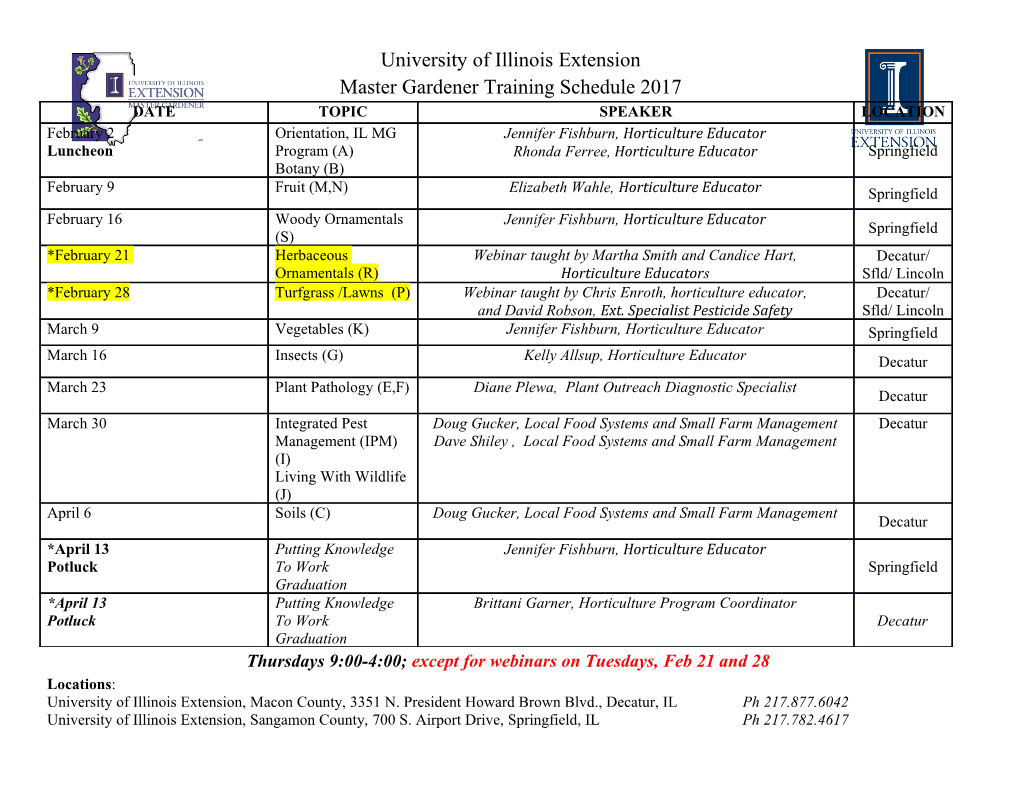
energies Article Automated Design Optimization of a Mono Tiltrotor in Hovering and Cruising States Lifang Zeng 1, Jianxin Hu 2,*, Dingyi Pan 1,* and Xueming Shao 1 1 School of Aeronautics and Astronautics, Zhejiang University, Hangzhou 310027, China; [email protected] (L.Z.); [email protected] (X.S.) 2 Faculty of Mechanical Engineering & Automation, Zhejiang Sci-Tech University, Hangzhou 310018, China * Correspondence: [email protected] (J.H.); [email protected] (D.P.) Received: 2 February 2020; Accepted: 2 March 2020; Published: 4 March 2020 Abstract: A mono tiltrotor (MTR) design which combines concepts of a tiltrotor and coaxial rotor is presented. The aerodynamic modeling of the MTR based on blade element momentum theory (BEMT) is conducted, and the method is fully validated with previous experimental data. An automated optimization approach integrating BEMT modeling and optimization algorithms is developed. Parameters such as inter-rotor spacing, blade twist, taper ratio and aspect ratio are chosen as design variables. Single-objective (in hovering or in cruising state) optimizations and multi-objective (both in hovering and cruising states) optimizations are studied at preset design points; i.e., hovering trim and cruising trim. Two single-objective optimizations result in different sets of parameter selections according to the different design objectives. The multi-objective optimization is applied to obtain an identical and compromised selection of design parameters. An optimal point is chosen from the Pareto front of the multi-objective optimization. The optimized design has a better performance in terms of the figure of merit (FM) and propulsive efficiency, which are improved by 7.3% for FM and 13.4% for propulsive efficiency from the prototype, respectively. Further aerodynamic analysis confirmed that the optimized rotor has a much more uniform load distribution along the blade span, and therefore a better aerodynamic performance in both hovering and cruising states is achieved. Keywords: mono tiltrotor (MTR); multi-objective optimization; BEMT; figure of merit; propulsive efficiency 1. Introduction The speed limit of a conventional helicopter is normally below 350 km/h [1] due to its inherent aerodynamic characteristics; e.g., the tip stall of the retreating blade and compressibility effects of the advancing blade. New concepts of rotorcraft design compounded with fixed wings have been put forward to break this speed limit. These conceptual rotorcrafts combine both the capabilities of conventional helicopters, such as vertical takeoff and hovering, and fixed-wing airplanes, such as the long range of cruising and large payload performance. An example of these conceptual designs is the Bell/Boeing V-22 Osprey [2], the first production tiltrotor in the world. The V-22 Osprey is capable of vertical take-off and landing, and its maximum flight speed is up to 509 km/h. Later, the innovative design of a mono tiltrotor (MTR) was proposed [3], in which only one rotor is used, combining the concepts of a tiltrotor and coaxial rotor. The original design of an MTR, which innovatively combines the concepts of a tiltrotor and coaxial rotor, is presented in Figure1. In particular, a contra-rotating coaxial rotor system is employed in this aircraft to achieve high aerodynamic performance with a compact structure. Compared with traditional helicopters, a coaxial rotor is able to fulfill torque trim without a separate anti-torque tail system, and it has a relatively high aerodynamic efficiency [4]. Benefiting from these advantages, the coaxial rotor design has been widely applied in shipboard Energies 2020, 13, 1155; doi:10.3390/en13051155 www.mdpi.com/journal/energies EnergiesEnergies 20202020, 13, 13, x, 1155FOR PEER REVIEW 2 2of of 20 20 has been widely applied in shipboard helicopters, micro unmanned helicopters [5], advanced high-speedhelicopters, compounded micro unmanned helicopters helicopters [6], etc. [5], The advanced present high-speed MTR integrates compounded a coaxial helicopters tiltrotor system, [6], etc. twoThe fixed present wings, MTR a integrates fuselage aand coaxial a twin-boom tiltrotor system, tail system. two fixed It distinguishably wings, a fuselage uses and a coaxial a twin-boom rotor tailto changesystem. from It distinguishably a lifter to a uses propeller a coaxial by rotor converti to changeng from from the a lifter vertical/hovering to a propeller by flight converting mode from to forward/cruisingthe vertical/hovering flight flight mode. mode When to forward converting/cruising between flight different mode. When modes, converting the coaxial between rotor di shaft,fferent wingmodes, and the fuselage coaxial rotorare fixed shaft, to wing each and other, fuselage tilting are through fixed to eachseveral other, hinges tilting with through the support several