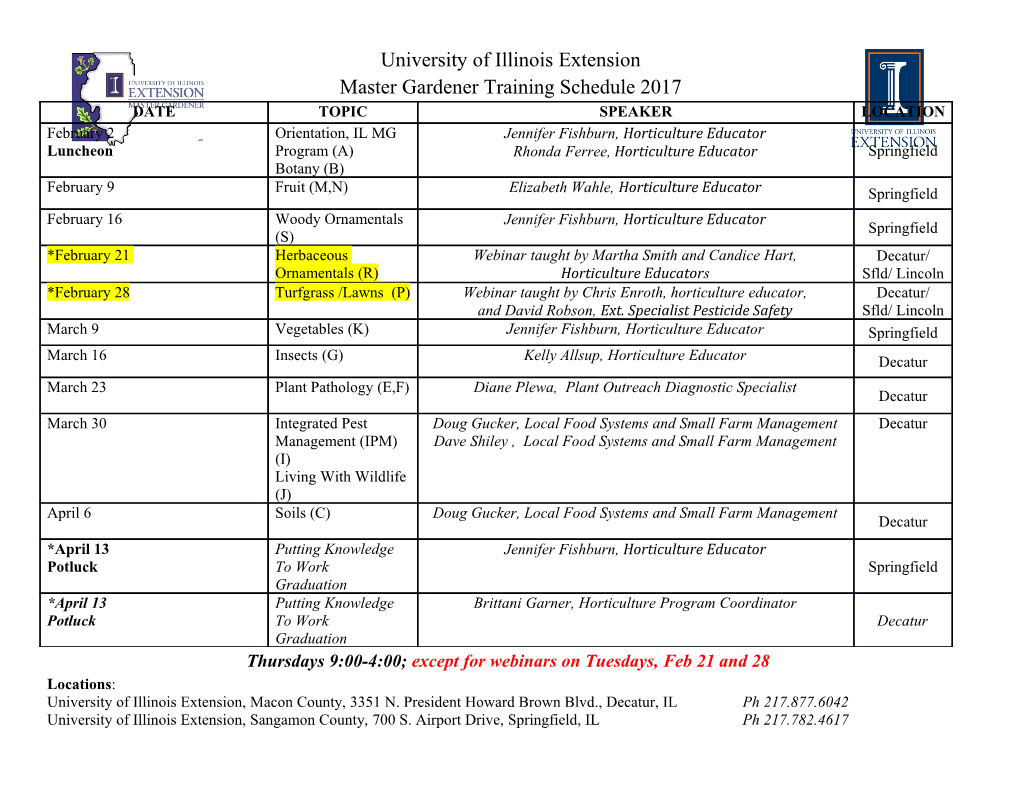
The impact of fretting wear on structural dynamics: Experiment and Simulation A. Fantetti, L.R. Tamatam, M. Volvert, I. Lawal, L. Liu, L. Salles, M.R.W. Brake, C.W. Schwingshackl, D. Nowell To cite this version: A. Fantetti, L.R. Tamatam, M. Volvert, I. Lawal, L. Liu, et al.. The impact of fretting wear on structural dynamics: Experiment and Simulation. Tribology International, Elsevier, 2019, 138, pp.111- 124. 10.1016/j.triboint.2019.05.023. hal-02530466 HAL Id: hal-02530466 https://hal.archives-ouvertes.fr/hal-02530466 Submitted on 3 Apr 2020 HAL is a multi-disciplinary open access L’archive ouverte pluridisciplinaire HAL, est archive for the deposit and dissemination of sci- destinée au dépôt et à la diffusion de documents entific research documents, whether they are pub- scientifiques de niveau recherche, publiés ou non, lished or not. The documents may come from émanant des établissements d’enseignement et de teaching and research institutions in France or recherche français ou étrangers, des laboratoires abroad, or from public or private research centers. publics ou privés. The Impact of Fretting Wear on Structural Dynamics: Experiment and Simulation A. Fantettia, L. R. Tamatamb, M. Volvertc, I. Lawald, L. Liue, L. Sallesa, M. R. W. Braked, C. W. Schwingshackla, D. Nowella aImperial College London, South Kensington Campus, London SW7 2AZ, UK bPolitecnico di Torino, Corso Duca degli Abruzzi 24, 10129 Torino, Italy cSpace Structures and Systems Laboratory, Department of Aerospace and Mechanical Engineering, University of Li`ege,Li`ege, Belgium dWilliam Marsh Rice University, 6100 Main St., Houston, TX 77005, USA eUniversity of Wisconsin-Madison, 1415 Engineering Drive, Madison, WI 53706, USA Abstract This paper investigates the effects of fretting wear on frictional contacts. A high frequency friction rig is used to measure the evolution of hysteresis loops, friction coefficient and tangential contact stiffness over time. This evolution of the contact parameters is linked to significant changes in natural frequencies and damping of the rig. Hysteresis loops are replicated by using a Bouc-Wen modified formulation, which includes wear to simulate the evolution of contact parameters and to model the evolving dynamic behaviour of the rig. A comparison of the measured and predicted dynamic behaviour demonstrates the feasibility of the proposed approach and highlights the need to consider wear to accurately capture the dynamic response of a system with frictional joints over its lifetime. Keywords: Fretting Wear, Nonlinear Dynamics, Hysteresis Loops, Friction Coefficient, Contact Stiffness 1. Introduction Stick,T=Kt⋅x Microslip Full sliding, μ=T/N 60 A major challenge in the modelling of the dynamics of jointed structures is the accurate characterization of 40 the contact forces occurring at friction interfaces. These contact forces can lead to significant changes in natural 20 frequencies and damping of the structure and, in addi- tion, may lead to catastrophic failures due to the effect 0 Energy of wear on the single components. Several contact models Dissipation have been proposed over the years to describe the con- -20 tact behaviour under oscillatory loadings [1{11], with the [N] Force Friction most common model being a Coulomb slider in series with Kt a spring (Jenkins element [5, 6]). These contact mod- -40 els have been successfully