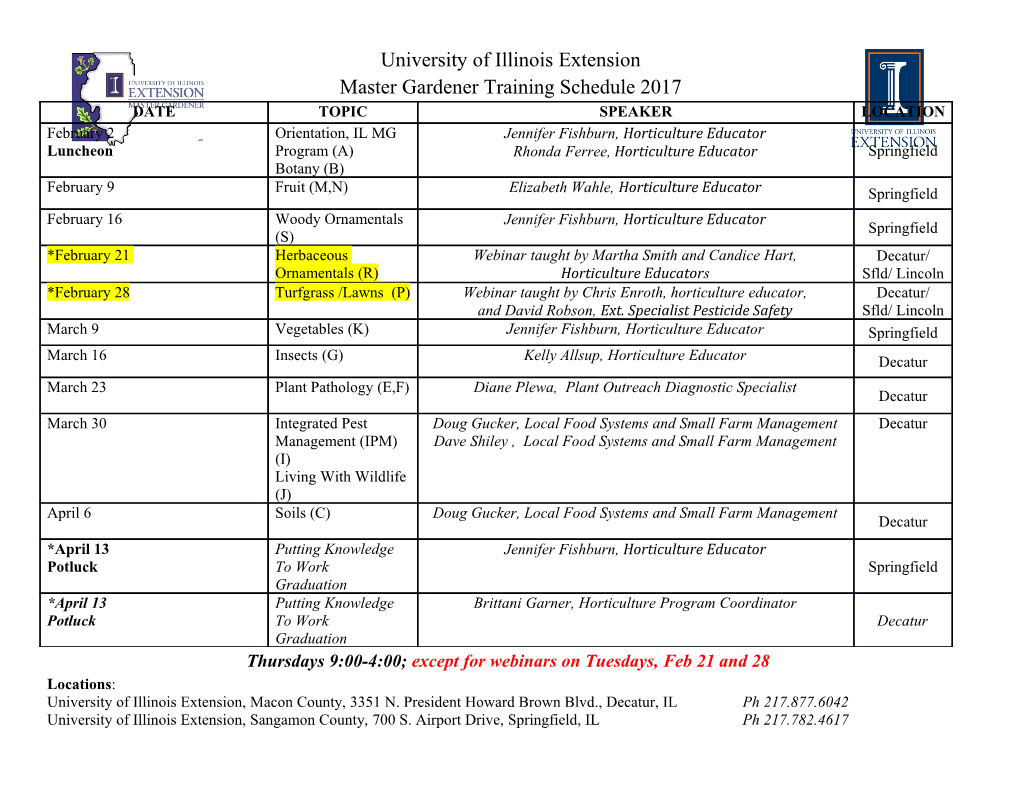
Post combustion in converter steelmaking Oghbasilasie Haile Holappa Lauri Helsinki University of Technology Department of Materials Science and Rock Engineering Laboratory of Metallurgy Report TKK-V-B128 .r - - .. ' _ - _ . -T .rsaaa Espoo 1997 DISCLAIMER Portions of this document may be illegible electronic image products. Images are produced from the best available original document. Helsinki University of Technology Department of Materials Science and Rock Engineering Laboratory of Metallurgy Post combustion in converter steelmaking Oghbasilasie Haile Holappa Lauri Research programme: SULA II Project: Post combustion in converter process Key words: post combustion, saving energy, smelting reduction, steelmaking, top blowing, bottom blowing, combined blowing Vuorimiehentie 2 K FIN-02150 Espoo, Finland ISSN 0785-5168 ISBN 951-22-3487-4 CONTENTS ABSTRACT....................................................................................................................................4 1. INTRODUCTION..................................................................................................................... 5 1.1. Definition ....................................................................................................................5 1.2. Post Combustion Ratio and Heat Transfer Efficiency ......................................... 7 1.2.1. Measurement of Post Combustion Ratio............................................................8 1.2.2. Measurement of Heat Efficiency ......................................................................... 9 2. PHYSICO-CHEMICAL BASES OF POST COMBUSTION......................................... 11 2.1. Thermodynamics of Post Combustion Reaction ................................................ 11 2.1.1. Carbon-Oxygen Equilibrium ..................................... 13 2.1.2. Influence of Iron on Post Combustion ..............................................................16 2.2. Rate Phenomena .....................................................................................................17 2.2.1. Hydrodynamics .....................................................................................................17 2.2.2. Heat Transfer .........................................................................................................22 3. INFLUENCE OF DIFFERENT PROCESS PARAMETERS ON POST COMBUSTION............................................................................................. 25 3.1. Post Combustion in LD process............................................................................ 25 3.2. Effect of Lance Height on Post Combustion ........................................................28 3.3. Bottom Stirring........................................................................................................30 3.4. Special Lance Construction .................................................................................... 32 3.5. Refractory Wear /Vessel Volume ..........................................................................34 3.6. Effect of Slag on Post Combustion Ratio............................................................ 37 4. CONTRIBUTION OF SMELTING REDUCTION...........................................................40 4.1. Post Combustion Behaviour in In-bath Type Smelting Reduction ...................40 2 4.2. Kinetics .....................................................................................................................42 4.3. Post Combustion in Different Smelting Reduction Processes...........................43 5. FUTURE...................................................................................................................................49 6. CONCLUSIONS................................................................................................... 50 REFERENCES............................................................................................................................. 51 3 ABSTRACT The purpose of this work is to study the fundamentals of post combustion and the effect of different process parameters on the post combustion ratio (PCR) and heat transfer efficiency (HTE) in converter steelmaking process. The PCR and HTE have been determined under normal operating conditions. Trials assessed the effect of lance height, vessel volume, foaming slag and pellet additions on PCR and HTE. Based on enthalpy considerations, postcombustion of CO gas is regarded as one of the most effective means of increasing the heat supply to the BOP. The thermodynamic study of gas-metal-slag reactions gives the limiting conditions for post combustion inside the converter reactor. Different process parameters influencing both thermodynamic equilibria and kinetic conditions can greatly affect the post combustion ratio. Different features of converter processes as well smelting reduction processes utilizing post combustion have been reviewed. 