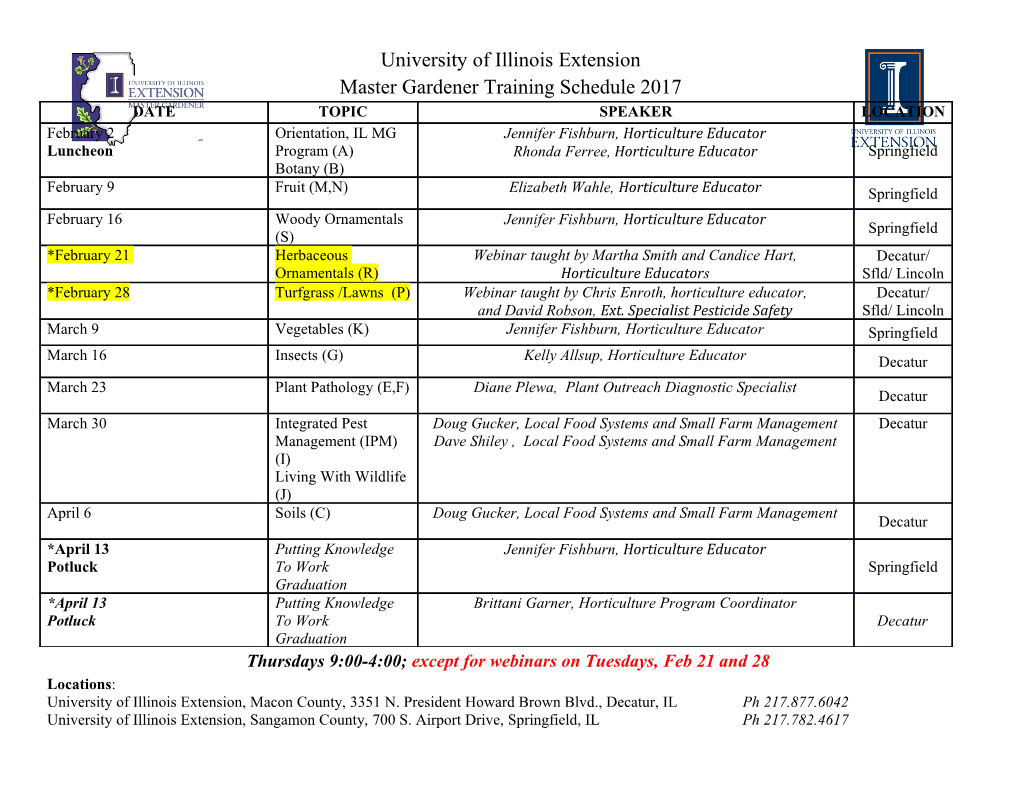
Operating Instructions & Parts Manual Hydraulic Truck Jack & 1” Air Impact Wrench Model Capacity 23221CIMPACT 22 Ton 1" Air Impact Wrench Hydraulic Truck Jack U.S. Patent No's. 6,012,377 & 5,946,912 This is the safety alert symbol. It is used to alert you to potential personal injury hazards. ! Obey all safety messages that follow this symbol to avoid possible injury or death. SFA Companies http://www.omegalift.com Read this manual and follow all the Safety Rules and Operating Instructions before using this product. © September 2017 23221CIMPACT-M0_092017 SAFETY AND GENERAL INFORMATION Save these instructions. For your safety, read, understand, and follow the information provided with and on this device before using. The owner and/or operator shall have an understanding of the device, its operating characteristics and safety operating instructions before operating the equipment. The owner and/or operator shall be aware that use and repair of this product may require special skills and knowledge. Instructions and safety information shall be read to and discussed with the operator in the operator's native language, making sure that the operator comprehends their contents, before use of this equipment is authorized. If any doubt exists as to the safe and proper use of this device, remove from service immediately. Inspect before each use. Do not use if abnormal conditions such as cracked welds, damaged, loose or missing parts are noted. Any equipment that appears damaged in any way, is found to be worn, or operates abnormally shall be removed from service until repaired. If the equipment has been or is suspected to have been subjected to an abnormal load or shock, immediately discontinue use until inspected by a factory authorized repair facility (contact distributor or manufacturer for list of authorized repair facilities). It is recommended that an annual inspection be made by an authorized repair facility. Labels and Operator's Manuals are available from the manufacturer. PRODUCT DESCRIPTION Hydraulic Truck Jacks are designed to lift, but not support, rated capacity partial vehicle loads consisting of one end of a vehicle. Immediately after lifting, support loads with a pair of appropriately rated matched jack stands. The 1" Air Impact Wrench is a hand-held air powered impact wrench designed to be used by one operator for the tightening, loosening or installing of threaded fasteners. PREPARATION (Hydraulic Truck Jacks) Assemble, align and insert the handle assembly and handle position bar into the handle sleeve, then tighten the bolt on handle sleeve to prevent accidental removal of handle while in use. Before Use 1. Verify that the product and application are compatible, if in doubt call Omega Technical Service (888) 332-6419. 2. Before using this product, read the operator's manual completely and familiarize yourself thoroughly with the product, its components and recognize the hazards associated with its use. 3. To familiarize yourself with basic operation, locate and turn the release valve (handle knob): a. Clockwise until firm resistance is felt to further turning. This is the CLOSED‘ ’ release valve position used to raise the load. b. Counter-clockwise, no more than 1 full turn from closed position. This is the ‘OPEN’ release valve position used to lower the load. The further the release valve is turned counter-clockwise, the faster the load descends. 