasa Hori*** Variable speed drive systems of brushless DC motor have been widely used for industry applications, home electric appliances, and so on, due to the progress of the power electronics, because of simple structure, easy maintenance, high efficiency, etc.. However, structural imperfectness of brushless DC motor and its control sys- tem produce torque ripple, and cause mechanical vibration by torque ripple and acoustic noise. In this paper, authors propose a suppression control method of vibration for brushless DC motor utilizing feed- forward compensation control, and a generation method of compensating signals for the feedforward control by repetitive control with Fourier transform utilizing a vibration signal acquired by an acceleration sensor attached to the motor frame. Because the vibration signals detected by the acceleration sensor contain various complicated frequency com- ponents due to motor torque vibrations and mechanical resonant vibrations around the motor load system, we can not stabilize the repetitive control system and reduce the vibration by directly using the vibration signals from sensor itself. So we propose a generation method of the compensating signals of the repetitive controller consid- ering the periodicity of motor torque ripples, and using Fourier transformer which can select particular frequency components. In order to realize on-line generation of feedforward compensating signals to reduce the vibration, auto-tuning method of the repetitive control parameters is also presented. An experimental system to detect and reduce the motor torque vibration is constructed, and the effectiveness of the proposed method is confirmed by experimental results. Key Words: Brushless DC motor, Torque ripple, Acceleration sensor, Repetitive control, Fourier transform 1. Introduction ever, structural imperfectness of brushless DC motor and its control system produce torque ripple, which causes Variable speed drive systems of brushless DC motors mechanical vibration and acoustic noise [1]-[3]. As the have been widely used for industry applications, home ripple torque suppression methods, the feedforward electric appliances, and so on, due to the progress of the compensation method of the compensation current esti- power electronics, because of simple structure, easy mated from the spatial harmonics of reluctance [4], the maintenance, high efficiency, etc.. Moreover, because method of using skewed rotor [5], [6] and so on are the brushless DC motor can realize the same high per- reported. formance as DC motor, it is used in the fields where the Also, it was well known that the torque ripple could high speed and high accuracy control is required. How- be reduced by addition of special feedforward compen- sation voltage/current to the usual voltage/current for the * Dept. of Electrical, Electronics and Information Engi- control input [4]. However, how do we obtain the feed- neering, Faculty of Science and Engineering, Shizuoka Institute of Science and Technology, 2200-2 Toyosa- forward compensation signals or data? Of course, we wa, Fukuroi, Shizuoka 437-8555, Japan can derive the compensation signals by analysis consid- ** Dept. of Electrical and Electronics Engineering, ering the structure of the motors, estimation from the Faculty of Engineering, Mie University, 1515 Kamiha- e.m.f. waveshape, etc. approximately, but cannot obtain ma-cho, Tsu, Mie 514-8507, Japan *** Dept. of Electronics and Information Engineering, the accurate signals. Finally for the individual motor, we Faculty of Engineering, Aichi University of Technolo- must make a fine adjustment of the compensation signal gy, 50-2 Manori, Nishihazama-cho, Gamagori, Aichi 443- in order to suppress the torque ripple sufficiently. 0047, Japan * Same to ** until March 2002 In earlier papers, from the viewpoint of direct reduc- *** Same to ** until March 2002 tion of the vibration of the motor frame caused by torque T. SICE Vol.E-2, No.1 (2002) ripple, we attached the acceleration sensor on the motor 2. Detection Method of Mechanical Vibration frame, and we have proposed some generation methods of compensating signals to reduce the torque ripple of 2.1 Detection System of Mechanical Vibration the brushless DC motor, 3-phase HB-type stepping motor and the induction motor by repetitive control. [7]- Fig.2 shows the detection system of the motor vibra- [10] (Fig.1). tion. This system is the usual case, where the motor base The purposes of this research is to construct the con- and the load base are separated each other. Here, the trol system utilizing the feedforward compensation sign- motor base is supported by vibration proof rubbers and als to reduce the torque ripple, and the generation the load (DC generator) base is fixed by bolts. method of compensating signals for the feedforward The ripple torque is caused by the imperfectness of control by repetitive control. Furthermore, in this paper, the motor, current sensors, driving source, etc. when