4 1. INTRODUCTION 1.1. Definition The off-gas of the oxygen converter contains considerable chemical energy which is being increasingly utilized with off-gas collection. From the economic point of view, it would be advantageous in the converter process to return at least a part of this energy to the process. With full combustion of CO to CO2 and the utilization of this heat in the converter, sufficient energy would be available to increase the scrap rate to about 55 % of the total charge. But it is known that complete combustion of CO to CO2 cannot be reached in contact with liquid iron because of the required high oxygen potential, which then would significanty oxidize iron. The energy obtainable by post combustion can thus only be utilized if the post combustion takes place in the gas space and the enormous amount of heat released thereby will be transferred from the gas phase back into the bath. If a larger portion of the post combustion energy remained in the off-gas, the off gas temperature would increase so drastically that the refractory lining of the converter would be destroyed. For example, the explicit aim of the rotary furnace processes to reduce the heat load of the vessel wall caused by the high off-gas temperature of the post combustion in such a way that the melt had constantly to cool the wall during the rotary movement. However, it is known that the rotary furnace although offering the highest energy utilization of the steel refining processes, has failed for insufficient life of the refractory lining /!/. The post combustion ratio in the converter is dependent upon the balance between the oxidation of CO produced to CO2 and the reduction of CO2 to CO. It is considered that the post combustion ratio depends on the results of complicated heterogeneous reactions in a nonsteady state. Under the assumption that the main reactions of post combustion are the formation of CO2 by the reaction between the oxygen jet and CO in the atmosphere and the formation of CO by the reaction between CO2 produced as described above and carbon 5 contained in the steel, the post combustion ratio was studied by Hirai. M, Tsujino. R. et al. /2/ on the basis of a reaction model shown in Fig. 1. •Lance nozzle CO entrained - O2 jet by O2 jet Supersonic jot core region COo getting Free jet out of jet region CO by de- carburization reaction X Region of COg' getting out Fig. 1 Schematic diagram of post combustion 111 The velocity of the oxygen jet with increasing distance from the outlet of the lance nozzle changes from the supersonic jet core region to the free jet region through the transition jet region. In this model a jet of CO% is formed by the reaction between oxygen free jet region arid CO produced by the decarburization reaction, being entrained from the atmosphere into the oxygen free jet region (CO + 1/20% —> CO%). The main reactions are shown in table 1 /Based in Refer. 2 and 18/. Table 1. Gibbs energies for the reactions of post combustion in converter. Reactions AG°; cal / mol rci + i/2o9(g) = co(g) - 33939 - 9.75T (1) C0(g) + l/20?(g)-»C0?.(g) -67890 +21.10T (2) C0?(g) + [C]-»2C0(g) 34580 - 30.95T (3) CO?(g) + Fem -> (FeO) + CO(g) 7094 - 7.48T (4) (FeO) + [C]->CO(g) + Fem 27486 - 23.47T (5) 6 Carbon dioxide at the surface layer of jet with the velocity below a certain critical value is entrained into and dissipated with the flow of CO produced from the spot, and the rest of CO2 which is not dissipated and the oxygen jet reacts with carbon in the steel bath to form CO. It is assumed that the amount of CO2 dissipated is proportional to the flow rate with the velocity below a certain critical value in the free jet region, and that the post combustion ratio is proportional to the ratio of the amount of CO2 dissipated to the amount of CO produced by the decarburization reaction /2/. 1.2. Post Combustion Ratio and Heat Transfer Efficiency One of the most important process parameters in steelmaking processes is the post combustion ratio (PCR) obtained in the furnace. The post combustion ratio is defined as: %C02 +%H2 0 PCR X 100 (6 ) %CO + %C02 + %H2 + %H2 0 Higher post combustion ratios imply that more heat is generated in the vessel, this heat is necessary to heat scrap and carry out the steelmaking reactions. Unfortunately , not all the heat generated by the post combustion reactions is actually transferred to the bath, thus, a heat- transfer efficiency (HTE) term is required. Conventionally, HTE is defined: excess heat in off - gas HTE = X 100 % (7) heat available from PC According to this definition, the HTE will be 100 % if the gas leaves the vessel at the
Details
-
File Typepdf
-
Upload Time-
-
Content LanguagesEnglish
-
Upload UserAnonymous/Not logged-in
-
File Pages55 Page
-
File Size-