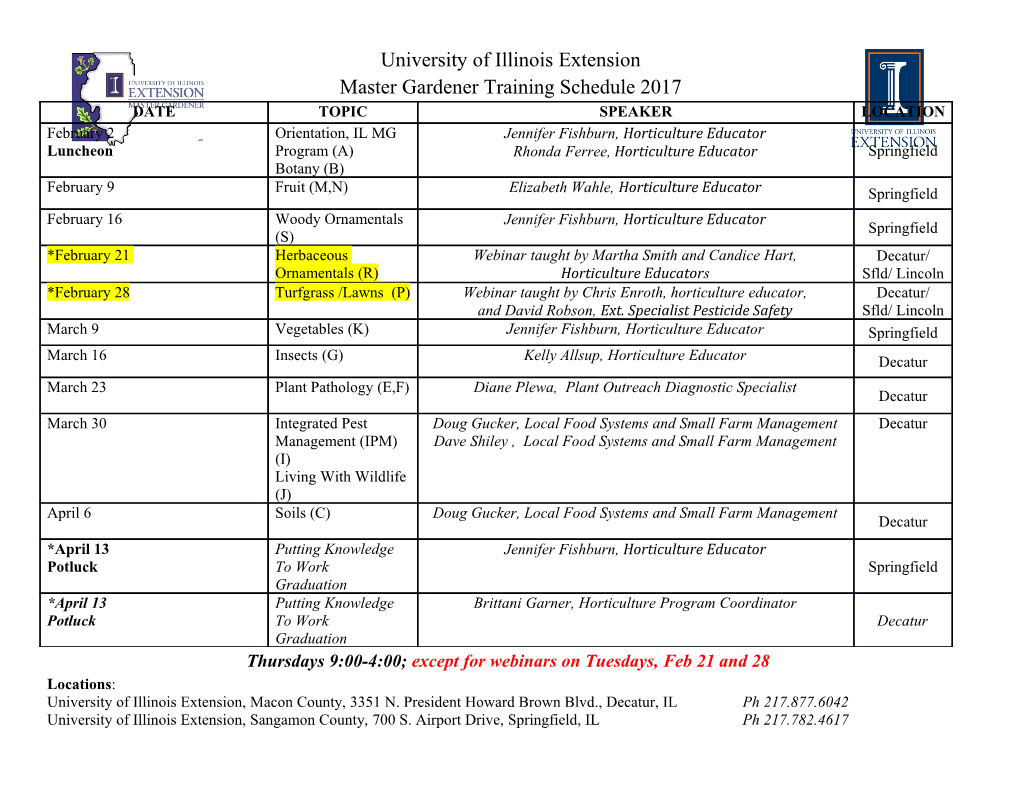
The International Journal of Advanced Manufacturing Technology https://doi.org/10.1007/s00170-018-3021-7 ORIGINAL ARTICLE Monitoring and evaluation of the wire drawing process using thermal imaging Joakim Larsson1 & Anton Jansson1 & Patrik Karlsson 1 Received: 24 August 2018 /Accepted: 11 November 2018 # The Author(s) 2018 Abstract Wire drawing is a cold work metal forming process which is dependant of a functional lubrication process. If the lubrication fails, there is a risk that both the tools and the produced wire will be damaged. Process monitoring of wire drawing is rare in today’s industry since there are no commercialised methods that deliver consistent results. In this paper, a method for monitoring of the wire drawing process is proposed and evaluated. A thermal imaging camera was used for acquiring thermal images of the wire as it leaves the drawing tool. It was found that the proposed method could capture changes in the wire drawing process and had correlation to the drawing force. An equation for estimating the friction condition between the wire and the drawing die using the wire temperature was also proposed and evaluated against experiments. The results showed that the new equation produced results that correlated well to results obtained using a conventional equation that use drawing force. Keywords Wire drawing . Thermal imaging camera . Process monitoring 1 Introduction normally used for larger dimensions (over 1 mm in diameter) and wet drawing for smaller dimensions. The dry drawing Wire drawing is a metal forming process where warm rolled method provides the lowest coefficient of friction between wire is refined. The dimensional tolerances and mechanical the wire and the die and a friction coefficient between 0.01 properties are set during this process. The wire is drawn and 0.07 can be considered as good if the process is function- through conical dies and becomes hardened due to the large ing as intended. For wet drawing, the coefficient of friction is deformation in the cold work process. In theory, it is possible normally between 0.08 and 0.15 [3]. In dry drawing, the lu- to have strains up to 63.2%, but in practice, this is not possible bricant used is either a calcium- or a sodium-based soap. If the due to friction and redundant work [1]. During the pass lubrication process malfunctions, there might be metallic con- through the first die, it is in practice possible to have strains tact between the wire and the die, resulting in high friction and up to 43% [2]. These high strains cause a high pressure inside process failure. the drawing die and in order to protect the wire from metallic In today’s wire drawing process, it is not common to use a contact with the die, it is important to have a functional lubri- system that will predict or even give a warning if the process cation process. Wire drawing is divided into two different fails. If quality inspection of the wire is required, it is done on categories depending on which type of lubricant is used in the finished wire product. This is usually done with the eddy- the process: dry drawing and wet drawing. Dry drawing is current (EC) testing method [2]. During the last four decades, different monitoring methods for the wire drawing process have been studied. Experiments * Joakim Larsson [email protected] performed in the 1980s focused on a device that measured the electrical resistance between the wire and the die. The group Anton Jansson claimed that this resistance would indicate on the condition of [email protected] the lubrication in the wire drawing process. If the lubrication Patrik Karlsson layer thickness between the wire and the die would change, [email protected] the resistance between them would also change. Thus, poor lubrication would result in low resistance. An industrial mon- 1 School of Science and Technology, Örebro University, itoring system was also developed called the “Tearing Örebro, Sweden Int J Adv Manuf Technol detector” which used the technique. The product was sold in a evaluated for process monitoring of the wire drawing process small number at the time when it was released [4–9]. In 1984, also are used for process monitoring of metal cutting. Thermal a patent for flaw detection in wire drawing using acoustic imaging cameras were suggested in the study, but were con- emission was filed. This was inspired by a paper published sidered only to be suitable for laboratory tests at that time in 1980 about assessment of the frictional condition in wire (1995) [24]. In 2016, a paper was published where an infrared drawing of aluminium using acoustic emission [10, 11]. thermal camera was used to monitor the tool condition in a During the 1980s, several attempts were made using acoustic turning process. The signal from the thermal imaging camera emission for monitoring the lubrication process in wire draw- was compared