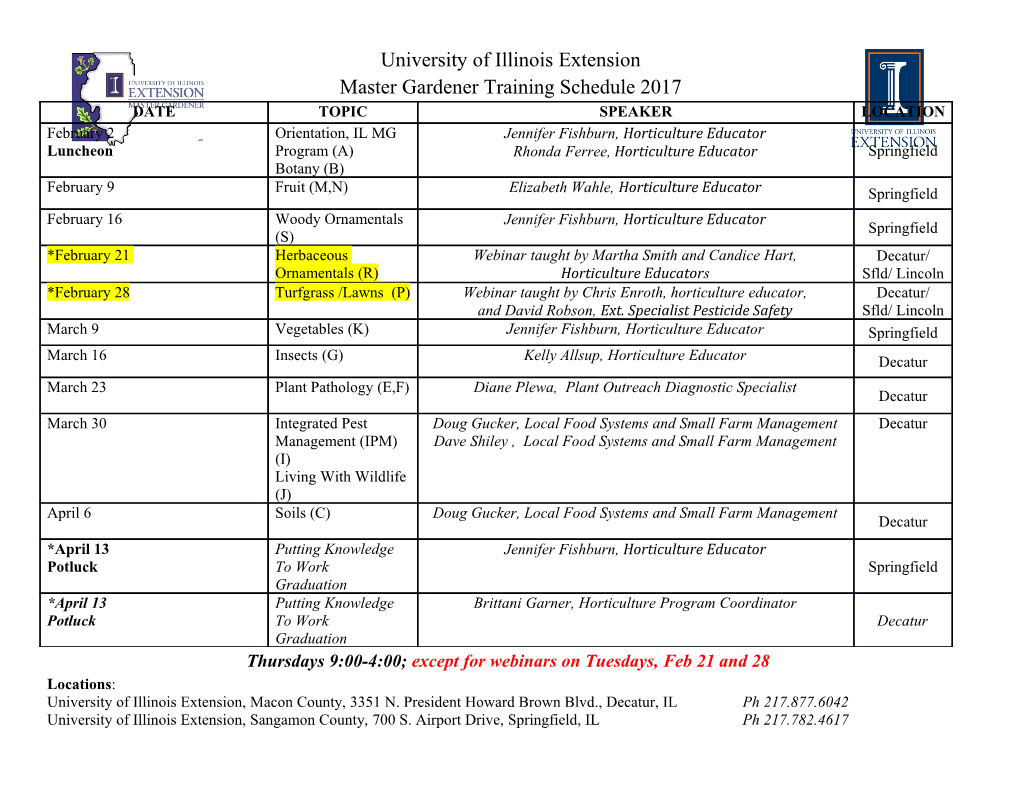
An Overview of Space Robotics © 2007 David L. Akin 3.1 Introduction Spacecraft, dating back to the first Earth satellites, have always been referred to as “robotic” systems. For the purposes of this overview of robotic technologies, the term “robotics” will be restricted to systems which have the capability to directly interact with their environment. This may take the form of mobility, grasping, or full dexterous manipulation. The intent of this effort is to look at the current state of space robotics, and to extrapolate to future capabilities and applications, while suggesting critical development steps that need to be taken to bring the far-term vision to fruition. Very large future space systems may well require the use of nonterrestrial materials, which will in turn need extensive robotic capabilities for their collection, processing, and assembly. For this reason, the technologies and applications considered will include planetary surface systems, as well as on-orbit robotics. 3.1.1 Potential Applications of Space Manufacturing The “market” envisioned for the purposes of this report is the development of a capable and robust space manufacturing infrastructure. The need for increased capabilities, whether in intelligence-gathering, science, or operations, drives toward larger and larger space systems. Taking observational astronomy as a representative (and unclassified) case, the transition from the 2.5-meter optics of Hubble Space Telescope to the 6-meter optics of the James Webb Space Telescope has required a paradigm shift from the launch of a monolithic spacecraft to the development of a highly articulated deployable system. Indeed, JWST may well be at (or slightly beyond) the technological feasibility limits for single-launch deployables: one developmental design required over 100 deployment actuators, all of which were single failure points for the success of the mission. To move beyond the 6-meter horizon for quantum increases in system performance, whether a terrestrial planet finder or highly sensitive SIGINT, will at a minimum require on-orbit assembly, where systems and components are integrated and tested post-launch. Some of the bigger potential systems, such as solar power satellites, only become feasible when we move beyond space assembly into the realm of space manufacturing – transporting raw materials to the production site, and fabricating components in situ for assembly and testing. Why would any rational program manager accept the risks of space manufacturing? Given the predominate role of Earth launch costs in overall program budgets, a robust space manufacturing capability represents a beneficial form of “bootstrapping”. Spacecraft are traditionally volume-, rather than mass-limited for conventional launch systems. Moving to raw materials significantly increases the bulk density and packing efficiency of the transportation system, thereby increasing efficiency in the single most expensive element. Since the predominate structural load sources are due to launch vehicle accelerations and vibrations, a system fabricated on-orbit can be optimized solely for operating loads in microgravity, which are (in general) 2-3 orders of magnitude less than launch loads. This gives rise to innovative designs of extremely lightweight systems, with much lower transportation costs than a traditional system. Of course, these economic An Overview of Space Robotics © 2007 David L. Akin advantages are greatly enhanced when the initial development costs of the space manufacturing infrastructure are supported by government funding, and made available to a range of space systems to amortize the costs over multiple programs. The ultimate benefit of space manufacturing, especially for extremely large projects such as space solar power, lies in the use of nonterrestrial materials. Earth is the largest rocky body in the solar system; the energy costs of getting materials from Earth’s surface to orbit are therefore the highest possible. Nonterrestrial materials are available in abundance from the lunar surface, from Apollo-Amor Earth-crossing asteroids, or (deeper in space) from Mars, main-belt asteroids, or from planetary moons throughout the solar system. A study performed under contract to NASA Marshall Space Flight Center in 1978 showed that solar power satellites could be fabricated and assembled in space from lunar materials for significantly lower costs than for Earth-launched components. Despite the high-tech nature of the required systems, it was found that 95% of the spacecraft could be fabricated in situ from lunar materials. With the possible discovery by Clementine and Lunar Prospector Orbiter of water ice in the vicinity of the lunar poles, the feasible percentage of nonterrestrial material would further increase, and the costs of establishing a lunar mining and transportation infrastructure would drop precipitously. 