hinges of a twin-boomwith the support tail system. of a twin-boom This convertible tail system. wing This supplies convertible enough wing lift and supplies results enough in a high lift and lift-to-drag results in ratioa high in lift-to-dragcruising state. ratio The in cruising lift-to-drag state. ratio The lift-to-dragis expected ratio to be is expectedmore than to betwice more the than ratio twice of thea conventionalratio of a conventional helicopter helicopter[7]. [7]. Figure 1. The mono tiltrotor (MTR) and its three flight modes. Figure 1. The mono tiltrotor (MTR) and its three flight modes. The aerodynamic shape designs of a traditional rotor craft are usually based on parametric studies or physicalThe aerodynamic analysis [8 ],shape which designs rely to aof large a traditional extent on rotor experience. craft are However, usually forbased a new on concept parametric rotor studiescraft such or asphysical MTR, thereanalysis is little [8], relevant which experience.rely to a large The extent physical on analysis experience. method However, will be complex for a new and concepttime-consuming rotor craft with such such as MTR, little there experience. is little Inrele thevant preliminary experience. design The physical stage of aanalysis new layout method craft, will it is bedi complexfficult for and designers time-consuming to decide onwith the such appropriate little expe initialrience. values In the of preliminary parameters. design This paperstage of proposes a new layouta high-e craft,fficiency it is difficult automated for designers optimization to decide framework on the appropriate for MTR preliminary initial values design of parameters. by integrating This paperaerodynamic proposes modeling a high-efficiency and advanced automated optimization optimization algorithms. framework It will for explore MTR the preliminary relationship design of the bydesign integrating parameters aerodynamic and help modeling designers toand determine advanced trade-o optimizationffs in the algorithms. preliminary It design will explore stage. the relationshipIn the designof the design of MTR, parameters the optimization and help of ade coaxialsigners rotor to determine system plays trade-offs a crucial in the role preliminary in achieving designhigh e stage.fficiency in both cruising and hovering states. Single-objective optimization was applied in theIn design the design of the of traditional MTR, the coaxial-rotoroptimization systemof a coax [9ial]; however,rotor system it is plays not able a cr toucial cover role most in achieving working highconditions efficiency of MTR.in both In cruising other words, and hovering incompatible states. Single-objective sets of design parameters optimization are was possibly applied rendered in the designfor MTR of the in cruisingtraditional and coaxial-rotor hovering, respectively system [9]; [however,10]. A highly it is not effi cientable hoveringto cover most state working normally conditionsrequires low of MTR. disk loading,In other words, while aincompatible highly efficient sets cruising of design state parameters corresponds are possibly to a minimized rendered drag for MTRprofile in cruising of the blades and hovering, and compressibility respectively losses. [10]. A Therefore, highly efficient the design hovering targets state for no thermally two statesrequires are lowinconsistent. disk loading, Recently, while fewa highly works efficient in coaxial cruising rotor designstate corresponds have focused to ona minimized multi-objective drag designprofile (forof theboth blades hovering and and compressibility cruising states), losses. and mostTherefore, of them the are design based ontargets parametric for the studies two withoutstates are any inconsistent.integrated optimization Recently, few strategies works in [coaxial11,12]. rotor In view design of this,have it focused is necessary on multi-objective to develop and design validate (for bothcomprehensive hovering and multi-objective cruising states), optimization and most strategies. of them are The based goal ofon the parametric present work studies is to without construct any an integratedautomated optimization and efficient strategies design approach [11,12]. for In theview coaxial of this, rotor it designis necessary of MTR to coveringdevelop multipleand validate states comprehensivein its flight envelope. multi-objective optimization strategies. The goal of the present work is to construct an automatedTo ensure and the efficient efficiency design and approach accuracy for ofthe thecoaxial MTR’s rotor optimization design of MTR framework, covering multiple two key statesfactors—aerodynamic in its flight envelope. modeling and optimization algorithms—should be thoroughly explored. First, Energies
Details
-
File Typepdf
-
Upload Time-
-
Content LanguagesEnglish
-
Upload UserAnonymous/Not logged-in
-
File Pages20 Page
-
File Size-