used in combination with har- -60 monic balance solvers [12{16] or time integration tech- -10 -5 0 5 10 niques [17, 18] to model the dynamics of realistic struc- Tangential Relative Displacement [μm] tures such as flanges [19], blades equipped with dampers Figure 1.1: Typical hysteresis loop and its parameters: the friction or shrouds [20{24] or lap joints [17]. coefficient µ, the contact stiffness kt and the energy dissipation. Due to the oscillatory nature of the excitation, frictional forces have the form of a hysteresis loop when plotted against the relative displacement that occurs between the ing of these contact parameters to build predictive mod- contact interfaces (see Fig. 1.1). When a simple macroslip els. In this case, an estimation of the contact parameters contact model is employed, hysteresis loops can be approx- is performed beforehand by means of specifically designed imated using three contact parameters: friction coefficient, frictional test rigs [27{29] or fully numerically by exploit- µ, normal contact stiffness, kn, and tangential contact ing physics-based contact models where roughness is ac- stiffness, kt. These parameters are normally used as tun- counted for [30]. ing factors to update numerical models, until the output One main limitation of all the approaches above is the as- of these models matches the experimental frequency re- sumption that the contact interface does not change over sponse function of the assembled structure [23{26]. Some time and hence the dynamic response remains unchanged. researchers have exploited instead the clear physical mean- However, fretting wear will occur at the interface leading Preprint submitted to Elsevier April 9, 2019 to a modification of the contact parameters and conse- the micro-asperity deformation, as the relative tangential quently of the hysteresis loop and of the dynamic response. displacement is measured relatively close to the interfaces, The goal of this work is to understand the evolution of less than 1mm far from the contact, making the bulk de- hysteretic behavior from both a material and a structural formation effect negligible. µ and kt are strongly affected perspective, and, in doing so, to see if new insights into by fretting wear: the hysteretic behavior of frictional contacts can be gained. Friction coefficient: The evolution of the friction coef- This is achieved by measuring the very high cycle evolution ficient with fretting wear has been widely investigated in of hysteretic properties for fretting by using the friction rig the recent past [27, 36{60]. Most of those studies have con- [27] built in the Dynamics Group of Imperial College Lon- firmed that the friction coefficient rapidly increases during don. The test rig measures friction input parameters for a running-in period, after which it reaches a steady state. industrial applications, such as the contact dynamics of The rapid increase is attributable to the removal of sur- aero engine components in contact. In addition, a physi- face layers, such as adsorbed gas layers, oxide layers or cally based, wear evolving constitutive model is proposed nature pollution films, which weakens the metal-to-metal to describe the hysteresis over time, and is used in com- adhesion between contact interfaces [58{63]. The removal bination with structural dynamics simulations to capture of such layers results in a metal-to-metal and/or metal- the