3.1.2 Robotics Requirements for Space Manufacturing What, then, will be required to bring space manufacturing into reality? For near-term applications, which will likely be limited to assembly and servicing, primary interest will be on manipulation capabilities, along with the ability to maneuver with high accuracy around an extended microgravity work site. With expansion to on-orbit fabrication and use of nonterrestrial materials, the entire field of planetary surface mobility becomes relevant, along with human-robot interactions and dedicated processes such as mining, refining, and parts fabrication. In developing a taxonomy for robotics requirements, manipulation may be broken down into categories of constrained and unconstrained motion. Unconstrained motion consists of transporting a payload (of whatever mass) from one state (position and attitude) to a desired final state. This may involve avoiding obstacles in the manipulator work space, but is unconstrained motion in that no external contact is allowed as part of the maneuver. This is clearly the simplest of all manipulation tasks, and technological limitations are largely based on the capabilities of the maneuvering robot arm. Following an inadvertent maneuver or actuator runaway, the system will have to bring the payload to a controlled stop short of obstacles without exceeding the limitations of the end effector grasp or any braking systems on the robot actuators. This creates limits on energy imparted to the payload, which in turn sets limits on speed of motion. There are several external considerations, even in unconstrained manipulator motions. Reaction control system thruster firings can transmit substantial loads to the grappled payload; it is routine, for instance, to inhibit space shuttle primary RCS firings during remote manipulator system (RMS) operations. Reaction torques based on manipulator motions will be imparted to the base of the arm, and into the host spacecraft. Many of the velocity limitations applied to the Space Station Remote Manipulator System (SSRMS) are due to reaction torques and control system disturbances to the space station itself, An Overview of Space Robotics © 2007 David L. Akin which has limited authority to absorb these disturbance forces without saturating its attitude control system. Constrained motion consists of the controlled motion of a payload in the presence of physical constraints, which limit available degrees of freedom and create significant disturbance forces in the manipulator itself. A typical example of this would be berthing a payload into a receptacle: guides are typically provided to ensure that the mating mechanism is properly aligned, but these guides produce friction, lock the manipulator payload into a single orientation during the final insertion maneuver, and give rise to the possibility of binding or other failure of the procedure. Most manipulators planned for dexterous activity incorporate some form of active compliance control, wherein external forces (such as insertion friction) are sensed and automatically nulled out, to prevent binding and ease operator workload requirements. Manipulators without active compliance, such as the shuttle RMS, typically utilize passive compliance elements such as flexibility in the manipulator arm, or design contact tasks to minimize insertion requirements. An alternate dimension to use as a metric for manipulation is the complexity and precision required of the end effector. This may be measured in the number of degrees of freedom required to perform a particular task, to grasp a specific interface, or merely to touch or actuate a switch. This is also associated with the required precision of motion to use an interface, ranging from the ±4 inches of RMS and SSRMS grapple fixtures to the precise (±0.005 in) control required to torque a standard bolt or use a microconical interface. 3.2 Space Robotics State-of-the-Art This section will endeavor to provide a concise overview of the current state-of-the-art of space robotics, as context to the following section on necessary future development activities. While focusing on systems flown and successfully operated to date, this section will also include systems in the development process for future flights, and major systems developed for past programs which, for whatever reason, did not survive until flight. It does not attempt to cover all of the development activities in laboratories which may be relevant to future space robotics systems, other than in identifying essential research efforts which are not currently underway. 3.2.1 Manipulation Systems “Manipulation” implies the ability to physically
Details
-
File Typepdf
-
Upload Time-
-
Content LanguagesEnglish
-
Upload UserAnonymous/Not logged-in
-
File Pages46 Page
-
File Size-