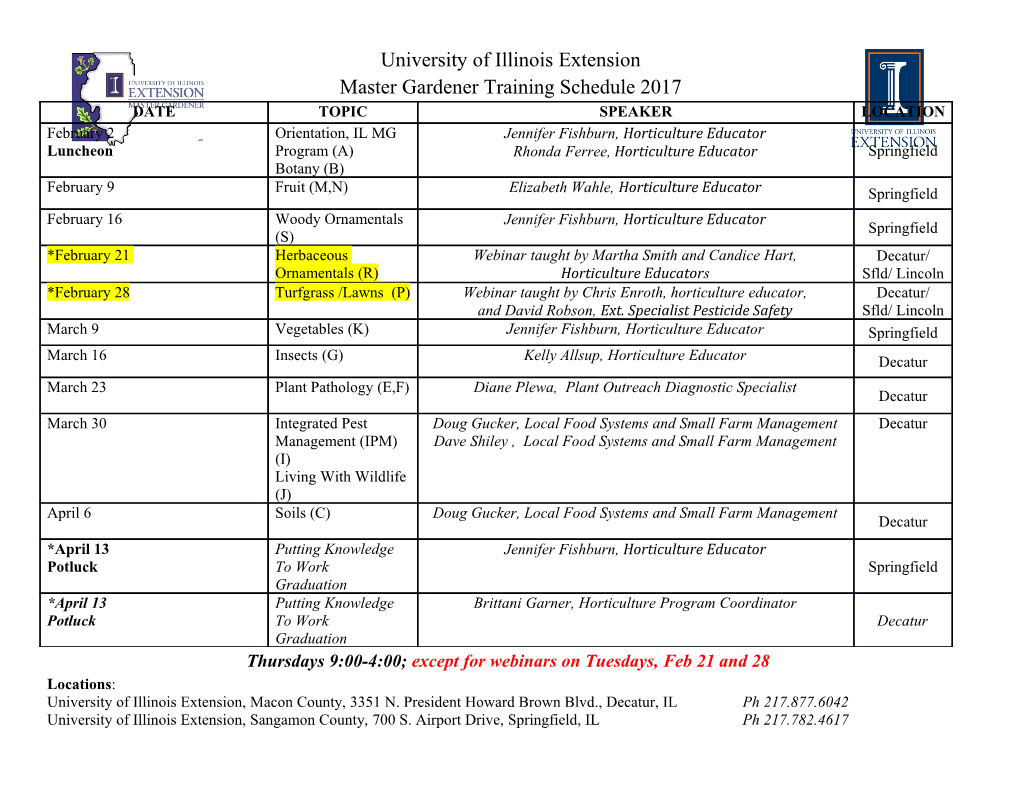
Cold and Hot Forging Fundamentals and Applications Copyright © 2005 ASM International® Taylan Altan, Gracious Ngaile, Gangshu Shen, editors, p7-15 All rights reserved. DOI:10.1361/chff2005p007 www.asminternational.org CHAPTER 2 Forging Processes: Variables and Descriptions Manas Shirgaokar 2.1 Introduction process conditions are difficult to predict and an- alyze. Often in producing discrete parts, several forging operations (preforming) are required to In forging, an initially simple part—a billet, transform the initial “simple” geometry into a for example—is plastically deformed between “complex” geometry, without causing material two tools (or dies) to obtain the desired final failure or degrading material properties. Con- configuration. Thus, a simple part geometry is sequently, the most significant objective of any transformed into a complex one, whereby the method of analysis is to assist the forging engi- tools “store” the desired geometry and impart neer in the design of forging and/or preforming pressure on the deforming material through the sequences. For a given operation (preforming or tool/material interface. Forging processes usu- finish forging), such design essentially consists ally produce little or no scrap and generate the of (a) establishing the kinematic relationships final part geometry in a very short time, usually (shape, velocities, strain rates, strains) between in one or a few strokes of a press or hammer. As the deformed and undeformed part, i.e., predict- a result, forging offers potential savings in en- ing metal flow, (b) establishing the limits of ergy and material, especially in medium and formability or producibility, i.e., determining large production quantities, where tool costs can whether it is possible to form the part without be easily amortized. In addition, for a given surface or internal failure, and (c) predicting the weight, parts produced by forging exhibit better forces and stresses necessary to execute the forg- mechanical and metallurgical properties and re- ing operation so that tooling and equipment can liability than do those manufactured by casting be designed or selected. or machining. For the understanding and quantitative design Forging is an experience-oriented technology. and optimization of forging operations it is use- Throughout the years, a great deal of know-how ful to (a) consider forging processes as a system and experience has been accumulated in this and (b) classify these processes in a systematic field, largely by trial-and-error methods. Nev- way [Altan et al., 1983]. ertheless, the forging industry has been capable of supplying products that are sophisticated and manufactured to very rigid standards from newly developed, difficult-to-form alloys. 2.2 Forging Operation as a System The physical phenomena describing a forging operation are difficult to express with quantita- A forging system comprises all the input vari- tive relationships. The metal flow, the friction at ables such as the billet or blank (geometry and the tool/material interface, the heat generation material), the tooling (geometry and material), and transfer during plastic flow, and the rela- the conditions at the tool/material interface, the tionships between microstructure/properties and mechanics of plastic deformation, the equipment 8 / Cold and Hot Forging: Fundamentals and Applications used, the characteristics of the final product, and Deformation Zone finally the plant environment where the process ● is being conducted. The mechanics of deformation, model used for analysis The “systems approach” in forging allows ● study of the input/output relationships and the Metal flow, velocities, strain, strain rate (kin- effect of the process variables on product quality ematics) ● Stresses (variation during deformation) and process economics. Figure 2.1 shows the ● different components of the forging system. The Temperatures (heat generation and transfer) key to a successful forging operation, i.e., to ob- Equipment taining the desired shape and properties, is the understanding and control of the metal flow. The ● Speed/production rate direction of metal flow, the magnitude of defor- ● Binder design and capabilities mation, and the temperatures involved greatly ● Force/energy capabilities influence the properties of the formed compo- ● Rigidity and accuracy nents. Metal flow determines both the mechan- Product ical properties related to local deformation and the formation of defects such as cracks and folds ● Geometry at or below the surface. The local metal flow is ● Dimensional accuracy/tolerances in turn influenced by the process variables sum- ● Surface finish marized below: ● Microstructure, metallurgical and mechani- cal properties Billet Environment ● Flow stress as a function of chemical com- ● Available manpower position, metallurgical