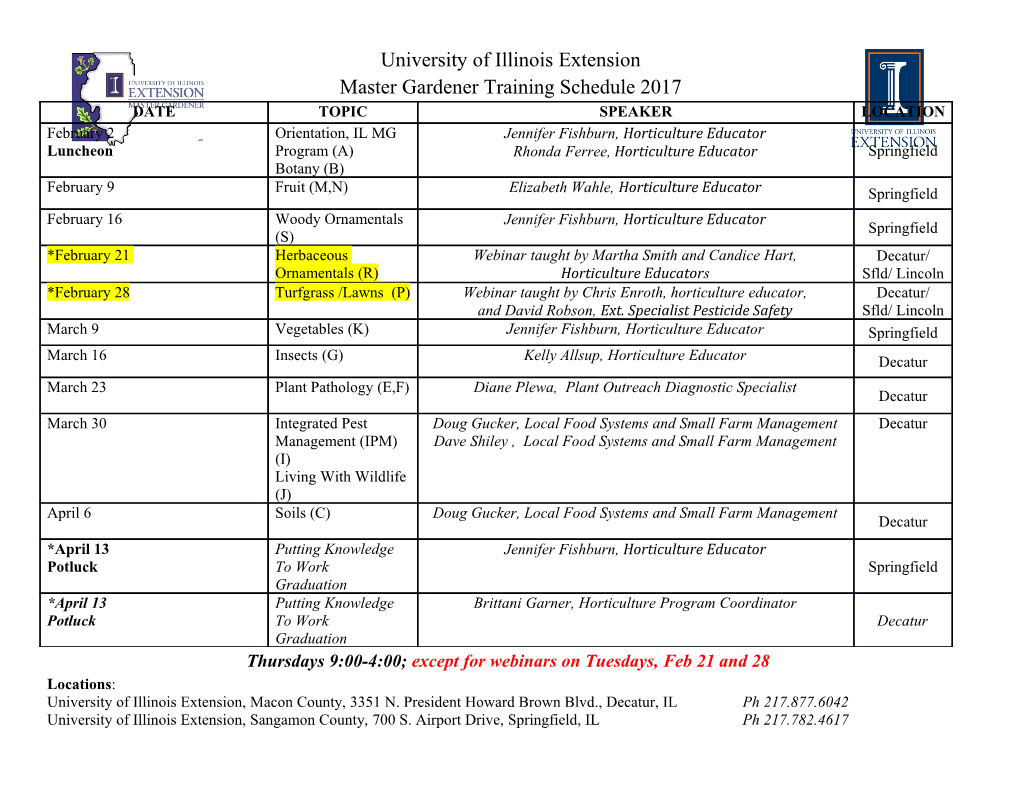
• SSC98-III-3 • The Orbital/Suborbital Program (OSP) "Minotaur" Space Launch Vehicle: • Using Surplus ICBM Motors To Achieve Low Cost Space Lift For Small Satellites Major Steven 1. Buckley, Captain Steven C. Weis, • Lieutenant Luis M. Marina, Jr., and Lieutenant Christopher Blair Morris Space and Missile Test and Evaluation Directorate 3550 Aberdeen Avenue SE • Kirtland AFB, NM 87117-5776 (505) 846-0185 • [email protected] • Scott Schoneman Orbital Sciences Corporation Launch Systems Group • 3380 South Price Road Chandler, AZ 85248 • (602) 814-6688 • [email protected] Abstract. The United States Air Force is developing a new family of launch vehicles using surplus Minuteman II • rocket motors to support both orbital launches of small satellites and suborbital ICBM-trajectory missions. Under the OSP contract awarded to Orbital Sciences Corporation in September 1997, four different vehicle configurations are being developed: I) single reentry vehicle ballistic launch, 2) multiple payload ballistic launch, 3) flight test • capability for developmental upper stages, and 4) space lift capability for small U.S. Government satellites. The space launch vehicle or "Minotaur" is composed of an M-55 (Minuteman II Stage 1), SR-19 (Minuteman II Stage • 2), Orion 50XL (Pegasus Stage 2), Orion 38 (Pegasus Stage 3), Pegasus avionics section, and Pegasus fairing. The initial launch of Minotaur will take place in September 1999 and will carry two military satellites: the FalconSat • payload for the U.S. Air Force Academy and the JA WSAT payload for the Space Test Program. • Introduction pursued the use of surplus Intercontinental Ballistic Missile (ICBM) rocket motors to reduce the cost of • The desire for reliable, low-cost access to Low Earth small space lift in support of DoD and other U.S. Orbit (LEO) for small Research and Development Government small satellite projects. The concept is (R&D) satellites has increased in recent years. For simple. The largest components of hardware costs for • example, numerous small satellite initiatives have small space lift are the rocket motors that make up the emerged at colleges and universities. The Department various stages. This cost is typically 300/0-50% of the • of Defense (DoD) has a long history of using small cost of a ride to orbit. satellites to support the testing of new components prior • to incorporation into large-scale operational satellite The U.S. Air Force has developed and fielded several programs. There are significant small satellite programs generations of ICBMs in support of national defense within NASA, the Department of Energy, and other programs. These missiles served long and well on • United States government agencies. Finally, advances "alert" guarding the United States from attack. As in satellite manufacturing technology have allowed the these systems aged, they were retired and replaced with • size and mass of satellites to diminish without loss of newer systems. These ICBM components were stored capability. All of these factors have contributed to the for future use or disposal. Over the years, these assets • growing need for reliable, low-cost small spacelift. have been used to support a variety