evolution of the system dynamics. to-wear particles contact that increases the adhesive and ploughing components of the friction coefficient. When surface layers are completely removed and a balance is 2. Overview of Fretting Wear reached between generation and ejection of wear debris, Fretting occurs when two contacting surfaces exhibit the friction coefficient stabilizes to a steady state value a relative sliding motion, and is a major source of uncer- [62]. tainty for the dynamics modelling of jointed structures due Sauger et al. [64] and Fouvry et al. [65] pointed out that to the lack of understanding behind it. Two types of fret- during the first hundred fretting cycles, a tribologically ting have been described in the literature [31{33]: fretting transformed surface (TTS) forms because of a plastic de- fatigue and fretting wear. formation of the metals in contact. This TTS has a nano- Fretting fatigue generally occurs when the relative sliding crystalline structure corresponding to the chemical com- motion is small enough that part of the contact interface position of the bulk materials. This phenomenon may also is stuck and part of it slips. This type of fretting involves be involved in the evolution during the running-in period. the generation of cracks at the interface. Tangential Contact stiffness: To the authors' knowl- In contrast, fretting wear occurs when the relative sliding edge, only few studies have investigated the evolution of motion is larger and the whole interface exhibits a full slid- the tangential contact stiffness with wear [29, 36{38], since ing. Fretting wear leads to the joint degradation by means a reliable measurement of this parameter requires an ac- of material removal. This type of fretting can also lead to curate estimation of the relative sliding distance between noticeable system level changes in the dynamic response. specimens. In fact, in order to account for the mirco- Understanding the impact of fretting wear on the dynamic asperity deformation only, and not for the bulk elastic de- response of systems is crucial in designing high confidence formation, the displacement measurement points need to components. In this study, the effects of fretting wear were be very close to the contact interface [?? ]). Schwing- investigated in terms of the evolution of hysteresis loops shackl et al. [37] measured the contact stiffness using the previous generation of the friction rig used in the present (µ and kt) and the evolution of the system's dynamics. study. They found that the contact stiffness increases 2.1. Effects of fretting wear on hysteresis loops rapidly within the first 30,000 cycles (5 minutes at 100Hz) and then it slowly reaches a steady state in 15 minutes Hysteresis loops are characterized by two contact pa- (corresponding to 90,000 fretting cycles) for a wide range rameters (see Fig. 1.1): friction coefficient, µ, and tangen- of materials and contact conditions. This running-in is tial contact stiffness, k . The friction coefficient defines the t probably due to an increase in the conformity of the con- limit, µN, at which the contact start to slide: when the tact interfaces. In fact, larger areas of contact imply more tangential force occurring between the contact interfaces asperities in contact.
Details
-
File Typepdf
-
Upload Time-
-
Content LanguagesEnglish
-
Upload UserAnonymous/Not logged-in
-
File Pages20 Page
-
File Size-