the the auto-tuning method of the repetitive control parame- motor is rotating. The rotational speed of the brushless ters is considered for the reasons as shown below: DC motor is fluctuated due to the ripple torque. At the (1) Even when the characteristics of mechanical systems same time, the ripple torque is applied to the motor are not known clearly, the repetitive control must be frame by a reaction from the rotor and, as a result, the always performed stably. vibration of the motor frame occurs. Since the vibration (2) In the case of the operating point of the motor and is periodical in phase with the rotation of the motor, the the parameter of the controlled system change, on- repetitive control can be applied to the reduction of the line update of the compensation signal is necessary vibration. to reduce the vibration increased by those change. 2.2 Extraction of Specific Component of Vibration by In this paper, we propose a suppression control Fourier Transform method for torque vibration of brushless DC motors uti- lizing the acceleration sensor, the Fourier Transformer The periodical torque ripple occurs synchronously and the repetitive controller. In the proposed system, with the motor rotation. And also the repetitive con- only one frequency component of vibration signal from troller has large loop gain (basically infinity) only for the acceleration sensor is inputted to repetitive controller, fundamental repetitive frequency component and its har- the stability of the control system can be improved. monics. For the above reasons, the repetitive control sys- Approximate analysis is performed to study the stability tem is effective to reduce the vibration due to periodical of the repetitive control system. In order to realize on- torque ripples. line generation of feedforward compensation signals to However, because the vibration signals detected by reduce the vibration, auto-tuning method of the repeti- the acceleration sensor contain various frequency com- tive control parameters is also presented. An experimen- ponents and the mechanical system around the motor tal mechanical system to realize the mechanical vibra- and load has complicated resonant characteristics, we tion is constructed, and the effectiveness of the proposed can not stabilize the repetitive control system and reduce method is confirmed by experimental results. the vibration by directly using the vibration signals from sensor [8]. Then, we investigate the method which only Inverter Encoder Acceleration sensor one frequency component of the vibration signal is extracted from the vibration signals detected by the + SPMSM DCG acceleration sensor, and the repetitive control is per- formed for every frequency component of the vibration. Motor frame Generally, since the period of the vibration may not Fixed base coincide with that of the power supply but may be multi- PWM Fourier controller transformer ple of that, we set the period of the vibration to Tr (= Nr T, T = f -1, f : motor driving frequency). For example, in Torque command + - Compensating signal Repetitive controller the case of Nr =2, the frequency components of the vibration are 0.5f, 1.0f, 1.5f, ... and 0.5f is fundamental Fig.1 Schematic diagram of control system wave component of the vibration. If the vibration signal a S detected by the acceleration sensor is expressed as equation (1), the Fourier coefficients an, bn are given T. SICE Vol.E-2, No.1 (2002) equation (2) and (3), respectively, and a certain compon- 3. Configuration of Control System ent of the vibration a S nf (t) whose frequency is nf is given by equation (4), where, n = m / Nr (m=1, 2, 3, ...), Fig.4 shows a block diagram of the proposed system. w = 2pf. Therefore, we can extract the specific compon- Here, d axis coincides with a direction of the magnetic ent of the vibration from the vibration signal which con- flux produced by the field of SPMSM (Surface Perma- tains various frequency components by equations (2), nent Magnet Synchronous Motor), and a S is the mechan- (3), (4). ical vibration signal of the motor frame. The reduction ¥ ¥ control of the mechanical vibration is performed by the a0 S (t) = + å an cos(n t) + å bn sin(n t) (1) repetitive control system and/or the feedforward control 2 m =1 m =1 system. 2 Tr a = (t)cos( n t) n 0 S (2) Tr 3.1 Dynamic Equations of SPMSM 2 Tr b = (t)sin(n t) (3) Generally, in a d - q coordinate system, the dynamic n T 0 S r equations of SPMSM, used as the brushless DC motor, = + Snf(t) ancos(n t) bn sin(n t) (4) are described equation (5). Here, the coordinates trans- In this research, the above-mentioned calculations on formations from the (u, v, w) coordinate system to the (d real time are realized by the digital signal processor , q) coordinate system are described as equation (7) by (denoted by DSP in the following).
Details
-
File Typepdf
-
Upload Time-
-
Content LanguagesEnglish
-
Upload UserAnonymous/Not logged-in
-
File Pages12 Page
-
File Size-