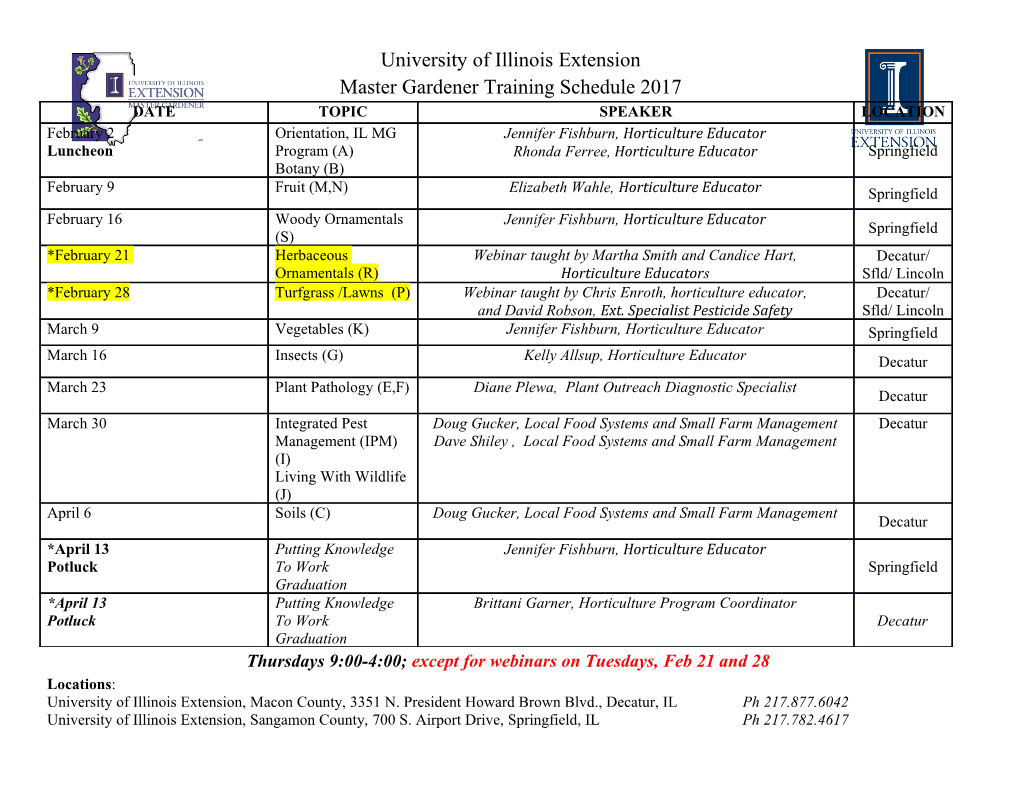
AUTOMOTIVE BATTERIES 101 JULY 2018 WMG, University of Warwick Professor David Greenwood, Advanced Propulsion Systems The battery is the defining component of an electrified vehicle Cost Power Range Package Life Ride and Handling © 2018 2 Primary functions of the battery across vehicle types ENGINE MOTOR ‘BATTERY’ BATTERY FUNCTION CONVENTIONAL 100kW Starter motor 12V Engine starting (ICE) Full transient Stop/start 3kW, 1kWh (3kW, 2-5Wh) Ancillary loads (400W average, 4kW peak, ~1kWh) MILD HYBRID 90-100kW 3-13kW 12-48V Absorb regenerated (MHEV) Full transient Torque boost/re-gen 5-15kW, 1kWh braking energy FULL HYBRID 60-80kW 20-40kW 100-300V Support acceleration (HEV) Less transient Limited EV mode 20-40kW, 2kWh PLUG-IN HYBRID 40-60kW 40-60kW 300-600V Provide primary power (PHEV) Less transient Stronger EV mode 40-60kW, 5-20kWh and energy Increasing power to energy ratio power to energy Increasing RANGE-EXTENDED 30-50kW 100kW 300-600V Provide primary power (REEV) No transient Full EV mode 100kW, 10-30kWh and energy ELECTRIC VEHICLE No Engine 100kW 300-600V Provide sole power (EV) Full EV mode 100kW, 30-80kWh and energy source © 2018 3 Biggest challenge for mass market uptake is cost COMPONENT COSTS FOR ELECTRIFICATION OF POWERTRAIN BATTERY Conventional COST IS THE SINGLE MHEV BIGGEST FACTOR HEV Engine/Transmission Battery Power Electronics Motor PHEV Charger E-ancillaries EV 0 2000 4000 6000 8000 10000 12000 Bill-of-Materials Component Cost € © 2018 4 Lithium-ion batteries are improving rapidly 18650 CELL CAPACITY (MAH) • Costs have fallen dramatically due to technology, production volume and market dynamics 4000 • Pack cost fallen from $1,000/kWh to <$250/kWh in less than 8 years 3000 2,000 95% conf interval whole industry 1,900 95% conf interval market leaders 2000 1,800 Publications, reports and journals 1,700 News items with expert statements 1,600 Log fit of news, reports, and journals: 12 ± 6% decline 1,500 Additional cost estimates without clear method 1,400 1000 Market leader, Nissan Motors, Leaf 1,300 Market leader, Tesla Motors, Model S 1,200 Other battery electric vehicles 1,100 Log fit of market leaders only: 8 ± 8% decline 1,000 Log fit of all estimates: 14 ± 6% decline 900 0 Future costs estimated in publications 800 2014 US$ per kWh <US$150 per kWh goal for commercialization 1995 2000 2005 2010 2015 700 600 500 400 300 200 100 • Volumetric energy density is increasing due to better 0 2005 2010 2015 2020 2025 2030 materials and cell structure Year • Doubled in 15 years • Requires continuous chemistry and materials innovation to continue Graph credit: Nkyvist et al 2014 Lithium-ion batteries are © 2018 improving rapidly 5 What makes up an automotive battery? Lithium-ion cell Module Pack e.g. pouch or cylindrical cell e.g. module for pouch cells (Nissan Leaf) e.g. pack for pouch cells (Nissan Leaf) As a single unit, a ‘cell’ performs the A ‘module’ is formed by connecting A ‘pack’ is formed by connecting primary functions of a rechargeable multiple ‘cells’, providing them with multiple ‘modules’ with sensors ‘battery’. Cells come in varied formats: a mechanical support structure and and a controller and then thermal interface and attaching housing the