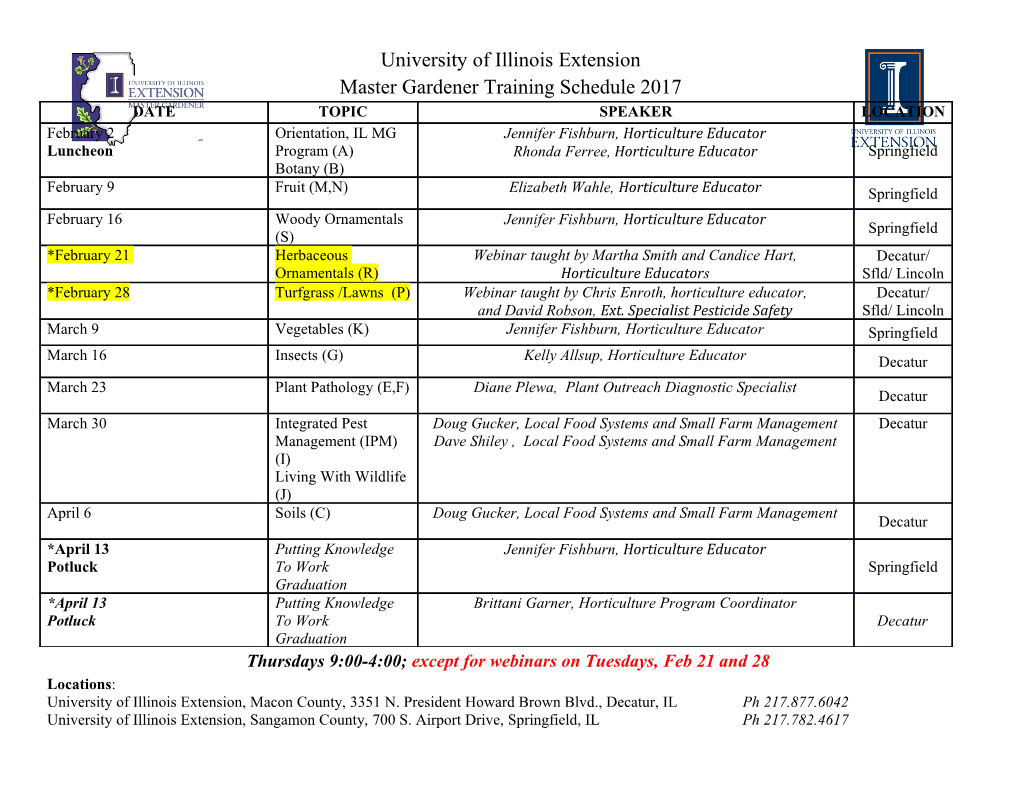
ON ACHIEVING AN OPTIMAL RIVETED LAP JOINT DESIGN FOR FIBRE METAL LAMINATES A.M. Brown, C.D. Rans, and P.V. Straznicky Department of Mechanical and Aerospace Engineering, Carleton University, 1125 Colonel By Drive, K1S 5B6, Ottawa, Ontario, Canada ABSTRACT Fibre metal laminates are designed to provide a damage tolerant alternative to monolithic metallic materials in airframe structures without the need for new structural design solutions required by pure fibre reinforced composites. This advantage allows fibre metal laminates to be incorporated directly into existing airframe design practices with little effort. Although such a simple transition is possible, fibre metal laminates exhibit different properties and behaviour than monolithic metallic materials. Consequently, differences may exist in optimal design details for a given structural design solution. This paper overviews the results of a study examining this possibility for a common airframe joint design solution: the riveted lap joint. Focusing on fatigue performance, a series of studies were completed to assess how major differences between monolithic aluminum sheet and a glass fibre-aluminum fibre metal laminate variant known as GLARE could be treated and exploited to obtain an optimal GLARE joint. These studies include an examination of alternative countersinking methods for thin laminated sheets, the formation of residual stresses in GLARE due to fastener interference, and material stiffness effects on joint bending. Results from these studies will form the basis for a discussion on achieving an optimal riveted lap joint design for GLARE. INTRODUCTION Fibre metal laminates (FML’s) are a family of hybrid laminates consisting of alternating layers of monolithic metallic sheet and fibre reinforced epoxy pre-impregnated fibre (prepreg) layers (Figure 1). Originating from the development of built-up structures pioneered by Fokker Aircraft in the late 1940’s, FML’s were found to exhibit benefits from both their metallic and fibre reinforced composite constituents. Specifically, FML’s possess many of the damage tolerant properties inherent in fibre reinforced composite materials while retaining the fabrication and repair capabilities of sheet metal. Within the aerospace field, these properties are attractive as they provide an opportunity to enhance the damage tolerance of airframe structures without the need for new structural design solutions required by pure fibre-reinforced composites. Although FML’s can be incorporated directly into metallic airframe design practices with little effort, FML’s do exhibit different properties and behaviour compared to monolithic metallic materials. Consequently, differences may exist in optimal design details for a given structural design solution. This paper provides an overview of studies examining this possibility for a common airframe joint design solution: the riveted lap joint. 1 FibreLayers Metallic Layers Figure 1 Illustration of fibre metal laminate Figure 2 Illustration of fibre bridging construction. mechanism. GLARE LAMINATES Within the family of FML’s, a material known as GLARE (GLAss REinforced aluminum) has been developed as a replacement for monolithic 2024-T3 aluminum in aircraft fuselage construction. This material consists of 2024-T3 aluminum for the metallic layers and S2-glass fibre epoxy for the prepreg layers. The focus of this paper is the GLARE3-2/1-0.3 laminate which would be a suitable replacement for 1 mm 2024-T3 fuselage skin. FML’s and, more specifically, GLARE variants are known to have beneficial characteristics in the area of fatigue and damage tolerance with fatigue lives in excess of 10 times that of 2024-T3 [1]. The reason for the increased fatigue performance is the material’s superior crack propagation life through a mechanism called fibre bridging. With fibre bridging, the load normally carried by the cracked aluminum plies gets redistributed into the adjacent intact fibre layers and the stress concentration at the crack tip is effectively reduced (Figure 2). A further benefit of the sandwich lay-up is that through thickness crack propagation does not occur. A crack growing through the thickness of an aluminum ply will stop once it hits a prepreg layer. It then remains for the other intact aluminum plies to nucleate cracks. This unique laminate construction contributes to several other desirable properties [2-4] for an aircraft material but will not be discussed here. Although the fatigue propagation behaviour of GLARE is superior to 2024-T3, crack nucleation actually occurs earlier than in monolithic sheet. This stems from the difference in flexibility of the material plies and from residual tensile stresses in the aluminum plies introduced during the curing cycle of the manufacturing stage. These tensile residual stresses contribute to any applied stress and helps lead to crack nucleation. In addition to the presence of tensile residual stresses, the lower stiffness of the prepreg plies in the sandwich lay-up means that the aluminum plies will experience greater stresses than the applied bulk stress. 