4. With ram fully lowered, remove the oil filler screw. Check oil level. Proper oil level should be just below the rim of the opening. Reinstall the oil filler screw. 5. Pour a teaspoon of good quality air tool lubricant into the air supply inlet of the lift control valve. Connect to air supply, then squeeze the lift control valve for 3 seconds to evenly distribute lubricant. NOTICE: These models are equipped with 1/4" NPT air couplers. If installing a different air coupler, ensure thread tape or compound is used on connections. To ensure dependable, trouble free operation an inline air dryer and oiler is recommended. 6. Ensure that jack rolls freely. Raise and lower the unloaded ram throughout the lifting range before putting into service to ensure the jack operates smoothly. Replace worn or damaged parts and assemblies with Omega authorized replacement parts only. Bleeding/Venting Trapped Air 1. Open oil filler screw (reference Figure 2, #26). 2. Open release valve. 3. Activate air motor to vent air. 4. Remove set screw (reference Figure 2, #39) and use a screw driver to hold down check ball while very slowly pumping air motor until oil exiting from screw hole is steady without bubbles. 5. Reinstall set screw approximately two turns into hole (do not fully tighten). 6. Activate air motor a few additional times to vent air, while slowly tightening set screw. Ram should start to raise as screw is fully tightened. 7. Check oil level and reinstall filler screw (reference Figure 2, #26). 2 SPECIFICATIONS Min. Max. Hyd. Extension Model Capacity Jack Size (L x W) Height Height Range Screw Hydraulic Truck Jack 22 Ton 22" x 12-5/8" 9-3/4" 21-3/4" 5-5/8" 3-7/8" Model Drive Size Max. Torque Max. Pressure Air Inlet Hose Size 1" Air Impact Wrench 1" Square 2,065 ft.-lbs. 140 PSI 1/2" 1/2" Handle Handle Knob (release valve) Air Supply Inlet, 1/4NPT Lift Control Valve Handle Position Release Adapter, 2-1/2" Saddle Adapter Holder Extension Screw Handle Sleeve Oil Filler Screw Carrying Handle Wheel Figure 1 - Typical Truck Jack Nomenclature 3 1" Air Impact Wrench: ! WARNING Operating Hazards • Rotating drive sockets and drive extensions can easily • The use of this tool can expose the operator’s hands to entangle rubber-coated or metal-reinforced gloves. hazards including, impacts, cuts and abrasions and heat. • Do not wear loose-fitting gloves with cut of frayed fingers. Wear suitable gloves to protect hands. • Never hold the drive, socket or drive extension. • Operators and maintenance personnel shall be physically • Keep hands away from rotating drives. able to handle the bulk, weight and power of the tool. • Hold the tool correctly; be ready to counteract normal or Noise Hazards sudden movements and have both hands available. • Exposure to high noise levels can cause permanent, • Maintain a balanced body position and secure footing. disabling loss and other problems, such as tinnitus • In cases where the means to absorb the reaction torque (ringing, buzzing, whistling or humming in the ears). are requested, it is recommended to use a suspension Therefore a risk assessment and implementation of arm whenever possible. If that is not possible, side appropriate controls for these hazards are essential. handles are recommended for straight-case and pistol- • Appropriate controls to reduce the risk may include grip tools. It is recommended to use a means to absorb actions such as damping materials to prevent the reaction torque above 2.95 ft.