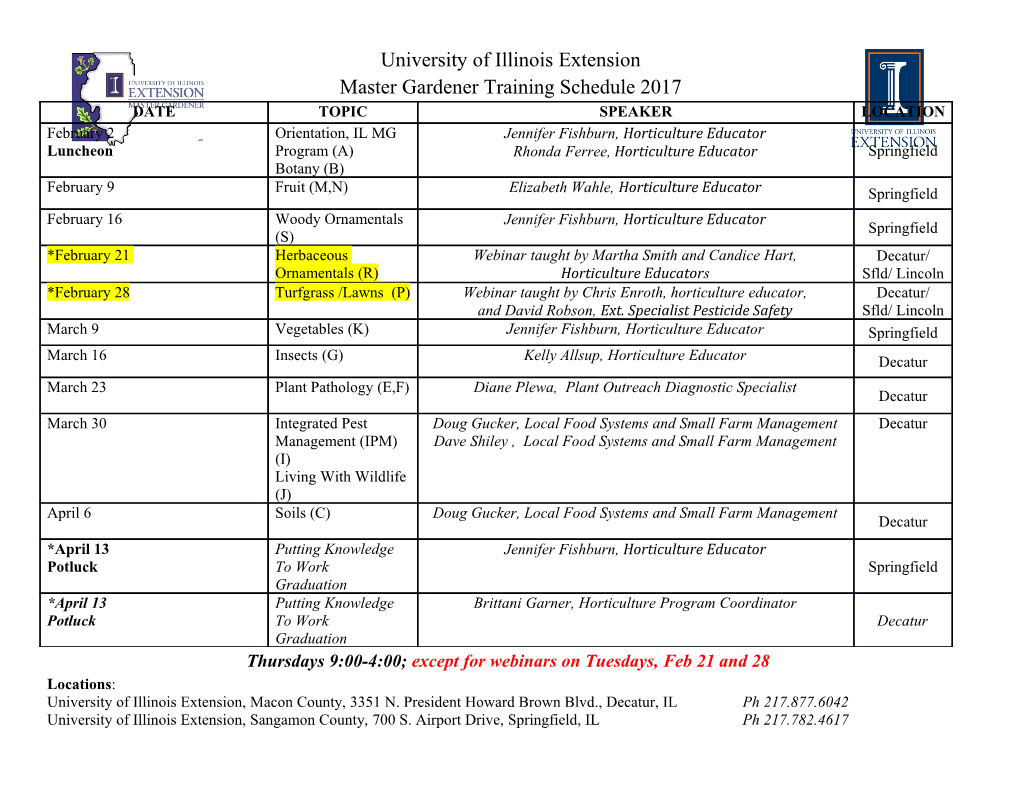
Polymer Testing 36 (2014) 10–19 Contents lists available at ScienceDirect Polymer Testing journal homepage: www.elsevier.com/locate/polytest Material behaviour Experimental study of crystallization of PolyEtherEtherKetone (PEEK) over a large temperature range using a nano-calorimeter Xavier Tardif a,*, Baptiste Pignon b, Nicolas Boyard b, Jürn W.P. Schmelzer c, Vincent Sobotka b, Didier Delaunay b, Christoph Schick c a IRT Jules Verne, Chemin du Chaffault, 44340 Bouguenais, France b LUNAM Université, Université de Nantes, CNRS, Laboratoire de Thermocinétique de Nantes, UMR 6607, La Chantrerie, rue Christian Pauc, BP 50609, 44306 Nantes cedex 3, France c University of Rostock, Institute of Physics, Wismarsche Str. 43-45, 18051 Rostock, Germany article info abstract Article history: The recently developed fast scanning differential calorimetry is used for the first time to Received 30 January 2014 determine the crystallization kinetics of Poly(EtherEtherKetone) (PEEK). In our experi- Accepted 15 March 2014 ments, crystallization is studied in isothermal conditions over a large temperature range from 170 Cto310C. Two different measurement protocols were employed. Between Keywords: 200 C and 300 C the heat flow was directly measured during isothermal crystallization. PEEK Outside this temperature range we measured the heat of fusion on heating after inter- Flash DSC rupted isothermal crystallization. We show that data can be analyzed with the Avrami Crystallization kinetics Avrami approach incorporating a term describing secondary crystallization. The crystallization fi Secondary crystallization half-times are measured. The Avrami kinetic coef cient KAv associated with primary crystallization is evaluated from isothermal crystallization between 170 C and 310 C where data were not previously available. The kinetics of crystallization of PEEK has only one maximum located around 230 C and its Avrami exponent is close to 3, suggesting instantaneous nucleation with subsequent spherical growth. The whole isothermal crys- tallization process is modeled in terms of Hillier’s model since it takes secondary crys- tallization kinetics into account. Finally, it is shown that the double melting peak behavior observed after isothermal crystallization (below 260 C) is a consequence of the reorga- nization process during heating. Ó 2014 Elsevier Ltd. All rights reserved. 1. Introduction since its maximum crystallinity is close to 40% [1]. The glass transition temperature of PEEK is 143 C [2], the fi N PolyEtherEtherKetone (PEEK) is a high performance in nite polymer melting temperature, Tm , is usually semi-crystalline thermoplastic that is nowadays the sub- considered to be about 390 C [3] and its pyrolysis tem- ject of a large number of studies because its mechanical perature is 550 C [4]. and chemical properties are very promising, especially for Composite part quality (residual stresses, shape dis- leading edge industries. It is a low crystalline polymer, tortion.) at the completion of the manufacturing process can be predicted from thermo-elastic simulations involving coupling between mechanical and thermal properties of * Corresponding author. the samples under consideration. However, the imple- E-mail addresses: [email protected], xav.tardif@gmail. com (X. Tardif). mentation of such an approach requires comprehensive http://dx.doi.org/10.1016/j.polymertesting.2014.03.013 0142-9418/Ó 2014 Elsevier Ltd. All rights reserved. X. Tardif et al. / Polymer Testing 36 (2014) 10–19 11 and accurate knowledge of the thermo-physical properties secondary crystallization on the overall crystallization to provide coherent results. In particular, in the case of kinetics. semi-crystalline polymers, the modeling of the samples So far, only morphology and crystallization kinetics of also requires detailed knowledge of the crystallization PEEK at high temperatures have been studied employing kinetics. different methods [2,3,21–23]. Crystallization kinetics is The phase change of an amorphous polymer into a commonly studied at high temperatures (between 280 C semi-crystalline solid material is commonly described by and 320 C for PEEK) in isothermal conditions from DSC overall crystallization kinetic theories [5]. Kinetic studies (Differential Scanning Calorimeter) experimental data generally start by considering experiments performed because of the low cooling rates in DSC and/or from optical under isothermal conditions. The ratio of the crystalline microscopy experiments by measuring the growth rate phase, a(t), with respect to time, t, can be described in such (nucleation step cannot be observed) of spherulites (acti- cases by the Avrami equation Eq (1) [6–8], vated nuclei) and their number. For example, Wei et al. [21] study experimentally the kinetics of crystallization of PEEK að Þ¼ À