2 FATIGUE OF RIVETED LAP JOINTS The basic riveted lap joint configuration consists of two sheets joined by one or more rows of rivets. The two sheets are differentiated by their location and accessibility for inspection along the joint overlap; in an airframe application, the outer sheet would be accessible from the outside of the aircraft while the inner sheet would be accessible from the inside. Additional variables and terminology used in defining a riveted lap joint design are illustrated in Figure 3. Outer free OUTER surface Outer faying SHEET s surface (rivet pitch) t (sheet thickness) TOP ROW Do (rivet p diameter) (row pitch) BOTTOM ROW INNER SHEET Inner free Inner faying surface surface Figure 3: 3-row riveted lap joint nomenclature. Developing a lap joint design based on fatigue performance requires the designer to manipulate the local stress state around fatigue prone rivet locations in order to prolong fatigue crack nucleation and reduce the rate of propagation of existing cracks. This local stress state can be broken down into components related to load transfer, and secondary loads such as secondary bending and rivet interference as illustrated in Figure 4. These components and the influence of lap joint design variables on them will be briefly discussed in order to establish a baseline for lap joint design which will be expanded on later in the context of GLARE specific lap joint design. Load Transfer Load transfer in riveted lap joints occurs by two mechanisms. The majority of load is transferred by means of bearing between the rivets and inner and outer sheets while the remainder is transferred through friction between the faying joint surfaces. The magnitude of the bearing stress at a rivet hole is related to the load transferred by a single rivet and the bearing area (rivet diameter multiplied by sheet thickness) over which that load is transmitted into the joined sheets. Large bearing stresses promote crack nucleation and reduce the crack free life of a joint. Although bearing stresses can be reduced easily in practice by increasing the total bearing area, either through increasing the rivet diameter, increasing the number of rivets, or both, these steps negatively impact crack growth. The reduced amount of sheet material along the net section of a rivet row that 3 would accompany such efforts to reduce bearing stress increase crack propagation rates and reduce critical crack lengths. Bearing Friction Bypass Load Transfer Secondary Loads Secondary Bending Interference Figure 4: Illustration of local stress field components in a riveted lap joint. Figure 5: Illustration of load carried by inner and outer sheets in a 3-row lap joint. Friction comprises a small portion of the overall load transfer in a riveted joint and is often neglected. Any load that is transferred through friction reduces bearing stress and generally results in an improvement in fatigue performance. More important than the amount of load transferred through friction is the amount of fretting damage that occurs as a result of friction. Fretting damage is a destructive process associated with clamped bodies undergoing oscillatory loading [5]. In riveted lap splices, the evidence of fretting damage is a black oxidized region surrounding the rivet hole on the sheet faying surface. This damaging process is known to generate microcracks in the surface that, under further loading, can propagate into the substrate as a fatigue crack. In multiple-row lap joints, each rivet row transfers a portion of the applied load from the outer to inner sheet while the remainder (referred to as the bypass load) remains in the outer sheet (Figure 5). The amount of load transferred by each rivet row is related to the relative flexibilities of the rivets and sheets being joined, neglecting the contribution from friction. For a 3-row lap joint, the top and bottom rivet rows transfer the same amount of load due to joint asymmetry while the load transferred by the middle rivet row can be determined by: 4 frivet TT21 (1) ffrivet sheet where: TT12, = load transferred by top and middle row respectively frivet, f sheet = rivet and sheet flexibilities As negative flexibilities are not possible, this equation shows that the top and bottom rivet rows will always transfer (through bearing) a larger percentage of the load than the middle rivet rows. The combination of large bearing stresses and high bypass stresses along these rivet rows results in two fatigue critical locations: in the outer sheet along the top rivet row and in the inner sheet along the bottom rivet row (Figure 5). In practice, the inner sheet location is typically less critical due to improved hole filling within this sheet during riveting and due to the possible added stress concentration in the outer sheet due to countersinking. Although adding more rows of rivets beyond three can reduce the amount of load transferred through the top and bottom rivet rows, this reduction drops off exponentially with the number of rivet rows and is typically viewed as a weight and manufacturing penalty.
Details
-
File Typepdf
-
Upload Time-
-
Content LanguagesEnglish
-
Upload UserAnonymous/Not logged-in
-
File Pages12 Page
-
File Size-