to data from optical acoustic emission measure- ing [12, 13]. Acoustic emission as a process monitoring tool ments with encouraging results [25]. for wire drawing has also been studied more recently leading The purpose of this paper was to investigate if monitor- to a patent and a product [14]. Measurements of vibrations ing of the wire drawing process using a thermal imaging using accelerometers instead of acoustic emission have also camera is viable. The hypothesis is that if the lubrication been studied recently, showing promising results [15]. conditions of the wire drawing process changes, then the In 2001, studies on different ways to monitor the drawing signal from the thermal imaging camera will also change. process using indirect measurements were investigated. Four The change in the signal is most likely depending on three methods were suggested: thermoelectric voltage occurring be- process factors: tween core and case, thermoelectric voltage occurring be- tween core and wire, acoustic emission, and the electric con- & The temperature of the wire: an increase of the friction tact resistance between the wire and die [16]. In 2014, an between the wire and the die leads to an increased amount investigation of possible monitoring processes for the detec- of energy that goes to the wire, which causes a higher wire tion of defects in the wire during the wire drawing process was surface temperature. made. One of the methods that were investigated was the use & The emissivity of the wire surface: there is a significant of a pyrometer to monitor the wire drawing process as the wire difference in the reflectivity between an unlubricated and a was already wound up on the block in the drawing machine. lubricated wire surface [18]. Experiments displayed promising results in detecting com- & Damage on the wire surface: if the lubrication process fails plete loss of lubrication, not because the pyrometer could de- galling may occur, which can lead to large scratches tect changes in wire temperature, but due to its ability to detect forming on the wire surface. This can cause patterns in changes in the emissivity of the wire surface. However, when the thermal images caused by both changes in temperature using a pyrometer, there is a disadvantage, the exact position and emissivity. and size of the measuring point is unknown. At the distance which the pyrometer was mounted from the block, the mea- suring point was larger than the diameter of the wire. This resulted in problems when the wire was unevenly winded on the block, the pyrometer would measure the temperature of 2 Materials and methods the block instead of the wire [17]. In 2017, a paper was pub- lished where a CCD-sensor was used to monitor the lubrica- To test the hypothesis, a thermal camera was placed in tion process of the wire drawing process. This was done by front of the drawing machine acquiring images of the wire studying the reflectivity of the wire as it passed by the sensor as it was leaving the drawing die. The distribution among in a box with a controlled light source. The method showed values from the pixels in the images from the thermal im- promising results when compared to drawing force measure- aging camera was studied by looking at pixel value stan- ments [18]. dard deviation of a small area of the wire surface. If the Several techniques have been evaluated for monitoring the lubrication process is functioning as intended, the mea- wire drawing process, but still, there is no system that is used sured values inside this area will be similar in every pixel. in the industry today. In recent years, the prices of thermal With an unstable or malfunctioning lubrication process, imaging cameras have dropped which makes the technique there should be detectable difference in measured values more available. Today, it is found in many vastly, different among the pixels. The signal level (absolute temperature) areas, such as human emotion detection, fault diagnostic in of the pixels is not of interest for monitoring purposes rotary machinery, monitoring of heat distribution systems, because the instantaneous emissivity of the wire surface control of laser welding, and fault detection in induction mo- is unknown. A change in emissivity has a significant influ- tors [19–23]. ence on the signal; this can cause a change in wire temper- Tool condition monitoring with focus on process monitor- ature to be compensated by a lower emissivity. However, ing of metal cutting has been investigated showing that the in this study, the emissivity of the wire from different same types of process monitoring sensors that have been stages of the drawing process was measured after the wire Int J Adv Manuf Technol drawing experiments had been performed for evaluation typically is 8 ms.
Details
-
File Typepdf
-
Upload Time-
-
Content LanguagesEnglish
-
Upload UserAnonymous/Not logged-in
-
File Pages14 Page
-
File Size-