ð , nÞ; t 1 exp KAv t (1) at high temperatures by an Avrami approach with tem- perature modulated DSC. Following the Avrami approach, which is characterized by the Avrami kinetic coefficient they observed that secondary crystallization is character- “KAv” and the Avrami exponent “n”. The Avrami kinetic ized by an Avrami exponent 0.52 < n < 1.37 if these pro- coefficient is a function of temperature and pressure, while cesses proceed above 290 C. However, it is difficult to the Avrami exponent depends on shape, growth mode of assign a physical meaning to these values based on the the crystallites and the nature of the nucleation process Avrami theory. Wang et al. [3] studied isothermal crystal- (sporadic: constant nucleation frequency or instantaneous: lization of PEEK with a Perkin-Elmer DSC 7. Above 280 C, all the nuclei are formed instantaneously). The Avrami they used the Avrami equation whereas below 170 C they approach supposes four assumptions: (i) The nuclei are studied the cold crystallization process. In the range in randomly dispersed in the bulk. (ii) The growth rate is only between those two temperatures the crystallization pro- dependent on temperature at a given pressure. (iii) The cess was too fast to be studied by DSC. Kuo et al. [22] also nucleation rate is also only dependent on temperature at a performed isothermal crystallization of PEEK from 260 C given pressure and (iv) disappearance of potential nuclei to 310 C by DSC analysis using a Perkin Elmer Diamond when activated or absorbed. However, polymer and com- DSC. Finally, the kinetic coefficient KAv and the Avrami posite processing involves much more complex thermal exponent n are computed from the experimental data. conditions, including non-isothermal crystallization. Its These methods are dedicated to small samples (wmg) appropriate theoretical treatment requires the develop- and cannot survey the whole area of conditions encoun- ment of appropriate models to describe the associated ki- tered in all the material forming processes: pressure up to netics. In particular, Ozawa [9] extended the Avrami theory 40 MPa, cooling rate up to 1000 K/s and shear rate of À to the case of crystallization at a constant cooling rate. 400 s 1 (conditions for injection molding). Thus, the Introducing an additional isokinetic assumption into the Avrami function has to be extrapolated to lower tempera- Avrami model, Nakamura [10] proposed a new description tures [24]. of the overall crystallization kinetics valid whatever tem- Despite a large number of characterization devices, the perature course is followed. The Nakamura model is widely study of the kinetics at very low crystallization tempera- used in crystallization modeling and, particularly, in in- tures (e.g. T < 260C for PEEK, T < 80C for PP) remains a jection molding [11,12]. A differential form of this approach challenging task. It requires as a precondition to reach very has been advanced by Patel and Spruiell [13]. An alternative high cooling rates and, hence, to reduce the sample mass. to these models is the use of a system of differential “rate Thus, it requires greatly improved sensitivity of the calo- equations” [14–16]. rimetric sensor and to reduce the time constant of the However, at least some of the assumptions underlying apparatus. In this context, laboratory devices [25–28], and above mentioned theories are often not fulfilled over the especially the nano-DSC [29–31], have been developed to whole crystallization time. Deviations can be attributed, in reach cooling rates up to more than 103 K/s. These nano- particular, to higher complexity of the nucleation process DSC devices were developed for very small sample mass: and/or secondary crystallization. The latter phenomenon is from 10 nano grams to hundreds of nano grams. This new as a rule not taken into account in the previously cited apparatus supplies us with a novel opportunity to reach theories, but it is well known to occur in polyamide (PA), lower crystallization temperatures as compared to classical polyethylene (PE), polyoxymethylene (POM), polyethylene DSC and to determine the parameters of overall crystalli- oxide (PEO) and PEEK. It essentially consists of perfecting of zation kinetic models. the spherulites created during primary crystallization, and In the present work, a commercial nano calorimeter, occurs when they impinge each other. At this time, the Flash DSC 1, Mettler Toledo, has been used to follow the degree of crystallinity (crystalline volume divided by the isothermal crystallization of PEEK from 170Cto310C. The total volume of the polymer) of the spherulites themselves Flash DSC 1 allows one to reach heating rates up to is increasing by thickening of the crystals,
Details
-
File Typepdf
-
Upload Time-
-
Content LanguagesEnglish
-
Upload UserAnonymous/Not logged-in
-
File Pages11 Page
-
File Size-