unit in a case. • Cylindrical Cells terminals. Modules are designed Electric vehicles are equipped • Pouch Cells according to cell format, target pack with batteries in a ‘pack’ state voltage and vehicle requirements. which are connected to • Prismatic Cells the powertrain. © 2018 6 Charging How a Lithium-ion Li+ e- cell works NiO - + 6 e Li Cathode Charge Anode • Lithium-ion (Li-ion) is a negative electrode to the Discharge general term for a variety of positive through the outer + - batteries whose properties circuit (the power supply). Li e rely on lithium as the When no more lithium-ions Li e- Li+ charge carrier. Li-ion offers will flow, the battery is advantages over other fully charged Cathode Material Anode Material e.g. LiCoO2 e.g. graphite chemistries such as weight • During discharge, the and voltage. For automotive lithium-ions flow back purposes, rechargeable through the electrolyte/ Anode/cathode materials: specific capacities and cells are used separator to the cathode. operating voltages vs pure lithium • There are many types of Electrons flow back to the Different chemistries suit specific requirements Li-ion battery depending anode through the outer 5 LiMn Ni O on the exact combination circuit. When all ions have 1.5 0.5 4 ENERGY DENSITY 4.5 LiMn1/3Co1/3Ni1/3O2 of materials used for the moved back, the battery is LiMn2O4 4 Cathode anode and cathode fully discharged and needs LiNiO2 3.5 LiCoO2 recharging 2.8V Anode • During charging, the 3 LiFePO 3.7V 4 3.5V positively charged lithium- • A motor converts the 2.5 Li2FeS2 ions flow from the cathode, electrical energy from the 2 3.2V Voltage vs Li(V) Voltage LTO 2.0V through the electrolyte/ battery into mechanical 1.5 TiO -B 2 Hard Carbons separator, to the anode energy to turn the wheels 1 Metal Nitrides 3.8V Silicon where they are stored. Graphite Lithium • Electricity from the grid is M alloys Electrons flow from the 0 used to charge the battery 0 200 400 600 3500 4200 141 mAh/g Specific Capacity (mAh/g) 3.7 V x 141 Ah/kg = 512 Wh/kg © 2018 7 Current lithium-ion battery chemistries: CATHODE/ANODE MATERIAL STRENGTHS WEAKNESSES Lithium Cobalt Oxide • High energy • Thermally unstable (LCO) Cathode • High power • Relatively short life span • Limited load capabilities Lithium Manganese Oxide Spinel • High power and thermal stability • Low capacity compared to other cathode materials (LMO) Cathode • Enhanced safety • Limited life cycle • Low cost • Need advanced thermal management Lithium Nickel Cobalt Aluminium • High specific energy • Safety issues Oxide (NCA) Cathode • Good specific power • Cost • Long life cycle Cathode Lithium Nickel Manganese Cobalt • Ni has high specific energy; Mn adds low • Nickel has low stability Oxide (NMC) Cathode internal resistance • Manganese offers low specific energy • Can be tailored to offer high specific energy or power Lithium Iron Phosphate • Inherently safe; tolerant to abuse • Lower energy density due to low operating (LFP) Cathode • Acceptable thermal stability voltage and capacity • High current rating • Long cycle life Graphite/Carbon-based • Good mechanical stability • Low volumetric capacity Anode • Good conductivity and Li-ion transport • Good gravimetric capacity Lithium Titanate • Withstands