-lbs. (4 N•m) for straight workpieces from “ringing”. tools, above 7.38 ft.-lbs. (10 N•m) for pistol-grip tools. • Use hearing protection in accordance with employer’s • Release the start-and-stop device in the case of an instructions and as required by occupational health and interruption of the energy supply. safety regulations. • Do not use in confined spaces and beware of crushing • Operate and maintain the impact wrench as hands between tool and workpiece recommended in the instructions handbook, to prevent an unnecessary increase in noise levels. Workplace Hazards • Select, maintain and replace the consumable/inserted • Slips, trips and major causes of workplace injury. Be tool as recommended in the instructions handbook, to aware of slippery surfaces caused by the use of the prevent an unnecessary increase in noise. tool and also of trip hazards caused by the air line or hydraulic hose. Vibration Hazards • Proceed with care in unfamiliar surroundings. Hidden • Exposure to vibration can cause disabling damage to the hazards, such as electricity or other utility lines, can exist. nerves and blood supply of the hands and arms. • The impact wrench is not intended for use in potentially • Wear warm clothing when working in cold conditions and explosive atmospheres and is not insulated against keep your hands warm and dry. coming into contact with electric power. • If you experience numbness, tingling, pain or whitening • Make sure there are no electrical cables, gas pipes, etc., of the skin in your fingers or hands, stop using the impact that can cause a hazard if damaged by use of the tool. wrench, tell your employer and consult a physician. • Dust and fumes generated when using impact wrench • Operate and maintain the impact wrench as recommended can cause ill health (for example cancer, birth defects, in the instructions handbook, to prevent an unnecessary asthma and/or dermatitis); risk assessment and increase in vibration levels. implementation of appropriate controls for these hazards • Do not use worn or ill-fitting sockets or extensions, as this are essential. is likely to cause a substantial increase in vibration. • Direct the exhaust so as to minimize disturbance of dust • Hold the tool with a light but safe grip, taking account of in a dust-filled environment. the required hand reaction forces, because the risk from • Use respiratory protection in accordance with employer’s vibration is generally greater when the grip force is higher. instructions and as required by occupational health and • Support the weight of the tool in a stand, tensioner or safety regulations. balancer, if possible. • Sleeve fittings should be used where practicable. Projectile Hazards • Failure of the workpiece,of accessories or even of the Repetitive Motion Hazards inserted tool itself can generate high-velocity projectiles. • If the operator experiences symptoms such as • Always wear impact-resistant eye protection during the persistent or recurring discomfort, pain, throbbing, operation of the impact wrench.
Details
-
File Typepdf
-
Upload Time-
-
Content LanguagesEnglish
-
Upload UserAnonymous/Not logged-in
-
File Pages12 Page
-
File Size-