of DoD programs. Smaller rocket motors have been used to drive rocket There are currently several initiatives underway to meet sleds to test aircrew egress systems, missile guidance • this requirement. The techniques used to reduce launch systems, or conduct scientific research in human factors costs include new manufacturing techniques, reusable engineering or other areas of scientific investigation. • systems, streamlined operational procedures, and the Larger motors have been integrated with other motors • use of surplus components. The U.S. Air Force has to make small sub-orbital rockets used for R&D • Major Steven 1. Buckley 12th AIAA/USU Conference on Small Satellites • • activities or target systems. Some ICBM systems, such fairing from the Pegasus XL air-launched space • as the Atlas and Titan II missiles, have been converted vehicle. The Minotaur approach reduces development to stand-alone space launch vehicles. and recurring launch costs by the utilization of • commercially developed, flight proven components and Currently, the Air Force has retired all Minuteman I propulsion from the Pegasus vehicle. Moreover, launch and Minuteman II solid rocket ICBM systems. These support costs are further reduced by adapting much of • missiles were dismantled and transported to the austere site stool launch approach demonstrated by government depots for storage under controlled the Taurus launch vehicle. • conditions. There are several hundred motor sets available to support DoD launch vehicle initiatives. The overall vehicle configuration is shown in Figure I. • These components are controlled and maintained by the It consists of two major subassemblies: I) the Lower Rocket Systems Launch Program (RSLP) located at Stages Assembly (LSA) consisting of the Minuteman Kirtland Air Force Base, New Mexico. RSLP has used boosters and 2) the Upper Stages Assembly (USA) • these Minuteman assets over the last thirty years to incorporating the Pegasus-derived front section and support DoD research and testing, chiefly as target new interstage. The vehicle length is approximately • vehicles for interceptor and sensor testing. The Air 63 ft from Stage nozzle exit planes to the top of the Force has a goal to use these components to support fairing. The launch weight of the Minotaur is 79,800 orbital launches as welL • Ibm, not including the mass of the payload. A variety of launch vehicle configurations have been • proposed over the years but none met the minimum lift Propulsion requirements and none were developed until the RSLP • program initiated the OrbitaVSuborbital Program All four boosters are solid propellant motors with the (OSP). The goal of the OSP program is to develop and characteristics shown in Table 1. The M55 and SRI9 field suborbital and orbital Minuteman II derived utilized for Stages I and 2 were originally developed • launch vehicles in support of DoD activities. The and produced for the Minuteman II ICBM. Because of program consists of two suborbital configurations, the the reduction in ICBMs due to the START-l treaty, • capability to use Minuteman II stages to boost several hundred sets of Minuteman boosters are in developmental upper stages into space for flight test, storage and available