fast charge/discharge rates • Lower energy density compared to (LTO) Anode • Inherently safe graphitic anodes Anode • Long cycle life • Cost Silicon Alloy • High gravimetric/volumetric capacity • High degree of mechanical expansion (Si) Anode • Low cost on charging • Chemical stability © 2018 8 Promising battery chemistries: early stage research CHEMISTRY* PROPERTIES/BENEFITS RESEARCH CHALLENGES Solid State Batteries • Solid electrolyte and separator components; no concerns over • Improving poor conductivity ‘leakage’ • High volume manufacturing at • Improved safety due to lack of liquid electrolyte acceptable cost • High operating voltages increase potential energy density • Lighter and more space efficient; less need for cooling Metal Air Batteries • Pure metal anode and ambient air/O2 cathode • Short life cycle e.g. Li, Al, Zn, Na • Very high theoretical capacity • Issues with practical rechargeability • Increased safety vs Li-ion • Air handling • No use of heavy metals • Energy density reduces at high power Lithium Sulphur • High theoretical gravimetric energy density • Poor volumetric energy density (Li-S) • Sulphur is a low cost, abundant material • Issues with power density and • Improved safety discharge rate • Issues with cycle life stability Sodium-ion • Sodium is a low cost, abundant material • Issues of volumetric/gravimetric energy (Na-ion) • Improved safety for battery transportation density compared to Li-ion Silicon-based Electrodes • Si has ~x10 gravimetric capacity compared to graphite • Does not offer long cycle life (Si) • Could be lighter and/or store more energy • Practical application constraints * Promising chemistries included are those demonstrating suitable application potential for automotive requirements at lab scale. © 2018 9 Automotive battery: cell components +ve/-ve Terminals Electrolyte Active electrodes: Thinly wound or stacked into alternating sheets of material following a pattern: cathode – separator – anode. Quality and purity of material has an impact on charge efficiency and battery life. • Cathode: Positively charged electrode in the battery cell, often made of a lithium metal oxide and coated on to a current collecting aluminium (Al) foil. Metallised • Anode: Negatively charged electrode in the battery cell, often made of foil pouch graphite and coated on to a current collecting copper (Cu) foil. Anode • Terminals: positive and negative contacts to connect the cells and module. Separator Cathode • Separator: Thin layer of polymer electrically isolates the cathode and anode from one another to prevent short circuit. Its structure allows lithium ions to pass through, allowing current to flow through the cell (microporosity) +ve/-ve Electrolyte Terminals • Electrolyte: A liquid transport medium which surrounds the electrodes and soaks into the separator, allowing lithium ions to flow freely • Additives: Electrode and electrolyte properties can be improved by adding small amounts of other components, e.g. conductive additives Metal • Current Interrupt Device: A pressure valve disables the cell in case of case over-charge/over-heating
Details
-
File Typepdf
-
Upload Time-
-
Content LanguagesEnglish
-
Upload UserAnonymous/Not logged-in
-
File Pages24 Page
-
File Size-