structure, grain size, ● Air, noise, and wastewater pollution segregation, prior strain history, temperature ● Plant and production facilities and control of deformation, degree of deformation or strain, rate of deformation or strain, and mi- crostructure 2.2.1 Material Characterization ● Forgeability as a function of strain rate, tem- For a given material composition and defor- perature, deformation rate mation/heat treatment history (microstructure), ● Surface texture the flow stress and the workability (or forge- ● Thermal/physical properties (density, melt- ability) in various directions (anisotropy) are the ing point, specific heat, thermal conductivity most important material variables in the analysis and expansion, resistance to corrosion and of a metal forging process. oxidation) For a given microstructure, the flow stress, ● Initial conditions (composition, temperature, r¯ ,¯is expressed as a function of strain,e, strain history/prestrain) rate,e¯˙, and temperature, T: ● Plastic anisotropy ● Billet size and thickness Tooling/Dies ● Tool geometry ● Surface conditions, lubrication ● Material/heat treatment/hardness ● Temperature Conditions at the Die/Billet Interface ● Lubricant type and temperature ● Insulation and cooling characteristics of the interface layer ● Lubricity and frictional shear stress Fig. 2.1 One-blow impression-die forging considered as a ● system: (1) billet, (2) tooling, (3) tool/material inter- Characteristics related to lubricant applica- face, (4) deformation zone, (5) forging equipment, (6) product, (7) tion and removal plant environment Forging Processes: Variables and Descriptions / 9 m/Ί 3). There ס f(¯e,¯e˙, T) (Eq 2.1) and f is the friction factor(f ס ¯r are various methods of evaluating friction, i.e., To formulate the constitutive equation (Eq 2.1), estimating the value of l or m. In forging, the it is necessary to conduct torsion, plane-strain most commonly used tests are the ring com- compression, and uniform axisymmetric com- pression test, spike test, and cold extrusion test. pression tests. During any of these tests, plastic work creates a certain increase in temperature, 2.2.4 Deformation which must be considered in evaluating and us- Zone/Mechanics of Deformation ing the test results. Workability, forgeability, or formability is the In forging, material is deformed plastically to capability of the material to deform without fail- generate the shape of the desired product. Metal ure; it depends on (a) conditions existing during flow is influenced mainly by (a) tool geometry, deformation processing (such as temperature, (b) friction conditions, (c) characteristics of the rate of deformation, stresses, and strain history) stock material, and (d) thermal conditions exist- and (b) material variables (such as composition, ing in the deformation zone. The details of metal voids, inclusions, and initial microstructure). In flow influence the quality and the properties of hot forging processes, temperature gradients in the formed product and the force and energy re- the deforming material (for example, due to lo- quirements of the process. The mechanics of de- cal die chilling) also influence metal flow and formation, i.e., the metal flow, strains, strain failure phenomena. rates, and stresses, can be investigated by using one of the approximate methods of analysis (e.g., finite-element analysis, finite difference, 2.2.2 Tooling and Equipment slab, upper bound, etc.). The selection of a machine for a given process is influenced by the time, accuracy, and load/ 2.2.5 Product Geometry and Properties energy characteristics of that machine. Optimal equipment selection requires consideration of The macro- and microgeometry of the prod- the entire forging system, including lot size, con- uct, i.e., its dimensions and surface finish, are ditions at the plant, environmental effects, and influenced by the process variables. The pro- maintenance requirements, as well as the re- cessing conditions (temperature, strain, strain quirements of the specific part and process under rate) determine the microstructural variations consideration. taking place during deformation and often influ- The tooling variables include (a) design and ence the final product properties. Consequently, geometry, (b) surface finish, (c) stiffness, and (d) a realistic systems approach must include con- mechanical and thermal properties under con- sideration of (a) the relationships between prop- ditions of use. erties and microstructure of the formed material and (b) the quantitative influences of process 2.2.3 Friction and Lubrication at the conditions and heat treatment schedules on mi- crostructural variations. Die/Workpiece Interface The mechanics of interface friction are very complex.
Details
-
File Typepdf
-
Upload Time-
-
Content LanguagesEnglish
-
Upload UserAnonymous/Not logged-in
-
File Pages9 Page
-
File Size-