for use. They are provided as and an orbital small launch vehicle nicknamed • Government Furnished Property (GFP) through RSLP. "Minotaur". All elements of the OSP program, with The Orion 50XL developed for Pegasus is used as the the exception of the experimental upperstage test third stage motor instead of the normal Minuteman II • capability, are designed to be a "launch service". M57. This provides additional throw-weight capability as well as allowing the existing Pegasus Orion 38 motor • The Air Force contracted with Orbital Sciences and fairing to be used without changes. A relatively Corporation to integrate the surplus rocket motors with simple metallic interstage structure is used to integrate other components (the Minotaur uses Pegasus XL the Pegasus and Minuteman motors. This approach • components), integrate the launch vehicle with the reduces design risk by keeping the top two stages of payload and launch facilities, and execute the launch Minotaur identical to the Pegasus XL's top two stages • mission. This gives the Air Force flexibility to support a variety of sub-orbital missions as well as an efficient system to support small space lift requirements. The Payload Fairing • major interest of the small satellite community is in the Minotaur Small Launch Vehicle (SL V) so this paper The baseline Payload Fairing utilized by Minotaur is • will concentrate on this configuration. the same fairing design used by Pegasus. It is 14.5 feet long with and principal diameter of 50 inches. The • nominal mass for the integrated fairing system is 374 Vehicle Description Ibm. It is constructed of 60 mil face sheets over 0.5 in aluminum honeycomb. Honeycomb venting is provided • The Minotaur is a four stage, ground launched, solid through small holes in the inner face sheet, while bulk propellant, and inertially guided spacelift vehicle. It venting is accommodated via two cutouts near the base • uses the fITst two stages from the Minuteman II ICBM of the fairing. The fairing completely encloses the combined with the upper two stages, structure, and payload, avionics subsystem and fourth stage motor. • • Major Steven J. Buckley 2 12''' AIAAlUSU Conference on Small Satellites • • • • • • • • • r.~"'1.'.s1i:,1'.t'8.(.(j~;·I2~ ~1 'ie,," • ;\iZI,.ITVC • ';l~~IGvrol1d6.,.~ • • -'i.llif'l'lt(l"':'A • • • Figure 1. Minotaur Vehicle Configuration • Table 1. Minotaur Booster Characteristics • Stage 1 Stage 2 Stage 3 Stage 4 MM55Al MM SR-19 Orion 50XL Orion 38 Dimensions • Length 294.87 in 162.32 in 141 in 52.7 in Diameter 65.69 in 52.17 in 50.2 in 38in Mass (each) • Propellant Mass 45830 Ibm 13753 Ibm 8633 Ibm 1699 Ibm Gross Mass 50885 Ibm 15506 Ibm 9551 Ibm 1977 Ibm Structure • Type Monocoque Monocoque Case Material D6AC Steel 6AI-4V titanium Graphite Epoxy Graphite Epoxy Propulsion • Propellant TP-HIOll Type II ANB-3066 HTPB HTPB Average Thrust 178000lbs 603l21bs 345151b 704351b Number of Motors 1 1 1 1 • Number of Segments 1 1 1 1 Isp 237 sec vac 287.5 sec vac 290.1 sec vac 290.2 sec vac Chamber Pressure 1019 psia 656 psia • Expansion Ratio 58.6:1 67.5:1 Control-Pitch,
Details
-
File Typepdf
-
Upload Time-
-
Content LanguagesEnglish
-
Upload UserAnonymous/Not logged-in
-
File Pages14 Page
-
File Size-